Los siguientes factores juegan un papel fundamental en el proceso de corte por láser:
- Modo láser
- potencia del láser
- Posición de enfoque
- Altura de la boquilla
- Diámetro de la boquilla
- Gases auxiliares
- Pureza del gas auxiliar
- Flujo de gas auxiliar
- Presión de gas auxiliar
- Velocidad cortante
- Material laminar
- Calidad de la superficie de la placa (por ejemplo, óxido, residuos, etc.)
Los parámetros del proceso asociados con el corte por láser se muestran en la siguiente figura.
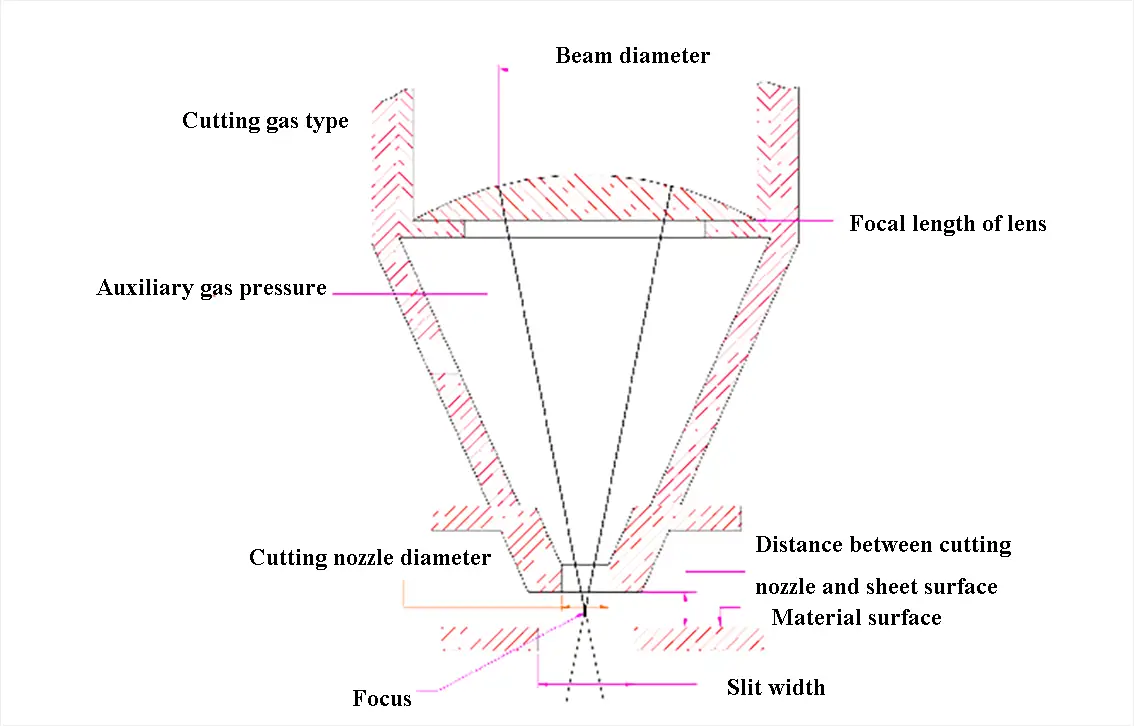
Fig. 1 Parámetros del proceso de corte
I. Modo láser
El modo láser tiene un gran impacto en el proceso de corte y produce mejores resultados al cortar láminas de acero. Esto está estrechamente relacionado con el modo del láser y la calidad de la lente óptica externa.
La distribución de la intensidad de la luz a lo largo de la sección transversal del rayo láser se denomina modo transversal del láser. Generalmente se considera que el modo transversal es el modo láser.
Varios modos transversales están representados por el símbolo TEMmn, donde TEM significa onda electromagnética transversal y M y N son números enteros positivos que representan los números ordinales de puntos con intensidad de luz cero en las direcciones del eje X e Y, respectivamente, conocidos como modo ordinal.
La siguiente figura muestra los focos de varios modos transversales diferentes del rayo láser. El modo TEM00, también conocido como modo básico, no tiene puntos con intensidad de luz nula. El modo TEM10 tiene un punto de intensidad cero en el
Los rayos láser con varios modos transversales se denominan multimodo.
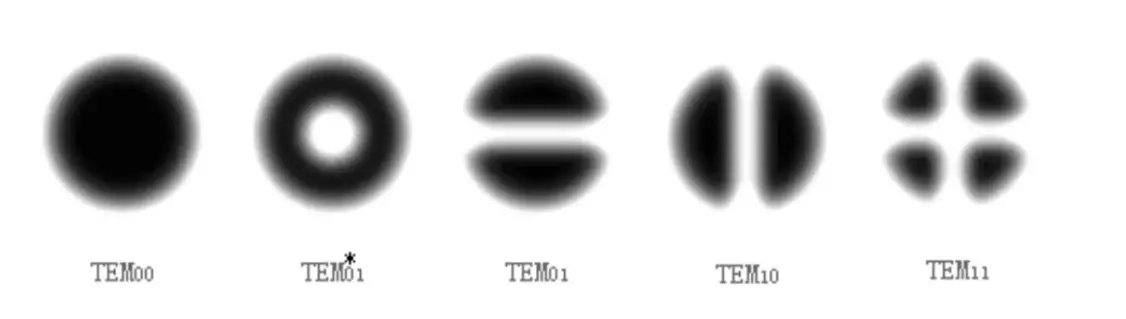
Fig. 2 Modo puntual
En la figura mencionada anteriormente, el modo TEM00 se denomina modo fundamental.
El modo TEM*01 es un modo de un solo toque y también se conoce como modo cuasi fundamental. Se agrega un asterisco * para distinguirlo de TEM01.
En realidad, el modo TEM01 y el modo TEM10 pueden considerarse el mismo modo porque los ejes X e Y están divididos artificialmente. A continuación se muestran estereogramas de varios modos.
Figura 3: estereograma del modo TEM00
Figura 4: estereograma del modo TEM20
Figura 5: estereograma del modo TEM23
Figura 6: Estereograma multimodo.
