316L pertenece al acero inoxidable austenítico, correspondiente a la marca nacional 022Cr17Ni12Mo2, que tiene buena plasticidad y resistencia a la corrosión.
La adición de elemento Mo a este acero inoxidable mejora enormemente su resistencia a la corrosión.
Por lo tanto, el acero inoxidable 316L se usa ampliamente en las industrias petroquímica, farmacéutica y otras.
Se encontró que un serpentín de acero inoxidable 316L utilizado en una empresa presentó fuga y perforación en la pared del tubo durante su uso.
El medio de trabajo dentro del tubo es vapor de agua, con una presión de trabajo de 0,9 MPa.
El medio fuera del tubo es un álcali fuerte y polvo de cobre, con una presión de trabajo de 1,0 MPa.
Hay una diferencia de presión entre las paredes interior y exterior.
El motivo del fallo se analiza y estudia experimentalmente.
1. Macroanálisis
1.1 Inspección visual
A partir de una inspección visual macroscópica externa, se encuentra que el orificio de fuga es un pequeño orificio con un diámetro de aproximadamente 2 mm en la pared exterior, como se muestra en la Fig.
En la pared interior, hay cuatro pequeños agujeros dispuestos longitudinalmente con un diámetro de aproximadamente 1 mm, y se puede ver una gran cantidad de grietas de "piel deformada", como se muestra en la Fig.
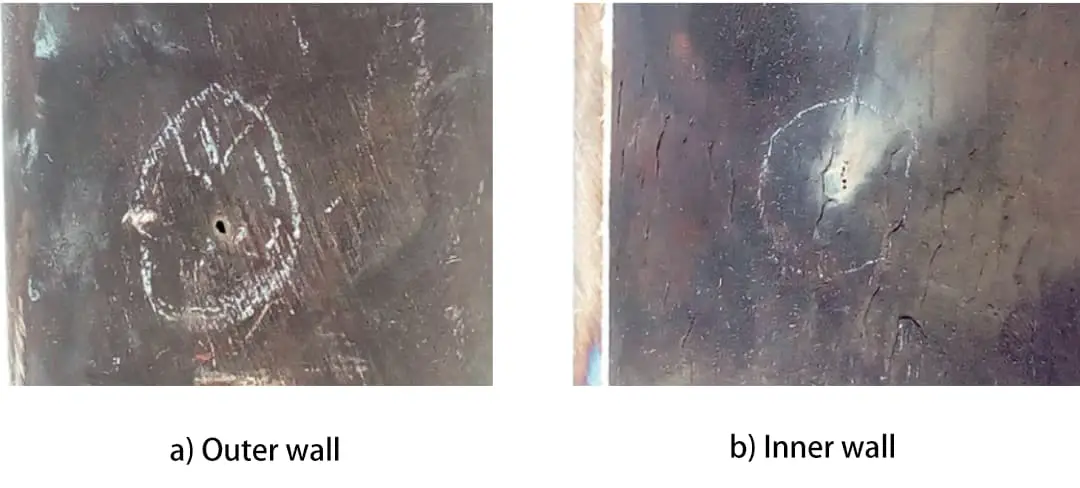
Fig. 1 Macromorfología del orificio de fuga
1.2 Macroinspección extendida
Cuando se observa con un microscopio estereoscópico de aumento variable, la Fig. 2a es una fotografía macro del orificio de fuga de la pared interior después de un aumento de 40x;
La figura 2b muestra la forma del orificio de fuga después del corte.
El espacio dentro del agujero es relativamente grande, con un volumen total de aproximadamente 4 mm 3 .
La pared del agujero es ondulada e irregular.
