Las piezas forjadas de tipo I son piezas comunes en la industria de la perforación petrolera, incluidos dispositivos de boca de pozo, árboles petrolíferos, equipos de estrangulación y presión, y existe una gran demanda en el mercado para ellas.
La forma de este tipo de forjado tiene las siguientes características: los dos extremos de la brida y el cilindro intermedio son coaxiales, y existe una diferencia de diámetro entre la brida y el cilindro intermedio de conexión.
Estado y análisis del proceso de forja.
El proceso de producción actual comúnmente utilizado para piezas forjadas en forma de I implica dos pasos:
(1) El proceso de producción comienza forjando directamente piezas forjadas cilíndricas grandes en función de las dimensiones aproximadas del diámetro de la brida del producto. Estas grandes piezas forjadas cilíndricas luego se procesan mediante mecanizado.
(2) Además del proceso anterior, se utiliza un proceso simbólico de tracción y estiramiento para formar la pequeña parte cilíndrica central.
Sin embargo, ambos procesos tienen las siguientes deficiencias:
- Bajo uso de materias primas, que en casos extremos puede ser inferior al 50%. Para los productos estudiados en este artículo, la tasa de utilización de materia prima utilizando el proceso de forjado libre directo fue solo del 74% como máximo.
- Grandes cantidades de repuestos para procesamiento y altos costos de procesamiento, lo que resulta en altos costos de producción y baja rentabilidad del producto.
- Ciclo de producción largo y bajo índice de satisfacción del cliente.
En este artículo, nos centramos en el tipo de forja. Nuestro objetivo es romper las limitaciones del proceso productivo tradicional y evitar los problemas mencionados anteriormente, con el fin de reducir los costos de producción, adaptarnos a los ritmos del mercado y aumentar la competitividad del mercado.
Nos centramos principalmente en la forma de dichas piezas forjadas, empezando por el diseño de troquel dividido y utilizando el proceso de forjado de troqueles de neumáticos para la producción para lograr la precisión dimensional de las piezas forjadas.
Flujo de proceso de piezas forjadas en forma de I.
Debido a que estas piezas forjadas se producen principalmente en lotes pequeños y medianos, se fabrican mediante el proceso de forjado con matriz.
Debido a las excesivas inversiones en ropa de trabajo y los altos costos de producción, mejorar la competitividad del mercado se ha convertido en un desafío. Por lo tanto, se está considerando un análisis exhaustivo. La investigación sobre el proceso de producción de troqueles divididos puede proporcionar beneficios dobles, como la precisión en los productos forjados y la producción de múltiples lotes pequeños de neumáticos forjados.
El diagrama de flujo del proceso específico se ilustra en la Figura 1.
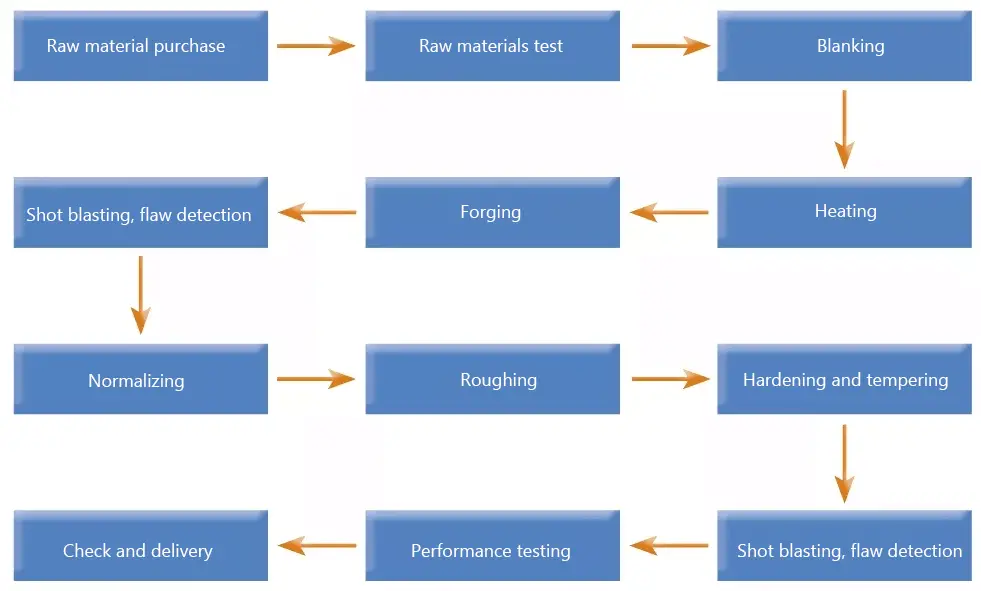
Figura 1: Diagrama de flujo del proceso
Diseño de forja
Las piezas en forma de I recientemente desarrolladas pesan 101,96 kg de masa y 154 kg de forjado. El cálculo del proceso de forja indica un factor de complejidad S de 0,53.
