I. Parámetros de materiales
1. Propiedades básicas del aluminio
El aluminio es de color blanco plateado y puede formar una película protectora de óxido en el aire húmedo para evitar la corrosión del metal. Tiene una densidad relativa de 2,7 g/cm 3 , un punto de fusión de 660 °C, un punto de ebullición de 2327 °C y es ligero. También tiene buena conductividad eléctrica y térmica, alta reflectividad y resistencia a la oxidación.
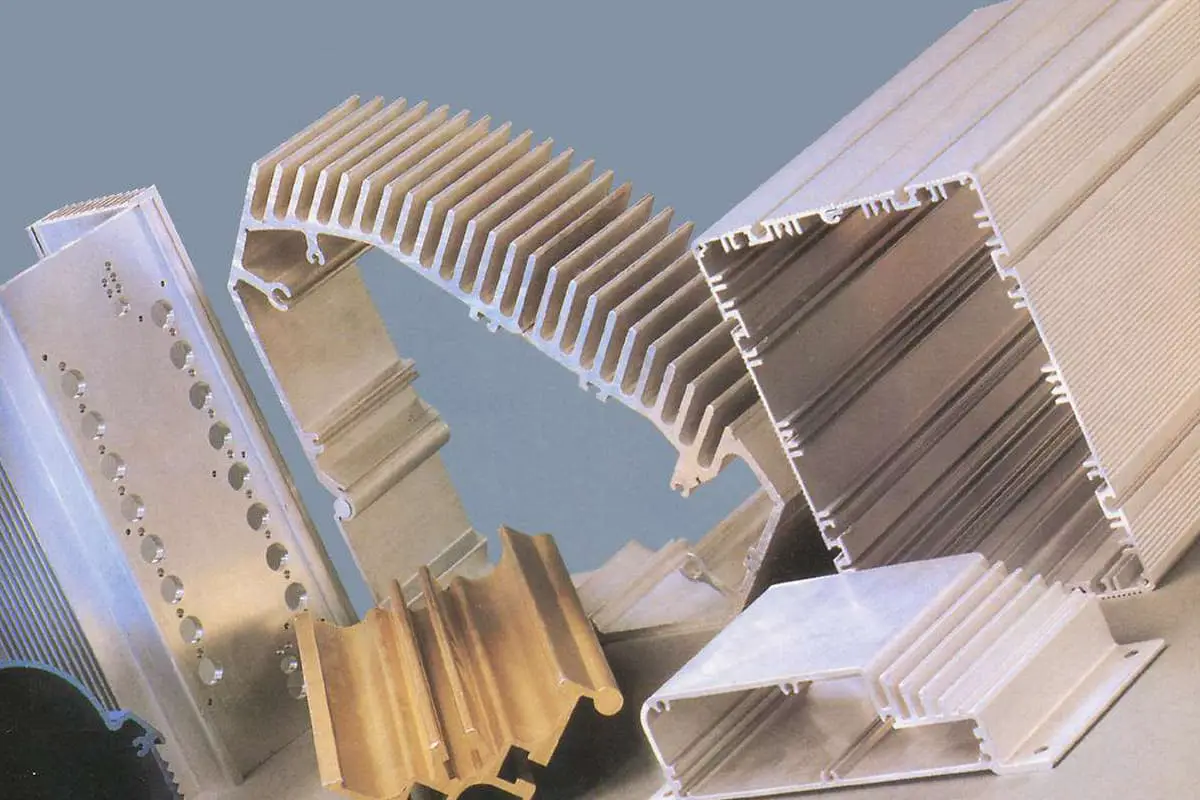
2. Propiedades relacionadas del aluminio
① Densidad
El aluminio tiene una densidad pequeña, sólo 2,7 g/cm3, aunque es relativamente blando, se puede fabricar en varias aleaciones de aluminio, como aluminio duro, aluminio superduro, aluminio inoxidable, aluminio fundido, etc. Ampliamente utilizado en las industrias manufactureras de aviones, automóviles, trenes, barcos, etc.
② Conductividad térmica
El aluminio es un buen conductor del calor, su conductividad térmica es tres veces mayor que la del hierro. En la industria, el aluminio se puede utilizar para fabricar diversos intercambiadores de calor, materiales de disipación de calor y utensilios de cocina, etc.
