Con el continuo desarrollo de la tecnología de corte por plasma, el uso de máquinas de corte por plasma CNC se está generalizando cada vez más.
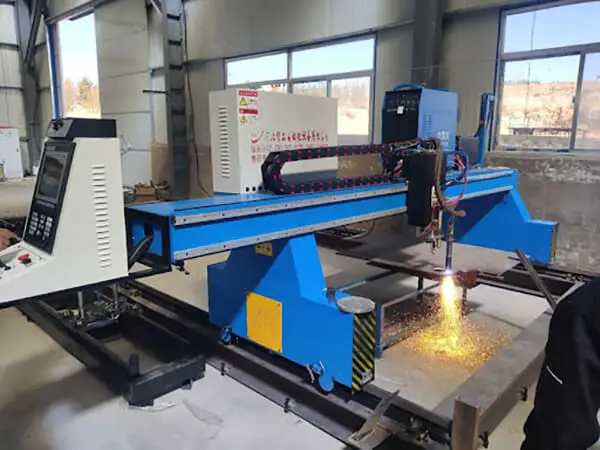
La máquina de corte por plasma CNC es uno de los principales equipos de corte y estampado utilizados para láminas de espesor medio y pequeño. Ofrece numerosos beneficios, como fácil operación, alta precisión, alta eficiencia en el trabajo y baja intensidad de mano de obra.
Es ampliamente utilizado en diversos sectores, incluyendo la industria química, industria automotriz, industria de maquinaria, industria del transporte ferroviario, entre otros.
Cuando los métodos de corte tradicionales no pueden cortar materiales resistentes, las máquinas de corte por plasma CNC resultan útiles.
En términos de velocidad de corte, al cortar placas de acero al carbono de espesor medio y pequeño, la velocidad de corte por plasma CNC es más rápida que la velocidad de corte por llama tradicional, y la superficie de corte permanece lisa con una deformación mínima en caliente.
Además, el método de corte por plasma CNC es una opción más económica que el corte por láser.
Principio de corte por plasma
Un cortador de plasma funciona ionizando una mezcla de gases a través de un arco de alta frecuencia. Este gas ionizado, o plasma, luego se expulsa de la boquilla de corte debido a la presión del gas.
La temperatura del plasma es extremadamente alta, superando con creces el punto de fusión del material que se está cortando.
Esto hace que el material se derrita rápidamente y luego el material fundido es expulsado por el gas a alta presión de la boquilla. Este proceso produce una cantidad importante de humo y escoria fundida.
Por tanto, las cortadoras de plasma requieren sistemas de eliminación de polvo y escoria. Al utilizar diferentes mezclas de gases, el plasma puede cortar metales de diferentes materiales y espesores, sobresaliendo particularmente en el corte de metales no ferrosos.
Elegir el proceso de corte por plasma
En el proceso de operación CNC (Control Numérico por Computadora) con una cortadora de plasma, la programación es el paso inicial. El proceso de mecanizado sigue una secuencia preprogramada.
En esta fase de programación, factores como la velocidad de corte, la secuencia de corte y el punto de partida juegan un papel clave para determinar la calidad del corte.
Selección del punto de partida
Lo ideal es que el punto de inicio del corte esté en el borde de la lámina o dentro de una costura previamente cortada. Si la boquilla está demasiado alejada del material, se producirá un corte incompleto, lo que provocará un desperdicio innecesario de material.
Por otro lado, si la boquilla está demasiado cerca, podría provocar un cortocircuito. Esto no sólo daña el material y afecta la calidad del corte, sino que también puede dañar la boquilla.
Elegir la dirección de corte
La dirección de corte debe garantizar que el borde final a cortar esté en su mayor parte separado del material principal.
Si se suelta prematuramente, es posible que la estructura delgada alrededor de la pieza no resista la tensión térmica del corte, lo que hace que la pieza se desplace durante el proceso de corte. Este cambio puede provocar imprecisiones dimensionales que afecten a la calidad del corte.
Seleccionar la secuencia de corte
Durante la programación, para maximizar la utilización del material, la pieza suele anidarse dentro de la chapa.
Por tanto, la secuencia de corte dicta el orden de eliminación del material. Generalmente, la secuencia sigue el principio de cortar piezas más pequeñas antes que las más grandes y cortar los contornos internos antes que los externos.
De lo contrario, la tensión generada al cortar contornos internos o piezas más pequeñas puede provocar una concentración de tensiones, dando como resultado una pieza desechada.
Elegir la velocidad de corte
La selección de la velocidad de corte está influenciada por varios factores, como el tipo y espesor del material, el diseño de la boquilla, la corriente de corte y el gas elegido.