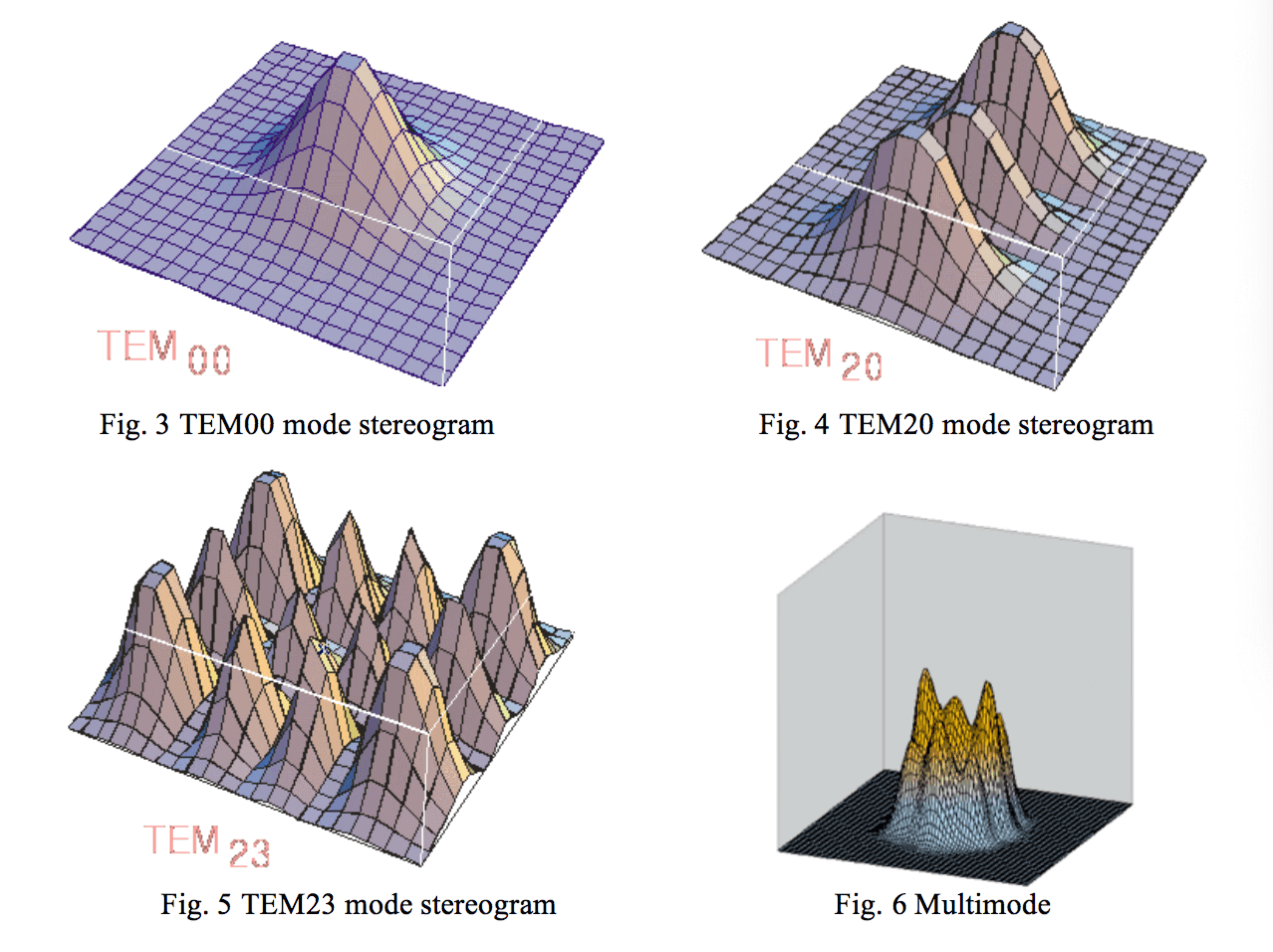
II. Posición focal
La posición de enfoque es un parámetro crucial y debe ajustarse en consecuencia.
1. La relación entre la posición de enfoque y la superficie de corte.
Posición focal | Diagrama esquemático | Características |
Distancia focal cero:
La atención se centra en la superficie de la pieza. |
![]() |
Es adecuado para acero al carbono fino de menos de 5 mm.
(sección cortada) ![]()
Cuando el foco está en la superficie superior de la pieza de trabajo, el resultado del corte es suave en la superficie superior, pero la superficie inferior no es lisa. |
Distancia focal negativa:
El foco está debajo de la superficie de la pieza de trabajo. |
![]() |
El aluminio, el acero inoxidable y otras piezas adoptan este método.
(sección cortada) ![]() El foco está situado en el centro y en la parte inferior, lo que da como resultado una superficie lisa más grande. Los resultados indican que el ancho de corte es mayor y el flujo de gas de corte es mayor con un enfoque en esta ubicación, en comparación con un enfoque con distancia focal cero. Además, el tiempo de perforación es mayor en esta posición de enfoque. |
Distancia focal positiva:
El foco está en la superficie de la pieza de trabajo. |
![]() |
Al cortar placas de acero gruesas, se utiliza oxígeno. La oxidación del oxígeno utilizado en el corte debe ocurrir de arriba a abajo. Para adaptarse al grosor del tablero, se requiere un ancho de corte mayor, que se puede lograr ajustando la configuración. La sección de corte se asemeja a la del corte con gas, con oxígeno soplando y produciendo una sección rugosa. |
2. La influencia de la posición de enfoque en la sección de corte.
1,5 mm por encima de la superficie | 0,5 mm por encima de la superficie | 2,5 mm por encima de la superficie |
![]() |
![]() |
![]() |
3. Búsqueda de enfoque
El concepto básico es utilizar pegamento de enmascarar para bloquear la boquilla y ajustar la distancia de enfoque. Luego se comprueba el tamaño de los agujeros. La posición con el agujero más pequeño es el foco. Finalmente, el mejor enfoque para cortar se determina basándose en el proceso de corte después de que se haya encontrado el enfoque.
III. Boquilla
La forma, el diámetro y la altura de la boquilla (la distancia entre la salida de la boquilla y la superficie de la pieza de trabajo) afectarán el resultado del corte.
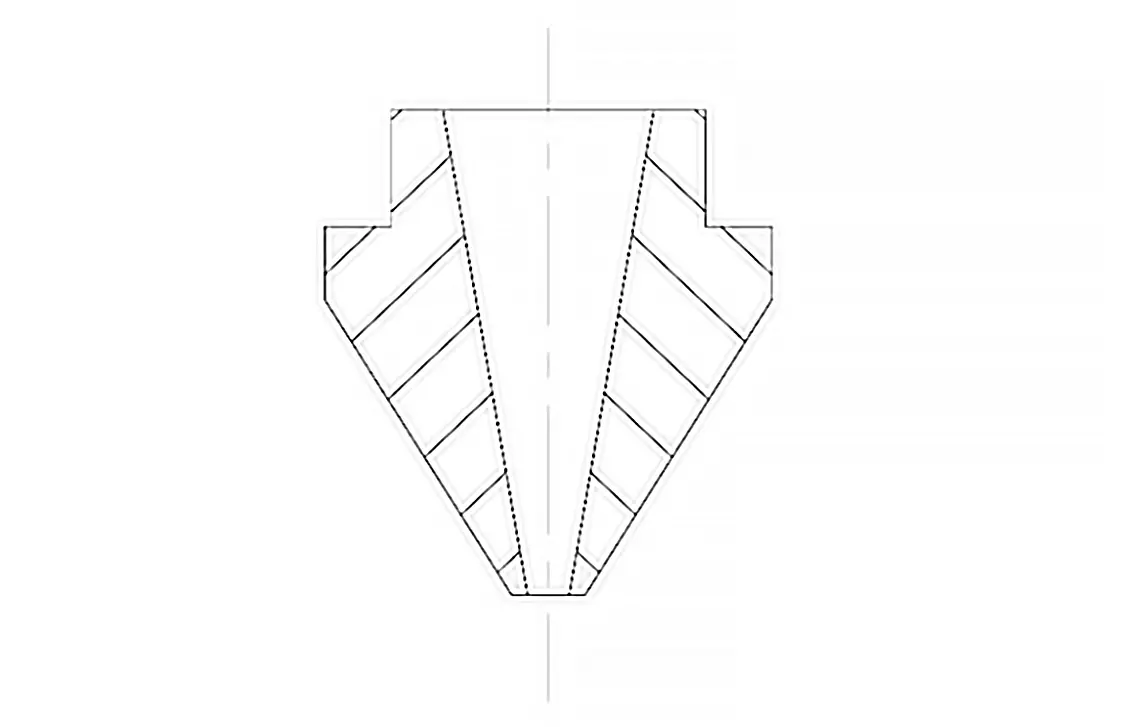
Figura 7 Boquilla
1. Función de la boquilla
- Ayuda a evitar que las impurezas, como los residuos derretidos, salten, pasen a través de la boquilla y contaminen la lente de enfoque.
