El corte térmico de metales es un proceso esencial en la mayoría de la fabricación de metales, como el procesamiento de láminas de metal, donde primero debemos cortar la placa de acero en la forma aproximada que necesitamos y luego realizar un mecanizado o soldadura de precisión para crear el componente deseado.
En la producción industrial, el corte térmico de metales generalmente incluye el corte con gas, el corte por plasma y el corte por láser, entre otros.
En comparación con el corte con gas, el corte por plasma tiene un rango de corte más amplio y una mayor eficiencia.
La tecnología de corte por plasma fino ha alcanzado el límite inferior del corte por láser en términos de la calidad de la superficie del material cortado y es mucho más económica que el corte por láser. Por lo tanto, ha sido muy utilizado en el corte real.
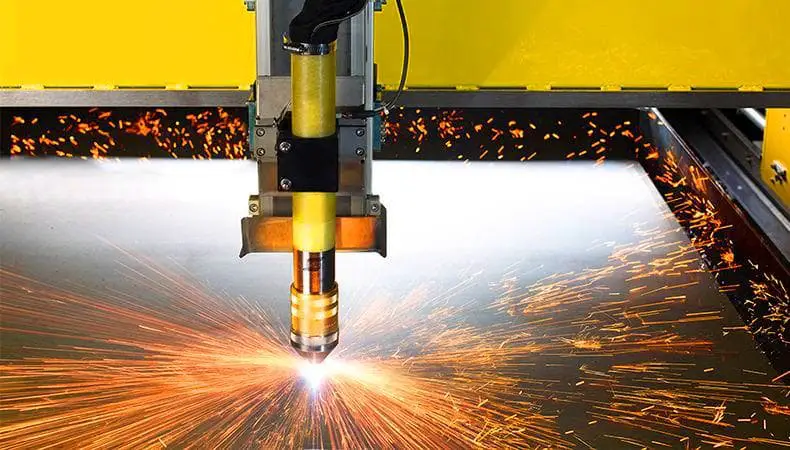
1. Comprensión del corte térmico de metales
El corte por llama, el corte por plasma y el corte por láser se clasifican según el tipo de energía térmica de corte y la forma del corte.
1.1 Corte con llama (corte con gas)
El corte se forma fusionando el metal con una llama producida al quemar una mezcla de gas inflamable y oxígeno y luego soplando.
Generalmente se utiliza gas acetileno, pero también se puede utilizar gas de petróleo, gas natural o gas de carbón.
Debido a factores como la presión del gas, la altura de la boquilla de corte y el tiempo de precalentamiento, el rango de deformación general del material cortado es relativamente grande en el corte con llama, lo que lo hace incapaz de satisfacer las necesidades del corte de alta precisión, y la velocidad de corte es relativamente baja. .
Además, se requiere precalentamiento antes del corte, lo que lleva tiempo y dificulta la adaptación a operaciones sin personal.
1.1.1 Ventajas:
(1) El oxicorte puede cortar acero al carbono muy grueso y su rango de corte es amplio, capaz de cortar placas de acero con un espesor de 6 mm a 200 mm;
(2) El precio del equipo de oxicorte es relativamente bajo y el costo de inversión inicial también es bajo.
1.1.2 Desventajas:
(1) Se requiere mucho tiempo de precalentamiento y perforación para cortar, velocidad de corte lenta;
(2) Deformación térmica significativa durante el corte, especialmente al cortar láminas delgadas (0,5-6 mm), baja precisión de corte;
(3) No se pueden cortar metales coloreados como cobre, aluminio y acero inoxidable;
(4) El método de quema de combustible es muy contaminante para el medio ambiente y no es respetuoso con el medio ambiente.
El oxicorte controlado numéricamente de láminas delgadas (0,5-6 mm) ha sido reemplazado gradualmente por el corte por plasma en el área de corte, pero en términos de corte de láminas gruesas y medianas, el oxicorte controlado numéricamente sigue siendo insustituible y el oxicorte todavía ocupa un cierto mercado. cuota debido a su ventaja de precio en el corte de láminas delgadas.
1.2 Corte por arco de plasma
Usando arco de plasma como fonte de calor e contando com gás de plasma térmico de alta velocidade (como nitrogênio, argônio e nitrogênio-argônio, gás de mistura argônio-hidrogênio, etc.) para derreter o metal e explodi-lo para formar uma costura Corte .