Sin embargo, bajo la misma potencia y condiciones, una velocidad de corte más rápida da como resultado un chaflán más grande en la pieza de trabajo.
Por lo tanto, la boquilla debe estar perpendicular al material durante el corte para facilitar una rápida eliminación de la escoria. Para garantizar la eficiencia, se debe elegir la velocidad máxima de corte sin comprometer la calidad del corte.
Optimización de la mesa de corte
La mesa de corte de la máquina cortadora está sostenida por varios diafragmas. Como se ilustra en la Figura 1, la distancia entre dos diafragmas es de 110 mm.
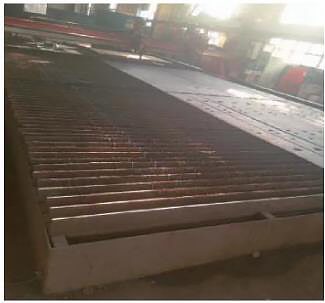
Fig.1 Máquina de corte por plasma CNC con mesa de corte
Al cortar piezas pequeñas, la pieza suele acabar entre los diafragmas, lo que dificulta su recuperación. El diafragma en sí es una placa de acero plana y recta que mide 8 mm × 190 mm × 4600 mm. Debido a los cortes frecuentes, el diafragma inferior acumula una cantidad significativa de escoria de óxido, lo que puede afectar negativamente la calidad del corte. Como resultado, requiere una limpieza o reemplazo frecuente para mantener las operaciones de corte normales.
Esquema de optimización e implementación de la mesa de corte
En la industria, las estructuras de productos y los lotes a menudo no son fijos, lo que lleva al uso de agrupaciones para ahorrar materiales. Se trata de combinar la composición tipográfica de materiales grandes y pequeños.
Actualmente, necesitamos abordar la cuestión de cómo aumentar la tasa de utilización de las máquinas de corte por plasma y extender la vida útil de los bancos de corte mediante la innovación en los procesos de los bancos de plasma.
Para abordar este desafío, primero analizamos y clasificamos los productos ciegos existentes. Luego seleccionamos la pieza de corte más pequeña, determinamos su tamaño y diseñamos un nuevo conjunto de banco de acuerdo con las condiciones del sitio, como se muestra en la Figura 2.
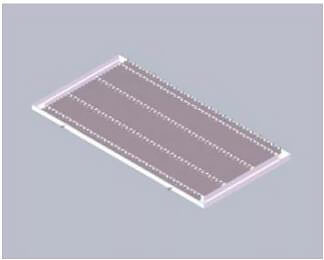
Fig. 2 Modelo de mesa después de la optimización de la máquina de corte por plasma CNC
(1) Régimen específico.
- La plataforma tiene un tamaño de 1500 mm × 3000 mm y se puede combinar con múltiples plataformas.
- La estructura externa de la plataforma está hecha de placas de 4 mm que se doblan en forma de U y se sueldan en una estructura rectangular. Este diseño garantiza la rigidez de la estructura y evita deformaciones durante el levantamiento.
- Dentro del marco hay 2-3 piezas en forma de V que se pliegan en placas de 4 mm y se pliegan longitudinalmente dentro del marco. Además, se corta una muesca de 3,5 mm de ancho en la viga longitudinal para facilitar la inserción del diafragma.
- El diafragma está hecho de una placa de 1500 mm × 200 mm con un lado cortado en una estructura dentada.
(2) Proceso de implementación específico.
- Diseñe el largo, ancho, alto y espaciado de las particiones de la mesa de corte según los parámetros del equipo y el tamaño de las piezas de corte requeridas.
- Realice el banco de corte según el plano del proyecto.
- Todas las piezas de la mesa de corte se cortan a la vez utilizando una máquina de corte CNC, lo que da como resultado tamaños precisos y un reemplazo conveniente del diafragma.
- El marco de la mesa de corte se programa y se dobla mediante una prensa plegadora CNC, lo que da como resultado un tamaño de posicionamiento preciso y una buena formabilidad.
- Ensamble, suelde y construya el marco del banco de corte.
- Inserte el diafragma en la mesa de corte.
- Coloque la mesa de corte sobre la mesa de corte original. Al cortar, coloque el material en la mesa de corte móvil para cortar, como se muestra en la Figura 3.
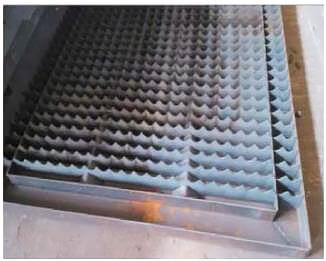
Fig. 3 Dibujo físico de la mesa de trabajo después de la optimización de la máquina de corte por plasma CNC.