- Regula el área y tamaño de difusión del gas para controlar la calidad del corte.
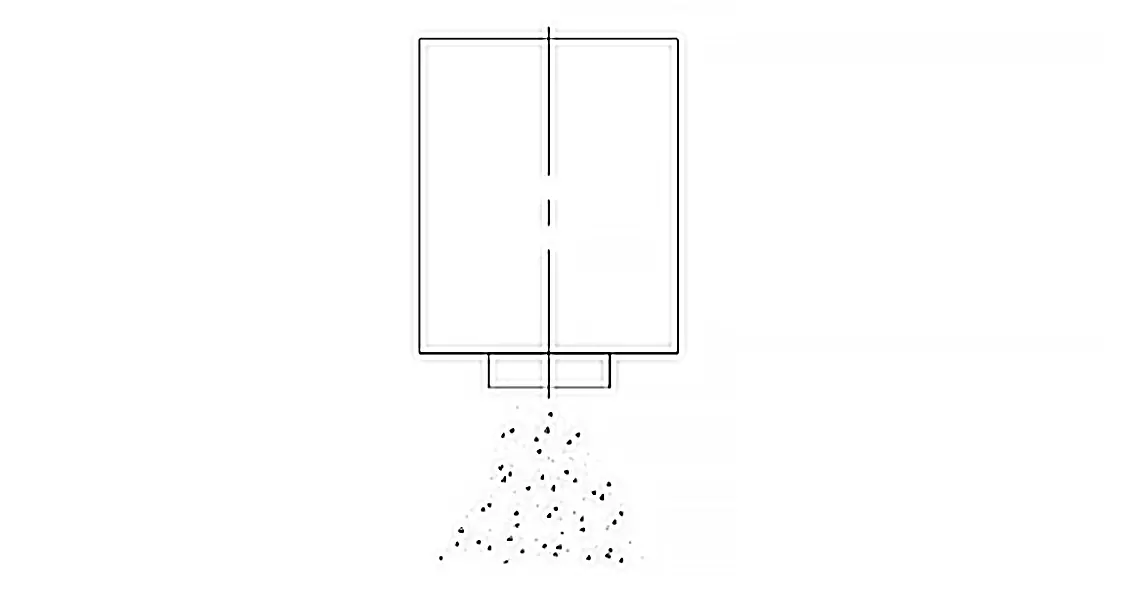
Fig. 8 Expulsión de gas sin boquilla
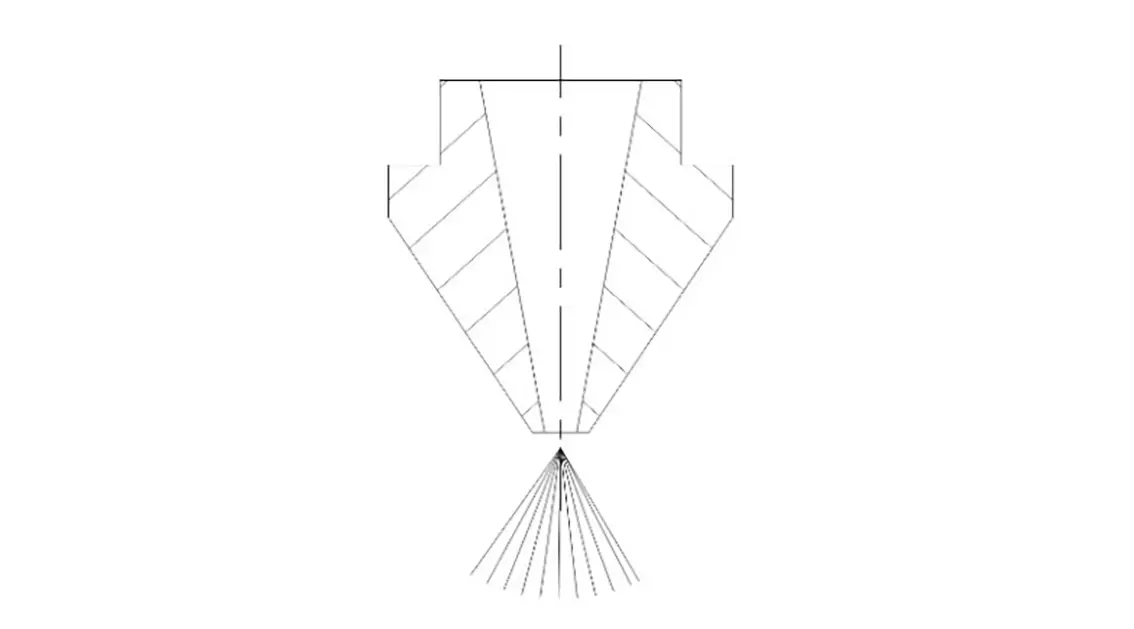
Fig. 9 Expulsión de gas con boquilla
2. La relación entre la boquilla y la calidad del corte.
La coaxialidad entre el centro del orificio de salida de la boquilla y el rayo láser es uno de los factores importantes que afectan la calidad del corte. Cuanto más gruesa es la pieza, mayor es la influencia. La coaxialidad se verá afectada directamente cuando la boquilla se deforme o haya un punto derretido.
Por lo tanto, la boquilla debe almacenarse con cuidado para evitar daños y deformaciones. La forma y el tamaño de la boquilla tienen una alta precisión de fabricación y se debe prestar atención al método de instalación correcto.
Si el estado de la boquilla es malo, puede que sea necesario cambiar las condiciones de corte y es mejor sustituirla por una nueva. Si la boquilla no está alineada con el eje del láser, afectará la calidad del corte de la siguiente manera.
1) Influencia en la sección de corte
Como se muestra en la figura, cuando el gas auxiliar se expulsa de la boquilla, el volumen del gas se vuelve desigual, con puntos fundidos en un lado pero no en el otro. El volumen desigual de gas tiene poco impacto cuando se cortan láminas delgadas de menos de 3 mm, pero se vuelve más grave cuando se cortan láminas más gruesas, a veces incluso impidiendo el corte exitoso.
