Perforación
Se realizan diversos procesos de corte, taladrado, escariado o avellanado utilizando diferentes tipos de brocas.
La perforación es un proceso de corte que produce agujeros utilizando brocas helicoidales, brocas planas o brocas centrales en materiales sólidos para crear agujeros pasantes o ciegos.
El escariado aumenta el diámetro de un orificio preexistente en una pieza de trabajo utilizando una broca avellanadora.
El avellanado se realiza utilizando una broca de avellanado en un extremo del orificio preexistente para producir avellanados, orificios cónicos, planos parciales o formas esféricas, que se utilizan para instalar sujetadores.
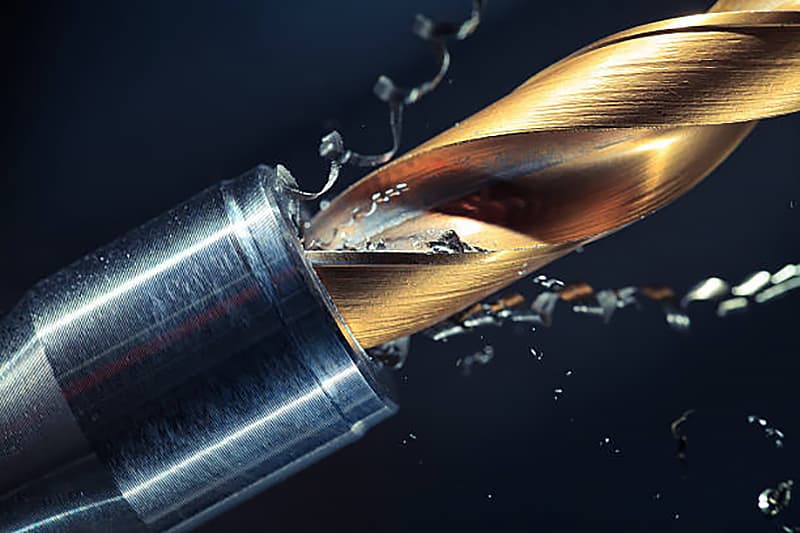
Durante el proceso de perforación, una broca helicoidal tiene dos filos de corte principales y un borde transversal, comúnmente denominado "una punta (centro de la broca) y tres hojas", que participan en el corte.
La broca helicoidal funciona en un estado semicerrado, donde el borde transversal está fuertemente comprimido y la eliminación de viruta es difícil. Por lo tanto, las condiciones de procesamiento son más complejas y desafiantes que el torneado u otros métodos de corte, lo que resulta en una menor precisión de procesamiento y superficies más rugosas.
La precisión de perforación de materiales de acero es generalmente IT13-10, con una rugosidad superficial de Ra20-1,25μm, mientras que la precisión de escariado puede alcanzar IT10-9, con una rugosidad superficial de Ra10-0,63μm.
La calidad y eficiencia del proceso de perforación depende en gran medida de la forma del filo de la broca.
En la producción, la forma y el ángulo del filo de una broca helicoidal a menudo se cambian mediante el afilado para reducir la resistencia al corte y mejorar el rendimiento de la perforación. La broca del grupo China es un ejemplo de broca helicoidal producida con este método.
Cuando la relación entre la profundidad (l) y el diámetro (d) de un orificio perforado es mayor que seis, generalmente se considera perforación profunda. La broca utilizada para perforaciones profundas es delgada y tiene poca rigidez. Durante la perforación, la broca está sujeta a deflexión y fricción con la pared del agujero, lo que dificulta el enfriamiento y la eliminación de viruta.
Por lo tanto, cuando la relación l/d es superior a 20, se requiere una broca de orificio profundo especialmente diseñada y se utiliza un fluido de corte con un cierto caudal y presión para enfriar y lavar la viruta para obtener resultados de perforación de alta calidad con alta eficiencia. . .

La parte cortante del taladro plano tiene forma de pala y su estructura es simple y tiene bajos costos de fabricación. El fluido de corte se puede introducir fácilmente en el agujero, pero su rendimiento de corte y eliminación de viruta es deficiente. Los taladros planos se pueden dividir en dos tipos: integrales y montados.
El tipo integral se utiliza principalmente para perforar microagujeros con un diámetro de 0,03 mm a 0,5 mm. Los taladros planos montados tienen cuchillas reemplazables y pueden enfriarse internamente. Se utilizan principalmente para perforar agujeros grandes con un diámetro de 25 mm a 500 mm.
Las brocas profundas generalmente se refieren a herramientas que tienen una relación entre profundidad y diámetro del orificio superior a 6. Las brocas profundas de uso común incluyen perforadoras de pistola, perforadoras profundas BTA, perforadoras de chorro, perforadoras profundas DF, etc. Se utiliza para el procesamiento de agujeros profundos.
