El acero inoxidable austenítico es uno de los principales materiales utilizados en las estructuras de los reactores nucleares, que contienen una gran cantidad de piezas soldadas.
Una pequeña cantidad de ferrita δ en soldaduras de acero inoxidable puede mejorar la resistencia y la resistencia a la corrosión intergranular de la soldadura y prevenir el agrietamiento en caliente en la soldadura. Sin embargo, demasiada ferrita δ provocará fragilidad en la fase σ y corrosión selectiva en la fase δ.
El contenido de ferrita δ es uno de los índices técnicos importantes para el desarrollo y la evaluación del rendimiento de la aplicación de materiales de soldadura de acero inoxidable austenítico.
En la actualidad, los métodos comúnmente utilizados para determinar el contenido de ferrita δ en soldaduras de acero inoxidable austenítico son el método metalográfico, el método químico y el método magnético.
El método metalográfico calcula la relación de área observando directamente la ferrita δ en la muestra metalográfica y luego calcula la fracción de volumen. Este método es destructivo y requiere un número suficiente de puntos de medición para obtener datos con alta confiabilidad, lo que aumenta el costo de detección.
El método químico puede obtener indirectamente el contenido de ferrita δ (fracción de masa) calculando el equivalente de níquel y el equivalente de cromo en el material y comparando el diagrama empírico. El diagrama de Schaeffer, el diagrama de Delong y el diagrama WRC-92 son tres diagramas que se utilizan comúnmente en los métodos químicos actuales. El diagrama de Schaeffer fue el primero en aplicarse, pero no consideraba la influencia del nitrógeno y el cobre. El diagrama de Delong incluye nitrógeno como elemento formador de austenita y mejora la precisión de la curva. El diagrama de la CMR-92 también considera el nitrógeno y el cobre.
El método químico también tiene algunos problemas, como la precisión del contenido de elementos de aleación, que afecta directamente la precisión del cálculo del contenido de ferrita δ, y la no linealidad del efecto de los elementos de aleación sobre el contenido de ferrita δ, lo que conduce a una cierta desviación entre el valor medido y el valor real.
El método magnético determina el contenido de ferrita δ midiendo una cierta cantidad física magnética relacionada con el contenido de ferrita δ. Sin embargo, este método se ve muy afectado por el principio del instrumento de medición, y si el contenido o la morfología de ferrita δ en el material es desigual, la reproducibilidad y precisión de los resultados serán deficientes.
El método magnético es fácil de operar y puede realizar pruebas no destructivas in situ, que se utilizan comúnmente. En la detección real, generalmente se seleccionan uno o dos métodos para la medición.
Investigadores del Laboratorio Clave de Combustibles y Materiales de Reactores del Instituto de Investigación y Diseño de Energía Nuclear de China utilizaron simultáneamente los tres métodos anteriores para medir el contenido de ferrita δ de la capa superficial de acero inoxidable austenítico para energía nuclear, y compararon y analizaron las diferencias en resultados de medición obtenidos mediante diferentes métodos de detección.
1. Contenido de la prueba
1.1 Materiales de prueba
El objeto de investigación es una tapa de acero inoxidable 308 con un tamaño de muestra de 50 mm × 25 mm × 10 mm. Su composición química cumple con las especificaciones descritas en ASTM A276-2006 para barras y perfiles de acero inoxidable.
1.2 Patrones de prueba
Las pruebas metalográficas se llevaron a cabo de acuerdo con las normas GB/T 1954-2008 para medir el contenido de ferrita de soldaduras de acero inoxidable austenítico de cromo-níquel y GB/T 15749-2008 para metalografía cuantitativa.
Además de los métodos de detección existentes, se llevó a cabo un análisis de la composición química utilizando los diagramas de Schaeffler y WRC-1992 para calcular el contenido de δ-ferrita.
Para medir el número de ferrita en el metal de soldadura de acero inoxidable austenítico al cromo-níquel, se utilizó el método magnético siguiendo los lineamientos de GB/T 1954-2008 y JB/T 7853-1995.
1.3 Equipo de prueba
El método metalográfico utilizado para la detección y análisis utilizó el microscopio metalográfico Olympus GX71 y su sistema de análisis de imágenes metalográficas TIGER3000.
