Introducción
La soldadura es un proceso primario en la fabricación de chapa metálica, caracterizado por una alta intensidad de mano de obra y condiciones laborales adversas. Como tal, un alto nivel de competencia es esencial.
La automatización en la soldadura y el desarrollo de métodos de unión innovadores han sido puntos focales constantes para los profesionales de la tecnología de soldadura.
Un aspecto fundamental de la automatización de la soldadura es controlar la calidad y eficiencia de la soldadura. Durante el proceso, se deben abordar desafíos como la alineación del arco y la costura de soldadura, la uniformidad de los espacios de los componentes, la penetración de la soldadura y el control de la distorsión de la soldadura.
Con los rápidos avances en la tecnología de soldadura láser, ha dado un salto significativo y ha madurado en su aplicación en diversas industrias, incluidos electrodomésticos, electrónica de alta tecnología, fabricación de automóviles, producción de trenes de alta velocidad y mecanizado de precisión.
Los beneficios de la soldadura láser se pueden entender comparándola con la soldadura por arco tradicional. Esta publicación profundizará en el proceso de soldadura láser y explorará cómo lograr mejores resultados.
Para evaluar la calidad de una soldadura láser se tienen en cuenta la relación profundidad/ancho y la morfología de la superficie. Esta publicación analizará los parámetros del proceso que afectan estos índices.
Se llevaron a cabo experimentos de soldadura láser en placas de acero inoxidable, aluminio y acero al carbono. Los resultados proporcionan información práctica que se puede utilizar en la producción de soldadura.
La soldadura láser es una técnica de producción de última generación que utiliza un láser de alta densidad energética como fuente de calor para la soldadura. Se utiliza ampliamente en la industria de fabricación de chapa debido a sus ventajas que incluyen alta densidad de energía, rápida velocidad de soldadura, respeto al medio ambiente, mínima deformación de la placa y más.
La soldadura láser, según las características de la formación del cordón de soldadura, se puede dividir en soldadura por conducción y soldadura de penetración profunda. La soldadura por conducción utiliza una potencia láser baja, lo que da como resultado tiempos de formación del baño de soldadura más prolongados y profundidades de fusión reducidas.
Se utiliza principalmente para soldar componentes pequeños.
Por el contrario, la soldadura de penetración profunda tiene una alta densidad de potencia, donde el metal en el área de irradiación láser se funde rápidamente.
Esta fusión va acompañada de una intensa vaporización, consiguiendo cordones de soldadura de importante profundidad y una relación ancho-profundidad de hasta 10:1.
Los componentes de chapa delgada se pueden unir mediante varios métodos de soldadura, incluida la soldadura láser, la soldadura fuerte, la soldadura con hidrógeno atómico, la soldadura por resistencia, la soldadura por arco de plasma y la soldadura por haz de electrones.
Al comparar la soldadura láser con otras técnicas de soldadura comunes, ofrece ventajas significativas en términos de zona afectada por el calor, deformación térmica, calidad de la costura de soldadura, requisitos de material de relleno y entorno de soldadura.
La comparación entre la soldadura láser y otros métodos de soldadura se puede encontrar en la Tabla 1.
Tabla 1 Comparación entre soldadura láser y otros métodos de soldadura
soldadura por láser | menos | menos | preferiblemente | No | ningún requerimiento especial |
Soldadura | comúnmente | comúnmente | comúnmente | Sí | Calefacción general |
Soldadura por arco de argón | más | más | comúnmente | Sí | Electrodo requerido |
Soldadura por resistencia | más | más | comúnmente | No | Electrodo requerido |
Soldadura por arco de plasma | comúnmente | comúnmente | comúnmente | Sí | Electrodo requerido |
Soldadura por haz de electrones | menos | menos | preferiblemente | No | vacío |
Características de la soldadura láser.
La soldadura láser utiliza un láser que canaliza un rayo láser de alta energía hacia una fibra óptica. Después de la transmisión, se colima en luz paralela mediante una lente colimadora y luego se enfoca en la pieza de trabajo.
Esto da como resultado una fuente de calor de energía extremadamente alta que funde el material en la junta. El metal fundido se enfría rápidamente para formar una soldadura de alta calidad. La apariencia de una pieza de chapa soldada con láser se muestra en la siguiente figura.