En las mismas condiciones, la velocidad de corte del arco de plasma es mayor que la del corte con gas, y la gama de materiales cortados también es más amplia que la del corte con gas.
Hay tres tipos comunes: corte por arco de plasma de corriente pequeña, corte por arco de plasma de corriente grande y corte por arco de plasma con chorro de agua.
1.2.1 Ventajas:
(1) Amplio campo de corte, puede cortar todas las láminas de metal;
(2) Velocidad de corte rápida, alta eficiencia, la velocidad de corte puede alcanzar 10 m/min o más;
(3) La precisión del corte es mayor que la del corte con llama, el corte bajo el agua no tiene deformación y la precisión del corte por plasma fino es aún mayor.
1.2.2 Desventajas:
(1) Es difícil cortar láminas de acero de más de 20 mm, lo que requiere una fuente de plasma de alta potencia y alto costo.
(2) Al cortar placas gruesas, la verticalidad del corte es deficiente y el corte adquiere forma de V.
El corte por plasma submarino puede eliminar el ruido, el polvo, los gases nocivos y la contaminación del arco generado durante el corte, mejorando eficazmente el entorno de trabajo.
Lectura relacionada: Eliminación de polvo por corte por plasma CNC: explicada
Con el uso del corte por plasma fino, la calidad del corte se ha acercado al nivel del corte por láser y con la madurez de la tecnología de corte por plasma de alta potencia, el espesor de corte ha superado los 150 mm, ampliando la gama de corte de las máquinas de corte por plasma CNC.
1.3 Corte por láser
Corte utilizando un rayo láser como fuente de calor (fuente láser).
Su temperatura supera los 11.000 ℃, suficiente para vaporizar cualquier material. El corte por láser tiene un filo estrecho y preciso, una superficie lisa y una calidad superior a cualquier otro método de corte térmico.
La fuente láser es generalmente un rayo láser de CO 2 con una potencia de trabajo de 500 ~ 2500 vatios; el rayo láser se concentra en un área muy pequeña a través de lentes y espejos reflectantes.
La energía altamente concentrada puede calentar rápidamente un área local, provocando que el acero inoxidable se evapore.
Además, debido a que la energía está altamente concentrada, sólo se transmite una pequeña cantidad de calor a otras partes del acero, lo que provoca una deformación mínima o nula.
El láser puede cortar con precisión formas complejas a partir de la materia prima, y la materia prima cortada no necesita procesamiento adicional.
1.3.1 Ventajas:
(1) Buena calidad de corte, ancho de corte estrecho, alta precisión, buena rugosidad de la superficie de corte y, en general, sin necesidad de procesamiento adicional;
(2) Puede soldarse directamente después del procesamiento;
(3) Velocidad de corte rápida, pequeña zona afectada por el calor, mínima deformación;
(4) Limpio, seguro y libre de contaminación.
1.3.2 Desventajas:
(1) Actualmente, el corte por láser solo es adecuado para cortar placas delgadas (generalmente lleva mucho tiempo perforar agujeros en placas gruesas);
(2) El precio del equipo de corte por láser es bastante caro, alrededor de 1,5 millones de yuanes o más.
A partir de la situación actual de la aplicación de corte por láser, cada vez más empresas adoptarán la tecnología de corte por láser de CO2 .
El corte por láser de CO 2 se utiliza ampliamente en placas de acero con bajo contenido de carbono de 12 mm de espesor, placas de acero inoxidable de 6 mm de espesor y materiales no metálicos de 20 mm de espesor.
Para cortar superficies curvas tridimensionales, también comenzó a utilizarse en las industrias automovilística y aeroespacial.
2. Comparación de las características técnico-económicas de tres métodos de corte en caliente”
El corte por llama, el corte por plasma y el corte por láser tienen actualmente una gran demanda, cada uno con una determinada cuota de mercado dependiendo de los requisitos de corte y los precios del mercado.
Una comparación de sus características técnico-económicas se puede ver en las Tablas 1 y 2.