③ Ductilidad
Tiene buena ductilidad (su ductilidad es superada solo por el oro y la plata) y se puede convertir en papel de aluminio de menos de 0,01 mm a 100 ℃ ~ 150 ℃. Estas láminas de aluminio se utilizan ampliamente para envasar cigarrillos, dulces, etc., y también se pueden convertir en alambres de aluminio, barras de aluminio y se pueden enrollar para obtener diversos productos de aluminio.
④ Conductividad eléctrica
Ocupa el segundo lugar después de la plata y el cobre. Aunque su conductividad es sólo 2/3 de la del cobre, su densidad es sólo 1/3 de la del cobre. Por lo tanto, para transmitir la misma cantidad de electricidad, la masa del alambre de aluminio es sólo la mitad que la del alambre de cobre. La película de óxido sobre la superficie del aluminio no solo tiene la capacidad de resistir la corrosión, sino que también tiene cierta propiedad aislante. Por lo tanto, el aluminio tiene una amplia gama de usos en la industria de fabricación eléctrica, la industria de alambres y cables y la industria de la radio.
3 . Composición química
Las carcasas de aleación de aluminio generalmente utilizan aleaciones de la serie 6, con un contenido de aluminio generalmente superior al 80 % y la gran mayoría entre 85 % y 90 %.
Tabla de composición química de aleaciones de aluminio comunes | |
Serie AL1/Aluminio puro | El aluminio puro Serie 1 tiene un contenido de aluminio superior al 99%. La serie con menor contenido de aluminio, como la 1050, tiene un contenido de aluminio del 99,5%. El proceso de producción es relativamente simple y el precio es relativamente barato. Es la serie más utilizada en las industrias convencionales. |
Serie AL-Cu2/aleación de aluminio y cobre | La aleación de aluminio Serie 2 representa 2024, 2A12 (es decir, LY12). La placa de aluminio Serie 2 se caracteriza por su alta dureza, muy alta resistencia y buena procesabilidad de corte, pero baja resistencia a la corrosión. Entre ellos, el contenido del elemento cobre es el más alto, alrededor del 3-5%. El material de aluminio de la Serie 2 pertenece al material de aluminio de aviación y el precio es relativamente alto. |
Serie AL-Mn3/aleación de aluminio-manganeso | La aleación de aluminio de la serie 3 representa principalmente 3003 y 3A21. La Serie 3 está compuesta principalmente de manganeso, con un contenido entre 1,0-1,5. Es una serie con buena capacidad de prevención de la oxidación, utilizada para procesar piezas que requieren buena conformabilidad, alta resistencia a la corrosión y buena soldabilidad. |
AL-Mg5/Aleación de aluminio y magnesio | La aleación de aluminio de la serie 5 representa 5052, 5083 y 5A06. El aluminio serie 5 es una de las series de placas de aleación de aluminio más utilizadas, con magnesio como elemento principal y un contenido de magnesio entre 3-5%. También puede denominarse aleación de aluminio y magnesio. Sus características principales son baja densidad, alta resistencia a la tracción, alto alargamiento, buena resistencia a la fatiga, pero no puede tratarse térmicamente para fortalecerlo. En la misma zona, el peso de la aleación de aluminio y magnesio es menor que el de otras series y se utiliza ampliamente en las industrias convencionales. |
AL-Mg-Si6/Aleación de aluminio-magnesio-silicio | La aleación de aluminio de la serie 6 representa 6061, 6063 y 6082, y contiene principalmente elementos de magnesio y silicio. La Serie 6 es una aleación de refuerzo tratable térmicamente con buena conformabilidad, soldabilidad y maquinabilidad, y también tiene resistencia media. Después del recocido, aún puede mantener una buena operatividad, lo que es adecuado para aplicaciones con alta resistencia a la corrosión y requisitos de oxidación. Tiene buena usabilidad, es fácil de recubrir y tiene buena procesabilidad. |
AL-Zn7/aleación de aluminio y zinc | La aleación de aluminio de la serie 7 representa el 7075 y contiene principalmente elementos de zinc. También pertenece a la serie de aviación, es una aleación de aluminio-magnesio-zinc-cobre, es una aleación tratable térmicamente, pertenece a la aleación de aluminio súper dura y tiene buena resistencia al desgaste. También tiene buena soldabilidad, pero baja resistencia a la corrosión. Entre esta serie, la aleación de aluminio 7075-T651 es particularmente superior, conocida como el mejor producto de aleación de aluminio, con alta resistencia, muy superior a cualquier acero al carbono. Esta aleación también tiene buenas propiedades mecánicas y reacciones anódicas. |
En términos de perfiles de aluminio industriales, los materiales más utilizados en la actualidad son los materiales 6063 y 6061. Estos dos materiales de aleación de aluminio son los más utilizados en materiales de aluminio industriales. 6063 es más suave, tiene mejor rendimiento de corte y procesamiento, especialmente en el tratamiento de superficies, es mejor que 6061, por lo que se debe elegir este material para fabricar carcasas de aluminio.