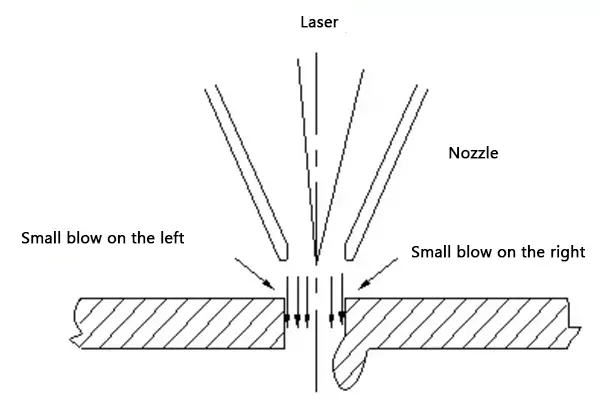
Fig. 10 Influencia de la coaxialidad en la sección de corte.
2) Impacto en esquinas afiladas
Si la pieza de trabajo tiene ángulos agudos o pequeños, estará sujeta a una fusión excesiva, lo que puede impedir el corte de placas gruesas.
3) Impacto en la perforación
Puede producirse inestabilidad en la perforación, dificultades para controlar la sincronización, fusión excesiva de placas gruesas y dificultad para dominar las condiciones de penetración. Sin embargo, estos problemas tienen poco efecto al cortar láminas delgadas.
3. Ajuste de coaxialidad entre el orificio de la boquilla y el rayo láser.
Los pasos para ajustar la coaxialidad entre el orificio de la boquilla y el rayo láser son los siguientes:
(1) Aplique pintura a la cara del extremo de salida de la boquilla (generalmente en rojo) y coloque cinta adhesiva en la cara del extremo de salida de la boquilla como se muestra en la figura.
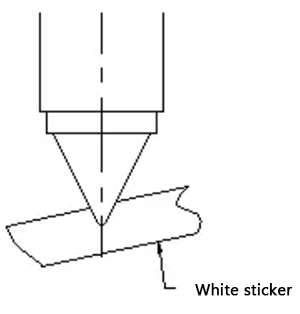
Fig. 11 Ajuste coaxial paso 1
(2) Utilice una potencia de 10 a 20 vatios para la perforación manual.
(3) Retire el papel autoadhesivo, teniendo cuidado de mantener su orientación para compararlo con la boquilla.
En condiciones normales, el láser quemará una mancha negra en el papel autoadhesivo. Sin embargo, si el centro de la boquilla se desvía demasiado del centro del rayo láser, el punto negro no será visible (ya que el rayo láser incidirá en la pared de la boquilla).
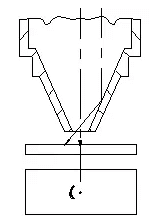
Fig. 12 Desviación de la boquilla demasiado grande
(4) Si el punto central es demasiado grande o pequeño, verifique si las condiciones son consistentes y si la lente de enfoque está segura.
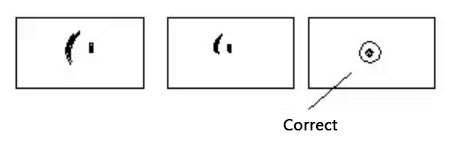
Fig. 13 Espejo de enfoque suelto
(5) Tenga en cuenta la dirección del punto negro con respecto al centro de la boquilla y ajuste la posición de la boquilla en consecuencia.
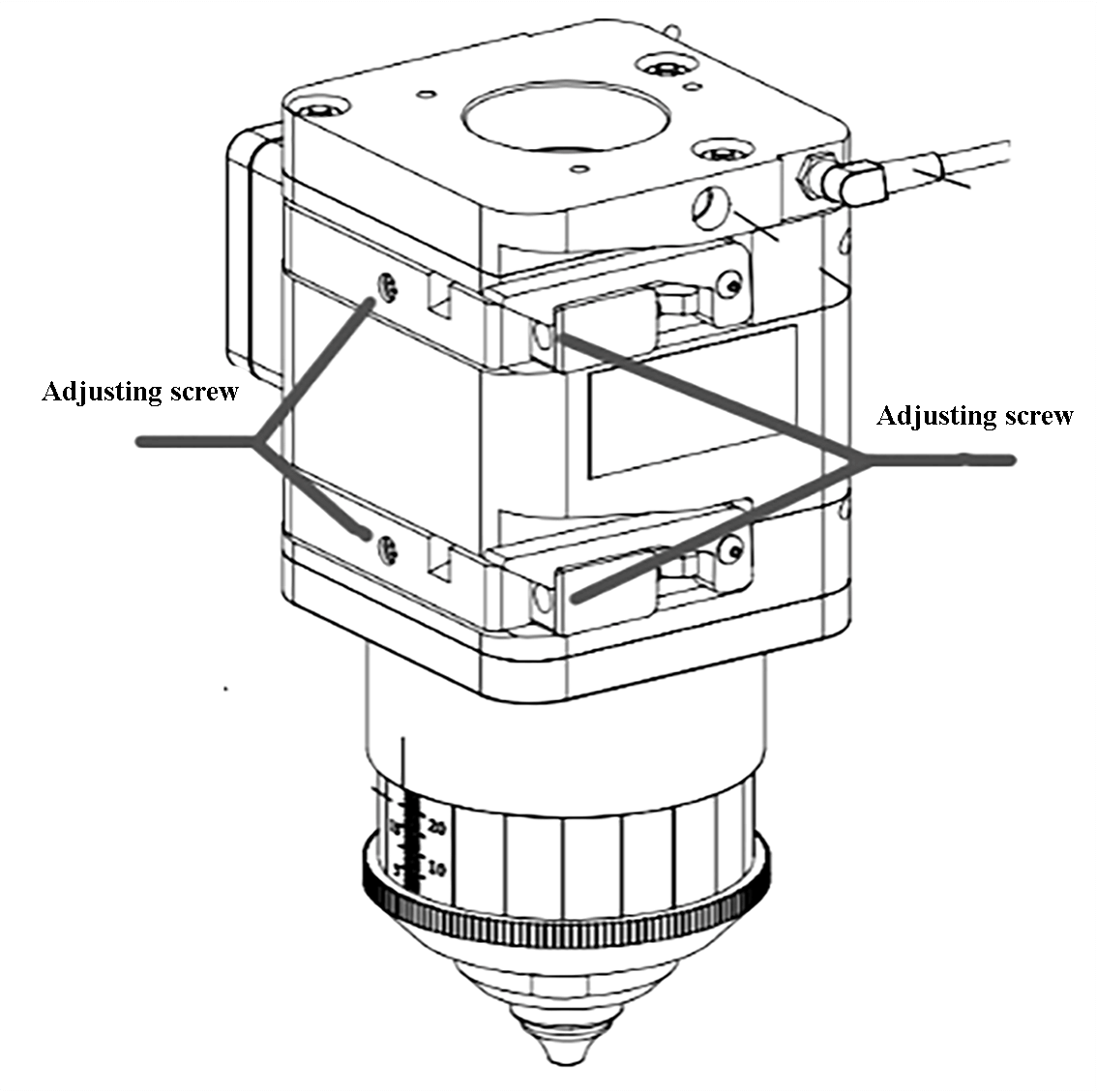
Fig. 14 Ajuste de la posición del rayo láser coaxial
4. Diámetro de la boquilla
El tamaño de la abertura tiene un impacto decisivo en la calidad del corte y la perforación. Si la abertura de la boquilla es demasiado grande, el material derretido puede salpicar durante el corte y pasar a través del orificio de la boquilla, dañando potencialmente la lente. Cuanto mayor sea la apertura, más probable será que esto ocurra, lo que reducirá la protección de la lente de enfoque y reducirá su vida útil.