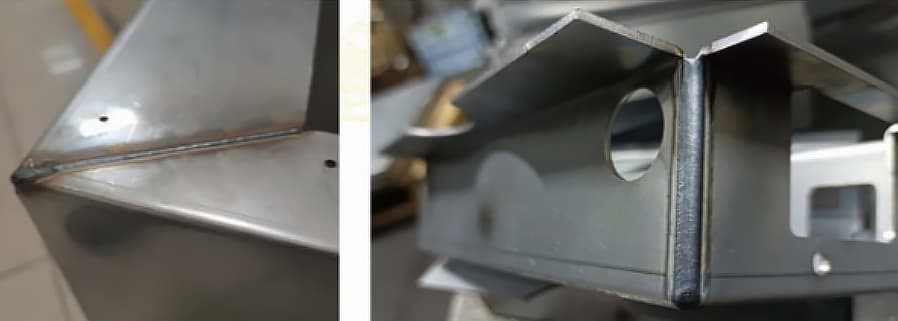
Operación fácil:
Las máquinas de soldadura láser son fáciles de usar. El funcionamiento es sencillo, fácil de aprender y fácil de usar. El nivel de especialización requerido de los operadores es relativamente bajo, lo que se traduce en ahorros en costes laborales.
Alta flexibilidad:
Los soldadores láser pueden soldar desde cualquier ángulo y son expertos en acceder a áreas de difícil acceso. Pueden manejar componentes de soldadura complejos y piezas grandes con formas irregulares, ofreciendo una flexibilidad incomparable en la soldadura en cualquier orientación.
Seguridad mejorada:
La boquilla de soldadura de alta seguridad se activa únicamente en contacto con el metal y cuenta con un interruptor táctil con sensor de temperatura corporal. Se deben cumplir normas de seguridad específicas al operar el generador láser especializado, incluido el uso de gafas protectoras para minimizar posibles daños oculares.
Calidad superior del rayo láser:
Una vez enfocado, el láser alcanza una alta densidad de potencia. Con enfoque láser de alta potencia y modo bajo, el diámetro del punto resultante es pequeño, lo que promueve significativamente la automatización en la soldadura de placas delgadas.
Velocidad de soldadura rápida con penetración profunda y distorsión mínima:
Debido a la alta densidad de potencia de la soldadura láser, durante el proceso se forman pequeños poros en el metal. La energía láser penetra profundamente en el material a través de estos poros con una mínima propagación lateral. La profundidad de fusión del material es considerable y la velocidad de soldadura es rápida, cubriendo un área grande en poco tiempo.
Costos laborales reducidos:
Debido al mínimo aporte de calor durante la soldadura láser, la distorsión posterior a la soldadura es menor. Esto da como resultado un acabado de soldadura visualmente atractivo, lo que lleva a un procesamiento posterior a la soldadura reducido, lo que a su vez reduce significativamente o incluso elimina los costos de mano de obra asociados con el alisado y la nivelación.
Capacidad para soldar materiales difíciles:
La soldadura láser no sólo es adecuada para unir una variedad de metales diferentes, sino también para soldar metales y aleaciones como titanio, níquel, zinc, cobre, aluminio, cromo, oro, plata, acero y aleaciones de corte. Satisface bien las necesidades de desarrollo de nuevos materiales en electrodomésticos.
Especialmente indicado para soldar chapas finas y componentes estéticos no revestidos:
Dada su alta relación de aspecto de soldadura, su bajo aporte de calor, su mínima zona afectada por el calor y su reducida distorsión, la soldadura láser es especialmente adecuada para soldar láminas delgadas, componentes estéticos sin recubrimiento, piezas de precisión y componentes térmicamente sensibles. Esto puede minimizar aún más las correcciones posteriores a la soldadura y el procesamiento secundario.
Comparación entre soldadura láser y soldadura por arco tradicional
Introducción a la soldadura por arco
La soldadura por arco tradicional se puede clasificar en términos generales en varios tipos, incluida la soldadura por arco revestido, la soldadura con gas inerte de tungsteno (TIG), la soldadura con gas inerte de metal (MIG) y la soldadura por arco sumergido.
La soldadura por arco revestido implica formar un arco entre el electrodo y la pieza de trabajo, generando calor que funde el metal en el punto de contacto entre el electrodo y la pieza de trabajo. Esto crea un charco de metal fundido. Luego, el electrodo se mueve en una dirección específica, creando nuevos charcos de metal fundido y solidificando los charcos anteriores, lo que da como resultado la formación de una soldadura.