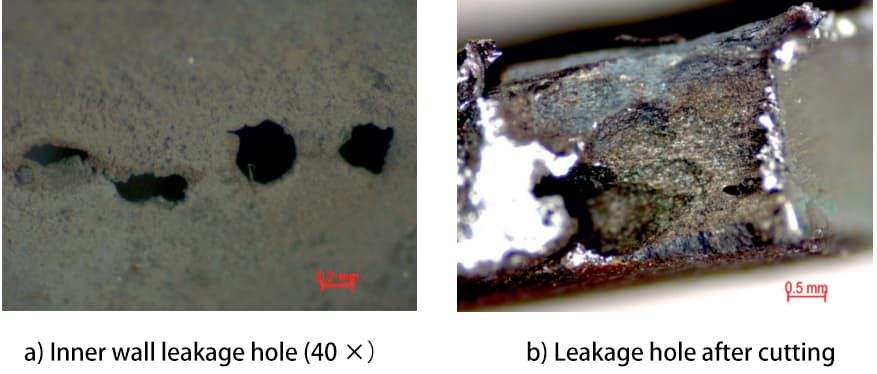
Fig. 2 Morfología del orificio de fuga
2. Detección y análisis
2.1 Análisis espectral de composición química.
El espectrómetro de lectura directa de espectro completo se utiliza para analizar la composición química de las muestras alrededor del orificio de vertido.
Los resultados (valor promedio) se presentan en la Tabla 1.
En comparación con la composición del material TP316L en ASME SA213, cumple con los requisitos de la norma.
Tabla 1 Resultados del análisis de composición química (fracción de masa) (%)
Tipo | W. | Sí | Minnesota | PAG | s | cr | No | Mes |
Valor estandar | ≤0,035 | ≤1,00 | ≤2,00 | ≤0,045 | ≤0,030 | 16,0~18,0 | 10,0~14,0 | 2:00 ~ 3:00 |
Valor medido | 0,02 | 0,28 | 0,86 | 0.041 | 0.003 | 16.21 | 10.17 | 2.18 |
2.2 Prueba de tracción
La máquina de prueba universal electrónica se utiliza para recolectar muestras de la bobina para pruebas de tracción.
Los resultados se muestran en la Tabla 2.
La morfología de fractura de la muestra es de fractura plástica.
A través de la comparación, se puede ver que la resistencia a la tracción, el límite elástico y el alargamiento después de la fractura del material cumplen con el estándar ASME SA213.
Tabla 2 Resultados de las pruebas de propiedades mecánicas.
Tipo | Resistencia a la tracción R eu / MPa | Límite elástico R po.2 /MPa | Elongación tras fractura A (%) |
Valor estandar | ≥486 | ≥170 | ≥35 |
Valor medido | 693 | 476 | 48,5 |
2.3 Prueba de rendimiento del proceso
La máquina de prueba universal electrónica se utiliza para realizar la prueba de abocardado y aplanamiento.
Los resultados se muestran en la Tabla 3.
El aspecto de la muestra quemada después de la prueba se muestra en la Fig.
No hay grietas en la pared interior del tubo.
La morfología del espécimen aplanado se muestra en la Fig.
Se generan grietas en la superficie de tracción de la pared exterior de la muestra aplanada.
La pared exterior del extremo de la abertura de la grieta es una fractura antigua y la punta de la grieta es una fractura nueva.
Se puede ver que hay viejas grietas en la pared exterior de la tubería.
Tabla 3 Resultados de las pruebas de rendimiento del proceso
prueba de quemado | Prueba de aplanamiento | |||
Β(°) | D(%) | Resultados | Distancia entre placas de prensado / mm | Resultados |
60 | 15 | Sin grietas en la pared interior. | 29,5 | Grietas en la deformación por tracción de la pared exterior. |
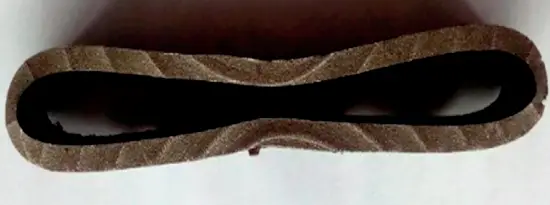
Fig.3 muestra quemada
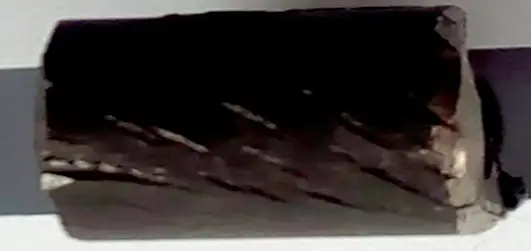
Fig. 4 Grieta en la superficie de tracción de la muestra aplanada.