Las fresas tienen de 3 a 4 dientes y son más rígidas que las brocas helicoidales. Se utilizan para agrandar los agujeros existentes y mejorar la precisión y suavidad del procesamiento.
Las brocas avellanadas tienen múltiples dientes y se utilizan para dar forma al extremo de los orificios, como orificios avellanados para varios tipos de tornillos avellanados o para nivelar la superficie del extremo exterior de los orificios.
Las brocas centrales se utilizan para perforar orificios centrales en piezas tipo eje. Básicamente, se componen de brocas helicoidales y brocas avellanadoras con ángulos de hélice muy pequeños y también se denominan brocas centrales compuestas.
La aplicación del taladro parabólico en el mecanizado de agujeros profundos.
Cuando el personal de procesamiento mecánico elige una broca para una tarea específica de procesamiento de orificios, primero se debe considerar la profundidad del orificio procesado. Cuanto más profundo sea el orificio procesado, más virutas deberán descargarse durante el proceso de mecanizado.
Si las virutas generadas durante el procesamiento no se pueden descargar de manera oportuna y efectiva, pueden bloquear la ranura de extracción de virutas de la broca, retrasando así el proceso de mecanizado y, en última instancia, afectando la calidad del procesamiento del orificio.
Por lo tanto, la eliminación eficaz de virutas es un factor clave para completar con éxito la tarea de procesamiento de agujeros de cualquier material.
La relación longitud-diámetro de las brocas.
Cuando el personal de procesamiento elige el tipo de broca más adecuado para una tarea específica de procesamiento de orificios, debe calcular la relación longitud/diámetro de la broca.
La relación longitud-diámetro es la relación entre la profundidad del orificio procesado y el diámetro de la broca. Por ejemplo, si el diámetro de la broca es de 12,7 mm y la profundidad del orificio a mecanizar es de 38,1 mm, entonces su relación longitud-diámetro será 3:1.
Cuando la relación longitud-diámetro es de aproximadamente 4:1 o menos, la mayoría de las brocas helicoidales estándar pueden descargar suavemente las virutas cortadas desde la punta de la broca.
Sin embargo, cuando la relación longitud-diámetro excede el rango anterior, se requieren brocas para agujeros profundos especialmente diseñadas para lograr un mecanizado eficaz.
Dado que la relación longitud/diámetro del orificio procesado excede 4:1, es difícil para las brocas helicoidales estándar retirar las virutas del área de corte y descargarlas fuera del orificio. Las virutas bloquearán rápidamente la ranura de extracción de virutas del taladro.
En este punto, es necesario detener la perforación, retirar la broca del agujero, retirar las virutas de la ranura de extracción de virutas y luego reanudar la perforación para continuar cortando.
La operación anterior debe repetirse varias veces para lograr la profundidad de agujero requerida. Este método de perforación a menudo se denomina “perforación profunda”. El uso de “perforación profunda” para mecanizar agujeros profundos reducirá la vida útil de la herramienta, reducirá la eficiencia del mecanizado y afectará la calidad del agujero procesado.
Cada vez que la broca se retira del orificio para eliminar virutas y se reinserta en el orificio, puede desviarse de la línea central del orificio, lo que hace que el diámetro del orificio aumente más allá del rango de tolerancia de tamaño especificado.
Para resolver el problema del mecanizado de agujeros profundos, en los últimos años los fabricantes de brocas han desarrollado dos nuevos tipos de brocas para el mecanizado de agujeros profundos: brocas parabólicas ordinarias y brocas parabólicas de hoja ancha.
Taladro parabólico común
La ranura de eliminación de viruta de una broca parabólica tiene forma parabólica y se utiliza específicamente para la perforación continua de orificios profundos con una relación longitud-diámetro de hasta 15:1 y una dureza del material que no exceda los 25-26 HRC (incluidos los de baja calidad). acero), carbono, diversas aleaciones de aluminio, aleaciones de cobre, etc.).
Por ejemplo, una broca parabólica con un diámetro de 12,7 mm puede mecanizar con éxito una profundidad de agujero de hasta 190 mm.
Debido a su gran espacio de eliminación de virutas, un taladro parabólico común puede descargar virutas rápidamente al filo, lo que permite que ingrese más fluido de corte al área de corte, lo que reduce en gran medida la posibilidad de fricción de corte y soldadura de virutas.
Además, también reduce el consumo de energía, la carga de torsión y el impacto de corte durante el mecanizado.
El ángulo de hélice de una broca parabólica es de 36°-38°, que es mayor que el ángulo de hélice de una broca helicoidal estándar (28°-30°). El ángulo de la hélice puede indicar el grado de "giro" de la broca, y cuanto mayor sea el ángulo de la hélice, más rápida será la velocidad de la broca y la eliminación de viruta.
Otra característica de las brocas parabólicas comunes adecuadas para el mecanizado de agujeros profundos es que el núcleo de la broca es más grueso (el núcleo de la broca se refiere a la parte central de la broca que no ha sido rectificada después de formar la ranura de eliminación de viruta).
