El mecanizado por descarga eléctrica (EDM) y el mecanizado electroquímico (ECM) solo pueden procesar materiales metálicos conductores y no pueden trabajar con materiales no metálicos no conductores.
Por el contrario, el mecanizado ultrasónico (USM) no sólo permite el procesamiento de materiales metálicos duros y quebradizos, como aleaciones duras y acero endurecido, sino que también es más adecuado para trabajar con materiales no metálicos no conductores, como vidrio, cerámica y semiconductores. , obleas de germanio y silicio.
Además, USM se puede utilizar para aplicaciones como limpieza, soldadura y pruebas no destructivas.
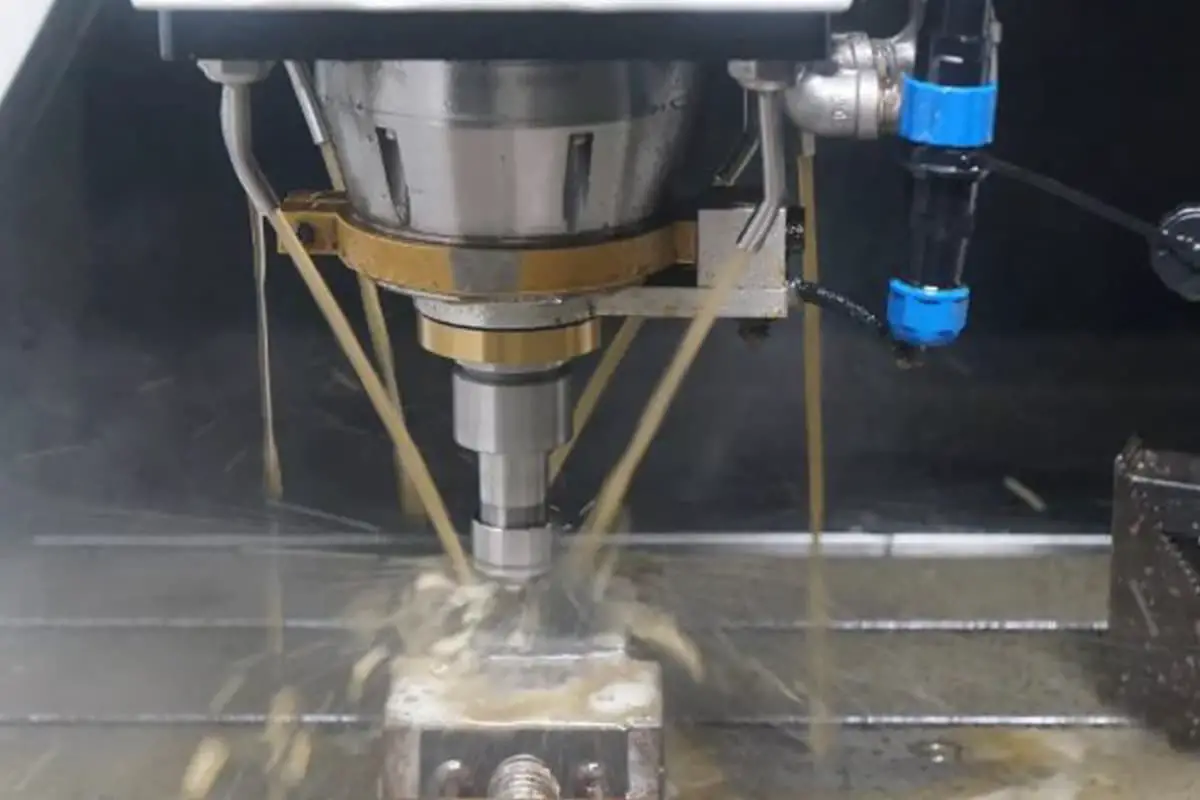
La soldadura ultrasónica utiliza ondas de vibración de alta frecuencia transmitidas a las superficies de dos objetos que deben soldarse. Bajo presión, las dos superficies rozan entre sí, lo que da como resultado la fusión entre las capas moleculares.
Los componentes necesarios para la soldadura ultrasónica incluyen un generador ultrasónico, un convertidor, un amplificador y herramientas de soldadura.
I. Principios del mecanizado ultrasónico
Los componentes principales de un sistema de soldadura ultrasónica incluyen un conjunto trío de generador ultrasónico, transductor, impulsores, cabezal de soldadura, molde y marco.
