Las conexiones roscadas, un método de fijación removible y ampliamente utilizado, tienen una estructura simple, confiables y fáciles de ensamblar y desmontar. Son uno de los métodos de conexión más utilizados y más amplios en estructuras de productos de chapa y poseen ventajas irremplazables.
Los métodos comunes de remachado para sujetadores roscados en piezas de chapa metálica incluyen remachado a presión, remachado por expansión y remachado por tracción.
1. Principios para la selección de remaches
1) Preste atención a las dimensiones exteriores del remache para evitar interferencias.
2) Dependiendo del método de remachado del remache, considere la dirección de la fuerza aplicada al remache durante el montaje para evitar incidentes de extracción.
3) La longitud de la sección del remache debe ser ligeramente menor que el espesor de la lámina, determinado en función del espesor de la lámina.
4) Al elegir los remaches, considere el método de remachado y deje espacio para la operación de remachado.
5) Como la placa base se deforma durante el remachado a presión y la conexión se deforma durante el remachado por expansión, para acero inoxidable o materiales con mayor dureza, elija el método de remachado por expansión.
6) Para placas base de menos de 1 mm de espesor, se debe evitar el remachado a presión. Si existen requisitos especiales, utilice el método de remachado por expansión.
7) Los remaches hinchables son más seguros que los remaches de empuje y deben usarse a menos que existan requisitos especiales.
8) Para placas base de más de 3,0 mm de espesor, se deben evitar los remaches a presión de cabeza hexagonal. Utilice remaches de cabeza redonda para asegurar la planitud después del remachado.
9) Al elegir remaches a presión, tenga en cuenta: Los remaches a presión de cabeza redonda M5 e inferiores son adecuados para remachar láminas con un espesor de entre 1,0 y 2,0 mm; Los remaches de cabeza redonda M6 son adecuados para remachar láminas con un espesor de entre 2,0 y 2,5 mm; Los remaches de cabeza redonda M8 son adecuados para remachar láminas de más de 2,5 mm de espesor.
2. Formas estructurales y proceso de remachado de componentes remachados
Las formas estructurales comunes de los componentes remachados incluyen columnas de tuercas remachables, tuercas remachables (espárragos), tuercas remachables expandibles (espárragos), tuercas remachables, tuercas remachables flotantes y más.
(1) Presione la columna de tuerca remachadora
También conocido como remache a presión o columna de tuerca, es un tipo de sujetador muy utilizado en chapa, placas delgadas, chasis y gabinetes. No existe una norma nacional específica para columnas con tuercas remachables prensadas. La base de la columna de la tuerca remachable a presión es hexagonal y el otro extremo es cilíndrico, con una ranura en el medio de la base hexagonal y el cilindro.
El remachado a presión se realiza en una prensa especial utilizando un molde, aplicando una cierta presión para presionar la cabeza hexagonal en un orificio predefinido en la placa (el diámetro del orificio predefinido suele ser ligeramente mayor que el diámetro exterior del cilindro). columna de tuerca remachadora a presión).
Esto provoca una deformación plástica alrededor del orificio, comprimiéndose la parte deformada en la ranura del poste de la tuerca del remache a presión, remachando así firmemente el poste de la tuerca del remache a presión a la placa. Este tipo de remachado generalmente requiere que la dureza de la columna de tuerca remachadora a presión sea mayor que la dureza de la placa delgada.
Placas comunes de acero con bajo contenido de carbono (dureza inferior a 70 HRB), placas de aleación de aluminio, placas de cobre, etc. son todos adecuados para columnas de tuercas remachables prensadas. Para placas de acero inoxidable y placas de acero con alto contenido de carbono, debido a su material duro, las columnas especiales de tuercas remachables prensadas de alta resistencia no solo son costosas, sino también difíciles de prensar, poco confiables para remachar y fáciles de caer.
Para garantizar la confiabilidad del remachado, a menudo es necesario soldar de 2 a 3 puntos en el costado de la columna de tuerca remachadora prensada, por lo que el proceso es deficiente. Si el producto se va a remachar con láminas de acero inoxidable y acero con alto contenido de carbono, la dureza de la lámina de acero debe ser inferior a 80 HRB.
