1. Introducción
En la fabricación de tubos de escape de automóviles y piezas tubulares similares, a menudo se producen problemas de calidad como arrugas o desgarros debido a factores como el radio de curvatura y las propiedades del material. Es particularmente crucial reducir o eliminar estos problemas para mejorar la calidad del producto y reducir las tasas de desperdicio.
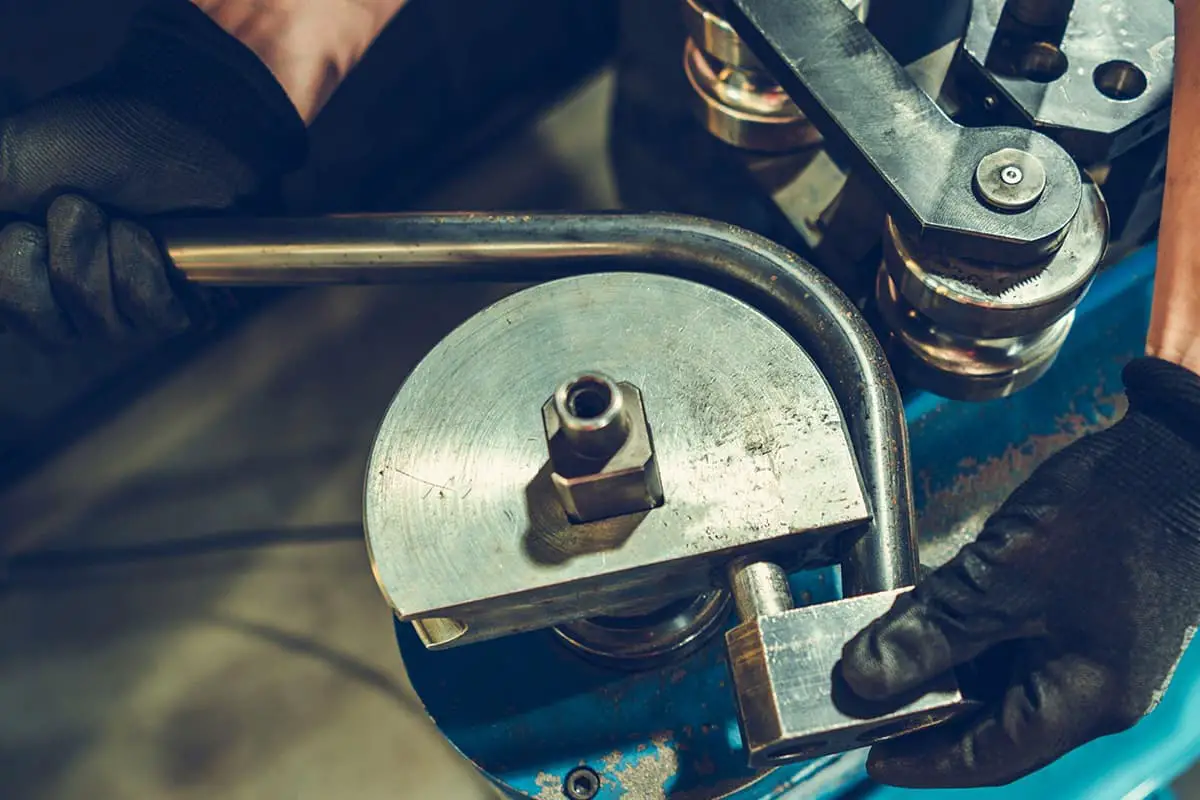
El proceso de curvado de los tubos es comparable al de la chapa metálica: la pared exterior de la capa neutra se somete a tensiones de tracción, lo que adelgaza la pared, mientras que la pared interior de la capa neutra se somete a tensiones de compresión, lo que engrosa la pared. Una deformación excesiva puede provocar grietas en la pared exterior y arrugas en la pared interior. La Tabla 1 presenta los radios de curvatura mínimos para tubos de acero.