Tabla 1: Comparación de uno de los tres métodos de corte
Comparación técnica y económica de tres métodos de corte. | |||||
Método de corte | Corte por llama | corte por plasma | Corte con laser | ||
Energía de fuente de calor | pequeño | promedio | grande | ||
Materiales adecuados para cortar. | Acero al carbono, acero de baja aleación. | Aceros con bajo contenido de carbono, aceros de baja aleación, aceros inoxidables, aceros, aluminio y sus aleaciones y otros metales no ferrosos. | Aceros con bajo contenido de carbono, aceros de baja aleación, aceros inoxidables, metales no ferrosos y no metales. | ||
Espesor máximo de corte/mm | =4000 acero al carbono) | =200 (acero inoxidable) | =20 (acero) |
||
Velocidad de corte/mm.min-1 | <1mm | – | 3.000 | >5000 | |
dos | – | 4000 | 3500 | ||
6 | 600 (boquillas de igual presión) |
3700 | 1000 | ||
12 | 500 | 2700 (corte por plasma de oxígeno 200A) | 360 | ||
25 | 450 | 1200 | – | ||
50 | 300 | 250 | – | ||
>100 | <150 | – | – |
Tabla 2: Comparación de dos de los tres métodos de corte
Comparación de las características tecnoeconómicas del método de los tres cortes | |||
Método de corte | Corte por llama | corte por plasma | Corte con laser |
Ancho de corte/mm | 1,5-2,5 | 2,5-5,0 | 0,2-0,8 |
Deformación de corte | grande | pequeño | Mínimo |
Precisión de la dimensión de corte/mm | Débil 1-2 | Generalmente 0,5-1 (0,2) | Muy bueno 0.2 |
Perpendicularidad de la superficie de corte. | bien | Pobre | bien |
Rugosidad de la superficie de corte | comúnmente | muy bien | preferiblemente |
Grado de fusión del borde superior de la superficie de corte. | no grande | Grande (no grande) | Muy pequeño |
Zona afectada por el calor (calor absorbido por la unidad)/J.mm-1 | Grande (22,53) | Mediano (pequeño) (7,33) | Pequeño (4.09) |
Contaminación ambiental | comúnmente | Se pueden reducir considerablemente los grandes cortes bajo el agua (polvo, ruido, luz de arco, etc.) | casi nunca |
Inversión en equipos finalizada/definida | Bajo | Más bajo | Alto |
El corte por plasma, cuando se combina con diferentes gases de trabajo, puede cortar varios metales que son difíciles de cortar con corte con oxígeno, especialmente metales no ferrosos (acero inoxidable, aluminio, cobre, titanio, níquel), con resultados de corte aún mejores.
Su principal ventaja es que al cortar metales delgados, el corte por plasma es rápido, especialmente al cortar láminas comunes de acero al carbono, con una velocidad que puede alcanzar de 5 a 6 veces la del corte con gas, con una superficie de corte lisa y mínima deformación térmica. , y casi sin zona de impacto térmico.
En la actualidad, con la madurez de la tecnología de corte por plasma de alta potencia, el espesor de corte puede alcanzar los 150 mm, y el uso de la tecnología de chorro de agua en el corte por plasma de alta potencia ha hecho que la calidad del corte se acerque al límite inferior de precisión del láser (± 0,2 mm). corte.
Debido al elevado precio de las máquinas de corte por láser y a su idoneidad actual sólo para cortar chapas finas (generalmente con un largo tiempo de perforación para chapas gruesas) y con máquinas de corte por plasma finas con una precisión de corte que puede llegar al límite inferior al corte por láser y un calidad de superficie de corte similar, pero con un costo de corte mucho menor que el corte por láser, alrededor de 1/3, con un espesor máximo de corte de 25 mm, es ventajoso reemplazar las costosas máquinas de corte por láser por máquinas de corte por plasma fino, para realizar cortes finos y altos. -Cortes rápidos de chapa media y fina de la forma más económica.
3. Clasificación y Aplicación del Corte por Plasma
3.1.1 El método de corte por plasma se puede clasificar en corte por plasma de oxígeno, corte por plasma de nitrógeno, corte por plasma de aire y corte por plasma de argón-hidrógeno según el gas de trabajo del plasma.
Los diferentes métodos de corte tienen diferentes aplicaciones debido a las diferencias en las propiedades físicas y químicas de los medios de trabajo utilizados.