Por tanto, en piezas de chapa con columnas de tuercas remachables prensadas se debe evitar el uso de placas de acero inoxidable. Lo mismo se aplica a los pernos y tuercas remachables a presión, que no son adecuados para su uso en placas de acero inoxidable. El proceso de remachado a presión de la columna de tuercas remachables a presión se muestra en la Figura 9-1.
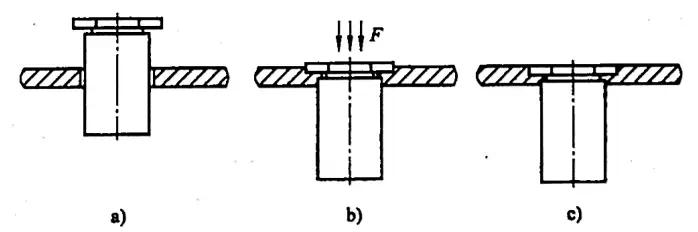
- a) Estado inicial
- b) Proceso de deformación
- c) Finalización del remachado
(2) Presione la tuerca remachadora
Las tuercas remachables prensadas también son un tipo de sujetador ampliamente utilizado en láminas de metal, placas delgadas, carcasas de máquinas y gabinetes.
Actualmente no existe ninguna norma nacional específica para tuercas remachables prensadas. Se diferencian de las columnas de tuercas remachables en que tienen escalones dentados y cabezas invertidas, con una forma circular. El principio de remachado al presionar la tuerca remachable es el mismo que el de presionar la columna de tuercas remachables. El proceso de remachado de la tuerca remachable a presión se muestra en la Figura 9-2.
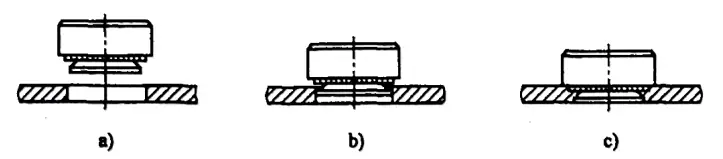
- a) Estado inicial
- b) Proceso de deformación
- c) Finalización de la compresión
(3) Tuerca remachable hinchada
La tuerca remachable expandible es un tipo de sujetador que se utiliza en láminas de metal, placas delgadas, cajas de máquinas y gabinetes. Actualmente, no existen normas nacionales específicas para tuercas remachables intumescentes. Hay dos tipos de tuercas remachables: hexagonales y redondas.
Antes de instalar la tuerca remachable extensible, se debe predefinir un orificio inferior en la chapa. Luego se inserta la tuerca remachable expandible en el orificio. En una prensa especial, mediante un molde (con un cono en la cabeza superior del molde), se aplica una cierta presión para expandir parte del mango hinchado de la remachadora (provocando que parte del material sufra deformación plástica).
Esto forma una cierta forma cónica, lo que hace que la tuerca remachable hinchada encaje perfectamente en la lámina de metal, fijando así la tuerca remachadora hinchada a la placa delgada, completando el remachado. Por lo general, no es necesario endurecer la tuerca remachable hinchada para garantizar su dureza, lo que garantiza que se pueda apretar sin agrietarse.
El proceso de remachado es relativamente simple, pero debido a que la conexión entre la tuerca remachable hinchada y la chapa es una conexión deformada en la dirección circunferencial, puede soportar una fuerza de expulsión mayor, pero el par que puede soportar es menor.
Para compensar esta deficiencia, se recomienda utilizar tuercas remachables hexagonales corrugadas con hebillas invertidas o tuercas remachables redondas corrugadas con dientes dentados. La mordida entre la hebilla inversa o dentada y la chapa aumenta el par de torsión que puede soportar la tuerca remachable extensible. El proceso de expansión de la tuerca remachable se muestra en la Figura 9-3.
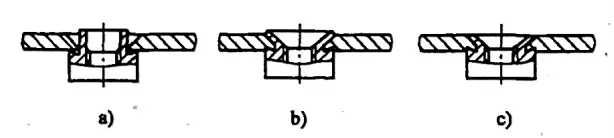
- a) Estado inicial
- b) Deformación disruptiva en frío
- c) Finalización del estampado
(4) Tuerca remachadora
También conocida como tuerca remachable o tapa remachable, se utiliza habitualmente para sujetar diversas piezas de chapa. El remachado se refiere al proceso en el que la tuerca remachable, bajo la influencia de una fuerza de tracción externa, sufre localmente una deformación por expansión plástica (generalmente en lugares especialmente diseñados) para fijar la chapa metálica, logrando así una conexión confiable.