Tabla 1: Radio mínimo de curvatura (R) para tubos de acero
![]() |
espesor de pared | Radio de curvatura mínimo R |
0.02D | 4D | |
0.05D | 3.6D | |
0.10D | 3D | |
0,15D | 2D |
Los métodos para doblar tuberías generalmente incluyen: doblar con herramientas manuales para doblar tuberías; curvado con máquinas curvadoras de tubos específicas; método de flexión antideformación; doblado por extrusión en frío; prensado de moldes para formar codos; Doblado por extrusión en caliente de la varilla central. Este artículo se centra principalmente en el uso de máquinas dobladoras de tubos dedicadas como ejemplos para analizar problemas de arrugas y desgarros.
dos . El proceso de doblar tubos utilizando una máquina dobladora de tubos dedicada.
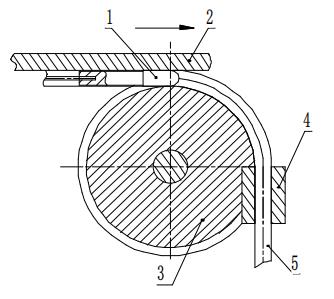
1. mandril
2. Placa guía
3. morir
4. Bloque de presión
5. Componente del tubo
La dobladora de tubos dedicada normalmente utiliza un mandril para doblar. El proceso implica ensamblar la matriz, elemento 3, en un husillo giratorio de la máquina. Antes de doblar el tubo, se fija en la matriz mediante el bloque de presión, elemento 4. Se inserta un mandril, elemento 1, en el tubo. Cuando se pone en marcha la máquina, el material del tubo se curva gradualmente alrededor de la matriz para tomar forma.
3. Análisis de elementos de control y métodos de control correspondientes
3.1 Radio de curvatura
Durante el proceso de curvado, un radio de curvatura más pequeño puede provocar arrugas en el lado interior o incluso grietas en la pared exterior. El diseño debe tener en cuenta el espesor de la pared de la tubería, el diámetro exterior y las propiedades del material. Se debe consultar la Tabla 1 al elegir el radio de curvatura.
Empíricamente, cuando se utiliza un mandril cilíndrico normal para doblar, el radio mínimo de curvatura puede ser ligeramente menor que el indicado en la Tabla 1, siempre que no provoque arrugas o grietas. Cuando se requiere un radio de curvatura más pequeño, se puede aumentar el espesor de la pared del tubo, reducir el diámetro exterior y se debe seleccionar un material con buena ductilidad y un exterior liso.
3.2 Forma del portabrocas y posición de sujeción
3.2.1 Posición de trabajo del portabrocas
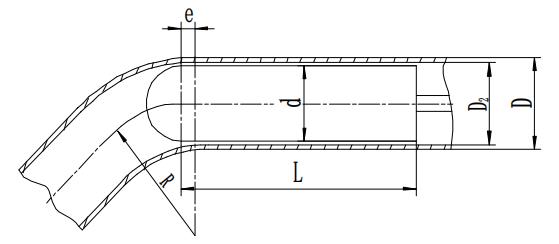
En el doblado de núcleos de tubos, la forma y la posición operativa del mandril tienen un impacto significativo en la calidad del doblado de tubos. Normalmente, el diámetro d del mandril debe ser entre 0,5 y 1,5 mm más pequeño que el diámetro interior del tubo, lo que facilita su inserción en el tubo.
La distancia e desde el punto donde el mandril ingresa al tubo hasta el inicio del proceso de doblado (ver Figura 2) se puede calcular usando la siguiente fórmula empírica.
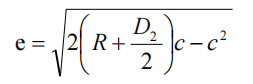
En la ecuación,
- e – la distancia donde el mandril comienza a doblarse dentro del tubo
- R – el radio de curvatura de la capa central de la sección transversal
- D2 – el diámetro interno del tubo
- c – la holgura entre el diámetro interno del tubo y el mandril. Normalmente, c se elige entre 0,5 y 1,5 mm.
3.2.2 Selección de la forma del mandril
Hay varias formas de mandriles, que se dividen aproximadamente en: mandriles cilíndricos estándar, mandriles de cuchara, mandriles de alambre y mandriles de eje flexible. El mandril cilíndrico estándar se utiliza a menudo debido a su estructura simple, facilidad de fabricación y fácil extracción después de doblarlo.
Sin embargo, dado que el área de contacto entre el mandril y la pared del tubo es pequeña, es menos eficaz para impedir la creación de una forma elíptica.