Comparación de apertura de boquilla
Apertura de la boquilla | caudal de gas | Capacidad de eliminación de material fundido |
Pequeño | Rápido | Grande |
Grande | Lento | Pequeño |
La diferencia entre la boquilla φ1 y φ1.5
Diámetro de la boquilla | Placa delgada (menos de 3 mm) | Placa gruesa (más de 3 mm)
Alto poder de corte, mayor tiempo de enfriamiento y mayor tiempo de corte |
φ1 | La superficie de corte es buena. | El área de difusión de gas es pequeña e inestable, pero básicamente está disponible. |
φ1.5 | La superficie de corte será más gruesa y es fácil que la solución tenga manchas en la esquina. | El área de difusión del gas es grande, la velocidad del gas es lenta y el corte es estable. |
5. Ajuste de altura de la boquilla
La altura de la boquilla se refiere a la distancia entre la salida de la boquilla y la superficie de la pieza. El rango para configurar esta altura es entre 0,5 mm y 4,0 mm, con un ajuste típico de 0,7 mm a 1,2 mm para corte.
Si la altura se ajusta demasiado baja, la boquilla puede chocar con la superficie de la pieza de trabajo. Por otro lado, si se ajusta demasiado alto, la presión y la concentración del gas auxiliar disminuirán, lo que provocará una disminución de la calidad del corte. Al perforar, la altura debe ser un poco más alta, alrededor de 3,5 mm a 4 mm, para evitar que la lente de enfoque se contamine con salpicaduras de perforación.
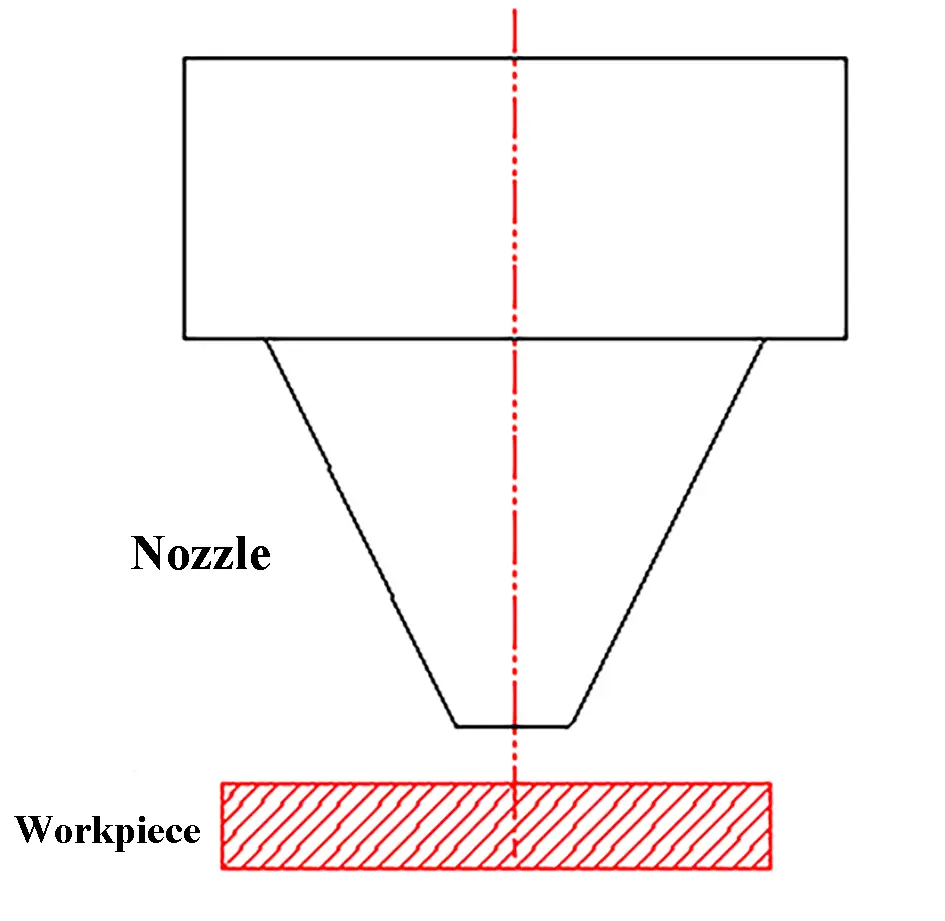
Fig. 15 Altura de la boquilla
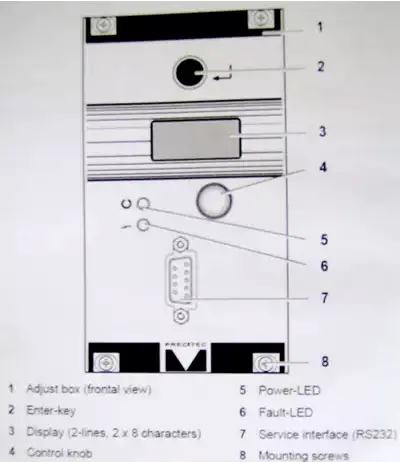
Caja de control de sensor capacitivo
