Debido al aumento de los costes laborales y la creciente demanda de productos de alta calidad en la industria de procesamiento de chapa, el margen de beneficio para el procesamiento de chapa se ha reducido.
Cada vez es más difícil aumentar la eficiencia y, en algunos casos, la producción puede incluso provocar pérdidas.
Las empresas de fabricación de chapa están recurriendo a la robótica o a equipos automatizados para sustituir la mano de obra, con el objetivo de reducir los costes de procesamiento y mejorar la eficiencia.
Aunque algunas empresas han implementado con éxito esta estrategia, han tenido que pagar un coste considerable.
Sin embargo, después de que la mayoría de las empresas comenzaron a utilizar robots y equipos de automatización, descubrieron que no sólo no podían lograr los resultados deseados, sino que también enfrentaban problemas de averías en los equipos.
Durante la visita, el cliente abrió la puerta para recibir sus pedidos.
La razón principal por la que la mayoría de los robots o equipos de automatización están inactivos no es que sean difíciles de usar o no puedan usarse, sino que las empresas de chapa metálica no pueden analizar a fondo el proceso y la producción de sus productos. Antes de comprar robots o equipos de automatización, no comprenden el rendimiento y las limitaciones del equipo.
Para realizar una venta, los vendedores de equipos de automatización tienden a exagerar el rendimiento del equipo. En consecuencia, las empresas compradoras asumen erróneamente que el equipo de automatización que compran es capaz de cualquier cosa.
Sin embargo, una vez que los equipos de automatización se ponen en producción, sólo el 30% de los productos se pueden producir automáticamente, mientras que el 70% restante aún requiere producción manual. Como resultado, la tasa de utilización de los equipos de automatización es muy baja.
Es fundamental analizar cuidadosamente el proceso y el lote del producto de la empresa y evaluar el rendimiento y las limitaciones de los equipos de automatización antes de adoptarlos. Esto se debe a que incluso el equipo de automatización más avanzado tiene sus limitaciones.
En conclusión, debemos compartir la inversión y selección de equipos de automatización de procesos de chapa, teniendo en cuenta la importancia de analizar el proceso y la producción del producto y evaluar el rendimiento y las limitaciones de los equipos de automatización antes de comprarlos.
proceso de borrado
Actualmente, el principal equipo para el corte son las máquinas de corte por láser y las punzonadoras CNC. Son máquinas CNC sofisticadas y con un alto grado de inteligencia.
Incorporando dispositivos automáticos de carga y descarga se puede conseguir una producción totalmente automática.
Selección de carga y descarga del láser.
La ventosa voladiza forma parte de un dispositivo de alimentación semiautomático económico y adecuado para alimentar placas delgadas con un espesor inferior a 5 mm y un peso inferior a 20 kg.
Sin embargo, utilizar el método voladizo semiautomático para alimentar placas gruesas sería un desafío para empujar manualmente la ventosa y, por lo tanto, no se recomienda.
El dispositivo de alimentación automática tipo pórtico es ideal para alimentar placas gruesas y grandes, garantizando seguridad y alta eficiencia.
Sin embargo, no se recomienda utilizar el dispositivo automático para la supresión láser automática, ya que el procesamiento láser se utiliza principalmente para lotes pequeños y trabajos de diversas variedades, y la supresión automática puede reducir la eficiencia del procesamiento.
Para lotes de producción grandes, se recomienda utilizar una línea de producción de corte de bobinas por láser para ahorrar materiales y lograr una alta eficiencia de procesamiento.
Selección de espacios en blanco y carga NC
Las ventajas del dispositivo de carga y descarga automática unilateral son:
La carga y descarga se realizan por el mismo lado y un único ciclo de carga y descarga dura entre 35 y 40 segundos.
La superficie útil del almacén es reducida.
El almacén de materiales se puede ampliar y añadir capacidad de almacenamiento adicional sin aumentar el área útil.
Las ventajas de los dispositivos automáticos de carga y descarga por ambos lados son:
La eficiencia de carga y descarga es mayor en comparación con la de un solo lado.