El método del proceso de remachado implica el uso de una pistola remachadora especializada. La pistola remachadora hace que el tornillo en su cabeza gire a través del acoplamiento con la rosca interna de la tuerca remachadora, lo que provoca el movimiento lineal correspondiente de la tuerca remachadora y hace que el área de pared delgada de la tuerca remachadora se expanda y se deforme. hasta que sujete la hoja.
Al fijar la placa mediante deformación local, la tuerca remachable puede soportar una gran fuerza de expulsión y una cierta cantidad de torque. A veces, para garantizar la capacidad de soportar un par elevado, se pueden utilizar tuercas remachables hexagonales o dentadas. La ventaja de las tuercas remachables es su construcción unilateral, que no se ve afectada por el cierre del producto. El proceso de remachado de la tuerca remachable se muestra en la Figura 9-4.
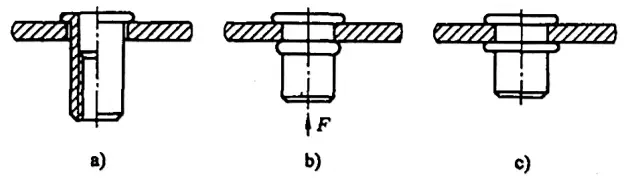
- a) Estado inicial
- b) Deformación bajo tensión
- c) Finalización del remachado
1) Los materiales comunes para las tuercas remachables incluyen acero, aleación de aluminio y acero inoxidable. Las variedades incluyen tuercas remachables de cabeza plana (GB/T17880.1-1999), tuercas remachables avellanadas (GB/T17880.2-1999), tuercas remachables pequeñas avellanadas (GB/T17880.3-1999), remaches avellanados pequeños de 120° (GB /T17880.4-1999) y tuercas remachables hexagonales de cabeza plana (GB/T17880.5-1999).
2) El uso de tuercas remachables: si un producto requiere que la tuerca se monte externamente mientras el espacio interno es estrecho, lo que impide que el cabezal de la máquina remachadora entre para remachar, y métodos como bridas y roscados no pueden cumplir con los requisitos de resistencia, entonces ni el remachado por presión ni por expansión funcionarán, por lo que será necesario el uso de remachado por tensión. Las tuercas remachables son adecuadas para unir piezas de chapa con un espesor de entre 0,5 y 6 m.
(5) Tuercas remachables flotantes
Los productos de chapa metálica, como gabinetes y cajas de computadoras, generalmente se componen de muchas partes. Algunas piezas o componentes de chapa metálica, debido a la compleja estructura general de las cajas o recintos y a los grandes errores acumulados en el tamaño del conjunto, dan lugar a desviaciones significativas en la posición de montaje de las tuercas remachables, lo que dificulta el montaje de otras piezas y, en algunos casos, , imposible.
Por lo tanto, utilizar tuercas remachables flotantes en determinadas posiciones en lugar de otro tipo de tuercas remachables puede mejorar significativamente esta situación. El proceso de remachado de una tuerca remachable flotante se muestra en la Figura 9-5. Actualmente no existen normas nacionales para tuercas remachables flotantes, sólo normas industriales. Al elegir su uso, el tamaño del orificio predefinido y el espacio de instalación deben determinarse de acuerdo con las muestras de productos del fabricante.
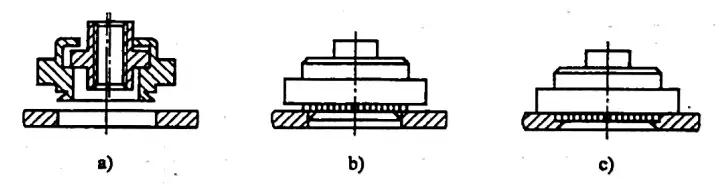
- a) Estado inicial
- b) Proceso de deformación
- c) Finalización del remachado a presión
(6) Dimensiones del orificio inferior de la pieza remachada y espesor de la placa aplicable
1) Para conocer el diámetro del orificio inferior del pilar de tuerca remachada a presión, consulte la Tabla 9-1.