01 Composición química de la aleación de aluminio 6063.
- Al: restante
- Sí: 0,20~0,60
- Cu: 0,10
- Magnesio: 0,45~0,9
- Zn:0,10
- Manga: 0,10
- Tí: 0,10
- Cr: 0,10
- Fe: 0,35
Sencillo: 0,05 Total: 0,15
02 Dureza de la aleación de aluminio 6063.
Entre 8-12HW, resistencia a la tracción ≥205mpa, límite elástico ≥170mpa, tasa de alargamiento ≥7%.
03 Características del perfil de aleación de aluminio 6063.
Dimensiones precisas, alta resistencia, después de la coloración por oxidación y el tratamiento de la superficie por pulverización, la apariencia es suave, hermosa, de color elegante, cómoda al tacto y tiene buena resistencia a la corrosión.
Grosor de la pared del perfil: Cumple con los estándares GB5237.1~5237.6-2004, GB/T6892
Indicadores de rendimiento: cumple con los estándares GB5237.1~5237.6-2004, GB/T6892
II. Parámetros de clasificación de la carcasa de aleación de aluminio
01 Adaptador de carcasa de aluminio
Ha desempeñado un papel notable en la reducción de los costos para el consumidor, el ahorro de recursos sociales y la reducción de los desechos electrónicos. Sin embargo, surgieron algunos problemas durante la implementación de este estándar, como que algunas carcasas de adaptadores no soportan la carga USB. La aplicación de este patrón puede causar daños al regulador de voltaje y una disminución en la velocidad de conexión durante la carga.
02 Fuente de alimentación de aluminio
Generalmente, la carcasa está hecha de caucho plástico, que puede proporcionar aislamiento. La calidad de la cáscara también está relacionada con la seguridad del consumidor. Una carcasa de alta calidad puede proporcionar un buen aislamiento e impermeabilización, mientras que una carcasa de baja calidad no sólo puede afectar el uso normal de la máquina, sino también poner en peligro la seguridad del consumidor. Entonces, ¿qué fuente de alimentación es más segura? La respuesta es, sin duda, una carcasa fabricada con materiales garantizados y de alta calidad.
03 Carcasa impermeable para fuente de alimentación
Principalmente, las carcasas de aluminio se producen mediante moldeo por inyección de materiales plásticos. Tiene un alto grado de impermeabilización, es resistente, no es propenso a la infiltración de agua y puede satisfacer bien las necesidades del cliente.
III. Parámetros comunes para procesos de tratamiento de superficies.
01 voladura
El proceso de limpieza y rugosidad de la superficie del metal por el impacto del flujo de arena a alta velocidad. Este método de tratamiento de la superficie de la pieza de aluminio puede darle a la superficie de la pieza un cierto grado de limpieza y rugosidad diferente, mejorar las propiedades mecánicas de la superficie de la pieza, aumentando así la resistencia a la fatiga de la pieza, aumentando la adhesión entre esta y el revestimiento. , alargando la durabilidad del revestimiento y facilitando la nivelación y decoración de la pintura.
02 Cepillado
El proceso de fabricación consiste en raspar repetidamente líneas en la placa de aluminio con papel de lija. El cepillado se puede dividir en cepillado en línea recta, cepillado en línea aleatoria, cepillado en espiral y cepillado en línea. El proceso de cepillado del metal puede mostrar claramente cada trazo fino, haciendo que el metal sea mate con un brillo fino, dando al producto una sensación de moda y tecnología.
03 Anodizado
Se refiere a la oxidación electroquímica de metales o aleaciones. En condiciones específicas del proceso y en el electrolito correspondiente, el aluminio y sus aleaciones forman una película de óxido sobre el producto de aluminio (ánodo) debido al efecto de la corriente aplicada.
El anodizado no solo resuelve los defectos de dureza de la superficie y resistencia al desgaste del aluminio, sino que también extiende la vida útil del aluminio y mejora su estética. Se ha convertido en una parte indispensable del tratamiento de superficies de aluminio y actualmente es el proceso más utilizado y exitoso.