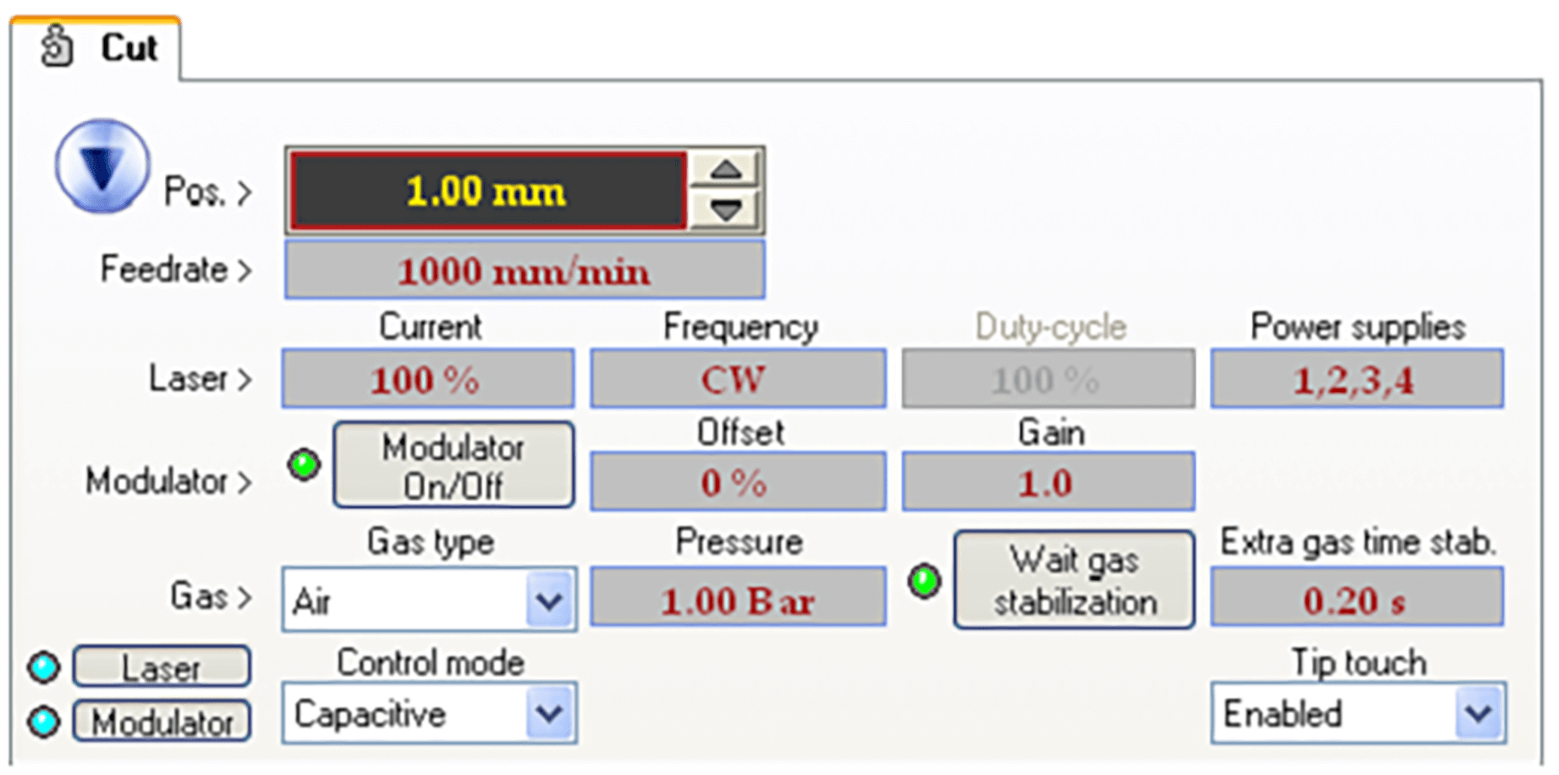
Como se muestra en la figura Se muestra el elemento de ajuste de altura de la boquilla.
4. Velocidad de corte
La velocidad de corte tiene un impacto directo en el ancho y la rugosidad de la incisión. Existe un valor ideal para la velocidad de corte que varía según el espesor del material y la presión del gas de corte. Este valor suele rondar el 80% de la velocidad máxima de corte.
1. Velocidad muy rápida
Si la velocidad de corte es demasiado alta, puede causar los siguientes problemas:
- Cortes incompletos con chispas aleatorias.
- Recortes inconsistentes con algunas áreas cortadas y otras no.
- Una sección de corte grueso sin solución.
La sección cortada tendrá rayas inclinadas y manchas de solución en la parte inferior.
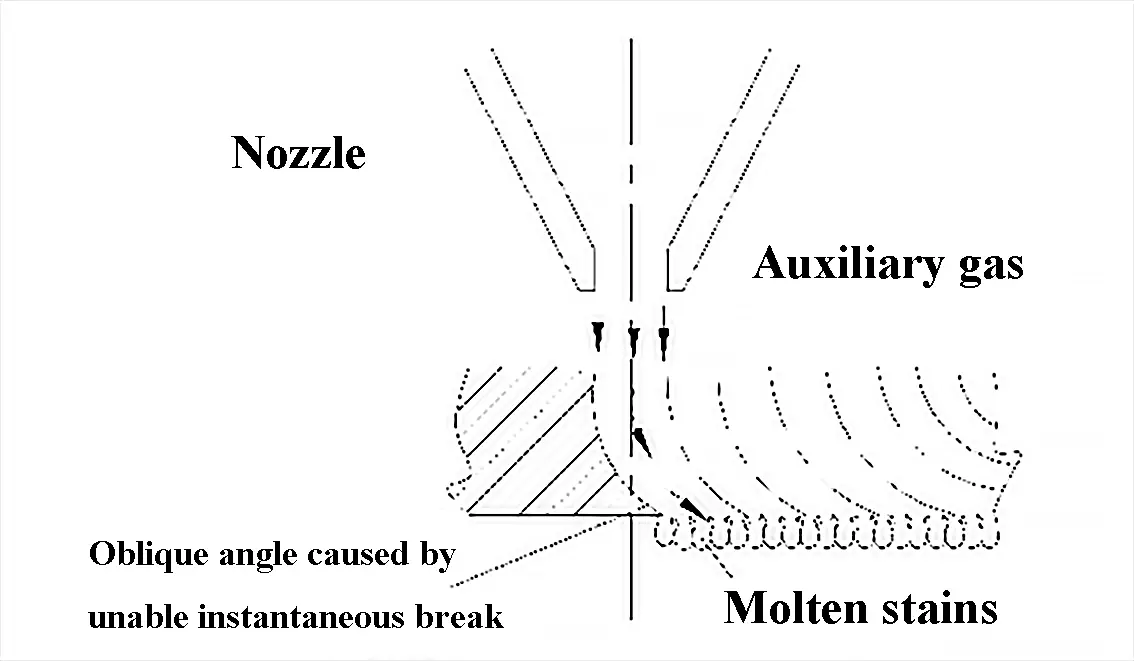
Fig.18 Velocidad muy rápida
2. Velocidad muy lenta
(1) Una fusión excesiva produce una superficie de corte áspera.
(2) La grieta se ensancha y las esquinas afiladas se derriten.
(3) Esto afecta la eficiencia de corte.
3. Determine la velocidad de corte adecuada
Determine si debe aumentar o disminuir la velocidad de alimentación según las chispas de corte.
1) Las chispas se esparcen de arriba a abajo
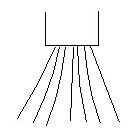
Fig. 19 Velocidad de corte normal
2) Si la chispa está inclinada, la velocidad de corte es demasiado rápida.
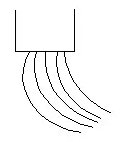
Fig. 20 Velocidad de corte demasiado rápida
3) Si las chispas no son difusas y pocas, y se juntan, la velocidad es muy lenta.