Como el proceso de forjado libre ya pertenece a la clase compleja de forjados, el diseño de matriz dividida requiere estándares más altos.
Utilizando el diagrama de piezas proporcionado por el usuario, se crean piezas forjadas según el nuevo plan de proceso. Este plano acerca el proceso de forjado al equilibrio, lo que da como resultado una alta precisión dimensional. La Figura 2 muestra los diagramas de piezas y forjado.
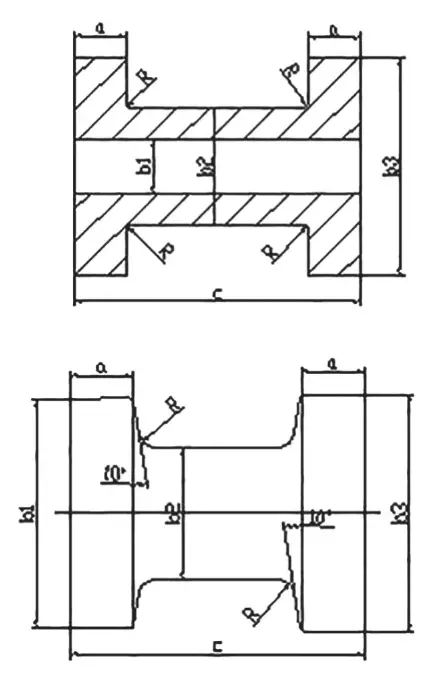
Figura 2 Diagrama de piezas y forjados.
Desarrollo del proceso de forja
El plan de producción para el proceso de forjado es el siguiente: primero, se estira el tocho y luego se forma la brida cortando un extremo de la matriz del neumático, seguido de formar la otra brida utilizando la combinación del inserto de partición y del troquel del tubo exterior.
Este proceso de forjado garantiza que el primer proceso de recalcado sirva como proceso de moldeo para el segundo proceso de recalcado, permitiendo así controlar las excentricidades de las piezas forjadas y la precisión dimensional de las piezas en bruto.
Después de cálculos cuidadosos, se determinó que la calidad de las piezas forjadas y la calidad del troquel de corte combinadas pesan más de 600 kg. Por lo tanto, para garantizar resultados óptimos durante el proceso final de forjado del troquel de corte, se debe utilizar un martillo de forjado libre de 3 toneladas como equipo de forjado.
Diseño de molde
Base de diseño de molde de neumático, inserto dividido y molde de manga
Base de diseño del molde de neumáticos: diagrama de forjado en frío → piezas de forjado en caliente → molde de neumáticos. Las dimensiones de las piezas forjadas en caliente se calculan según la fórmula (1).

En la fórmula, Lt representa el tamaño de forja a la temperatura final de forja (mm); L indica el tamaño de la pieza forjada en frío (mm); α representa el coeficiente de expansión de la línea de material (1/C); t representa la temperatura final de forjado (°C).
Para materiales de forja en la industria petrolera, principalmente AISI4130 y 410SS, la temperatura de forja inicial es generalmente de 1150 °C y la temperatura de forja final es de 860 °C o más. Como este proceso de forjado es relativamente largo y la temperatura final de forjado es baja, la tasa de contracción en frío se reduce adecuadamente a 1,2% - 1,4%.
El diseño del subempaque se basa en el proceso de diseño del molde del neumático, con énfasis en el ensamblaje del molde de manga durante el proceso de diseño. Este enfoque ayuda a evitar situaciones en las que el montaje sea imposible o difícil.
Diseño de moldes de neumáticos y molde dividido.