La anodización es un proceso común utilizado para carcasas de aleación de aluminio, donde los parámetros relacionados con la resistencia a altas temperaturas, luz ultravioleta y película de óxido son importantes.
1) Resistencia a altas temperaturas
La película anodizada tiene un excelente aislamiento y resistencia al calor. Esto se debe a que la conductividad térmica de la película anodizada es mucho menor que la del aluminio puro. La película anodizada puede soportar temperaturas de alrededor de 1.500 ℃, mientras que el aluminio puro sólo puede soportar 660 ℃.
La diferencia entre la aleación de aluminio anodizado y no anodizado radica en la disolución química de la película exterior de óxido en contacto con el electrolito. Cuando la tasa de formación de óxido en la superficie del aluminio se equilibra gradualmente con la tasa de disolución química, la película de óxido puede alcanzar su espesor máximo bajo estos parámetros electrolíticos.
En el electrolito de ácido sulfúrico, cuanto mayor es la temperatura de oxidación, mayor es la estabilidad térmica de la capa de película obtenida. Cuando se añaden ácido bórico o ácido bórico y glicerina al electrolito de ácido sulfúrico, la temperatura de oxidación se puede aumentar a 40°C (preferiblemente sin exceder los 39°C).
Para esta fórmula, la capa de película de óxido obtenida no se agrietará a 130°C cuando la temperatura sea de 29°C, y la resistencia al calor puede alcanzar 150°C o incluso más (el espesor de prueba de la capa de película es de aproximadamente 7 micras). cuando la temperatura es de 35°C. Si se utiliza un proceso de oxidación alcalina débil, la resistencia al calor de su capa de película es mayor que la de la película anodizada con ácido sulfúrico.
2) Luz Ultravioleta
En las clasificaciones estándar internacionales, el anodizado con luz ultravioleta implica un tratamiento de superficie y un recubrimiento metálico coloreado. Los siguientes son los estándares de la organización internacional de estándares para el anodizado con luz ultravioleta:
ISO 6581:2018
Anodizado de aluminio y sus aleaciones: determinación de la resistencia a la luz y al calor de revestimientos anodizados coloreados
ISO 6581:2010
Anodizado de aluminio y sus aleaciones: determinación de la solidez al calor y a la radiación ultravioleta de revestimientos anodizados coloreados
ISO 6581:1980
Anodizado de aluminio y sus aleaciones: determinación de la solidez ultravioleta de revestimientos anodizados coloreados
Las aleaciones de aluminio tienen alta resistencia, baja densidad, fuerte conductividad eléctrica y térmica, excelentes propiedades mecánicas y buena maquinabilidad. Después del tratamiento de anodizado, la superficie del aluminio y sus aleaciones puede obtener una capa de película densa, mucho más gruesa que la película de óxido natural, lo que mejora la resistencia a la corrosión de la superficie del metal. Le da al metal un brillo natural, una textura suave y belleza al mismo tiempo que produce un recubrimiento resistente. El tratamiento de superficie de aluminio anodizado puede proporcionar cualquier color y prevenir daños causados por las duras condiciones climáticas y los dañinos rayos ultravioleta.
3) Película de óxido
El. La película de óxido anódico es una estructura de dos capas. La capa interna es una película densa y delgada similar al vidrio de alúmina de alta pureza (Al2O3), con un espesor de aproximadamente 0,01 ~ 0,05 mm y alta dureza. La capa exterior es una película de alúmina hidratada (Al2O3·H2O).
B. La película de óxido tiene muchos poros, que tienen forma de capilar cónico, y el tamaño de los poros aumenta desde el interior hacia el exterior. Por tanto, tiene una excelente capacidad de adsorción, es fácil de teñir en diferentes colores, potenciando su función decorativa; Tiene una fuerte adherencia a la pintura, por lo que es adecuado como capa base para pintar. Para mejorar la resistencia a la corrosión se debe realizar un tratamiento de sellado de poros.
w. La película de óxido es un aislante. Cuando el espesor de la película es de 1 μm, el voltaje de ruptura es de 25 V. La resistividad de la película de óxido de aluminio puro es 109Ω/ cm2 .
d. La película de óxido tiene una excelente resistencia al calor y puede soportar temperaturas de hasta 1500°C. Su conductividad térmica es menor que la del metal.