1 . Prefacio
La tecnología láser es uno de los cuatro mayores avances tecnológicos del siglo XX, junto con las computadoras, los semiconductores y las tecnologías de energía atómica. A lo largo de los años, ha sido ampliamente adoptado en las áreas de comunicaciones ópticas, tratamientos médicos, pruebas y procesamiento de materiales.
En los últimos años, el desarrollo de la tecnología láser en el ámbito del procesamiento de materiales ha sido particularmente impresionante, con aplicaciones como el marcado láser, el corte, la perforación y la soldadura. Entre estos, la soldadura láser se ha vuelto especialmente popular ya que tiene varias ventajas únicas sobre los métodos de soldadura tradicionales, como la soldadura por arco de argón y la soldadura por resistencia.
Los beneficios de la soldadura láser incluyen un pequeño rango de influencia térmica, la capacidad de producir soldaduras con grandes relaciones de aspecto, alta resistencia de la soldadura y resistencia de la unión que puede igualar o superar la resistencia del material base. Además, los rayos láser se pueden transmitir fácilmente a través de fibras ópticas de alta energía, lo que permite automatizar el proceso de soldadura.
La soldadura láser normalmente emplea láseres de CO2, láseres de disco, láseres Nd:YAG, láseres de fibra y láseres semiconductores. Entre ellos, los láseres de fibra son un desarrollo relativamente nuevo en la tecnología láser, con una alta eficiencia de conversión fotoeléctrica del 30% y un tamaño compacto. Tienen bajos requisitos de mantenimiento, una larga vida útil y se utilizan comúnmente para soldar acero inoxidable y aleaciones de aluminio.
Los láseres de fibra de pulso casi continuo son un nuevo tipo de fuente láser desarrollada por la empresa estadounidense IPG en los últimos años. Ofrecen una potencia máxima alta y anchos de pulso de hasta milisegundos, lo que los hace adecuados para la soldadura de metales y el procesamiento de otros materiales. Aunque se utilizan ampliamente para soldadura electrónica de precisión, existe una investigación limitada sobre el proceso de soldadura detallado.
En este estudio, el enfoque, que es un factor crítico en el proceso de soldadura, se utiliza como punto de partida para investigar la diferencia en la calidad del rayo láser bajo diferentes condiciones de enfoque y su impacto en el efecto de la soldadura.
2. Equipos de soldadura y preparación de pruebas.
(1) Equipo de soldadura
Este artículo utiliza un láser de fibra de pulso casi continuo de 150 W como fuente de luz de soldadura. Las especificaciones técnicas del láser se pueden encontrar en la Tabla 1.
Tabla 1 Parámetros técnicos del láser
Potencia media /W | 150 |
---|---|
Potencia máxima /W | 500 |
Ancho de pulso/ms | 0,2-20 |
Frecuencia/Hz | 0-2500 |
método de enfriamiento | Aire acondicionado |
Calidad del haz BPP/mm*mrad | 1-2 |
El cabezal de procesamiento láser se mueve con respecto a la pieza de trabajo mediante la operación de la plataforma móvil X/Y/Z para realizar la soldadura de pistas. El cabezal de procesamiento láser y la señal de salida del láser están conectados a través de un tablero de control de movimiento, lo que significa que después de colocarse en una ubicación específica, el láser emite luz para soldar.
(2) Materiales de soldadura
En este artículo, se utiliza acero inoxidable 304 como material de prueba, aplicándose un método de soldadura por superposición. El grosor del material superior es de 0,2 mm, el grosor del material inferior es de 0,5 mm y las dimensiones del material son 100 mm x 50 mm.
Antes de soldar, se limpia la superficie del material con acetona y alcohol para eliminar impurezas como manchas de aceite. Se utiliza un dispositivo de fabricación propia para comprimir las capas superior e inferior de material, reduciendo los espacios entre las dos capas y garantizando la precisión y confiabilidad de los resultados de las pruebas de soldadura.
(3) Confirme la posición del enfoque del láser
Los principales factores que influyen en el resultado de la soldadura láser son la potencia máxima del láser, el ancho del pulso y el desenfoque (la distancia entre el foco del láser y la superficie de la pieza), siendo el desenfoque un factor especialmente crucial.