En la Figura 1 se muestra un diagrama del proceso de soldadura.
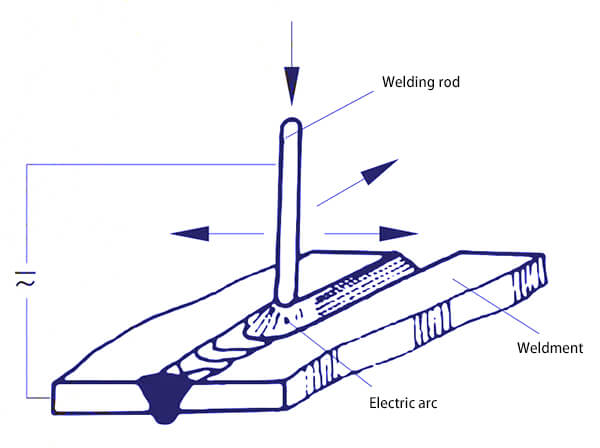
Fig. 1 Diagrama esquemático de la soldadura por arco con electrodo.
La soldadura con gas inerte de tungsteno (TIG) utiliza un electrodo de tungsteno como electrodo de descarga, que no se consume durante el proceso. El área de soldadura está protegida por un gas inerte, típicamente argón, y el calor generado por el arco se utiliza para fundir tanto el metal base como el material de soldadura. El resultado es una superficie de soldadura lisa con poca o ninguna salpicadura.
La soldadura por arco metálico con gas (GMAW) es un proceso en el que se genera un arco entre el alambre de soldadura y el metal base, lo que hace que el alambre y el metal base se fundan. El material fundido se solidifica formando una soldadura.
Aunque la soldadura por arco todavía mantiene una posición dominante en la industria de la soldadura, las crecientes demandas de soldadura eficiente y de alta calidad han llevado a limitaciones en su aplicación en algunos campos de fabricación de chapa metálica de alta calidad. Algunas de las desventajas de la soldadura por arco tradicional incluyen:
- La necesidad de utilizar argón de alta pureza como gas protector, que puede resultar caro.
- Se requiere un alto nivel de habilidad y certificación para su correcto funcionamiento, lo que lo hace inaccesible para muchos.
- La corriente de alta densidad y el calor generado durante el proceso de soldadura pueden afectar negativamente la soldadura de placas metálicas con puntos de fusión bajos.
- Baja eficiencia de soldadura y baja velocidad.
- La superficie de soldadura es rugosa y requiere un pulido adicional para obtener una superficie lisa.
- Fuerza de soldadura limitada.
Ventajas de la soldadura láser
Las principales técnicas de soldadura por láser incluyen la soldadura por autofusión, la soldadura por oscilación, la soldadura por relleno de alambre, la soldadura por galvanómetro y la soldadura compuesta que combina varios métodos de soldadura.
La Tabla 1 destaca las ventajas de la tecnología de soldadura láser en comparación con la soldadura por arco tradicional.
Para las industrias de fabricación de chapa de alta calidad que requieren productos de alto valor agregado con calidad constante, espacios de soldadura pequeños y alta eficiencia, la soldadura láser es la mejor opción.
Tabla 1 Comparación de características entre soldadura láser y soldadura por arco
Soldadura por arco | soldadura por láser |
Se requiere corriente de alta densidad y el efecto térmico es grande. | Bajo calor de soldadura, pequeña deformación y efecto térmico. |
Penetración superficial y baja resistencia a la soldadura. | Penetración profunda y alta resistencia a la soldadura. |
Tipo de contacto, limitado por espacio | Tipo sin contacto, menos limitado por el espacio |
Gran corriente de arranque de arco y amplio rango de soldadura | Punto de soldadura pequeño, capaz de soldar piezas de precisión. |
Los operadores tienen altos requisitos y requieren certificados de operación especiales. | Bajos requisitos para los operadores. |
Baja eficiencia de soldadura y velocidad de soldadura lenta. | Alta eficiencia de soldadura y rápida velocidad de soldadura |
Contaminación y pérdida de electrodos. | Sin pérdida de electrodos |
La superficie es rugosa y requiere un mayor pulido. | La morfología de la superficie es estable y básicamente no es necesario realizar más rectificado. |
Parámetros del proceso de soldadura láser.