Optimización de trayectoria en el proceso de corte.
Durante el proceso de corte, existe un movimiento relativo entre la pieza mecanizada y el material restante debido al efecto de expansión térmica y contracción en frío de la placa.
El movimiento relativo se puede clasificar en tres situaciones según la diferencia entre el peso de la pieza mecanizada y el peso del material restante:
- Cuando el peso de la pieza mecanizada es mayor que el peso del material restante, la pieza mecanizada permanece estacionaria mientras el material restante se mueve con respecto a la plataforma. Esto no afecta el tamaño de la pieza mecanizada.
- Cuando el peso de la pieza mecanizada es menor que el peso del material restante, la pieza mecanizada se mueve con respecto a la plataforma mientras el material restante permanece estacionario. Esto da como resultado una cierta desviación en la pieza mecanizada.
- Cuando el peso de la pieza mecanizada es igual al peso del material restante, tanto la pieza mecanizada como el material restante pueden moverse con respecto a la plataforma, lo que puede afectar el tamaño de la pieza mecanizada.
La práctica ha demostrado que el error dimensional de las piezas mecanizadas suele oscilar entre 0,3 y 4 mm debido al movimiento relativo de la pieza mecanizada o del material restante con respecto a la plataforma.
La ruta de corte en un lado de la pieza de trabajo.
Seleccionar un proceso de corte razonable puede resultar en diversos grados de deformación durante el proceso de corte por plasma CNC.
Al cortar la placa que se muestra en la Figura 4, si se elige el punto A como punto inicial del arco, la secuencia y dirección de corte debe ser: A → D → C → B → A (ver Figura 4a).
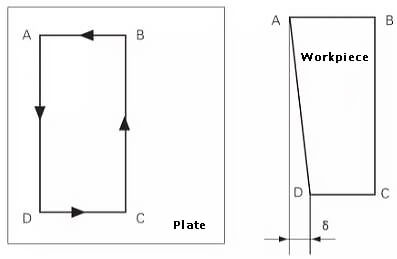
Fig.4 Ruta de corte y deformación de un lado de la pieza de trabajo
Cuando se corta la sección AD y se procesa la sección DC, el material residual estrecho en la sección DC se alarga linealmente debido a la alta temperatura durante el corte, lo que hace que la sección CB se desvíe hacia afuera.
Después del corte, el tamaño de la sección de CC se reduce en δ (como se muestra en la Fig. 4b). El valor de δ es proporcional al tamaño de la sección de CC.
Si se selecciona la secuencia de corte A → B → C → D → A, la pieza de trabajo se puede separar de la placa base a través de DA, lo que puede reducir efectivamente la deformación del corte.
Control de deformación de piezas delgadas.
Al cortar las piezas delgadas que se muestran en la Figura 5, siguiendo la secuencia A→B→C→D→A, la expansión de la sección BC puede evitar la expansión de la sección CD al cortar la sección DA.
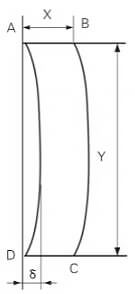
Fig.5 Cortar piezas finas
Después del proceso de corte y enfriamiento, la sección DA debe sufrir más contracción que la sección BC para doblar la pieza hacia el lado DA.
La cantidad de flexión lateral δ depende de la relación largo-ancho Y/X de la pieza mecanizada. A medida que aumenta la relación largo-ancho, también aumenta la cantidad de flexión lateral δ.
Cuando utilice dos pares para cortar, como se muestra en la Figura 6, elija el punto A como punto inicial del arco y siga la dirección y secuencia de corte: A → B → C → D → E → A → F.
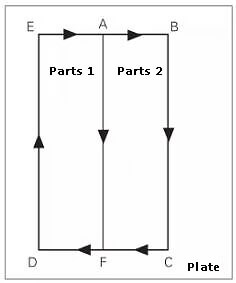
Fig.6 Corte emparejado de dos piezas finas
Cuando se trabaja en la sección DE, retirarla de la placa base es comparable a reducir a la mitad la relación largo-ancho de la pieza de trabajo, lo que resulta en una reducción en la cantidad de flexión lateral.
Al cortar la sección AF, la expansión y contracción en ambos lados de la pieza son uniformes, lo que conduce a una reducción considerable de la deformación δ de las piezas esbeltas.
Tecnología para cortar piezas con formas especiales.