El desenfoque se define como positivo cuando el enfoque está por encima de la superficie de la pieza de trabajo y negativo cuando está por debajo de la superficie.
El método más fiable para determinar la posición del foco láser es el método de calibración del láser triangular de acero inoxidable. Este método implica el uso de un láser de baja energía (50 W) para marcar un punto en el acero inoxidable, y la chispa más fuerte indica la ubicación del foco del láser. Luego se coloca un bloque triangular de acero inoxidable cerca del foco láser y se utiliza un rayo láser para dibujar una línea en el bloque, con una separación de aproximadamente 0,5 mm. El ancho de línea más estrecho se mide usando un microscopio y esta medida representa el foco del láser.
3. El efecto del desenfoque en la calidad del haz
La calidad del rayo láser se prueba mediante un analizador de rayo, una sonda láser y un atenuador láser. Primero se coloca la sonda láser en el foco del láser para realizar la prueba y luego se levanta el cabezal de procesamiento láser 1 mm a la vez, con el desenfoque establecido en 0 mm, 1 mm, 2 mm, 3 mm y 4 mm.
Los resultados de la prueba, que muestran la distribución del haz, se presentan en la Figura 1.

Figura 1 Cambios en la calidad del haz con desenfoque
Cuando el desenfoque se establece en 0 mm, la energía del láser se concentra principalmente en el centro del punto. A medida que aumenta el desenfoque, la distribución de la energía láser a través del punto se vuelve cada vez más uniforme. Con un desenfoque de 3 mm, la distribución de la energía láser en el punto es más equilibrada. Sin embargo, cuando el desenfoque aumenta a 4 mm, la distribución de la energía láser se vuelve desigual.
4.T El efecto del desenfoque sobre el efecto de soldadura.
(1) La cantidad de desenfoque afecta las uniones soldadas
La pieza de trabajo se posiciona en el foco del láser y se definen la potencia máxima del láser y el ancho del pulso. Luego se hace una mancha en la muestra de acero inoxidable aumentando gradualmente la potencia y el ancho del pulso hasta que se vean rastros claros en la parte posterior del material subyacente. En este caso, la potencia máxima del láser fue de 500 W y el ancho del pulso fue de 3 ms.
Sin cambiar la potencia máxima, el ancho del pulso y otros parámetros, la cantidad de desenfoque se ajustó 1 mm a la vez y se registró la apariencia de la unión de soldadura. Estos resultados se pueden ver en la Figura 2.

Figura 2 La apariencia de las uniones soldadas cambia con la cantidad de desenfoque
Los resultados mostraron que cuando el desenfoque se ajustó entre 0 mm y 1 mm, la junta soldada era más pequeña y mostraba salpicaduras de soldadura. Probablemente esto se debe a que, en este rango de desenfoque, la energía del láser se concentraba principalmente en el centro del punto, lo que daba como resultado una alta densidad de potencia del láser en el centro de la junta soldada, provocando salpicaduras.
A medida que el desenfoque siguió aumentando, las uniones de soldadura se volvieron más uniformes y libres de salpicaduras, probablemente debido a la distribución más uniforme del rayo láser. Sin embargo, cuando el desenfoque era superior a 4 mm, la circularidad de la junta de soldadura se volvió inconsistente y el tamaño de la junta de soldadura se redujo hasta cierto punto, posiblemente debido a la distribución desigual de la energía láser en el sitio.
Los resultados también mostraron que a medida que el desenfoque aumentaba de 0 mm a 3 mm, el tamaño de la junta de soldadura aumentaba gradualmente, y el diámetro de la junta de soldadura aumentaba de 0,4 mm a 0,5 mm. Esto se debe a que a medida que aumentaba el desenfoque, aumentaba el punto del láser en la superficie del material, lo que provocaba uniones de soldadura más grandes.
Sin embargo, cuando el desenfoque se aumentó a 4 mm, el tamaño de las uniones de soldadura disminuyó. Esto puede deberse a una distribución alterada del rayo láser, con baja energía en el borde del punto donde el láser estuvo en contacto con el material, lo que da como resultado un punto más grande en la superficie pero una junta de soldadura más pequeña.