Índice de costura de soldadura láser
Los requisitos para el efecto de soldadura de piezas de chapa varían según las necesidades del cliente. Estos requisitos se reflejan principalmente en los siguientes indicadores:
- Morfología de la superficie (por ejemplo, cóncava, plana o convexa)
- La relación profundidad-ancho del baño de soldadura.
- Ausencia de defectos como poros, grietas, impurezas y rebajes.
La morfología de la superficie de soldadura se puede cambiar ajustando factores como la potencia de soldadura, el desenfoque y el modo de empalme. La relación profundidad/ancho del baño de soldadura es un factor importante para determinar la resistencia de la soldadura.
Para los clientes que tienen requisitos de resistencia para sus productos de soldadura, se debe realizar una serie de pasos, que incluyen corte de alambre, incrustación, esmerilado y pulido, pruebas de corrosión y análisis metalográfico microscópico. Este proceso refleja la dureza de la soldadura, que está estrechamente relacionada con la relación profundidad/ancho. El índice de resistencia a la tracción de la soldadura también se puede determinar mediante una prueba de resistencia a la tracción. La Figura 2 muestra el análisis metalográfico de la tasa de penetración.
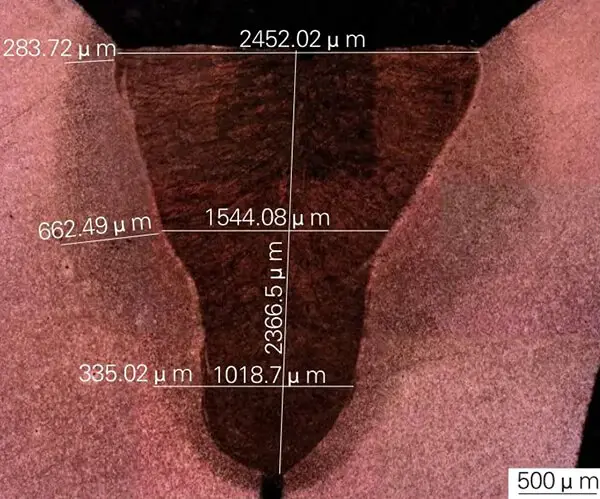
Fig. 2 Análisis metalográfico de la tasa de penetración.
En determinados entornos de trabajo, la soldadura puede presentar defectos como poros, grietas, impurezas y rebajes, que pueden suponer graves riesgos para la seguridad. Por ejemplo, algunos productos requieren normas estrictas de estanqueidad al aire y al agua.
La Figura 3 muestra una comparación entre soldaduras normales y soldaduras con defectos.
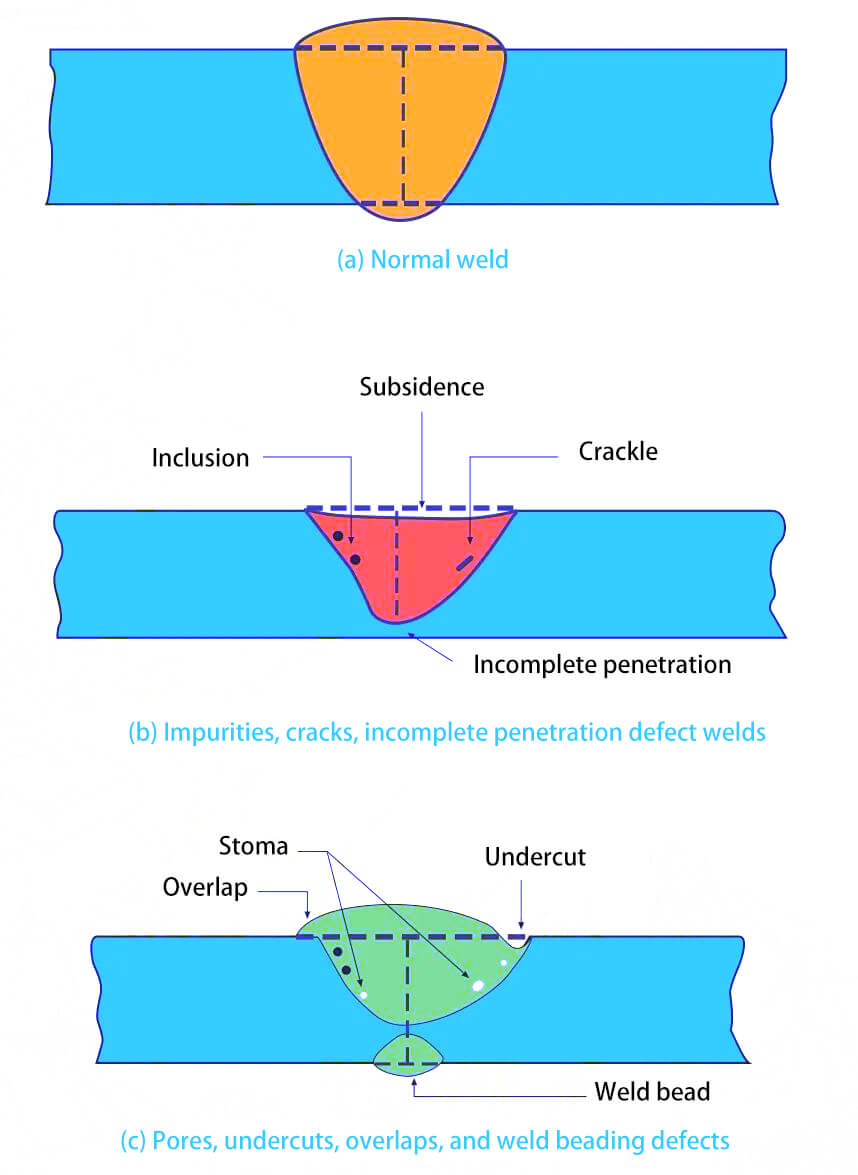
Fig.3 diagrama de costura de soldadura
Factores que influyen en la soldadura láser
Varios factores impactan directamente en la soldadura láser, incluida la temperatura de soldadura, el punto de fusión de los materiales de soldadura, la tasa de absorción del láser de los materiales de soldadura y la influencia térmica.
En el proceso de soldadura se deben tener en cuenta factores como las propiedades del material, la potencia del láser, la velocidad de soldadura, la posición del foco, el gas de protección y la ranura de soldadura.