En términos de análisis químico, se utilizó un analizador de carbono/azufre para detectar carbono y azufre, un espectrofotómetro para detectar silicio, fósforo y boro, y un espectrómetro de emisión atómica acoplado inductivamente para detectar otros elementos metálicos.
En cuanto a la medición del contenido de ferrita δ, el instrumento de medición de ferrita lo leyó directamente durante el método magnético.
2. Proceso de prueba y resultados
2.1 método metalográfico
Hay dos métodos metalográficos principales que se utilizan para medir el contenido de ferrita δ: el método de contraste del atlas de muestra estándar y el método de medición. Ambos métodos se pueden utilizar para medir el contenido de ferrita δ en la capa superficial del acero inoxidable 308.
2.1.1 Método de comparación de mapas
Según la norma GB/T 1954-2008, la muestra metalográfica se prepara y se observa al microscopio. Luego se selecciona para la fotografía un área relativamente uniforme de distribución de ferrita δ, como se muestra en la Figura 1.
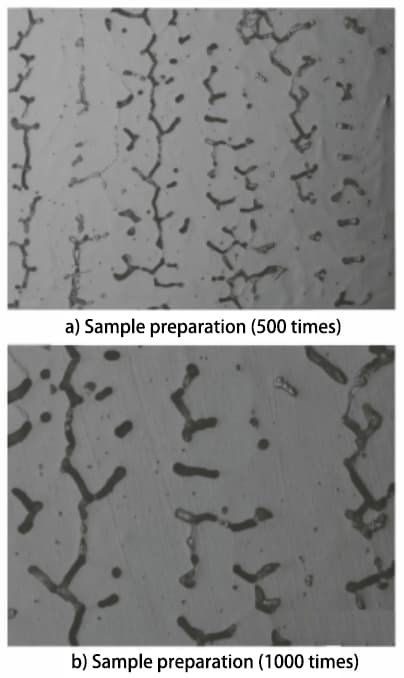
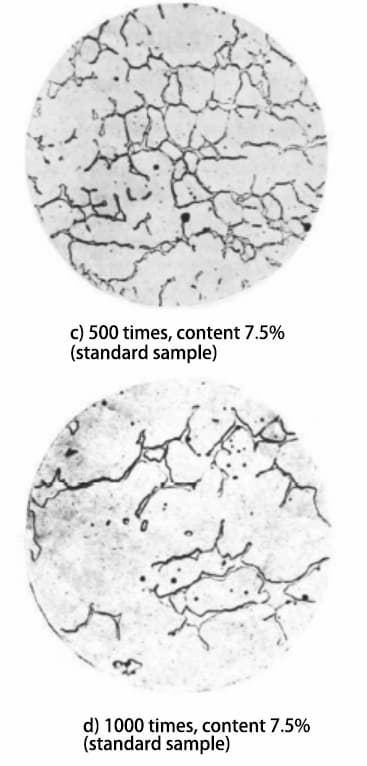
Fig. 1 Morfología microestructural de muestras preparadas y estándar.
Según las especificaciones descritas en la norma GB/T 1954-2008, la microestructura de la muestra metalográfica preparada debe observarse con un aumento no inferior a 500 veces. Se obtuvieron las microestructuras de la muestra preparada con aumentos de 500 y 1000 veces y se compararon con las microestructuras de muestras estándar con los mismos aumentos. Con base en esta comparación, se determinó que el contenido de ferrita δ en la muestra está entre 7,5% y 10%.
2.1.2 Método de medición
El estándar GB/T 15749-2008 es un estándar nacional que se aplica a la determinación de la fracción de volumen de fase en diversas microestructuras de aleaciones. Incluye una variedad de métodos de cálculo del contenido de fase, como el método de puntos numéricos de cuadrícula, el método de sección de cuadrícula y el método de calibración de segmentos de línea (incluido el método de cuatro líneas, el método de ocho líneas, etc.).
En comparación con el método de la secante metalográfica en GB/T 1954-2008, los métodos descritos en GB/T 15749-2008 tienen más líneas divisorias, un área de cobertura mayor y mayor precisión.