La longitud del mandril, indicada como L, debe ser (ver Fig. 2)
L = (3 a 5) d mm
Cuando el diámetro d del mandril es grande, el coeficiente asume un valor menor y viceversa.
3.2.3 Comprobación del espacio libre entre el mandril y la pared interior de los accesorios de tubería
Si el espacio entre el mandril y la pared interior de los accesorios de tubería es demasiado grande, al comienzo del proceso de doblado, el mandril y la pared de la tubería no se tocan completamente, lo que provoca arrugas severas en el lado interior de los accesorios de tubería. y la aparición de curvas muertas. Si el espacio es demasiado pequeño, al fijar una tubería soldada normal, la altura desigual de la soldadura en la pared interior de la conexión de la tubería puede dificultar la inserción del mandril en la conexión de la tubería.
Tras un largo período de resumen del trabajo de doblado de tubos, el autor determinó una holgura más adecuada entre la pared interior del tubo y el mandril:
c = D2 – d = 0,5 a 1,5 mm.
3.3 Ajuste de velocidad de la placa guía
En operaciones estándar de doblado de tubos en plegadoras, las placas guía (Figura 1) sujetan la pieza de trabajo y se mueven en sincronía con ella. La velocidad de esta placa guía es regulable y su velocidad de movimiento influye directamente en la calidad del tubo doblado.
La pieza de trabajo, fijada por el bloque de prensa en la matriz, contiene un mandril en su interior. A medida que la máquina funciona, el material del tubo se curva gradualmente alrededor de la matriz, y la placa guía avanza en sincronía con la velocidad de la matriz. Durante este proceso actúa sobre la pieza de trabajo una fricción estática entre la placa guía y la pieza de trabajo.
Si la velocidad de la placa guía es mayor que la de la matriz, transmite un empuje hacia adelante a la pieza de trabajo; por el contrario, aplica una fuerza de resistencia si su velocidad es menor. Las pruebas de flexión muestran que, en igualdad de condiciones, si la velocidad de la placa guía excede sustancialmente la velocidad lineal de la matriz, tienden a formarse arrugas en la pared interior del tubo.
Por otro lado, si la velocidad de la placa guía se retrasa significativamente, la pared exterior del tubo se volverá notablemente más delgada, hasta el punto de romperse. Por lo tanto, ajustar eficazmente la velocidad de empuje de la placa guía para que coincida con la velocidad del troquel es crucial para garantizar la calidad del plegado.
De este análisis, queda claro que la velocidad de empuje de la placa guía debe sincronizarse con la velocidad de flexión durante el proceso de flexión. Por lo tanto, antes de doblar o después de cambiar a una matriz con un radio de curvatura diferente, es necesario ajustar la velocidad de la placa guía en consecuencia.
Como se muestra en la Figura 1, la velocidad de curvatura α y el radio de curvatura R están predefinidos. Se calcula la longitud del arco que debe girar la matriz de curvado, es decir, la distancia que la placa guía debe avanzar de forma sincrónica al mismo tiempo. La plegadora está inactiva mientras el operador gira lentamente la palanca de la válvula de control de velocidad, observando cómo se mueve la placa guía.
Después de doblar hasta el ángulo establecido y detenerse, se mide el desplazamiento real de la placa guía con una regla, comparándolo con el cálculo teórico. Si son diferentes, se puede repetir el ajuste del ralentí hasta que el valor medido coincida con el valor calculado.
En realidad, debido a factores de carga, la velocidad de movimiento de la placa guía durante la flexión real es muchas veces más lenta que durante el ralentí. Por lo tanto, al ajustar la velocidad de empuje de la placa guía, el valor real puede ser ligeramente superior al valor teórico.
4. Conclusión
En conclusión, la presencia de arrugas, desgarros o deformidades elípticas en el tubo es una medida importante de la calidad del doblez.
Estos defectos de calidad se pueden minimizar seleccionando un radio de curvatura adecuado, una forma de mandril adecuada, controlando la holgura entre el mandril y la pared interior del tubo, ajustando la posición de inserción del mandril y la velocidad de movimiento de la placa guía.