La absortividad del láser de los materiales de soldadura afecta la calidad de la soldadura. Materiales como el aluminio y el cobre tienen una mayor absortividad del láser, mientras que el acero al carbono y el acero inoxidable tienen una menor absortividad del láser. Los materiales de soldadura con alta absortividad generalmente requieren más energía para fundirse y formar un baño de soldadura estable.
La potencia del láser es la fuente de energía para la soldadura láser y desempeña un papel fundamental en la determinación del efecto de la soldadura. Cuanto mayor sea la potencia del láser, mejor será el efecto de soldadura. Sin embargo, demasiada potencia del láser puede provocar inestabilidad en el baño de soldadura y reducción de la profundidad. Por lo tanto, elegir el valor de potencia del láser adecuado es fundamental.
Existe una relación inversa entre la velocidad de soldadura y la penetración. Las velocidades de soldadura más rápidas dan como resultado un menor consumo de energía, mientras que las velocidades más lentas pueden provocar sobrecalentamiento, especialmente en materiales sensibles al calor como el aluminio.
La posición del foco afecta directamente a la penetración y ancho de la soldadura. Cuando el foco se sitúa en la superficie del material de soldadura, se denomina foco cero. Cuando el foco está por encima o por debajo del material de soldadura, se denomina enfoque excéntrico. El punto de enfoque cero es el más pequeño y tiene la mayor densidad de potencia, mientras que la soldadura desenfocada tiene una densidad de potencia menor pero un punto de luz más grande, lo que la hace adecuada para soldar piezas con un rango más largo.
El tipo y método de protección con gas también afectan el proceso de soldadura. La función del gas protector no es sólo prevenir la oxidación durante la soldadura, sino también suprimir la nube de plasma generada durante la soldadura láser. La elección del gas protector puede afectar la apariencia y el color de la superficie de soldadura.
El espacio de soldadura de la pieza a soldar está relacionado con la penetración, ancho y morfología de la soldadura. Una separación de soldadura demasiado grande puede dificultar la fusión y el emparejamiento, además de exponer el láser y dañar potencialmente la herramienta o la pieza de trabajo. Aumentar el punto de luz o el parpadeo puede mejorar la soldadura, pero la mejora es limitada.