2.4 Análisis metalográfico
Se procesarán muestras micrometalográficas en las paredes internas y externas y en el interior de la bobina.
La sección transversal de las muestras debe lijarse y pulirse y luego observarse bajo un microscopio metalográfico.
Se puede ver en la Figura 5a que hay grietas de “piel deformada” en la pared interna de la bobina y microfisuras en la parte inferior de la “piel deformada”;
Se puede observar en la Figura 5b que existe una gran cantidad de microfisuras en la pared externa, las cuales se originan por defectos o picaduras de corrosión y se expanden a lo largo de las inclusiones;
Se puede ver en la Figura 5c que hay una gran cantidad de inclusiones granulares, masivas y en forma de banda en el interior, con un tamaño de 5 ~ 25 μm.
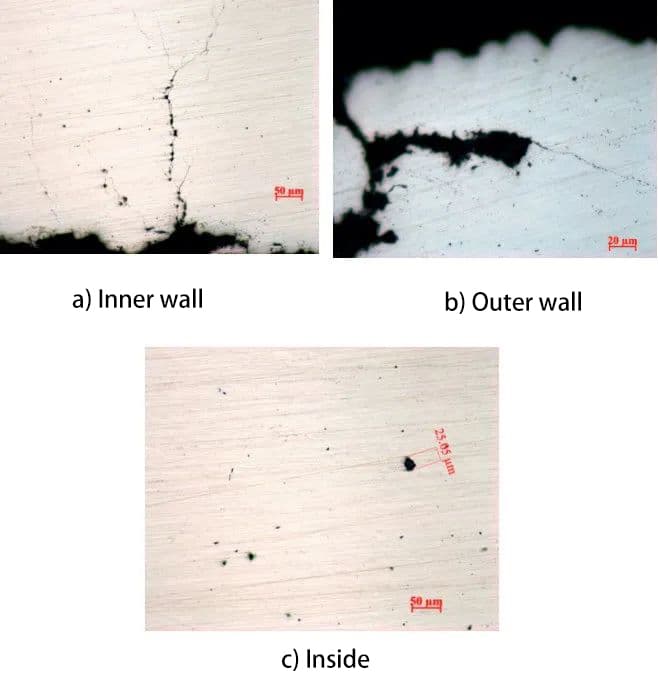
Fig. 5 áreas diferentes de materiales de bobina
La microestructura de la muestra corroída es austenita con un tamaño de grano promedio de 6,5 y se encuentran precipitados en el límite de grano.
Se puede observar en la Figura 6b que hay una gran cantidad de líneas de deslizamiento de deformación en la pared interior, lo que indica la existencia de tensión residual;
Se puede ver en la Fig. 6c que hay grietas transgranulares e intergranulares en la pared exterior.
Figura 6 diagrama metalográfico
2.5 Análisis SEM
El microscopio electrónico de barrido se utiliza para observar la fractura de la grieta. La figura 7a es una fractura antigua.
Se puede ver en la morfología de la pared interior del orificio de fuga en la Fig. 7b que hay productos de corrosión de "patrón de lodo" en la superficie.
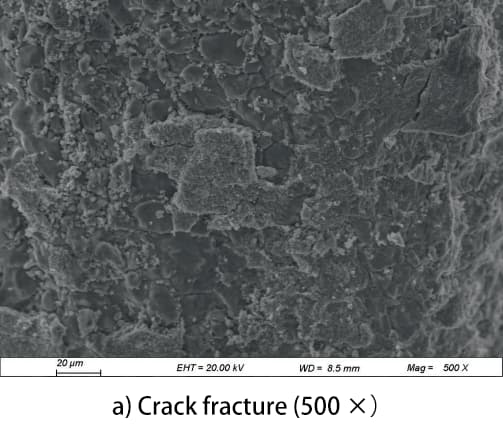
Fig. 7 Aspecto SEM de la pieza fallida
2.6 Y análisis del espectro energético
El análisis del espectro de potencia se realizó en las muestras de fracturas antiguas en la Figura 7a, como se muestra en la Figura 8. Los resultados se muestran en la Tabla 4.