El núcleo de una broca helicoidal estándar representa aproximadamente el 20 % de toda la broca terminada, mientras que el núcleo de una broca parabólica puede representar aproximadamente el 40 % de toda la broca.
En la perforación profunda, un núcleo de perforación más grueso puede aumentar la rigidez de la broca y mejorar la estabilidad del proceso de perforación. La punta de la broca parabólica tiene una ranura, por lo que se puede utilizar un diámetro de núcleo de broca mayor. Además, puede evitar que la broca se desplace durante la fase de perforación inicial.
Las brocas parabólicas están hechas de acero de alta velocidad y se les puede recubrir la superficie para mejorar su rendimiento de corte.
Taladro parabólico de hoja ancha
Para satisfacer las necesidades de perforación profunda de materiales difíciles de mecanizar (como materiales endurecidos trabajados en frío), algunos fabricantes de herramientas han desarrollado taladros parabólicos de hoja ancha.
Muchas características de este tipo de broca son similares a las de las brocas parabólicas comunes, como un ángulo de hélice más grande (36°-38°) para una fácil extracción de viruta y un núcleo de broca más grueso para una mejor rigidez y estabilidad al mecanizar agujeros profundos.
La diferencia con los taladros parabólicos habituales está en la forma de la ranura para la eliminación de virutas y en el filo de la hoja. El borde de la hoja del taladro parabólico de hoja ancha realiza una transición suave a la ranura de eliminación de viruta, lo que hace que la punta de la broca sea más fuerte y rígida. Al mismo tiempo, las virutas se pueden descargar suavemente a través de la ranura de extracción de virutas.
Al taladrar profundamente, la alta temperatura provocada por la fricción puede provocar un ligero ablandamiento o recocido del filo de la broca, lo que acelera el desgaste. La capacidad de la punta de la broca para mantener la dureza durante el procesamiento se puede expresar como "dureza roja".
Los taladros parabólicos de hoja ancha generalmente están hechos de acero de alta velocidad y materiales de acero de cobalto de alta velocidad. Debido a la mayor dureza al rojo del acero rápido de cobalto, la vida útil de la herramienta es más larga y la resistencia al desgaste es mayor.
Recubrimientos de superficies de perforación
Los siguientes recubrimientos de superficie se usan comúnmente para taladros parabólicos comunes y taladros parabólicos de hoja ancha:
① Recubrimiento de nitruro de titanio (TiN): este recubrimiento puede mejorar significativamente la vida útil de las brocas y la calidad de los orificios procesados. En comparación con las brocas sin recubrimiento, las brocas con recubrimiento de TiN son más adecuadas para la perforación a alta velocidad de diversos materiales (especialmente varias piezas de acero).
② Recubrimiento de carbonitruro de titanio (TiCN): a la temperatura de corte adecuada, las brocas recubiertas de TiCN tienen mayor dureza, mayor tenacidad y mejor resistencia al desgaste que las brocas recubiertas de TiN. También son adecuados para la perforación a alta velocidad de diversos materiales (especialmente piezas de acero).
Sin embargo, deben usarse con precaución al procesar materiales metálicos no ferrosos porque el recubrimiento de TiCN tiene una alta afinidad química por los metales no ferrosos y es propenso a desgastarse.
③ Revestimiento de nitruro de aluminio y titanio (TiAlN): este revestimiento puede mejorar la vida útil de las brocas, especialmente en entornos de corte a altas temperaturas. Al igual que el recubrimiento de TiCN, el recubrimiento de TiAlN no es muy adecuado para procesar materiales metálicos no ferrosos.
Optimización de los parámetros de perforación.
En el mecanizado de agujeros profundos, para maximizar el rendimiento de corte de la broca, la velocidad de perforación y el avance deben optimizarse en función de la relación específica entre longitud y diámetro.
Cuando la relación longitud/diámetro del proceso de perforación es 4:1, la velocidad de corte debe reducirse en un 20% y la velocidad de avance debe reducirse en un 10%.
Cuando la relación longitud/diámetro es 5:1, la velocidad de corte debe reducirse en un 30% y la velocidad de avance debe reducirse en un 20%. Cuando la relación longitud/diámetro alcanza 6:1-8:1, la velocidad de corte debe reducirse en un 40%. Además, cuando la relación longitud/diámetro es 5:1-8:1, la velocidad de avance debe reducirse en un 20%.
Aunque el precio de una broca parabólica es de 2 a 3 veces mayor que el de una broca helicoidal estándar, su excelente rendimiento en el mecanizado de agujeros profundos (relación longitud-diámetro superior a 4:1) reduce significativamente el coste de cada agujero perforado. fabricación -La herramienta preferida por los técnicos mecánicos para procesar agujeros profundos.