Con los avances en la reducción del peso de los vehículos y la seguridad en caso de colisión, el uso de placas de acero de alta resistencia en la industria automotriz está aumentando gradualmente.
Actualmente, las piezas de placas flexibles de alta resistencia se utilizan principalmente en componentes estructurales de chasis de automóviles.
El plegado de chapa se puede realizar de dos formas:
(1) Estampado Plegado
Esta técnica de doblado requiere que el troquel de doblado y el material de la lámina estén completamente adheridos entre sí y coincidan con precisión con las piezas de chapa.
Debido al alto coste de desarrollo del molde, es adecuado para piezas de chapa con estructuras complejas.
(2) Doblado de plegadora
Este método elimina la necesidad de que el troquel de doblado coincida con cada pieza de chapa de forma individual.
Al ajustar el proceso de doblado y la carrera de la plegadora, se puede producir un molde de doblado flexible para adaptarse a los requisitos de varias piezas dobladas.
Es económico para piezas de chapa con estructuras simples ya que el costo de desarrollo de un molde de plegadora es bajo.
Sin embargo, cuando se doblan placas de alta resistencia utilizando el método de doblado libre en una prensa plegadora, la eficiencia de la producción se reduce debido a diversos defectos causados por factores como el rendimiento del material, las condiciones del equipo y los parámetros del proceso de doblado.
Esto puede resultar en pérdidas económicas.
En este artículo analizaremos los principales tipos de defectos en la flexión libre de chapas de acero de alta resistencia y propondremos las correspondientes medidas de mejora y contramedidas.
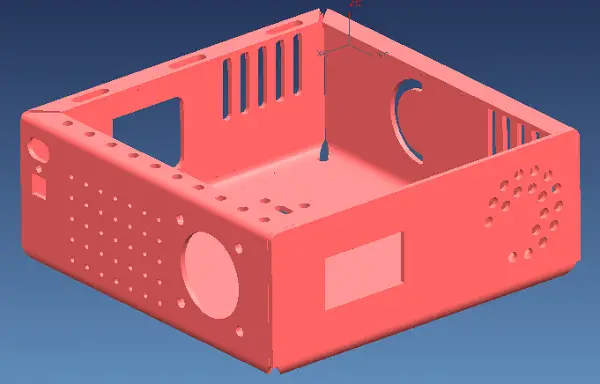
Grieta de flexión
Cuando el radio de curvatura interno (R) se reduce hasta cierto punto, una deformación excesiva puede dar como resultado grietas o microfisuras del material longitudinal lateral fuera del material laminar en el radio de curvatura, como se ilustra en la Figura 1.
Durante la fase inicial de la producción de prueba de piezas dobladas de acero de alta resistencia, los defectos de agrietamiento por flexión son una ocurrencia común, lo que conduce no sólo al desperdicio de la placa, sino también a un obstáculo para el progreso normal del proyecto.
Los principales factores que contribuyen al agrietamiento en piezas dobladas de acero de alta resistencia se pueden atribuir a los siguientes aspectos.
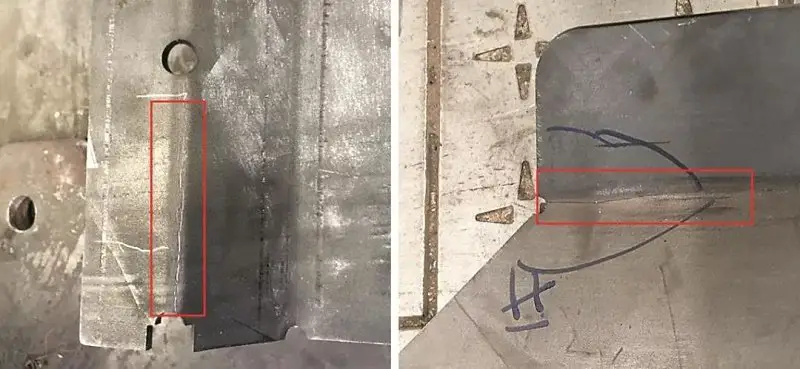
Fig. 1 Grietas en el radio de curvatura de piezas dobladas de acero de alta resistencia.
radio de curvatura
El radio de curvatura mínimo, que evita el agrietamiento de la fibra exterior, es el radio de curvatura final.
El radio de curvatura mínimo depende de varios factores, incluidas las propiedades mecánicas del material, la dirección de la veta del tablero, la calidad de la superficie del tablero, la calidad del borde y el espesor del tablero.
A medida que aumenta la resistencia del material, su plasticidad disminuye, lo que da como resultado un radio mínimo de curvatura mayor.
Además, las placas laminadas en frío tienden a exhibir anisotropía, con mayor plasticidad a lo largo de la dirección del grano que perpendicularmente a él.
Por lo tanto, cuando la línea de curvatura es perpendicular a la dirección de la fibra de la lámina, el radio de curvatura mínimo es menor.
Para evitar grietas o microfisuras por flexión, es esencial predecir con precisión de antemano el radio de curvatura mínimo del material de la lámina.