Análisis de pruebas de soldadura
La prueba de soldadura se llevó a cabo utilizando un robot Yaskawa GP25, un láser Prima, una junta de soldadura Ospri (diámetro del núcleo de 100 μm, distancia focal de 300 mm) y un alimentador de alambre WSX. El efecto de soldadura se probó en una placa de acero al carbono Q235 de 1,5 mm, acero inoxidable SS304 y una placa de aleación de aluminio de 3 series.
Según la experiencia, se puede proporcionar la siguiente referencia para el proceso de prueba:
Para la prueba de soldadura de placa delgada de 1 mm, se puede utilizar una potencia inicial de 1 kW y una velocidad de soldadura de 30 mm/s. La potencia de referencia se puede calcular como P=A·X, donde A es un coeficiente constante (A≥0) y X es el espesor de la placa. A medida que aumenta el espesor de la placa, el coeficiente constante A disminuye gradualmente y también está influenciado por el método de soldadura.
Análisis del proceso de soldadura de placas de acero al carbono.
Consulte la Tabla 2 para conocer los parámetros del proceso de soldadura por oscilación de una lámina de acero al carbono Q235 de 1,5 mm de espesor.
Tabla 2 Parámetros del proceso de soldadura oscilante de placa de acero al carbono Q235
NO. |
potencia del láser (kW) |
Velocidad de soldadura (mm/s) |
Rango de giro (mm) |
Velocidad de giro (mm/s) |
Efecto soldadura |
1 | 1.6 | 32 | 1 | 143 | bien |
dos | 1.6 | 31 | 1 | 148 | bien |
3 | 1.6 | 30 | 1 | 148 | bien |
4 | 1.7 | 33 | 1 | 151 | bien |
5 | 1.7 | 32 | 1 | 152 | bien |
6 | 1.7 | 34 | 1 | 150 | bien |
7 | 1.8 | 35 | 1 | 153 | bien |
8 | 1.8 | 35 | 1 | 154 | bien |
9 | 1.8 | 36 | 1 | 154 | bien |
10 | 1.9 | 36 | 1 | 156 | bien |
11 | 1.9 | 37 | 1 | 155 | bien |
12 | 1.9 | 37 | 1 | 160 | bien |
Los datos de las pruebas muestran que durante la soldadura por oscilación de placas de acero al carbono, la potencia del láser debe aumentarse al aumentar la velocidad de soldadura, garantizando al mismo tiempo que el rango de oscilación permanezca sin cambios. Si la velocidad de oscilación es demasiado lenta, la soldadura quedará desigual.
En general, se requiere menos energía para la soldadura oscilante por autofusión de acero al carbono en comparación con la soldadura oscilante por autofusión de acero al carbono, y se requiere menos energía para la soldadura oscilante por autofusión de acero al carbono en comparación con la soldadura con alambre de relleno del oscilador de acero al carbono. La energía requerida está controlada principalmente por la potencia y la velocidad, y una potencia mayor y una velocidad más rápida requieren más energía.
Idealmente, para equilibrar calidad y eficiencia, la velocidad de soldadura debería aumentarse tanto como sea posible. Sin embargo, soldar demasiado rápido puede causar inestabilidad y verse limitado por la potencia del láser y las propiedades del material. Por ello, se suele buscar un equilibrio entre potencia y velocidad.
Análisis del proceso de soldadura de placas de aluminio.
En la prueba, el diámetro del núcleo de la fibra óptica seleccionada fue de 100 μm. Para soldar materiales altamente reflectantes y absorbentes de calor, como el aluminio y el cobre, se requiere una mayor densidad de potencia para la fusión. En este caso, se requiere soldadura de foco cero.
La soldadura de enfoque cero permite una densidad de potencia máxima con una potencia mínima, lo que la hace ideal para soldar piezas pequeñas y fundir metal para formar un baño de soldadura. La Tabla 3 proporciona los parámetros del proceso de soldadura para diferentes materiales.
Tabla 3 Comparación de parámetros del proceso de soldadura para diferentes materiales
NO. |
potencia del láser (kW) |
Velocidad de soldadura (mm/s) |
Espesor del tablero |
Rango de giro (mm) |
Velocidad de giro (mm/s) |
Efecto blanqueador | Material |
1 | 1.5 | 2.1 | 1.5 | 1 | 300 | Bien | Acero al carbono Q235 |
dos | 1.5 | 1.8 | 1.5 | 1 | 300 | Bien | Aleación de aluminio serie 3 |
3 | dos | 2.0 | dos | 1 | 300 | Bien | Acero al carbono Q235 |
4 | dos | 1.7 | dos | 1 | 300 | Bien | Aleación de aluminio serie 3 |
Los datos de las pruebas indican que, si otros parámetros permanecen constantes, el efecto de soldadura ideal para la aleación de aluminio de la serie 3 requiere una velocidad de soldadura más lenta en comparación con el acero al carbono Q235, ya que se requiere más calor.