La soldadura por ultrasonidos consiste en convertir una corriente de 50/60 Hz en energía eléctrica de 15, 20, 30 o 40 KHz mediante un generador de ultrasonidos. La energía eléctrica de alta frecuencia convertida se transforma nuevamente en movimiento mecánico de la misma frecuencia a través de un transductor.
Posteriormente, el movimiento mecánico se transfiere al cabezal de soldadura a través de un conjunto de dispositivos de refuerzo que pueden cambiar la amplitud. El cabezal de soldadura transmite la energía vibratoria recibida a la unión de la pieza a soldar. En esta región, la energía vibratoria se convierte en energía térmica a través de la fricción, fusionando las áreas que necesitan soldarse.
El ultrasonido se puede utilizar no sólo para soldar metales y plásticos termoendurecibles, sino también para procesar tejidos y películas.
Específicamente, el mecanizado ultrasónico (USM) es un método de procesamiento de materiales duros y quebradizos mediante el uso de vibración ultrasónica en la cara final de la herramienta, combinada con la acción de la suspensión abrasiva.
USM es el resultado de los efectos combinados del impacto mecánico y el pulido abrasivo causado por la vibración de los abrasivos bajo ondas ultrasónicas, siendo el impacto continuo de los abrasivos el factor principal.
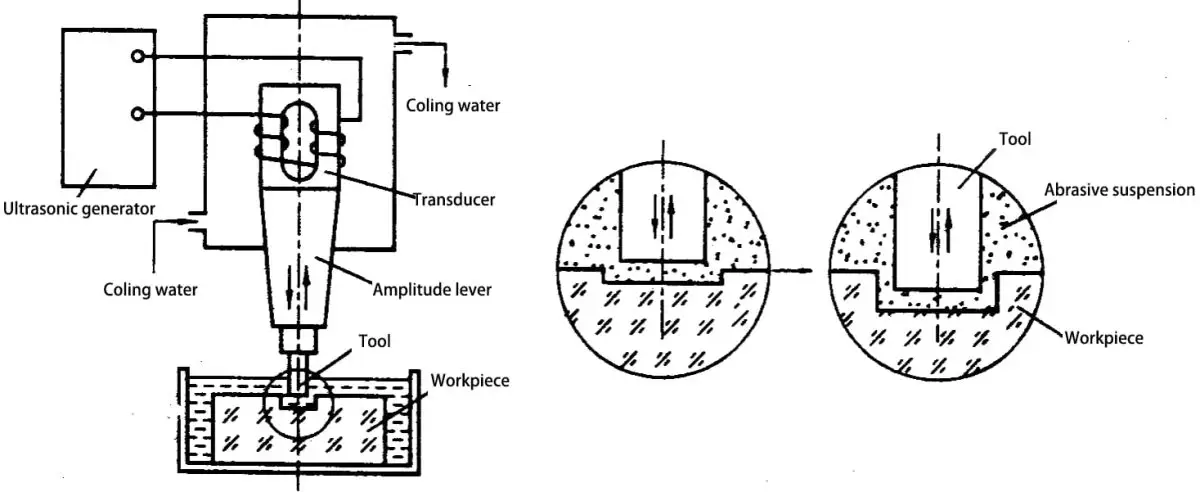
Durante el proceso de mecanizado por ultrasonidos, se introduce una suspensión de una mezcla líquida y abrasiva entre el cabezal de la herramienta y la pieza de trabajo. Se aplica una ligera presión en la dirección de vibración del cabezal de la herramienta.
La frecuencia ultrasónica generada por el generador ultrasónico es transformada en vibraciones mecánicas por el transductor. La amplitud se amplifica a 0,01-0,15 mm mediante la varilla de amplitud y luego se transmite a la herramienta.
La cara del extremo de la herramienta vibra ultrasónicamente, lo que hace que las partículas abrasivas en la suspensión impacten y muelen continuamente la superficie de la pieza de trabajo a alta velocidad. Esto da como resultado que el material se triture en la zona de mecanizado en partículas finas, que luego se eliminan del material.
Aunque cada impacto elimina una pequeña cantidad de material, la alta frecuencia de más de 16.000 impactos por segundo permite cierta velocidad de procesamiento.