(1) El corte con oxígeno por plasma tiene las características de alta velocidad de corte, pequeña deformación de la pieza de trabajo y rápido consumo de electrodos, debido al alto calor de disociación, el buen transporte de calor y las propiedades químicas activas del oxígeno como gas de trabajo, y generalmente solo se usa para cortar. acero carbono;
(2) El corte con nitrógeno por plasma utiliza nitrógeno como gas de trabajo y, debido a la presencia de nitrógeno, es fácil producir una capa nitrurada en la superficie de corte, lo que resulta en una mala calidad de la superficie, pero debido a que el nitrógeno es barato, este método es generalmente se utiliza para cortar acero inoxidable que no se utiliza directamente como material de soldadura y con bajos requisitos de calidad superficial;
(3) El corte por plasma utiliza aire como medio de trabajo, que tiene en común los dos métodos de corte anteriores y también se utiliza para cortar acero al carbono con bajos requisitos de calidad superficial.
En los últimos años, China ha desarrollado vigorosamente las pequeñas máquinas de corte por plasma de aire actuales, y su uso se está generalizando cada vez más, y el desarrollo de las máquinas de corte por plasma de aire con inversor ha creado las condiciones para la conservación de energía;
(4) El método de corte por plasma de argón-hidrógeno utiliza argón e hidrógeno fácilmente ionizables con buena conductividad térmica como gas de trabajo, y la combinación de los dos puede formar una columna de arco y un haz de plasma estables y de alta densidad de energía con una gran capacidad de corte.
Sin embargo, debido a su elevado precio, generalmente se utiliza para cortar acero inoxidable y aluminio con altos requisitos de calidad de corte.
3.1.2 Clasificación del corte por plasma y sus aplicaciones
Según el medio de corte por plasma, el método de enfriamiento por chorro de plasma y la calidad del corte, los métodos de corte por plasma se pueden dividir en corte por plasma tradicional, corte por plasma de doble gas, corte por plasma por chorro de agua y corte por plasma fino.
(1) El corte por plasma tradicional (Figura 1) generalmente utiliza el mismo gas (generalmente aire o nitrógeno) para enfriar y generar el arco de plasma.
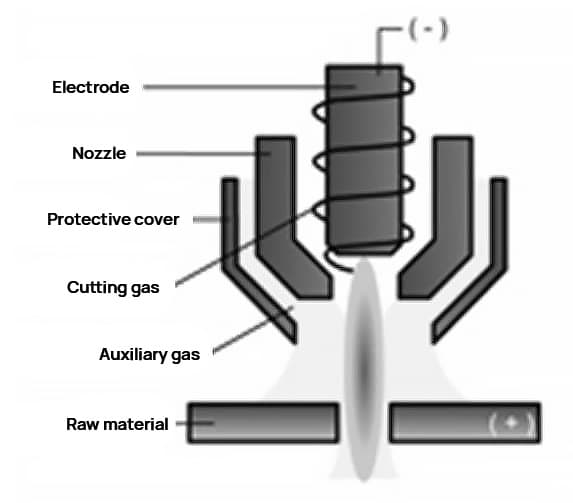
La mayoría de los sistemas tienen una corriente nominal inferior a 100 A y pueden cortar materiales de menos de 16 mm de espesor, utilizados principalmente para situaciones de corte manual.
(2) Corte por plasma con doble gas (Figura 2), utiliza dos gases; uno para formar plasma y el otro para protección. Se utiliza gas protector para aislar el área de corte del aire, lo que da como resultado un filo más suave.

Este es también el proceso de corte más popular porque se pueden utilizar diferentes combinaciones de gases para obtener la mejor calidad de corte para un material determinado.
(3) El corte por plasma protegido por agua (Figura 3) evolucionó a partir del proceso de doble gas, utilizando agua en lugar del gas protector. Mejora el efecto de enfriamiento de la boquilla y la pieza de trabajo y puede lograr una mejor calidad de corte al cortar acero inoxidable.
Este proceso es sólo para aplicaciones de corte industrial.
(4) El corte por plasma por chorro de agua (Figura 4) utiliza un gas para generar plasma e inyecta agua directamente en el arco de forma radial o vórtice, aumentando considerablemente el grado de compresión del arco y, por tanto, la densidad y temperatura del mismo. arco.
El rango actual de corte por plasma por chorro de agua es de 260 a 750 A y se utiliza para cortes de alta calidad de diversos materiales de diferentes espesores.
Este proceso también es sólo para aplicaciones de corte industrial.
(5) El corte por plasma fino (Figura 5) es un proceso que tiene una alta densidad de corriente de arco de plasma, típicamente varias veces mayor que la densidad de corriente de un arco de plasma convencional.