El ciclo de carga y descarga se puede completar en 16 a 20 segundos, pero requiere un área relativamente grande, lo que lo hace adecuado para empresas de chapa con ubicaciones ilimitadas.
Para más de 3 prensas CNC se recomienda añadir dispositivos de carga y descarga automática.
En un caso, una sola persona puede operar tres prensas CNC con dispositivos automáticos de carga y descarga, y un turno puede reducir de 3 a 4 operadores, lo que reduce la intensidad de trabajo de los operadores y libera trabajos mecánicos repetitivos de carga y descarga.
Los operadores tendrán más tiempo para considerar la preparación previa al procesamiento, como la preparación de matrices, la preparación de materiales y la optimización de los procedimientos de procesamiento, lo que mejorará significativamente la eficiencia del procesamiento.
El dispositivo automático de carga y descarga de punzonado NC es un esquema maduro.
Proceso de entrenamiento
Presione el freno formando
Las plegadoras se utilizan en el 98% de las fábricas de conformado de chapa. Este equipo requiere una inversión mínima y puede utilizarse para fines de procesamiento general. Sin embargo, el funcionamiento manual es un requisito, lo que constituye su única desventaja.
Al procesar piezas con una longitud o ancho superior a 50 mm, una persona puede tener dificultades para operar la máquina y se requiere que al menos dos trabajadores cooperen en el procesamiento (ver Fig. 1).
Además, cuando se trabaja con láminas de espesor superior a 2 mm, la eficiencia de plegado es baja y es más probable que se produzcan accidentes industriales.
El trabajo de flexión es físicamente exigente y requiere tiempo para aprender y adquirir experiencia. Por tanto, el salario de este tipo de trabajo es superior al de otros tipos de trabajo.
Para reducir los costes laborales se utilizan dos esquemas de automatización: plegado robótico y plegado servoasistido.
(1) Doblado del robot.
Al depurar el equipo de esta manera, es posible lograr una producción completamente automática sin paradas.
El procesamiento a largo plazo es más eficiente que el procesamiento manual porque un solo personal de puesta en servicio puede operar varias máquinas dobladoras.
Sin embargo, una desventaja importante de este método es que requiere un largo tiempo de depuración y tiene requisitos relativamente altos para los operadores. Además, no es adecuado para procesar múltiples variedades y lotes pequeños, ya que diferentes productos requieren el reemplazo de la estructura de la ventosa.
Muchas empresas han invertido en el plegado robótico; Sin embargo, debido al tamaño de lote insuficiente de los pedidos de productos fijos, los operadores no están familiarizados con el proceso de depuración, lo que resulta en equipos inactivos.
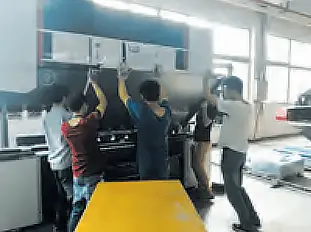
Fig.1 Flexión tradicional
(2) El doblado es ayudado por los seguidores de la hoja de cálculo (Figura 2).
Este método se puede utilizar para la producción de variedades múltiples, así como para la producción de lotes grandes y pequeños.
Las ventajas de doblar piezas de gran tamaño y chapas gruesas son obvias: reduce la necesidad de personal auxiliar para el plegado (Fig. 3), reduce la intensidad de la mano de obra y proporciona una gran flexibilidad.
Se puede utilizar un seguidor de una sola hoja con múltiples plegadoras y el costo de inversión es relativamente bajo.
La desventaja de este método es que se requieren operaciones de carga y descarga manuales y no se puede realizar completamente la producción automática.