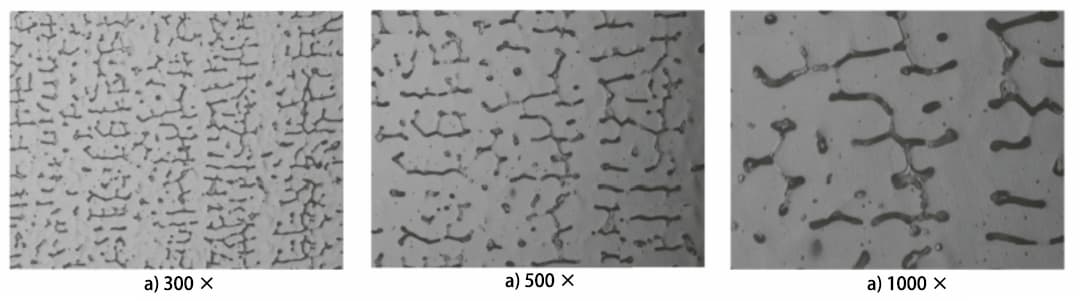
Fig. 2 Microestructura de δFerrita en la soldadura en la misma posición
Según el estándar GB/T 15749-2008, el método de sección de rejilla mide la muestra 300 veces, 500 veces y 1000 veces.
La figura 2 muestra la microestructura en la misma posición. El contenido promedio de ferrita δ medido en diferentes múltiplos es 11,0%, 7,6% y 9,5%, respectivamente (ver Tabla 1).
Tabla 1 δ Contenido de ferrita en el mismo lugar bajo diferentes tiempos de aumento
Amplificado | Fracción de masa | |||||||||
1 | dos | 3 | 4 | 5 | 6 | 7 | 8 | 9 | Valor medio | |
300 veces | 10 | 9.7 | 11.6 | 11.7 | 12.7 | 10.8 | 11.5 | 10.6 | 10.8 | 11 |
500 veces | 8.2 | 10 | 8.8 | 6.1 | 10.1 | 6.4 | 9.3 | 9.8 | 9.3 | 7.6 |
1000 veces | 10.6 | 11 | 8.2 | 7.7 | 10 | 7.8 | 10.5 | 10.8 | 9.6 | 9.6 |
La Tabla 1 muestra que el contenido de ferrita δ varía mucho con diferentes aumentos.
El contenido de ferrita δ más bajo se mide con un aumento de 500 veces, mientras que el contenido medido con 300 y 1000 aumentos es mayor.
Los resultados de las pruebas indican que la ampliación tiene un impacto significativo en los resultados del análisis metalográfico:
En las soldaduras, los granos de ferrita δ son generalmente muy pequeños. Con un aumento bajo (300x), la microestructura dentro del campo de visión parece muy densa, lo que dificulta discernir el borde del cálculo de segmentación de la imagen, lo que generalmente genera resultados más grandes.
Por otro lado, con un aumento muy alto (1000 veces), el área del campo de visión seleccionado es muy pequeña. Debido a que la tela en sí es desigual, es posible que tengas que medir más puntadas para obtener resultados precisos.
GB/T 1954-2008 especifica un aumento mínimo de 500 veces. Por lo tanto, es apropiado seleccionar un aumento de 500 veces para mediciones reales.
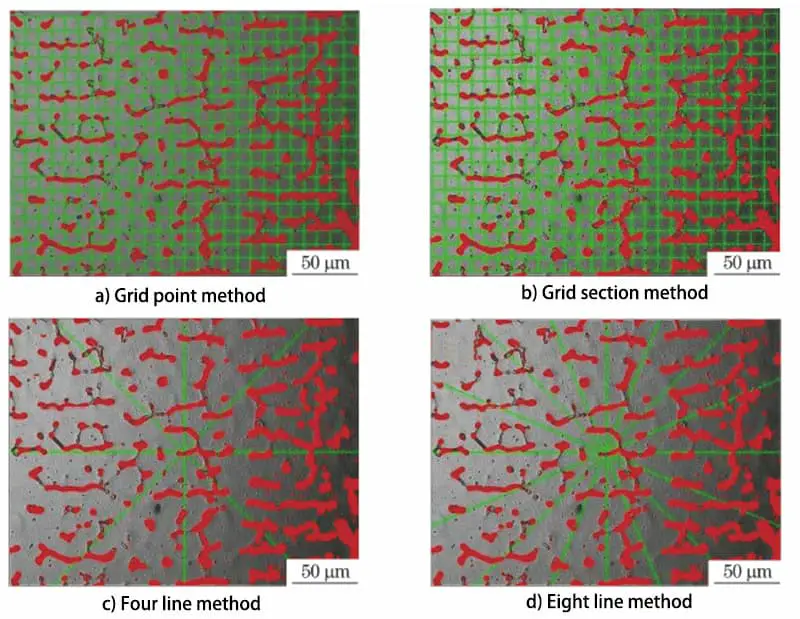
Fig. 3 Diagrama esquemático del método de medición del contenido de ferrita.