Para cortar piezas especiales (Fig. 7), se pueden seleccionar los siguientes procesos de corte de acuerdo con los métodos de procesamiento anteriores y diferentes piezas con formas especiales.
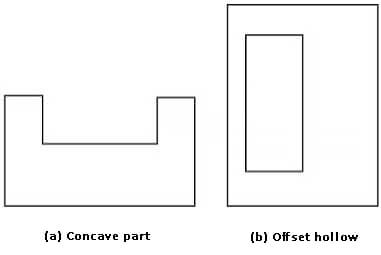
Fig.7 Corte de piezas especiales
(1) Para piezas cóncavas, se adoptan dos métodos de corte por pares.
Primero cortando el borde interior, luego cortando el borde exterior y finalmente separando las dos partes de fuera hacia dentro.
La secuencia de corte se muestra en la Fig.
El borde interior: A1 → B1 → C1 → D1 → A1;
Afuera: A → B → C → D → A y finalmente E → F, H → G.
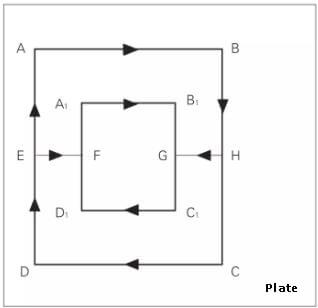
Fig.8 Corte emparejado de dos partes cóncavas.
(2) Para piezas huecas desplazadas, se deben cortar dos piezas en pares y finalmente se deben separar las dos piezas.
La secuencia de corte se muestra en la Fig.
El lado interior: A1 → B1 → C1 → D1 → A1, A2 → B2 → C2 → D2 → A2
El lado exterior: A → B → C → D → A y finalmente E → F.
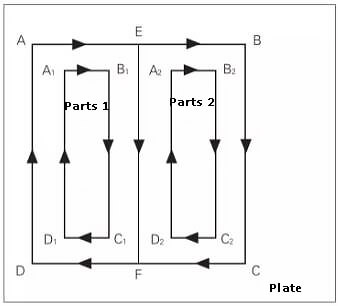
Fig. 9 Corte por parejas de dos piezas huecas desplazadas
Optimización de equipos de plasma
Durante el proceso de corte por plasma de aire, la parte superior del núcleo del electrodo sufre una reacción de oxidación a alta temperatura con el oxígeno del aire, por lo que el desgaste del electrodo es inevitable.
La vida útil de un electrodo está relacionada con el número de inicios de arco; En las mismas condiciones, cuanto más se inicia el arco, más se desgasta el electrodo. El inicio frecuente del arco reduce significativamente la vida útil del electrodo.
Sin embargo, el proceso de corte continuo reduce el número de puntos de inicio para piezas con bordes no comunes, de modo que las piezas con bordes compartidos tienen solo un punto de inicio de corte.
Esto reduce el número de inicios de arco durante el corte, aumentando así la vida útil del electrodo.
Conclusión
La innovación de procesos tiene varios efectos beneficiosos. En primer lugar, mejora enormemente la tasa de utilización de la máquina de corte por plasma. En segundo lugar, reemplazar el diafragma de la mesa de trabajo es conveniente y reduce la tasa de reemplazo a la mitad, reduciendo así el costo de reemplazo. En tercer lugar, puede cumplir con los requisitos de corte de piezas pequeñas.
Actualmente, esta innovación de proceso se utiliza ampliamente en el corte de estructuras metálicas para vagones de ferrocarril de pasajeros. Como cada automóvil tiene muchas piezas pequeñas que deben cortarse y cegarse, esta innovación mejora la eficiencia del trabajo y ahorra costos.
Cuando se utiliza el corte por plasma, se deben considerar los siguientes problemas: se debe analizar la ley de deformación y la influencia del corte de piezas en las máquinas de corte por plasma CNC. Antes del corte se debe realizar un tratamiento adecuado de nivelación de la placa y fijar la placa para evitar el movimiento de las piezas mecanizadas durante el corte.
Al compilar el programa de corte, se debe seleccionar un proceso de corte razonable para separar la superficie de tamaño máximo de la pieza de trabajo de la placa base. Para cortar piezas delgadas o con formas especiales, los métodos de control, como el corte emparejado de dos piezas, pueden prevenir o reducir eficazmente la deformación de las piezas cortadas.
En comparación con el corte por llama, el corte por plasma CNC es superior en términos de calidad de corte y beneficios en la industria de procesamiento. Puede cortar todo tipo de metales con diferentes gases de trabajo, especialmente metales no ferrosos.