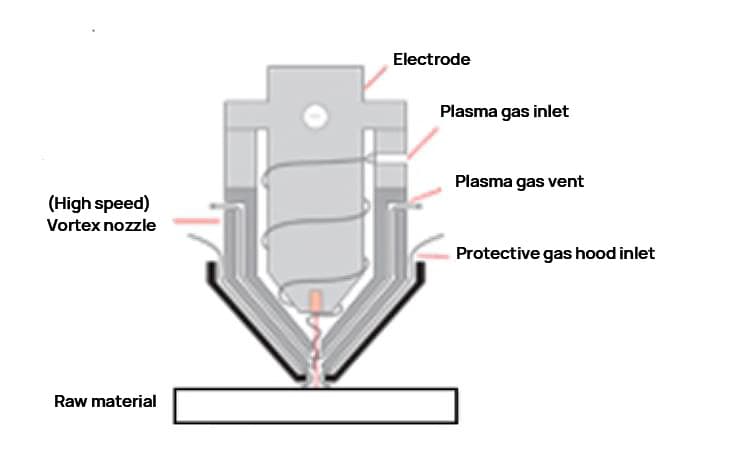
La estabilidad del arco también se ha mejorado mediante la introducción de técnicas como la rotación de campos magnéticos, lo que permite una precisión de corte muy alta.
Se puede lograr una excelente calidad de corte al cortar materiales delgados (menos de 16 mm) a velocidades más bajas. La mejora de la calidad se debe al uso de tecnología de punta para comprimir el arco de manera muy efectiva, aumentando así considerablemente la densidad de energía.
El requisito para operar a una velocidad más baja es permitir que el equipo de movimiento se mueva con mayor precisión a lo largo del contorno especificado. Este proceso sólo se utiliza en aplicaciones de corte industrial.
4. Selección de parámetros del proceso de corte por plasma.
Hay muchos parámetros del proceso de corte por plasma, incluida la corriente de corte, la velocidad de corte, el voltaje del arco, el gas de trabajo y el caudal, la altura de la boquilla, etc.
Diferentes parámetros tienen diferentes grados de impacto en la estabilidad y calidad del proceso de corte, y los parámetros deben seleccionarse de acuerdo con el tipo de material de corte, el espesor de la pieza de trabajo y los requisitos específicos durante el corte.
4.1 Corriente de corte
La corriente de corte es el parámetro más importante del proceso de corte, que determina directamente el espesor y la velocidad de corte, es decir, la capacidad de corte.
El impacto de la corriente de corte en el corte es el siguiente:
(1) Aumentar la corriente de corte aumenta la energía del arco, mejora la capacidad de corte y aumenta la velocidad de corte en consecuencia.
(2) Al aumentar la corriente de corte, aumenta el diámetro del arco, lo que hace que el arco sea más grueso y el corte más ancho.
(3) Una corriente de corte demasiado grande aumenta la carga térmica en la boquilla, provocando que la boquilla se dañe demasiado pronto y reduciendo la calidad del corte, o incluso imposibilitando el corte normal.
Por lo tanto, se debe seleccionar la corriente de corte correcta y la boquilla correspondiente en función del espesor del material antes de cortar.
Sobrecargar la boquilla (es decir, exceder la corriente de trabajo de la boquilla) dañará rápidamente la boquilla. La intensidad de la corriente generalmente debe ser del 95% de la corriente de trabajo de la boquilla.
4.2 Velocidad de corte
El rango de velocidad de corte ideal se puede determinar mediante las instrucciones del equipo o mediante experimentación. Debido a factores como el espesor del material, el material, el punto de fusión, la conductividad térmica y la tensión superficial después de la fusión, la velocidad de corte también cambia en consecuencia.
El impacto de la velocidad de corte en el corte se refleja principalmente en los siguientes aspectos:
(1) Aumentar moderadamente la velocidad de corte puede mejorar la calidad del corte, es decir, el corte es un poco más estrecho y la superficie de corte es más suave y, al mismo tiempo, puede reducir la deformación.
(2) Si la velocidad de corte es demasiado rápida, la energía de la línea de corte será menor que el valor requerido y el chorro no podrá eliminar rápidamente la escoria de corte, lo que resultará en una mayor cantidad de arrastre, acompañada de escoria suspendida, y la superficie la calidad del corte disminuye.