En las pruebas, utilizamos el método del número de cuadrícula, el método de la sección de cuadrícula, el método de cuatro líneas y el método de ocho líneas, respectivamente. Seleccionamos al azar 9 ubicaciones en 500 condiciones diferentes para medir el contenido de ferrita δ, y el método de medición se muestra en la Fig. 1.
Los resultados de estas mediciones fueron 7,6%, 7,6%, 6,7% y 7,6%, respectivamente, como se muestra en la Tabla 2.
Tabla 2: Contenido de ferrita δ medido en ubicaciones aleatorias por debajo de 500×
Posición y promedio | Punto numérico de cuadrícula | Sección de cuadrícula | cuatro lineas | Ocho lineas |
1 | 6.9 | 8.2 | 4.1 | 6.9 |
dos | 8.2 | 10 | 6.6 | 8.8 |
3 | 9.2 | 8.8 | 5.1 | 5.8 |
4 | 5.6 | 6.1 | 6.5 | 5.9 |
5 | 10.2 | 10.1 | 7.7 | 7.9 |
6 | 4.2 | 6.4 | 5.5 | 6.3 |
7 | 7.9 | 9.3 | 9 | 9.3 |
8 | 8.3 | 9.8 | 5.9 | 8.5 |
9 | 7.5 | 9.3 | 9.6 | 9.2 |
significar | 7.6 | 7.6 | 6.7 | 7.6 |
Según la Tabla 2, se puede observar que, con excepción del método de cuatro líneas, los resultados de medición de los otros tres métodos son los mismos.
2.2 método químico
La composición química de la capa superficial del acero inoxidable 308 se muestra en la Tabla 3 y cumple con los requisitos de los indicadores técnicos especificados.
Tabla 3 Composición química de la cubierta de acero inoxidable 308
W. | cr | No | Mes | Minnesota | co | Culo | V | s | B | PAG | Sí |
0,028 | 19:25 | 10.4 | 0.065 | 1.38 | 0,02 | 0,03 | 0,04 | 0.0078 | 0.0006 | 0.013 | 0,73 |
Según el diagrama de Schaeffler y su fórmula de cálculo, las fracciones de masa de cromo y níquel en el material de prueba son 20,41 % y 10,93 %, respectivamente, lo que indica un contenido de ferrita δ de aproximadamente 8,5 %.
Por otro lado, con referencia al valor de la CMR-1992, las fracciones másicas de cromo y níquel en el material de prueba son 19,315% y 10,24%, respectivamente, lo que resulta en un contenido de ferrita δ de aproximadamente 13%.
Es evidente que los resultados de los cálculos del método químico varían cuando se utilizan diferentes gráficos experimentales debido a la influencia de diversos factores.
Un análisis más detallado revela que la inclusión de cobre como equivalente de níquel en el diagrama de la CMR-1992, junto con el contenido de cobre del 0,03% del acero inoxidable 308, conduce a un contenido de ferrita δ calculado considerablemente mayor que el obtenido utilizando el diagrama de Schaeffler.
2.3 Método magnético
De acuerdo con las especificaciones dadas en GB/T 1954-2008 para la medición por método magnético, se deben seleccionar seis puntos al azar a lo largo de la dirección del cordón de soldadura de la capa superficial de acero inoxidable 308 con un promedio de cinco lecturas en cada punto, y la ferrita δ promedio. El contenido se calcula en 3,4%.