Análisis del proceso de soplado blanco de acero inoxidable
La Tabla 4 muestra la comparación de los parámetros del proceso de blanqueo para cordones de soldadura de acero inoxidable con un espesor de 1,5 mm. La comparación del efecto de soldadura se puede ver en la Figura 4.
Los parámetros de soldadura de las tres soldaduras en la Figura 4 (de izquierda a derecha) corresponden a los números de serie 1, 2 y 3 en la Tabla 4, respectivamente.
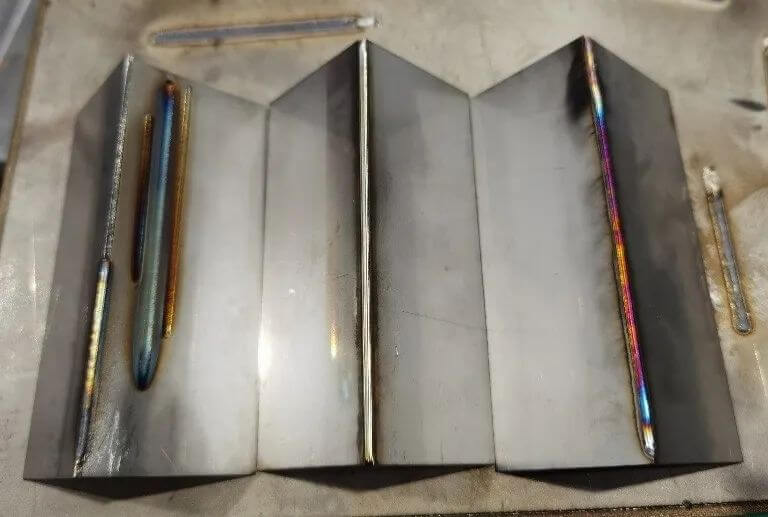
Fig. 4 Comparación del efecto de soldadura
Tabla 4 Comparación de parámetros del proceso de blanqueo de cordones de soldadura de acero inoxidable
NO. | potencia del láser (kW) |
Velocidad de soldadura (mm/s) |
Espesor del tablero | Rango de giro (mm) |
Velocidad de giro (mm/s) |
Efecto blanqueador |
1 | 1.2 | 1.7 | 1.5 | 1 | 300 | pobre |
dos | 1.5 | 1.8 | 1.5 | 1 | 300 | bien |
3 | 1.6 | 1.8 | 1.5 | 1 | 300 | pobre |
Para obtener una superficie blanqueada sobre acero inoxidable, es necesario enfriar y cristalizar rápidamente el metal en una atmósfera de gas protector después de la fusión con láser. Si la potencia es demasiado alta, mucho calor quedará atrapado en la placa de metal, provocando un enfriamiento lento y un mayor riesgo de oxidación y decoloración. Si la potencia es demasiado baja, es posible que el metal no se derrita por completo.
Si la velocidad es demasiado rápida, es posible que las herramientas de soplado no sean suficientes, lo que afectará el efecto de soplado. Si la velocidad es demasiado lenta, se acumulará un calor excesivo. Para conseguir una superficie blanqueada es importante encontrar el equilibrio entre potencia, velocidad y soplado.
Si no es posible lograr una superficie blanqueada en un solo intento, es posible hacerlo soldando una capa a una potencia ligeramente mayor y luego reduciendo la potencia para una segunda capa.
Conclusión
Durante el proceso de soldadura láser, para garantizar resultados de soldadura de alta calidad, es importante considerar una serie de factores, incluidas las propiedades del material, la potencia del láser, la velocidad de soldadura, la posición del enfoque, el gas protector y la separación de soldadura.
Para materiales comúnmente utilizados como acero al carbono, acero inoxidable y placas de aluminio, los parámetros de prueba iniciales mencionados anteriormente se pueden usar como referencia y luego ajustarse de acuerdo con las características específicas del material y los requisitos del cliente para lograr el efecto de velocidad de soldadura deseado.