Tabla 9-1 Diámetro del orificio inferior del pilar con tuerca remachada a presión (Unidad: mm)
Especificaciones del hilo | Nombre clave | Diámetro del orificio base d |
M3×0,5 | (B)S0(0)(S)-M3-H | φ4.2 |
M3×0,5 | (B)S0(0)(S)-3.5M3-H | φ5.4 |
M4×0,7 | (B)S0(0)(S)-M4-H | φ6.0 |
M4×0,7 | (B)S0(0)(S)-3.5M4-H | φ7.2 |
M5 ×0,8 | (B)S0(0)(S)-M5-H | φ7.2 |
M6×1.0 | (B)S0(0)(S)-M6-H | φ8.7 |
Nota: S0 S0S denota columnas de tuercas remachables prensadas sin rosca y con orificio pasante; S00 S00S denota columnas de tuercas remachables a presión de rosca pasante. Agregar una B antes del término indica un agujero ciego; agregar una S al final significa que el material es acero inoxidable y sin una S es acero. H representa la altura de la columna de tuerca.
2) Consulte la Tabla 9-2 para conocer el diámetro del orificio inferior de la tuerca remachada a presión.
Tabla 9-2: Diámetro del orificio inferior de la tuerca remachada a presión (Unidad: mm)
Especificaciones del hilo | Nombre clave | Diámetro del orificio base d |
M2x0.4 | S(CLS)-M2-A(0,1,2) | φ4.2 |
M2. 5 × 0,45 | S(CLS)-M2.5-A(0,1,2) | φ4.2 |
M3x0.5 | S(CLS)-M3-A(0,1,2) | φ4.2 |
M4x0.7 | S(CLS)-M4-A(0,1,2) | φ5.4 |
M5×0,8 | S(CLS)-M5-A(0,1,2) | φ6.4 |
M6×1.0 | S(CLS)-M6-A(0,1,2) | φ8.7 |
Poste: CLS significa tuerca remachable de acero inoxidable; S representa una tuerca remachable de acero; A (código de mango) indica el código de espesor aplicable para la tuerca remachable (0 indica un espesor de 0,8-1,2 mm, 1 indica un espesor de 1-1,5 mm, 2 indica un espesor de 1,5 ~ 2,5 mm).
3) Consulte la Tabla 9-3 para conocer el diámetro del orificio inferior de la tuerca empotrada.
Tabla 9-3 Diámetro del orificio inferior para tuerca empotrada (Unidad: mm)
Especificaciones del hilo | Nombre clave | Diámetro del orificio base d |
M2x0.4 | F(S)-M2-A | φ4.3 |
M2,5×0,45 | F(S)-M2.5-A | φ4.3 |
M3x0.5 | F(S)-M3-A | φ4.3 |
M4x0.7 | F(S)-M4-A | $7,4 |
M5x0.8 | F(S)-M5-A | φ7.9 |
M6x1.0 | F(S)-M6-A | φ8.7 |
Nota: “F” indica una tuerca de presión; “S” significa que el material es bronce; “A” (código de agarre) representa el código de espesor de placa aplicable para la contratuerca.
4) Consulte la Tabla 9-4 para conocer el espesor de placa adecuado para la contratuerca.
Tabla 9-4: Espesor de placa aplicable para tuerca prensada (Unidad: mm)
Manejar código A | Especificaciones del hilo | |||||
M2 | M2.5 | M3 | M4 | M5 | M6 | |
1 | 1.5-2.3 | 1,5 ~ 2,3 | 1.5-2.3 | 1.5-2.3 | 1.5-2.3 | |
dos | 2.3-3.2 | 2.3-3.2 | 2.3-3.2 | 2.3-3.2 | 2.3-3.2 | |
3 | 3.2-3.9 | |||||
4 | 4~4.7 | |||||
5 | >4.7 |
5) Para conocer el diámetro del orificio inferior de la tuerca estampada, consulte la Tabla 9-5.