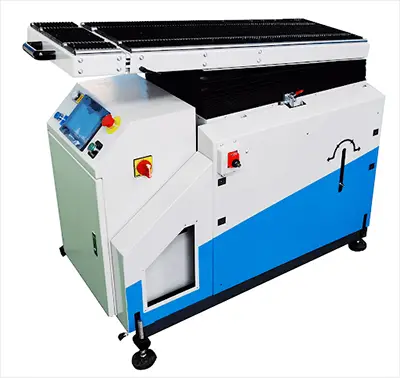
Fig. 2 Seguidor de hojas
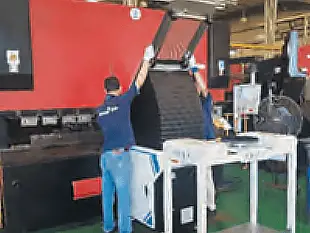
Fig.3 Doblado con seguidor de chapa
Dobladora de paneles
La paneladora presenta una alta eficiencia de procesamiento, lo que permite una producción totalmente automatizada y es adecuada para el procesamiento de chasis complejos.
Sin embargo, es importante resaltar que la máquina no fue diseñada para doblar láminas gruesas o productos con dobladillos mayores a 300 mm. Además, conlleva un alto coste de insumos y gastos de mantenimiento, haciéndolo inaccesible para las grandes fábricas.
La rentabilidad del procesamiento de chapa es baja, lo que dificulta recuperar la inversión inicial.
Proceso de sintonización
Los instaladores de chapa se dedican principalmente a actividades como taladrar, roscar y avellanar.
Ciertos productos de chapa requieren procesamiento de perfiles de aluminio, con pasos necesarios como evitar agujeros ciegos y agujeros de ojo de pez.
Los equipos de procesamiento convencionales empleados en este campo incluyen taladros de banco, máquinas roscadoras de mesa y fresadoras.
La operación de la línea de montaje manual tiene una mayor probabilidad de sufrir accidentes de calidad, como fugas en orificios y dientes.
Para piezas más complejas, es posible que se requieran varios procesos de roscado, escariado y escariado con diferentes especificaciones.
El procesamiento de equipos tradicionales es relativamente complicado, requiere coordinación entre varias personas y resulta en una baja eficiencia.
Para solucionar estos problemas, muchas empresas de chapa utilizan centros de taladrado, roscado y fresado (Fig. 4).
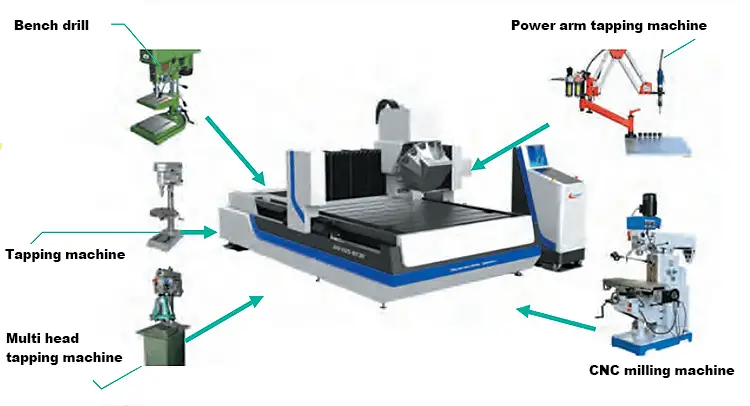
Fig.4 Centro de taladrado y roscado
Un centro de taladrado, roscado y fresado es un tipo de equipo de control numérico que integra las funciones de las máquinas perforadoras, roscadoras y fresadoras. Cuenta con programación fuera de línea y cambio automático de herramientas con una biblioteca de herramientas multiestación.
Este equipo puede sujetar varias piezas simultáneamente y procesar automáticamente todos los procesos de perforación, roscado, fresado de espacios y otros procesos necesarios según el programa. Además, puede acoplar y desmontar piezas sin necesidad de detenerse, lo que resulta en una alta eficiencia (40-60 agujeros por minuto). Además, también puede procesar productos de radiadores perfilados.
Sin embargo, una de las desventajas de este equipo es que requiere programación y herramientas, lo que lo hace inadecuado para probar o procesar muestras de productos.
Proceso de soldadura y rectificado.
No profundizaremos en la soldadura con manipuladores al ser una técnica de automatización muy consolidada.