La relación entre el diámetro de la junta de soldadura y la cantidad de desenfoque se muestra en la Figura 3.
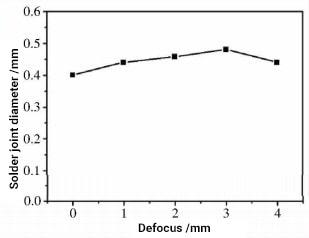
Figura 3 Relación entre el diámetro de la junta de soldadura y el desenfoque
(2) El efecto de la cantidad de desenfoque en la penetración de la junta soldada
Se utilizó un cortador para cortar a lo largo del borde de la junta soldada por láser. Después de someterse a esmerilado, esmerilado fino y pulido, se observó el centro de la junta soldada durante el pulido. Finalmente, después de someterse a un tratamiento anticorrosión con ácido nítrico y una solución de alcohol, se probó el cambio en la penetración de la junta soldada en diferentes condiciones de difuminado.
Los resultados mostraron que cuando el desenfoque se estableció entre 0 mm y 1 mm, la junta soldada tuvo la penetración más profunda y alcanzó el material subyacente. Cuando el desenfoque se estableció entre 2 mm y 3 mm, la penetración de la soldadura se volvió más superficial y solo penetró la mitad del espesor del material subyacente. Sin embargo, cuando el desenfoque se estableció en 4 mm, la profundidad de penetración de la soldadura se redujo significativamente y solo penetró 1/3 del espesor del material subyacente, como se muestra en la Figura 4.

Figura 4 Cambio en la penetración de la unión soldada con desenfoque
(3) El efecto de la cantidad de desenfoque sobre la resistencia de la soldadura
Se utilizó una máquina de tracción para probar la resistencia de una sola unión soldada sujetando el material inferior y tirando del material superior hacia arriba. Para garantizar datos precisos de las pruebas de tracción, se probaron 3 muestras para cada conjunto de parámetros y se obtuvo el valor promedio.
La cantidad de desenfoque se estableció en 0 mm, 1 mm, 2 mm, 3 mm y 4 mm, correspondientes a uniones de soldadura con resistencias de 7 N, 8 N, 11 N, 15 N y 6 N, respectivamente.
Como tendencia general, la resistencia a la tracción de las uniones soldadas aumentó a medida que aumentó el desenfoque. Esto se debió a que a medida que aumentaba el desenfoque, también aumentaba el tamaño de las uniones de soldadura, particularmente el ancho del contacto entre el material superior e inferior, lo que llevaba a un aumento en la resistencia a la tracción. Sin embargo, cuando el desenfoque se aumentó a 4 mm, la resistencia a la tracción disminuyó, probablemente debido al empeoramiento de la calidad del haz y al mayor tamaño del punto, lo que condujo a una disminución en la densidad de potencia del láser y, por lo tanto, en la profundidad de penetración del láser y en la resistencia de la soldadura. articulación.
Según los datos experimentales, la resistencia a la tracción de una sola junta de soldadura alcanzó su valor máximo de 15 N cuando el desenfoque se estableció en 3 mm.
5 . Conclusión
Este artículo investigó la distribución del rayo láser bajo diferentes condiciones de desenfoque y encontró que a medida que aumentaba el desenfoque, la distribución de la energía del láser en el sitio se volvía más uniforme, pero cuando el desenfoque excedía los 4 mm, la distribución de energía se volvía irregular.
Al probar el proceso de soldadura por solape de acero inoxidable, el estudio concluyó que bajo otros factores constantes, ajustar la cantidad de desenfoque afectaba la apariencia, el tamaño, la penetración y la resistencia a la tracción de la junta soldada, así como la apariencia general y los requisitos de resistencia.
Las conclusiones fueron:
- A medida que aumentó el desenfoque, la calidad de las uniones de soldadura mejoró y la resistencia a la tracción de las uniones de soldadura aumentó gradualmente.
- Cuando el desenfoque se estableció en 3 mm, las uniones de soldadura eran consistentes y tenían la mayor resistencia a la tracción.
- Sin embargo, cuando el desenfoque aumentó aún más, la resistencia y la calidad de las uniones de soldadura disminuyeron nuevamente.