Al mismo tiempo, el impacto hidráulico y el fenómeno de cavitación causado por la vibración ultrasónica en el extremo de la herramienta hacen que el líquido penetre en las grietas del material de la pieza de trabajo, acelerando el proceso de destrucción.
El impacto hidráulico también obliga al fluido de trabajo de la suspensión a circular en el espacio de mecanizado, asegurando la renovación oportuna de las partículas abrasivas desgastadas.
1) Principio de la soldadura de metales por ultrasonidos.
El principio de la soldadura ultrasónica de metales implica la utilización de energía vibratoria mecánica a frecuencias ultrasónicas (superiores a 16 KHz) para conectar metales idénticos o diferentes de una manera única.
Durante el proceso de soldadura ultrasónica, no se transmite corriente a la pieza de trabajo ni se aplica una fuente de calor de alta temperatura. La energía vibratoria simplemente se convierte en trabajo de fricción y energía de deformación entre las piezas, junto con un aumento limitado de temperatura, bajo presión estática.
La unión termoquímica entre juntas es un proceso de soldadura de estado sólido que se produce sin fundir el material original. Como tal, supera eficazmente los problemas de oxidación y salpicaduras que se producen durante la soldadura por resistencia.
Las máquinas de soldadura de metales por ultrasonidos pueden realizar soldaduras de un solo punto, soldaduras multipunto y soldaduras de tiras cortas en alambres delgados o láminas delgadas de metales no ferrosos como cobre, plata, aluminio y níquel. Se utilizan ampliamente para soldar cables de tiristores, regletas de fusibles, cables eléctricos, piezas polares de baterías de litio y orejas polares.
2) Principio de la soldadura plástica por ultrasonidos.
Cuando las ondas ultrasónicas actúan sobre la superficie de contacto de los materiales termoplásticos, generan vibraciones de alta frecuencia decenas de miles de veces por segundo. Esta vibración de alta frecuencia, al alcanzar una determinada amplitud, se transmite a la zona de soldadura mediante soldadura, convirtiendo la energía ultrasónica en calor.
La resistencia acústica en la unión de las dos soldaduras en la zona de soldadura es elevada, generando elevadas temperaturas locales. Debido a la mala conducción del calor de los plásticos, el calor no se puede disipar inmediatamente y se acumula en la zona de soldadura, provocando que las superficies de contacto de los dos plásticos se fundan rápidamente.
Al aplicar una cierta cantidad de presión, los plásticos se fusionan en uno solo. Cuando cesan las ondas ultrasónicas, se mantiene la presión durante unos segundos para permitir la solidificación, formando una cadena molecular robusta para lograr el propósito de soldar. La resistencia de la soldadura puede aproximarse a la resistencia del material original.
La calidad de la soldadura de plástico por ultrasonidos depende de tres factores: la amplitud del cabezal de soldadura del transductor, la presión aplicada y el tiempo de soldadura. Tanto el tiempo de soldadura como la presión del cabezal de soldadura se pueden ajustar, mientras que la amplitud está determinada por el transductor y la varilla de amplitud.
Estos tres factores interactúan y tienen un valor óptimo. Cuando la energía excede este valor ideal, la cantidad de plástico fundido es alta y el material soldado está sujeto a deformación.
Si la energía es demasiado baja, la soldadura resultante no será firme y la presión aplicada no deberá ser demasiado alta. La presión ideal es el producto de la longitud del borde de la pieza soldada y la presión ideal por milímetro del borde.
II. Características del mecanizado ultrasónico.
1. Amplia gama de aplicaciones:
El. Puede procesar metales y materiales no metálicos tradicionalmente difíciles de mecanizar, como acero templado, acero inoxidable, titanio, aleaciones y, especialmente, materiales no metálicos no conductores, como vidrio, cerámica, cuarzo, silicio, ágata y piedras preciosas. y diamantes. También puede procesar materiales metálicos conductores duros como acero endurecido y aleaciones duras, aunque con menor productividad.
B. Adecuado para procesar agujeros profundos, piezas de paredes delgadas, varillas delgadas, componentes de baja rigidez y piezas de formas complejas con altos requisitos.
w. Ideal para mecanizado de precisión de componentes de alta precisión y baja rugosidad superficial.