El rectificado constituye el cuello de botella del proceso para la mayoría de las empresas de chapa.
El proceso de rectificado es esencial para el procesamiento de chapa, pero es una tarea laboriosa, sucia y desagradable que se lleva a cabo en un entorno desafiante.
Contratar trabajadores calificados en molienda es un desafío importante.
La mayoría de los trabajadores de las fábricas están en el grupo de edad de más de 60 y 70 años y es difícil atraer a gente más joven al trabajo. Como resultado, el coste laboral de la molienda sigue siendo elevado.
En un intento por resolver este problema, algunas empresas de chapa han experimentado con el pulido robótico, aprovechando la experiencia adquirida con la automatización del pulido de hardware. Sin embargo, la mayoría de estos intentos terminaron en fracaso.
Le recomendamos la estación de trabajo de rectificado CNC de cinco ejes relativamente madura (Figura 5). Este equipo se utiliza para pulir cicatrices de soldadura en la superficie de piezas de chapa metálica, adecuado para pulir y pulir la superficie de cajas, gabinetes, paneles de puertas y piezas estructurales internas.
Esta máquina se utiliza principalmente en equipos de comunicación, equipos eléctricos, equipos médicos, equipos de protección ambiental, bastidores de equipos electrónicos, seguros corporales e industrias relacionadas, reemplazando el rectificado manual tradicional y mejorando la eficiencia del procesamiento de fábrica, acortando el tiempo de procesamiento de chapa.
La estación de trabajo tiene movimiento manual de materiales, con la pieza fijada en la mesa, y el servo X/Y/Z/B/C se posiciona y gira, lo que mejora enormemente la precisión y velocidad de respuesta del equipo. La plataforma utiliza un riel guía roscado de gran diámetro, que garantiza la precisión y mejora la estabilidad del banco.
El sistema CNC de 5 ejes, combinado con el servicio de autobús y la tecnología de enseñanza manual inteligente, resuelve el problema de la programación profesional en empresas de chapa y reduce los requisitos de habilidades de los operadores. Es sencillo, rápido y tiene gran puntualidad en la transformación del producto.
Una de sus desventajas es que no es adecuado para rectificar productos en lotes pequeños y es necesario fabricar accesorios para herramientas (los accesorios para herramientas de rectificado son relativamente simples y de bajo costo). Además, el interior y las esquinas pequeñas de algunos productos no se pueden pulir.
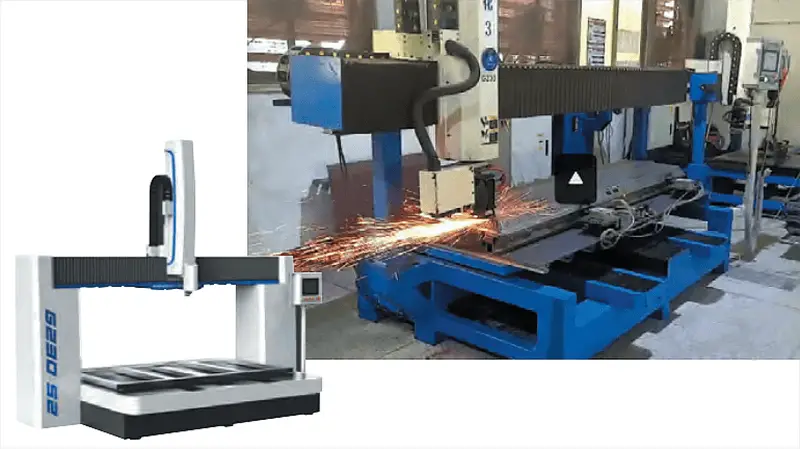
Fig. 5 Estación de trabajo de rectificado de cinco ejes
Conclusión
La selección de equipos de automatización de chapa no tiene por qué ser costosa.
Si bien los equipos de automatización importados pueden no ser fáciles de usar, la opción más barata puede que tampoco sea la más fácil de usar.
Las empresas de chapa deben seleccionar los equipos de automatización en función de las características de sus propios productos, lo que añade valor.