Tabla 9-5: Diámetro del orificio inferior de la tuerca estampada (Unidad: mm)
Especificaciones del hilo | Nombre clave | Diámetro del orificio base d |
M2,5×0,45 | Z-(S)-M2.5-A | φ5.0/Escariado φ5.5×90° |
M3x0.5 | Z-(S)-M3-A | 5.0/Escariado φ5.5×90° |
M4x0.7 | Z-(S)-M4-A | φ6.0/Escariado φ7.0×90° |
M5×0,8 | Z-(S)-M5-A | φ8.0/Escariado φ9.0×90° |
M6x1.0 | Z-(S)-M6-A | φ9.0/Escariado φ10×90° |
M8×1,25 | Z-(S)-M8-A | φ11/Escariado φ12×90° |
Nota: La adición de 'S' significa que el material es acero inoxidable, mientras que la ausencia de 'S' indica que el material es acero. 'A' (código de mango) representa el código para el espesor de lámina aplicable de la tuerca remachable.
6) El espesor de placa aplicable para tuercas remachables de expansión redondas se muestra en la Tabla 9-6.
Tabla 9-6: Espesor de lámina aplicable para tuercas remachables de expansión redondas (Unidad: mm)
Manejar código A | Especificaciones del hilo | |||||
M3 | M4 | M5 | M6 | M8 | M10 | |
1.2 | 1.2 | 1.2 | ||||
1.5 | 1.5 | 1.5 | ||||
2.0 | 2.0 | 2.0 | 2.0 | 2.0 | 2.0 | 2.0 |
3.0 | 3.0 | 3.0 | 3.0 | 3.0 |
7) El espesor de placa aplicable para tuercas remachables hexagonales se muestra en la Tabla 9-7.
Tabla 9-7 Espesor de lámina aplicable de tuerca remachable estampada hexagonal (Unidad: mm)
Manejar código A | Especificaciones del hilo | |||||
M3 | M4 | M5 | M6 | M8 | M10 | |
1.5 | 1.5 | 1.5 | ||||
2.0 | 2.0 | 2.0 | 2.0 | |||
3.0 | 3.0 | 3.0 | 3.0 | 3.0 | ||
4.0 | 4.0 | 4.0 | 4.0 | 4.0 | ||
5.0 | 5.0 | 5.0 | 5.0 | |||
6.0 | 6.0 | 6.0 |
Nota: Las tuercas remachables hexagonales se utilizan principalmente para conexiones que involucran placas base de cobre.
8) El diámetro del orificio inferior del tornillo remachador a presión se puede encontrar en la Tabla 9-8.
Tabla 9-8: Diámetro del orificio inferior del perno remachador a presión
(Unidad: mm)
Especificaciones del hilo | Nombre clave | Diámetro del orificio base d |
M2,5×0,45 | FH(S)-2.5-L | φ2.5 |
M3x0.5 | FH(S)-M3-L | φ3 |
M3x0.5 | NFH(S)-M3-L | φ4.8 |
M4x0.7 | FH(S)-M4-L | Φ4 |
M4x0.7 | NFH(S)-M4-L | φ4.8 |
M5x0. 8 | FH(S)-M5-L | φ5 |
M5x0.8 | NFH(S)-M5-L | φ6.8 |
M6 × 1,0 | FH(S)-M6-L | φ6 |
M6 × 1,0 | NFH(S)-M6-L | φ6.8 |
Nota: 'S' indica que el material es cobre inoxidable, mientras que ninguna 'S' implica que el material es acero. 'FH' representa una cabeza redonda, 'NFH' indica una cabeza hexagonal y 'L' significa la longitud total del tornillo.
9) Para conocer el diámetro del orificio inferior de la tuerca remachable y el grosor de la placa aplicable, consulte la norma nacional: Tuerca remachable de cabeza plana (GB/T17880.1-1999), Tuerca remachable avellanada (CB/T17880 .2 -1999), tuerca remache avellanada pequeña (GB/T17880.3-199), tuerca remache avellanada pequeña de 120° (GB/T17880.4-1999), tuerca remache hexagonal de cabeza plana (GB/T17880 .5-1999) .
(7) La distancia mínima desde el centro del orificio inferior de la parte remachada hasta el borde de la placa base.
1) La distancia mínima recomendada desde el centro del orificio inferior del perno remachable de uso común hasta el borde de la placa base se muestra en la Tabla 9-9.
Tabla 9-9 Distancia mínima recomendada desde el centro del orificio inferior del perno remachable de uso común hasta el borde de la placa base (unidad: mm).