Con base en el proceso de producción de forjado establecido, el molde de llanta (como se muestra en la Figura 3), los insertos divididos (como se muestra en la Figura 4) y el molde de manga (como se muestra en la Figura 5) se diseñaron incorporando los elementos del diseño del molde de llanta. .
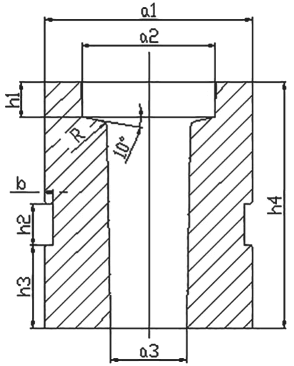
Figura 3 Molde de neumático
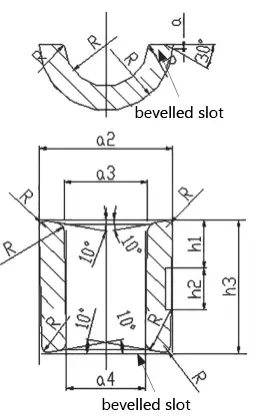
Figura 4 Inserto dividido
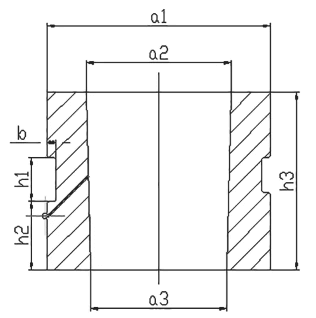
Patrón de manga figura 5
La Figura 3 muestra el primer troquel de asentamiento, que requirió un cálculo preciso del peso de la pieza forjada durante la fase de diseño inicial. De lo contrario, se puede producir un relleno posterior durante el forjado libre después del recalcado.
Los insertos divididos se ilustran en la Figura 4. El diseño debe tener en cuenta que el inserto dividido se ubica en el cilindro intermedio de la pieza forjada después del conformado por forjado. Para facilitar la extracción, se hace una ranura biselada en la interfaz del troquel partido. Esta ranura permite una fácil extracción del inserto dividido después de forjar.
Paralelamente se llevó a cabo un proyecto de optimización local. El diseño de la cara extrema en contacto con el interior de la brida estaba inclinada 10°. El chaflán interno era de R20 mm y el chaflán de contacto entre la parte externa y la segunda matriz del manguito torneado era de R15 mm.
La pendiente general del exterior del molde es la misma que la pendiente de la cavidad interior del molde de sujeción que se muestra en la Figura 3. El diámetro se reduce en 1 mm en un lado para facilitar la colocación en la cavidad del modelo de manga que se muestra en Figura 5 .
El troquel del manguito, que se muestra en la Figura 5, está diseñado para garantizar el tamaño de la brida después del prensado. Los tamaños A2 y A3 están diseñados para el tamaño de la pieza forjada en caliente, con una transición de la cavidad sin pendiente. La Figura 6 muestra una matriz dividida compuesta con inserciones divididas y módulo de manguito.
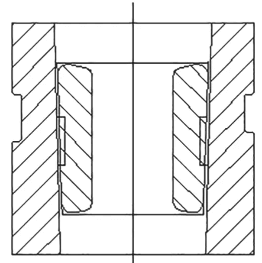
Figura 6 Matriz dividida
El molde del neumático se combina y se forja utilizando 3TZ, lo que genera una fuerza de rodadura significativa durante el proceso de forjado. En consecuencia, en la fase de diseño, el espesor del molde del guante se incrementa globalmente para compensar esto.
Conclusión
Después de verificar la producción real de lotes pequeños, el plan del proceso de forjado con matriz dividida demuestra ser exitoso y factible. También tiene la capacidad de garantizar el proceso de producción en masa.
Este artículo presenta un nuevo método de proceso para producir piezas forjadas en forma de I, que ahorra un 23 % de materia prima en comparación con la forja libre directa. El nuevo esquema produce efectivamente piezas forjadas en forma de I que cumplen con el valor objetivo del proceso deseado.
Las piezas forjadas realizadas con este método exhiben el mismo nivel de tecnología que la forja con matriz. En comparación con la forja con troquel o la forja libre directa, este proceso ahorra entre un 20% y un 40% de materias primas, reduce los costos de producción y aumenta la flexibilidad del proceso.