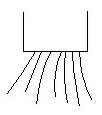
Fig. 21 Velocidad de corte demasiado lenta
La velocidad de alimentación es adecuada.
Como se muestra en la figura, la superficie de corte tiene una línea relativamente suave y no se derrite en la mitad inferior.
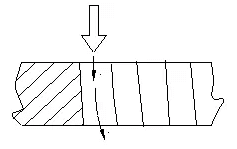
Fig. 22 Velocidad de corte normal
V. Corte de gas auxiliar
Considere los siguientes factores al seleccionar el tipo y la presión del gas auxiliar de corte:
- El oxígeno se utiliza normalmente para cortar acero al carbono común mediante perforación y corte a baja presión.
- El corte con aire se utiliza comúnmente para cortar metales no metálicos.
- Generalmente se utiliza nitrógeno para cortar acero inoxidable.
- La calidad del corte mejora con una mayor pureza del gas.
- Para cortar láminas de acero con bajo contenido de carbono, la pureza del gas debe ser de al menos el 99,6 % y para cortar láminas de acero al carbono con un espesor de más de 12 mm, la pureza del oxígeno debe ser superior al 99,9 %.
- La pureza del nitrógeno para cortar láminas de acero inoxidable debe ser superior al 99,6%.
- Una mayor pureza del nitrógeno da como resultado cortes de mejor calidad.
- La baja pureza del gas no sólo afecta la calidad del corte, sino que también provoca contaminación de la lente.
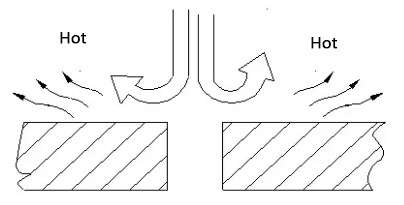
1. La influencia del gas auxiliar en la calidad del corte.
(1) El gas contribuye a la disipación del calor y la combustión, elimina la solución y mejora la calidad de la superficie de corte.
(2) Los efectos de la baja presión del gas en el corte.
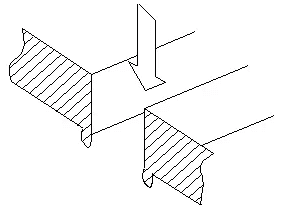
El. La superficie de corte se ha derretido.
B. La velocidad de corte no se puede aumentar, lo que afecta la eficiencia.
(3) La influencia de la alta presión del gas en la calidad del corte.
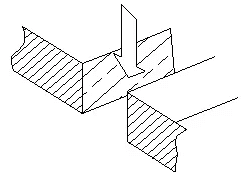
El. Si el flujo de aire es demasiado alto, la superficie de corte será más gruesa y la costura será más ancha.
B. Si el flujo de aire es excesivo, la pieza cortada se derretirá y no será posible una buena calidad de corte.
2. El efecto del gas auxiliar en la perforación.
(1) Cuando la presión del gas es demasiado baja, es difícil penetrar y el tiempo aumenta.
(2) Cuando la presión del gas es demasiado alta, el punto de penetración se derrite y se forma una gran área de fusión.
Como resultado, la presión de perforación para chapas delgadas es mayor que para chapas gruesas.
3. Asistencia de gas para corte de plexiglás
El plexiglás es inflamable. Para obtener una superficie de corte transparente y brillante, se elige nitrógeno o aire como retardantes de llama. Si se selecciona oxígeno, la calidad del corte no será lo suficientemente buena. Por lo tanto, es necesario seleccionar la presión adecuada según la situación real durante el corte.
Cuanto menor sea la presión del gas, más brillante será la luz de corte y más estrecha será la sección de cabello. Sin embargo, si la presión del gas es demasiado baja, se producirá una velocidad de corte lenta y llamas debajo de la superficie de la placa, lo que puede afectar negativamente la calidad de la superficie inferior.
SIERRA. potencia del láser
La potencia del láser necesaria para el corte por láser depende principalmente del tipo de corte y de las propiedades del material a cortar. El mayor requisito de potencia del láser es para el corte por vaporización, seguido del corte por fusión y el corte con oxígeno.
La potencia del láser tiene un impacto significativo en el espesor del corte, la velocidad y el ancho de la incisión. A medida que aumenta la potencia del láser, aumenta el espesor del material que se puede cortar, se acelera la velocidad de corte y también aumenta el ancho de la incisión.
La potencia del láser juega un papel crucial en la determinación del proceso de corte y la calidad.
1. La potencia es demasiado pequeña para cortarla.
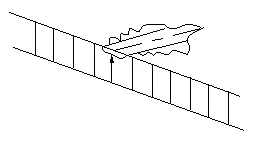
Fig. 26 Muy baja potencia
2. Si la potencia es demasiado alta, toda la superficie de corte se derretirá.
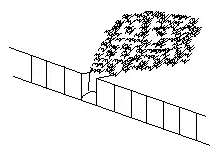
Fig. 27 Potencia excesiva
3. La potencia es insuficiente, lo que provoca puntos derretidos después del corte.
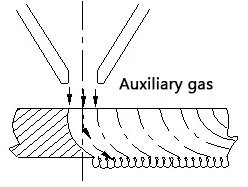
Fig.28 Deficiencia energética
4. La potencia es adecuada, la superficie de corte es buena sin puntos derretidos .
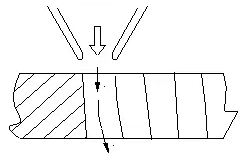
Fig. 29 Potencia adecuada
Resumen de parámetros de corte.
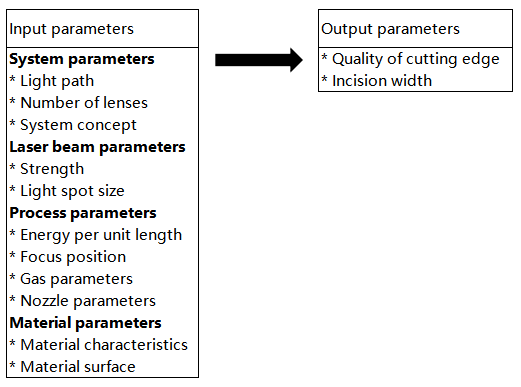
Los principales parámetros del corte por láser.
Velocidad cortante
Dada la densidad de potencia del láser y el material, la velocidad de corte sigue una fórmula empírica. Siempre que esté por encima del límite, la velocidad de corte del material es proporcional a la potencia del láser, lo que significa que aumentar la densidad de potencia puede aumentar la velocidad de corte.
La velocidad de corte también es inversamente proporcional a la densidad y espesor del material a cortar. Hay varias formas de mejorar la velocidad de corte:
(1) Aumentar la potencia (en el rango de 500-3000W);
(2) Cambiar el modo de haz;
(3) Reduzca el tamaño del punto de enfoque (por ejemplo, utilizando una lente de distancia focal corta).
Para materiales metálicos, si otras variables del proceso permanecen sin cambios, la velocidad de corte por láser se puede ajustar dentro de un rango mientras se mantiene una calidad de corte satisfactoria. Este rango parece ser relativamente amplio cuando se cortan metales finos.