Especificaciones del hilo | Nombre clave | Distancia mínima recomendada desde el centro del orificio inferior hasta el borde de la placa base. |
M3x0.5 | (B)S0(0)(S)-3.5M3-H | 6.8 |
M4x0.7 | (B)S0(0)(S)-M4-H | 8.0 |
M5x0.8 | (B)S0(0)(S)-M5-H | 8.0 |
M6x1.0 | (B)S0(0)(S)-M6-H | 10 |
2) La distancia mínima recomendada desde el centro del orificio inferior de la tuerca remachable comúnmente utilizada hasta el borde de la placa base se muestra en la Tabla 9-10.
Tabla 9-10 Altura mínima recomendada desde el centro del orificio inferior de la tuerca remachable de uso común hasta el borde de la placa base (unidades: mm)
Especificaciones del hilo | Nombre clave | Distancia mínima recomendada desde el centro del orificio inferior hasta el borde de la placa base. |
M3x0.5 | S(CLS)-M3-A(0,1,2) | 4.8 |
M4x0.7 | S(CLS)-M4-A(1,2) | 6.9 |
M5x0.8 | S(CLS)-M5-A(1.2) | 7.1 |
M6x1.0 | S(CLS)-M6-A(1.2) | 8.6 |
M8×1.0 | S(CLS)-M8-2 | 9.7 |
M10x1. 5 | S(CLS)-M10-2 | 13.5 |
3) La distancia mínima recomendada desde el centro del orificio inferior de la tuerca empotrada de uso común hasta el borde de la placa base se proporciona en la Tabla 9-11.
Tabla 9-11 Distancia mínima recomendada desde el centro del orificio inferior de la tuerca empotrada de uso común hasta el borde de la placa base (Unidad: mm)
Especificaciones del hilo | Nombre clave | Distancia mínima recomendada desde el centro del orificio inferior hasta el borde de la placa base. |
M3x0.5 | F(S)-M3-1.5 | 6 |
M4x0.7 | F(S)-M4-2.5 | 6 |
M5x0.8 | F(S)-M5-2.5 | 7.2 |
4) La distancia mínima recomendada desde el centro del orificio inferior de la tuerca remachable de expansión redonda de uso común hasta el borde de la placa base se muestra en la Tabla 9-12.
Tabla 9-12 Distancia mínima recomendada desde el centro del orificio inferior de la tuerca remachable de expansión redonda de uso común hasta el borde de la placa base (Unidad: mm)
Manejar código A | Especificaciones del hilo | ||||
M3 | M4 | M5 | M6 | M8 | |
1.2 | 4.8 | 6.9 | |||
1.5 | 4.8 | 6.9 | |||
2.0 | 4.8 | 6.9 | 7.1 | 8.6 | 9.7 |
3.0 | 7.1 | 8.6 | 9.7 |
5) La distancia mínima recomendada desde el centro del orificio de la base de la tuerca remachable hexagonal de uso común hasta el borde del sustrato se muestra en la Tabla 9-13.
Tabla 9-13 Distancia mínima recomendada desde el centro del orificio de la base de la tuerca remachable hexagonal de uso común hasta el borde del sustrato (Unidad: mm)
Manejar código A | Especificaciones del hilo | |||||
M4 | M5 | M6 | M8 | M10 | M12 | |
1.5 | 6.9 | |||||
2.0 | 6.9 | 7.1 | ||||
3.0 | 6.9 | 7.1 | 8.6 | 9.7 | ||
4.0 | 7.1 | 8.6 | 9.7 | 13.5 | 15 | |
5.0 | 8.6 | 9.7 | 13.5 | 15 | ||
6.0 | 9.7 | 13.5 | 15 |
6) La distancia mínima recomendada desde el centro del orificio del tornillo del remache común inferior hasta el borde de la placa base se muestra en la Tabla 9-14.
Tabla 9-14 Distancia mínima recomendada desde el centro del orificio inferior del tornillo remachador común hasta el borde de la placa base (Unidad: mm)
Especificaciones del hilo | Nombre clave | Distancia mínima recomendada desde el centro del orificio inferior (cabeza redonda) hasta el borde de la placa base. |
M3x0.5 | FH(S)-M3-L | 5.6 |
M4x0.7 | FH(S)-M4-L | 7.2 |
M5x0.8 | FH(S)-M5-L | 7.2 |
M6x1.0 | FH(S)-M6-L | 7.9 |
(8) Factores que afectan la calidad del ensamblaje de remaches.