Los productos de corrosión son relativamente complejos, compuestos principalmente de óxidos y mezclados con Cu, Na, etc.
W. | Minnesota | Mes | Fe | cr | No | oh | Culo | N / A |
8.2 | 0,6 | 1.3 | 41,5 | 17.4 | 5.0 | 22.9 | 0,7 | 1.8 |
Tabla 4 Resultados del análisis del espectro energético (fracción de masa) (%)
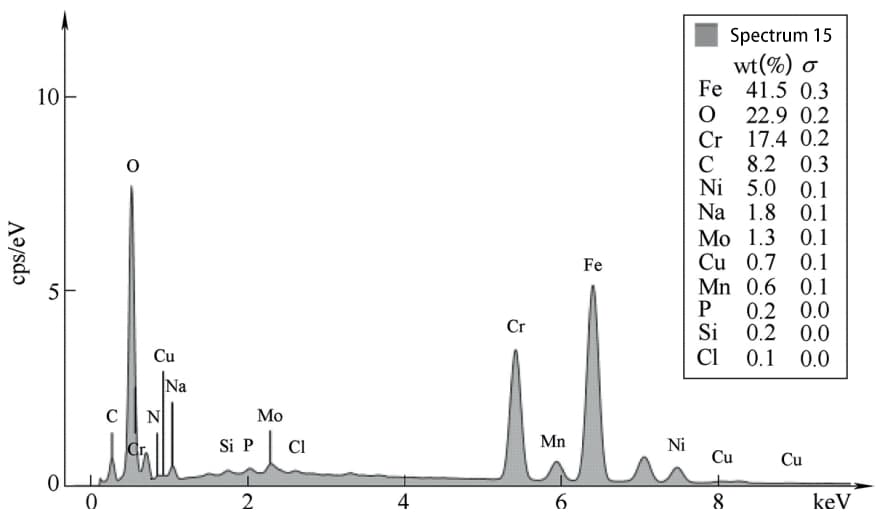
Fig. 8 Espectro de energía del punto de análisis.
3. Análisis integral
Según los datos de prueba anteriores, la composición química, la resistencia a la tracción, el límite elástico y el alargamiento después de la fractura de la bobina de acero inoxidable TP316L cumplen con los requisitos de ASME SA213.
La prueba de ensanchamiento está calificada, aparecen grietas en la superficie de tracción de la pared exterior del tubo de ensayo aplanado y el extremo abierto es una grieta vieja.
Los análisis metalográficos y SEM + EDS muestran que la estructura está hecha de acero inoxidable austenítico, pero hay inclusiones granulares de diferentes tamaños y productos de corrosión de "patrón de lodo" en la superficie, principalmente en el orificio de fundición.
La pared de los poros fluctúa de forma irregular y en la “piel deformada” hay una gran cantidad de microfisuras que se expanden a lo largo de las inclusiones.
4. Conclusiones y sugerencias
Las principales causas de las fugas en la bobina de acero inoxidable 316L son una gran cantidad de inclusiones, productos de corrosión de óxido y microfisuras en el material.
La continuidad de la matriz se destruye por la presencia de inclusiones.
Bajo la acción conjunta de la tensión residual y la diferencia de presión entre las paredes interior y exterior, se generan y expanden fácilmente grietas en la inclusión.
Sin embargo, la inclusión entra en contacto con el medio de vapor a alta temperatura.
Debido a que la resistencia a la corrosión de la inclusión es mucho menor que la del propio material, la inclusión se corroe y eventualmente se forman agujeros en la pared de la tubería, lo que resulta en la perforación de la pared de la tubería y fugas.
Para evitar fallas por fugas similares, se recomienda lo siguiente:
1) Para el entorno de servicio del serpentín, se debe seleccionar material de acero inoxidable 316L de alta calidad con pocas inclusiones.
2) Controlar la pureza del medio de trabajo para evitar en la medida de lo posible la influencia de sustancias corrosivas en la tubería.
3) Los componentes de la bobina deben tratarse térmicamente después de doblarlos y soldarlos para liberar eficazmente la tensión residual.