Posición de enfoque
Una vez enfocado el rayo láser, el tamaño del punto es proporcional a la distancia focal de la lente. Una lente de distancia focal corta da como resultado un tamaño de punto pequeño y una alta densidad de potencia en el punto focal, lo que la hace ideal para cortar material. Sin embargo, sus desventajas son una profundidad de enfoque muy corta y un rango de ajuste limitado, lo que generalmente lo hace adecuado para el corte a alta velocidad de materiales delgados.
Para piezas más gruesas, un teleobjetivo con mayor profundidad focal es más adecuado para cortar, siempre que tenga suficiente densidad de potencia.
En la mayoría de los casos, la densidad de potencia más alta se encuentra en el punto focal, que suele estar justo en la superficie o ligeramente debajo de la superficie de la pieza al cortar. Mantener una posición relativa constante entre el punto focal y la pieza de trabajo es crucial para lograr una calidad de corte estable.
Es importante tener en cuenta que durante el funcionamiento, la lente puede calentarse debido a un enfriamiento insuficiente, lo que provoca que cambie la distancia focal. En tales casos, es necesario ajustar la posición focal de manera oportuna.
Gas auxiliar
Se rocía gas auxiliar a lo largo del mismo eje que el rayo láser para proteger la lente de la contaminación y eliminar la escoria fundida en el fondo del área de corte. Para materiales no metálicos y algunos materiales metálicos, se utiliza aire comprimido o un gas inerte para eliminar los materiales fundidos y evaporados y evitar una combustión excesiva en el área de corte.
Presión de gas auxiliar
La mayoría del corte por láser de metales utiliza un gas reactivo (oxígeno) para crear una reacción oxidativa exotérmica con el metal caliente. Este calor adicional puede aumentar la velocidad de corte entre 1/3 y 1/2.
Al cortar láminas delgadas a altas velocidades, se requiere una mayor presión de gas para evitar que la parte posterior del corte se adhiera a la escoria. Al cortar materiales más gruesos o a velocidades más lentas, la presión del gas se puede reducir según corresponda.
Potencia de salida del láser
La potencia del láser y la calidad del modo tendrán un impacto significativo en el corte. En el funcionamiento real, la potencia máxima suele establecerse para lograr una alta velocidad de corte o para cortar materiales gruesos.
Envuélvelo
El párrafo anterior describe la mayoría de los factores que pueden afectar los parámetros del efecto de corte. La siguiente tabla enumera valores típicos para los parámetros de corte. Estos valores no son específicos de ningún caso en particular, pero pueden usarse como referencia para determinar los parámetros de inicio correctos.
Valores típicos de los parámetros de corte de acero inoxidable DC030.
Espesor (mm) |
Longitud focal (pulgada) |
Posición de enfoque (mm) |
potencia del láser (W) |
Velocidad cortante (m/min) |
Presion del gas N2(barra) |
Diámetro de la boquilla (mm) |
Distancia de la boquilla al plato (mm) |
---|---|---|---|---|---|---|---|
1 | 5 | -0,5 | 3.000 | 28 | 10 | 1.5 | 0,5 |
dos | 5 | -1 | 3.000 | 8 | 10 | 1.5 | 0,5 |
3 | 5 | -dos | 3.000 | 4.75 | 15 | 1.5 | 0,5 |
4 | 7.5 | -3 | 3.000 | 3.8 | 17,5 | dos | 0,7 |
5 | 7.5 | -4 | 3.000 | 2.2 | 20 | dos | 0,7 |
6 | 10 | -5 | 3.000 | dos | 20 | 2.2 | 0,7 |
8 | 12.5/15 | -6 | 3.000 | 13 | 20 | 3 | 0,7 |
10 | 15 | -6 | 3.000 | 0,55 | 20 | 3 | 0,7 |
Valores típicos de los parámetros de corte de acero con bajo contenido de carbono DC030
Espesor (mm) |
Longitud focal (pulgada) |
Posición de enfoque (mm) |
potencia del láser (W) |
Velocidad cortante (m/min) |
Presion del gas O2(barra) |
Diámetro de la boquilla (mm) |
Distancia de la boquilla al plato (mm) |
---|---|---|---|---|---|---|---|
1 | 5 | 0 | 750 | 9 | 3.5 | 1 | 0,5 |
dos | 5 | -0,5 | 800 | 7 | 3 | 1 | 1 |
3 | 5 | -0,5 | 800 | 4 | 3 | 1 | 1 |
4 | 7.5 | dos | 3.000 | 4.2 | 0,7 | 1 | 1 |
6 | 7.5 | dos | 3.000 | 3.3 | 0,7 | 1.2 | 1 |
8 | 7.5 | dos | 3.000 | 2.3 | 0,7 | 1.5 | 1 |
10 | 7.5 | dos | 3.000 | 1.8 | 0,7 | 1.5 | 1 |
12 | 7.5 | dos | 3.000 | 1.5 | 0,7 | 1.5 | 1 |
15 | 7.5 | dos | 3.000 | 1.1 | 0,7 | dos | 1 |
20 | 7.5 | 2.5 | 3.000 | 0,7 | 0,7 | 2.4 | 1 |
Valores típicos de parámetros de corte para acero DC025A1Mg3N2
Espesor (mm) |
Longitud focal (pulgada) |
Posición de enfoque (mm) |
potencia del láser (W) |
Velocidad cortante (m/min) |
Presion del gas O2(barras) |
Diámetro de la boquilla (mm) |
Distancia de la boquilla al plato (mm) |
---|---|---|---|---|---|---|---|
dos | 7.5 | -2.5 | 2500 | 45-6,5 | 10-12 | 1.5 | ≥1,0 |
3 | 7.5 | -3.5 | 2500 | 3.0-4.0 | 12-15 | 1.5 | ≥1,0 |
4 | 7.5 | -5.0 | 2500 | 1,5-2,0 | 12-16 | 2.0 | ≥1,0 |
5 | 7.5 | -5.0 | 2500 | 0,9-1,0 | 12-16 | 2.0 | ≥1,0 |
Las siguientes fotografías muestran el corte de láminas de acero al carbono de 15 mm y de acero inoxidable de 8 mm a diferentes distancias focales.
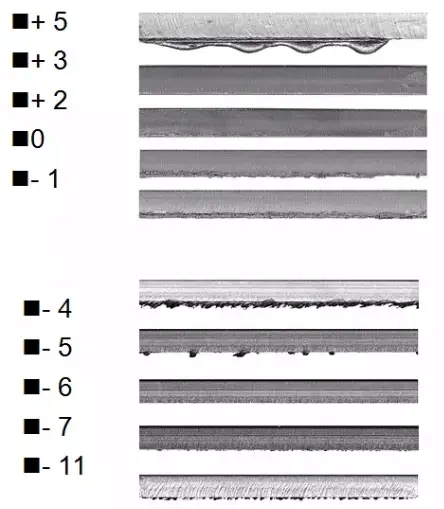