2. Baja fuerza de corte y consumo de energía:
Debido al impacto instantáneo localizado, el mecanizado ultrasónico impone una fuerza de corte macroscópica mínima, lo que reduce la tensión de corte y el calor.
3. Alta precisión de mecanizado y baja rugosidad superficial:
El mecanizado ultrasónico puede lograr una alta precisión de mecanizado (precisión dimensional de hasta 0,005-0,02 mm) y una baja rugosidad superficial (valor Ra de 0,05-0,2). El proceso no deja tensiones residuales ni marcas de quemaduras en la superficie mecanizada, lo que lo hace adecuado para paredes delgadas, espacios estrechos y componentes de baja rigidez.
4. Adecuado para procesar cavidades de formas complejas y superficies moldeadas.
5. Las herramientas pueden estar hechas de materiales relativamente blandos con formas complejas.
6. Los equipos de mecanizado ultrasónico generalmente tienen una estructura simple, lo que los hace fáciles de operar y mantener.
III. Leyes del proceso de mecanizado ultrasónico
1. Velocidad de mecanizado y factores que influyen:
La velocidad de mecanizado se refiere a la cantidad de material eliminado por unidad de tiempo y se expresa en mm 3 /min o g/min.
Los factores que influyen en la velocidad de mecanizado incluyen la amplitud y frecuencia de la herramienta, la presión de alimentación, el tipo y tamaño de las partículas abrasivas, el material de la pieza de trabajo y la concentración de la suspensión abrasiva.
El. Influencia de la amplitud y frecuencia de la herramienta:
Una amplitud excesiva y una frecuencia alta pueden someter a la herramienta y a la varilla de amplitud a tensiones internas elevadas. La amplitud está generalmente entre 0,01 y 0,1 mm y la frecuencia está entre 16.000 y 25.000 Hz.
En el mecanizado real, es necesario ajustar la frecuencia de resonancia según las diferentes herramientas para obtener la máxima amplitud y lograr una mayor velocidad de mecanizado.
B. Influencia de la presión de suministro:
La herramienta debe tener una presión de suministro adecuada durante el mecanizado. Una presión muy baja aumenta el espacio entre la cara del extremo de la herramienta y la superficie de la pieza, reduciendo la fuerza de impacto del abrasivo sobre la pieza.
El aumento de la presión reduce la holgura, pero cuando la holgura disminuye hasta cierto punto, reducirá la circulación y la velocidad de renovación del abrasivo y del fluido de trabajo, disminuyendo así la productividad.
w. Influencia del tipo de abrasivo y tamaño de partícula:
Se pueden seleccionar diferentes abrasivos para materiales con diferentes resistencias durante el mecanizado. Una mayor resistencia abrasiva da como resultado una mayor velocidad de mecanizado, pero también se debe considerar el costo. Para procesar materiales como piedras preciosas o diamantes, se deben utilizar abrasivos de diamante.
El carburo de boro es adecuado para mecanizar acero endurecido y aleaciones duras, mientras que los abrasivos de óxido de aluminio se utilizan para procesar materiales como vidrio, cuarzo, silicio y germanio.
d. Influencia del material de la pieza:
Los materiales duros y quebradizos son más fáciles de eliminar durante el mecanizado, mientras que los materiales con buena tenacidad son más difíciles de procesar.
Es. Influencia de la concentración de la suspensión abrasiva:
Una menor concentración de suspensión abrasiva significa menos partículas abrasivas en el espacio de mecanizado, lo que puede conducir a una disminución significativa en la velocidad de mecanizado, especialmente para áreas de superficie grandes y profundidades profundas.
Aumentar la concentración de abrasivos mejora la velocidad de mecanizado, pero una concentración excesivamente alta puede afectar la circulación y el impacto de las partículas abrasivas en el área de mecanizado, provocando una disminución de la velocidad de mecanizado.
2. Precisión del mecanizado y factores que influyen:
La precisión del mecanizado ultrasónico está influenciada por la precisión de la máquina herramienta y los accesorios, así como por el tamaño de las partículas abrasivas, la precisión y el desgaste de la herramienta, la magnitud de la vibración lateral, la profundidad de mecanizado y las propiedades del material de la pieza de trabajo.