(3) Cuando la velocidad de corte es muy baja, debido a que el corte es el cátodo del arco de plasma, para mantener la estabilidad del arco mismo, los puntos del cátodo o la región del cátodo deben encontrar un lugar para conducir la corriente cerca del Al mismo tiempo, la costura de corte más cercana transferirá más calor a la dirección radial del chorro, haciendo el corte más ancho.
El material fundido en ambos lados del corte se acumula y solidifica en el borde inferior, formando escoria que es difícil de eliminar, y el borde superior del corte forma un redondeo debido al calentamiento y fusión excesivos.
(4) Cuando la velocidad es extremadamente baja, el arco incluso se extinguirá debido al corte amplio. Se puede observar que la buena calidad de corte y la velocidad de corte son inseparables.
La velocidad de corte debe determinarse en función de la potencia del arco de plasma, el espesor de la pieza y el material. Con la misma potencia de corte, la velocidad de corte debería ser más rápida para el aluminio debido a su bajo punto de fusión, más lenta para el acero debido a su alto punto de fusión y más lenta para el cobre debido a su buena conductividad térmica y rápida disipación de calor.
4.3 Voltaje del arco
Generalmente se considera que el voltaje de salida normal de la fuente de alimentación es el voltaje de corte.
Las máquinas de corte por plasma generalmente tienen un voltaje sin carga y un voltaje de trabajo altos, y cuando se utilizan gases de alta ionización como nitrógeno, hidrógeno o aire, el voltaje requerido para estabilizar el arco de plasma será mayor.
Cuando la corriente es constante, aumentar el voltaje significa aumentar la entalpía del arco y la capacidad de corte.
Si al mismo tiempo que aumenta la entalpía, se reduce el diámetro del chorro y aumenta el caudal de gas, a menudo se pueden lograr velocidades de corte más rápidas y una mejor calidad de corte.
4.4 Gas y flujo de trabajo
El gas de trabajo incluye gas de corte y gas auxiliar, y algunos equipos también requieren gas de inicio de arco.
Por lo general, se debe elegir el gas de trabajo adecuado en función del tipo, espesor y método de corte del material de corte.
El gas de corte debe garantizar la formación del chorro de plasma y también la eliminación del metal fundido y los óxidos del corte.
Un flujo de gas demasiado alto puede alejar más calor del arco, acortar la longitud del chorro, reducir la capacidad de corte y provocar inestabilidad del arco, mientras que un flujo de gas demasiado bajo puede hacer que el arco de plasma pierda su rectitud, haciendo que el corte sea menos profundo y produzca fácilmente escoria.
Por lo tanto, el flujo de gas debe estar bien coordinado con la corriente y la velocidad de corte.
En la actualidad, las máquinas de corte por arco de plasma controlan principalmente el flujo de gas a través de la presión del gas, porque cuando el diámetro del cuerpo de la pistola es fijo, el flujo se controla controlando la presión del gas.
La presión del gas utilizada para cortar un espesor determinado de material generalmente debe seleccionarse de acuerdo con los datos proporcionados por el fabricante del equipo.
Si existen otras aplicaciones especiales, la presión del gas debe determinarse mediante pruebas de corte reales.
La presión (flujo) correcta del gas de trabajo es muy importante para la vida útil de los consumibles. Si la presión es demasiado alta, la vida útil del electrodo se reducirá considerablemente y si la presión es demasiado baja, la vida útil de la boquilla se verá afectada.
Los sistemas de corte por plasma requieren gas de trabajo limpio y seco para funcionar correctamente. El gas sucio generalmente es un problema del sistema de compresión de gas, lo que acortará la vida útil de las piezas de desgaste y provocará daños anormales.
4.5 Altura de la boquilla
La altura de la boquilla se refiere a la distancia entre la cara extrema de la boquilla y la superficie de corte y constituye parte de toda la longitud del arco.
Debido a que el corte por arco de plasma generalmente utiliza fuentes de energía externas de corriente constante o de caída pronunciada, cuando aumenta la altura de la boquilla, el cambio de corriente es pequeño, pero la longitud del arco aumentará y el voltaje del arco aumentará, lo que resultará en un aumento en la potencia del arco;
Sin embargo, al mismo tiempo, aumentará la longitud del arco expuesto al medio ambiente y aumentará la pérdida de energía de la columna del arco.