3 . Análisis y discusión
El contenido de ferrita α en la capa superficial del acero inoxidable 308 se midió mediante métodos metalográficos, químicos y magnéticos, como se muestra en la Tabla 4.
El contenido de ferrita δ en la estructura de soldadura del acero inoxidable austenítico normalmente está entre el 4% y el 12%.
Es evidente que el método magnético produjo mediciones más bajas, mientras que los resultados de las mediciones del diagrama de la CMR-1992 del método químico fueron mayores.
Tabla 4 Cobertura del acero inoxidable 308 medida por diferentes métodos δ Contenido de ferrita
Método de medida | δ - fracción de masa de ferrita | |
Metalografía (500 veces) | Método de contraste del atlas | 10.0 |
Método de medida | 7.6 | |
método químico | Gráfico de Schaeffler | 8.5 |
Gráfico de la CMR-1992 | 13.0 | |
método magnético | 3.4 |
Cuando se mide el contenido de ferrita δ utilizando diferentes métodos, como el método del número de cuadrícula, el método de la sección de cuadrícula, el método de cuatro líneas y el método de ocho líneas, el método de cuatro líneas tiende a tener menos datos de medición debido a la distribución desigual y a la forma de la ferrita δ. en cada campo de visión, lo que lleva a desviaciones mayores.
Aunque el método metalográfico ofrece un campo de visión amplio y aleatorio, la confiabilidad de sus resultados es generalmente alta.
Para reducir los efectos adversos de los métodos de medición y mejorar la confiabilidad de los resultados, se debe seleccionar el método de medición apropiado considerando exhaustivamente factores como el aumento, la posición del campo de visión y las diferencias entre los principios de los diferentes métodos.
Con un aumento de 500x, los valores promedio del contenido de ferrita δ obtenidos del método del número de cuadrícula, el método de la sección de cuadrícula y el método de ocho líneas son los mismos, lo que indica un resultado más confiable de un contenido de ferrita δ del 7,6%.
El método químico utiliza los resultados de la detección del contenido de elementos para calcular y comparar un gráfico experimental para obtener el contenido de ferrita δ. La precisión de la medición del elemento químico afecta directamente la precisión de los resultados.
El método químico se ve directamente afectado por factores como la precisión de los instrumentos de medición de elementos y la selección de gráficos experimentales.
El método magnético tiende a producir resultados de medición relativamente pequeños debido a las diferencias en las cantidades físicas medidas por diferentes instrumentos y a los errores de medición de los propios instrumentos. Además, la morfología y distribución de la ferrita δ pueden ser desiguales en materiales con bajo contenido de ferrita δ.
Las ubicaciones de muestreo inadecuadas pueden provocar una reproducibilidad y precisión deficientes de los resultados de la determinación.
Durante las pruebas y la producción, se recomienda evitar depender de un solo método para medir el contenido de ferrita δ de las soldaduras y utilizar múltiples métodos para la verificación mutua.
4. Conclusión
(1) Cada uno de los tres métodos tiene ventajas y desventajas y debe seleccionarse según la situación específica.
El método metalográfico es un método de prueba destructivo, pero proporciona resultados de medición muy fiables. Durante las pruebas, es necesario considerar el aumento, la posición del campo de visión y las diferencias entre varios métodos y principios para seleccionar el método de medición apropiado.
El método químico puede obtener fácil y rápidamente valores de detección basados en la composición química conocida del material. Sin embargo, es importante seleccionar un gráfico de experiencia y una fórmula de cálculo adecuados.
El método magnético es un método de inspección no destructivo adecuado para la inspección rápida de componentes de materiales grandes en el sitio, pero su valor medido es bajo.
(2) Los resultados de medición obtenidos utilizando el método de comparación del atlas metalográfico y el método químico del diagrama de Schaeffler son similares. De manera similar, los resultados de medición obtenidos utilizando el método del número de cuadrícula, el método de sección de cuadrícula y el método de ocho líneas en el método de medición metalográfica también son los mismos. Por lo tanto, estos métodos se pueden utilizar como métodos alternativos en la detección real.