3. Calidad de la superficie:
El mecanizado ultrasónico proporciona una excelente calidad superficial, sin generar capas superficiales ni marcas de quemaduras. La rugosidad de la superficie depende principalmente del tamaño de las partículas abrasivas, la amplitud ultrasónica y la dureza del material de la pieza.
Un tamaño de partícula abrasivo más pequeño, una amplitud ultrasónica más baja y un material de pieza de trabajo más duro conducen a una mejor rugosidad de la superficie, ya que el valor de rugosidad está determinado principalmente por el tamaño y la profundidad de las ranuras dejadas por el impacto de cada partícula abrasiva en el material de la pieza de trabajo.
Aunque la productividad del mecanizado ultrasónico es menor en comparación con el mecanizado por descarga eléctrica y el mecanizado electroquímico, su precisión de mecanizado y calidad de superficie son superiores.
Es importante destacar que puede procesar materiales semiconductores y no metálicos duros y quebradizos, como vidrio, cerámica, cuarzo, silicio, ágata, piedras preciosas y diamantes, que son difíciles de mecanizar con otros métodos.
Además, a menudo se emplea en las etapas finales de acabado de acero endurecido, moldes de aleaciones duras, matrices de trefilado y moldes de plástico procesados mediante mecanizado por descarga eléctrica, para reducir aún más la rugosidad de la superficie.
4. Aplicaciones de mecanizado ultrasónico
1. Mecanizado de cavidades y moldes:
El mecanizado ultrasónico se utiliza principalmente para procesar orificios circulares, orificios perfilados, cavidades, casquillos y microagujeros en materiales duros y quebradizos.
2. Procesamiento de corte:
El mecanizado ultrasónico es adecuado para cortar materiales duros y quebradizos como cerámica, cuarzo, silicio y piedras preciosas, que son difíciles de cortar con métodos convencionales. Ofrece ventajas como lonchas finas, cortes estrechos, alta precisión, alta productividad y rentabilidad.
3. Limpieza ultrasónica:
Este método se basa en el efecto de cavitación que produce la solución limpiadora bajo la acción de ondas ultrasónicas. El fuerte impacto que genera la cavitación actúa directamente sobre la superficie a limpiar, provocando que los residuos se desintegren y se desprendan de la superficie.
Este método se utiliza principalmente para la limpieza de precisión de piezas de precisión de tamaño pequeño y mediano con geometrías complejas, donde otros métodos de limpieza son menos efectivos, especialmente para orificios profundos, microagujeros, orificios curvos, orificios ciegos, ranuras, ranuras estrechas, etc. Proporciona alta productividad y tasas de purificación.
Actualmente, se aplica a la limpieza de componentes de circuitos integrados y semiconductores, piezas de instrumentos, dispositivos electrónicos de vacío, componentes ópticos e instrumentos médicos.
4. Soldadura ultrasónica:
La soldadura ultrasónica utiliza vibración ultrasónica para eliminar la película de óxido de la superficie de las piezas, exponiendo la superficie del material base. El impacto vibratorio de alta velocidad entre las dos superficies de la pieza soldada provoca calentamiento y unión por fricción.
Puede usarse para soldar productos de nailon, plástico y aluminio propensos a la formación de películas de óxido. También se puede utilizar para aplicar estaño o plata a las superficies de cerámica y otros materiales no metálicos, mejorando su soldabilidad.
5. Mecanizado de compuestos:
Para aumentar la velocidad de mecanizado y reducir el desgaste de la herramienta al mecanizar materiales metálicos duros, como aleaciones duras y aleaciones resistentes al calor, se emplea mecanizado combinado asistido por ultrasonidos con mecanizado electroquímico o por descarga eléctrica.
Esto se utiliza a menudo para mecanizar orificios o ranuras estrechas en componentes como inyectores de combustible y placas de trefilado, lo que mejora significativamente la productividad y la calidad.
El corte por vibración ultrasónico (por ejemplo, torneado, taladrado, roscado) también se ha desarrollado durante varias décadas como una nueva tecnología para el mecanizado de precisión y materiales difíciles de cortar, reduciendo las fuerzas de corte, la rugosidad de la superficie, el desgaste de las herramientas y aumentando la productividad.
Algunas aplicaciones comúnmente utilizadas incluyen torneado por vibración ultrasónica, rectificado por vibración ultrasónica, mecanizado ultrasónico de orificios profundos, orificios pequeños y roscado, entre otras.