Por ejemplo, el radio de curvatura del acero protector BP500 (con un límite elástico de no menos de 1250 MPa) debe ser al menos 4 veces el espesor del material, y la línea de curvatura debe ser perpendicular a la dirección de la fibra del material de la lámina.
Para evitar grietas por flexión causadas por un radio de curvatura insuficiente, es crucial considerar la relación entre el radio de curvatura y el radio de curvatura mínimo, así como la relación entre la línea de curvatura y la dirección de la fibra del material laminar durante Fase de revisión digital-analógica.
Método de posicionamiento de la línea de doblado
En el proceso de doblado, es importante colocar correctamente la línea de doblado para garantizar la precisión de las piezas dobladas.
Tradicionalmente, los métodos de posicionamiento manual de líneas incluyen posicionamiento de marcado manual o láser, posicionamiento de muescas de proceso y posicionamiento de bloques de máquinas herramienta.
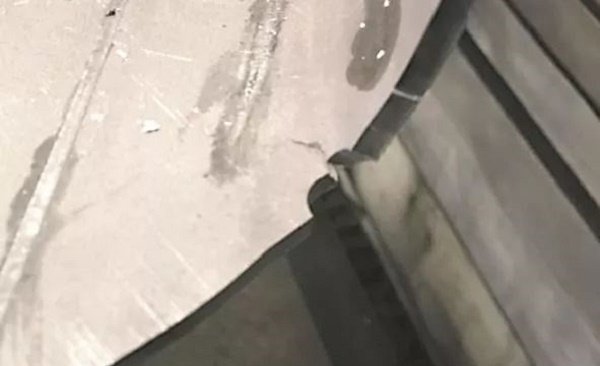
HIGO. 2 Grieta en el proceso de piezas dobladas de placas de alta resistencia
Durante la prueba de flexión de materiales en láminas BP500, cuando se utiliza el método de posicionamiento por muesca de proceso, pueden ocurrir grietas en el espacio de posicionamiento, como se muestra en la Figura 2.
El tratamiento de muesca cambia la forma original del borde liso del material a una forma afilada, lo que hace que la tensión se concentre en los espacios. Cuando se dobla el material laminar, el valor de la tensión en el espacio excede el límite de resistencia y se producen grietas.
Esto resalta los altos requisitos de calidad de superficie y bordes de las láminas BP500 durante el proceso de plegado. La superficie debe estar libre de grietas, rayones, rebabas y muescas en los bordes.
Por lo tanto, la placa BP500 no se puede posicionar para doblarse utilizando el método de posicionamiento de muesca de proceso.
Se recomienda utilizar el método de posicionamiento del bloque de máquina herramienta de chapa sin daños para doblar.
Duplicación del Springback
El resorte de flexión hacia atrás se refiere a la situación en la que el ángulo de flexión y el radio de las piezas dobladas son diferentes de los valores previstos después de ser retiradas de las herramientas de la plegadora.
La resiliencia de las piezas flexionadas está influenciada principalmente por los siguientes factores:
- Propiedades mecánicas del material.
- Radio relativo de curvatura (r/t)
- Método de flexión
- Ángulo de flexión en el centro
- Forma de las piezas plegadas.
El tamaño del ángulo de retorno elástico es proporcional a la resistencia al flujo y al índice de endurecimiento del material, e inversamente proporcional al módulo de elasticidad.
El límite elástico del acero de protección BP500 no es inferior a 1250 MPa, por lo que su tendencia a la recuperación elástica es mayor que la de las placas de acero ordinarias.
Principales métodos para mejorar la precisión de piezas dobladas:
- Cambiar la estructura local de las piezas plegadas.
- Elija materiales con baja resistencia al flujo y un gran módulo de elasticidad.
- Reemplace la flexión libre y la compensación del molde con una flexión correcta
La mejora del retorno elástico de flexión de la placa BP500 se logró principalmente mediante el método de compensación del molde, ya que la placa de refuerzo no se pudo agregar a la posición de flexión debido a limitaciones en la forma de las piezas a doblar.
La Tabla 1 muestra los resultados de los experimentos realizados al doblar placas BP500 con un radio de curvatura de 20 mm y ángulos de curvatura central de 90°, 120° y 135°, respectivamente.
Tabla 1 Relación entre el ángulo de flexión del resorte hacia atrás y el ángulo de flexión central para la placa BP500
Flexión del ángulo central | Ángulo de recuperación elástica |
---|---|
90° | 14 |
120° | 18° |
135° | 21° |
Como se muestra en la tabla, se puede observar que a medida que aumenta el ángulo de flexión central, también aumenta la resiliencia.
En el proceso de diseño del troquel de doblado para el material BP500, se realizó una compensación de 14° para el ángulo de recuperación elástica (para un ángulo de doblado de 90°) en las herramientas de la plegadora.
El molde fue diseñado con un ángulo negativo para optimizar la resistencia a la flexión de la placa BP500 y mejorar la precisión de las piezas dobladas.
La Figura 3 ilustra la estructura de la matriz de flexión inferior antes y después de la compensación del rebote elástico.