Hay varios factores que influyen en la calidad del ensamblaje del remache, incluidas las propiedades del material base, el diámetro del orificio inferior y el método de remachado.
1) Propiedades del material base: Cuando la dureza del material base es adecuada, la calidad del remachado y la capacidad de carga de las piezas remachadas son óptimas.
2) Diámetro del orificio inferior: El tamaño del orificio inferior afecta directamente la calidad del conjunto remachado. Un orificio inferior más grande da como resultado un espacio mayor entre el material base y las piezas remachadas. Los efectos de esta brecha en diferentes métodos de remachado son los siguientes:
i) Impacto en el remachado por compresión: el material base no puede deformarse lo suficiente como para llenar la ranura en la parte remachada, lo que genera una fuerza de corte insuficiente y afecta directamente la resistencia al empuje de la tuerca (o remache) del remache de compresión.
ii) Impacto en el remachado de expansión: si el orificio inferior es demasiado grande, la fuerza de compresión generada por la deformación plástica durante el remachado disminuye, afectando directamente el empuje y la resistencia a la torsión del remache de expansión.
iii) Impacto en el remachado por tracción: si el orificio inferior es demasiado grande, la fricción efectiva entre las dos partes disminuye después de la deformación plástica, lo que afecta la calidad del remachado.
Aunque un orificio más pequeño puede aumentar hasta cierto punto la capacidad de carga del remache, puede provocar una mala calidad estética, una alta fuerza de remachado, inconvenientes en la instalación, deformación de la placa base y una disminución de la eficiencia de producción y la calidad del remachado.
3) Distancia desde el centro del orificio inferior hasta el borde del material base: si esta distancia es demasiado corta, puede causar deformación del material base y afectar la calidad del remachado.
(9) Principios del proceso de ensamblaje de remaches
Al preparar láminas de proceso para piezas de chapa con componentes remachados, se debe prestar especial atención no sólo a la disposición racional del proceso de remachado, sino también a la posición del tornillo o tuerca del remachador.
Diferentes posiciones soportan diferentes cargas y tienen diferentes requisitos de proceso. Por tanto, la estructura de las piezas remachadas y el proceso de remachado deben adaptarse a la posición de remachado. Una selección inadecuada puede reducir el rango de carga del perno o la tuerca remachable, lo que provocará fallas en el remachado. Los principios generales para remachar tornillos y tuercas remachables son los siguientes:
1) No remache tornillos ni tuercas de acero o acero inoxidable antes de anodizar o tratar la superficie de las placas de aluminio.
2) El número de pernos o tuercas remachables de compresión remachados en la misma fila debe ser razonable. Si hay demasiados, el material comprimido no tendrá por dónde fluir, lo que puede provocar una gran tensión y doblar la pieza formando un arco.
3) Es preferible recubrir la superficie de las piezas antes de remachar los tornillos y tuercas.
4) Después del remachado, las tuercas remachables M5, M6, M8 y M10 generalmente necesitan soldarse por puntos para aumentar su resistencia. Las tuercas más grandes requieren mayor resistencia y pueden soldarse por arco. Para M4 (incluido M4) e inferiores, es mejor utilizar tuercas remachables de expansión.
5) Al remachar tuercas en un borde doblado, para garantizar la calidad del remachado de la tuerca, tenga en cuenta lo siguiente:
① La distancia desde el borde del orificio del remache hasta el borde del doblez debe exceder la zona de deformación del doblez.
② La distancia L desde el centro de la tuerca remachada hasta el lado interior del borde doblado debe ser mayor que la suma del radio del cilindro exterior de la tuerca remachada y el radio de curvatura interior, es decir, L>D/ 2+r.
6) Para sustratos de menos de 1 mm, la confiabilidad del remachado a presión es baja y, por lo tanto, no se recomienda. Si hay requisitos especiales, se puede cambiar a remachado expandible y se deben reforzar 2-3 puntos con soldadura por puntos de arco de argón (o punzonado de 2-3 puntos) en una superficie que no afecte las roscas.