Bajo el efecto combinado de estos dos factores, el primero suele ser completamente compensado por el segundo y, en cambio, la energía de corte efectiva disminuirá, lo que dará como resultado una reducción en la capacidad de corte.
Esto generalmente se refleja en una disminución de la fuerza de soplado del chorro de corte, un aumento de la escoria residual en la parte inferior del corte y bordes redondeados en el borde superior debido a una fusión excesiva.
Además, desde la perspectiva de la forma del chorro de plasma, el diámetro del chorro se expande hacia afuera después de salir de la pistola, y el aumento de la altura de la boquilla provocará inevitablemente un aumento del ancho de corte.
Por lo tanto, elegir la altura de boquilla más baja es beneficioso para mejorar la velocidad y la calidad del corte, pero una altura de boquilla demasiado baja puede causar el fenómeno de doble arco.
El uso de una boquilla cerámica externa puede ajustar la altura de la boquilla a cero, es decir, la cara extrema de la boquilla entra en contacto directo con la superficie de corte, lo que puede lograr buenos resultados.
De acuerdo a las instrucciones use una altura de boquilla razonable, al perforar use una distancia de 2 veces la distancia de corte normal o use la altura máxima que el arco de plasma pueda transmitir, esto puede aumentar la vida útil de las piezas de desgaste.
4.6 Densidad de potencia de corte
Para obtener un arco de corte por plasma de alta compresión, las boquillas de corte adoptan un diámetro de boquilla más pequeño, una longitud de canal de boquilla más larga y un efecto de enfriamiento mejorado, lo que aumenta la corriente que pasa a través de la sección efectiva de la boquilla, es decir, aumenta la densidad de potencia del arco.
Al mismo tiempo, la compresión también aumenta la pérdida de potencia del arco. Por lo tanto, la energía efectiva real utilizada para el corte es menor que la potencia de la fuente de energía, con una tasa de pérdida generalmente entre el 25% y el 50%.
Algunos métodos, como el corte por plasma con agua comprimida, tienen una mayor tasa de pérdida de energía, lo que debe tenerse en cuenta al diseñar los parámetros del proceso de corte o calcular los costos de corte.
Por lo tanto, el diámetro real de la boquilla de corte debe determinarse basándose en el espesor de la parte de corte y la especie de gas iónico seleccionada.
Cuando el espesor de corte es mayor, el diámetro de la boquilla también debe aumentarse en consecuencia.
Cuando se utiliza gas mixto Ar+H2, el diámetro de la boquilla puede ser un poco menor, mientras que si se utiliza N2, debe ser mayor.
5. Conclusión
El siglo XXI es una era que aboga por la protección ambiental verde.
Con el rápido crecimiento de la economía y el próspero desarrollo de la industria manufacturera, son inevitables mayores requisitos de tecnología de corte.
La tecnología de corte por plasma tiene muchas características respetuosas con el medio ambiente, por lo que el desarrollo de la tecnología de corte por plasma tiene la ventaja de mantenerse al día.
La tecnología de corte por plasma puede eliminar el ruido, el polvo, los gases nocivos y la luz del arco generados durante el corte a través de una plataforma de corte submarina o un dispositivo de tratamiento de humo y polvo, que básicamente cumple con los requisitos de protección ambiental.
En los últimos años, la tecnología de corte por plasma se ha desarrollado rápidamente y algunas tecnologías de corte precisas de alta velocidad están compitiendo con el corte por láser.
La tecnología de corte por plasma con control numérico es un campo de alta tecnología que integra tecnología de corte por plasma, tecnología de control numérico y tecnología de fuente de energía inversora, entre otras, y ha progresado junto con el desarrollo del control por computadora, la investigación de las características del arco de plasma y la electrónica de potencia. .
Además, el uso del corte por plasma con control numérico con software de programación de alimentador automático puede aumentar la tasa de utilización del material entre un 5% y un 10%. Con una capacidad de corte anual de 20 millones de toneladas, se pueden ahorrar entre 100.000 y 200.000 toneladas de acero al año, por un valor de miles de millones de yuanes.
En los países industrializados, existe una tendencia a sustituir las máquinas de corte por llama y las máquinas de corte por láser por máquinas de corte por plasma de control numérico.
En China, las máquinas de corte por plasma se utilizan ampliamente en diversas industrias, como automóviles, locomotoras, recipientes a presión, maquinaria química, industria nuclear, maquinaria en general, maquinaria de ingeniería y estructuras de acero.