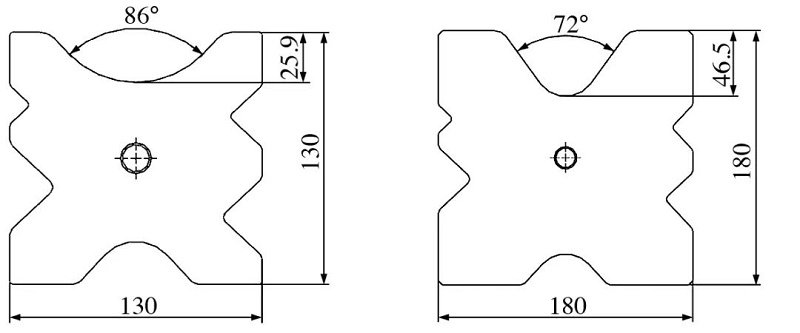
HIGO. 3 Diagrama esquemático del troquel de doblado inferior.
Deformación de la sección doblada.
Debido a los requisitos de modelado, algunas piezas dobladas tienen orificios grandes cerca de la línea de plegado, como se ilustra en la Figura 4(a).
Una vez finalizado el proceso de perforación, las piezas dobladas se deforman cerca del orificio, lo que afecta la instalación de otras piezas.
Para solucionar este problema, se ha ajustado el método de perforación de agujeros grandes. Se perforó parte del orificio, mientras que se retuvo parte de la tira de conexión, como se muestra en la Figura 4(b).
Una vez finalizado el proceso de doblado, se procesó el resto del agujero.
Este método mejora significativamente el problema de deformación, mejora la planitud de las piezas dobladas y garantiza una instalación adecuada de las piezas.
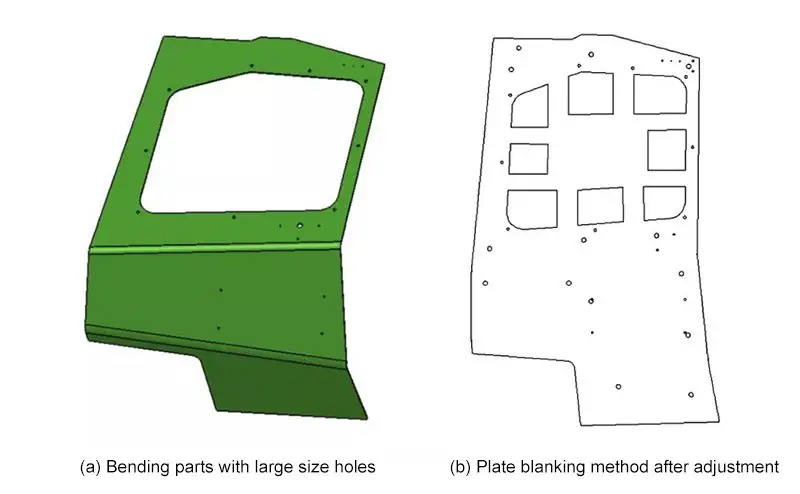
HIGO. 4 Método de supresión de agujeros grandes para piezas dobladas
Inconsistente Ángulo de flexión
En el proceso de doblado del material BP500, se encontró que los ángulos de doblado de los extremos izquierdo y derecho de las piezas con líneas de doblado largas eran inconsistentes.
Las razones de esta inconsistencia son las siguientes:
- Cuando el ariete de la plegadora alcanza la posición final de flexión, el paralelismo entre él y la superficie de la mesa excede la tolerancia.
- El paralelismo entre la superficie de montaje del troquel superior y la superficie de trabajo inferior excede la tolerancia.
- El grado de paralelismo entre la ranura en forma de V de la matriz de doblado inferior y la superficie de instalación inferior excede la tolerancia.
- El espesor de la placa plegada es inconsistente en los extremos izquierdo y derecho.
Incluso cuando el troquel de doblado inferior se giraba 180°, la diferencia angular entre los lados izquierdo y derecho de las piezas dobladas todavía existía y el valor se había cambiado.
Investigaciones adicionales revelaron que el tamaño del arco circular en la parte de trabajo inferior del punzón para doblar no era consistente, lo que llevaba a un paralelismo deficiente entre la superficie inferior de la instalación y la superficie de trabajo inferior del punzón para doblar.
Esto resultó en ángulos de caída inconsistentes de izquierda a derecha.
Al reprocesar el arco circular en la superficie de trabajo inferior del punzón de flexión, se mejoró la planitud a 0,05 mm/m y se resolvió el problema de los ángulos de flexión inconsistentes entre los extremos izquierdo y derecho de las piezas dobladas.
Conclusión
En conclusión, al doblar una placa de alta resistencia, es importante determinar su radio mínimo de curvatura y su tendencia a la recuperación elástica mediante experimentación.
Con base en estos hallazgos, es necesario garantizar la precisión de la plegadora, la precisión del molde y la uniformidad del espesor de la placa.
Una mayor optimización y ajuste de la técnica de doblado de la plegadora, como la optimización del método de posicionamiento, puede ayudar a reducir efectivamente los defectos en el doblado de placas de alta resistencia y mejorar la tasa de paso del producto.