3. Tuercas soldadas de proyección
Las tuercas para soldadura por proyección, también conocidas como tuercas para soldadura por puntos, se utilizan ampliamente en productos de chapa metálica. Sin embargo, durante la aplicación real, a menudo surgen problemas debido a un diámetro de orificio diseñado incorrectamente, lo que resulta en la incapacidad de colocar con precisión la tuerca de soldadura de proyección.
Las normas nacionales incluyen dos tipos de tuercas soldadas de proyección: tuercas soldadas cuadradas (GB13680-1992) y tuercas soldadas hexagonales (GB13681-1992). Las tuercas cuadradas soldadas tienen un posicionamiento irregular, lo que no solo provoca errores de posicionamiento significativos, sino que a menudo requiere roscas después de la soldadura.
Por el contrario, las tuercas soldadas hexagonales tienen una estructura de autoposicionamiento, lo que ofrece mayor precisión y operaciones de soldadura más convenientes. Por tanto, es recomendable utilizar tuercas soldadas hexagonales.
En la Figura 9-6 se muestra un diagrama esquemático de cómo soldar una tuerca hexagonal a una placa base. Los valores recomendados para el diámetro del orificio de la placa base D y el espesor de la placa t se presentan en la Tabla 9-15.
Figura 9-6: Diagrama esquemático de la tuerca hexagonal soldada a la placa base
Tabla 9-15: Valores recomendados para el diámetro del orificio de la placa base D y el espesor de la placa t
(Unidad: mm)
Especificaciones del hilo | D | t | ||
M4 | 6 +0.075 | 0,75~3 | ||
M5 | 7 +0.09 | 0,9~3,5 | ||
M6 | 8 +0.09 | 0,9 ~ 4 | ||
M8 | M8×1 | 10,5 +0,11 | 1-4.5 | |
M10 | M10×1 | M10x1.25 | 12,5 +0,11 | 1.25-5 |
M12 | M12x1.5 | M12×1,25 | 14,8 +0,11 | 1.5-5 |
M14 | M14x1.5 | 16,8 +0,11 | 2~6 | |
M16 | M16×1,5 | 18,8 +0,13 | 2~6 |
4. Bridas y Roscados
El bridado y roscado, también conocido como taladrado y roscado, se utiliza principalmente en piezas de chapa para establecer conexiones entre ellas. Dado que la base de la pieza de chapa es delgada, al golpearla directamente se obtendría un hilo demasiado corto que podría salirse fácilmente.
Por lo tanto, primero se perfora un orificio inferior en la pieza de chapa (determinado por las especificaciones de rosca). Luego, utilizando una matriz de brida (extracción de orificios) dedicada en una prensa, se extrae un borde vertical (la altura del estirado está determinada por las especificaciones de la rosca y el espesor de la placa). Finalmente se rosca el hilo, logrando el propósito de aumentar la longitud efectiva del hilo.
5. Comparación de rendimiento de tuercas remachables infladas, tuercas remachables prensadas, tuercas remachables y bridas y roscados
Las tuercas remachables hinchadas, las tuercas remachables prensadas, las tuercas remachables y las bridas y roscados tienen sus ventajas y desventajas. La comparación de desempeño se puede ver en la Tabla 9-16.
Tabla 9-16 Comparación de rendimiento de tuercas remachadas hinchadas, tuercas remachadas prensadas, tuercas remachadas de tracción y bridas y roscas
Método de conexión | Tuerca de estampado | Tuerca de presión. | Tuerca remachada | Bridas y Roscados |
maquinabilidad | Bien | Bien | Bien | Promedio |
Material de sustrato | Los remaches de acero inoxidable tienden a caerse fácilmente | El remachado de acero inoxidable es deficiente y requiere el uso de contratuercas especialmente fabricadas y soldadura por puntos. | Bien | Las placas delgadas y los materiales blandos de cobre y aluminio son propensos a deslizarse las roscas. |
Precisión | Bien | Bien | Bien | Promedio |
Durabilidad | Bien | Bien | Bien | La calidad de los materiales de cobre y aluminio es inferior y son preferibles otros materiales con más de tres alambres. |
Costo | Alto | Alto. | Promedio | Bajo |
Calidad | Bien | Bien | Bien | Promedio |