Laser cutting is a technology widely adopted in several sectors since its inception in the 1960s. The use of lasers in cutting has revolutionized the production process and made it possible to cut materials with great precision and efficiency.
However, with the increasing popularity of laser cutting, price competition between companies has become more intense, leading to a decrease in the profitability of laser cutting equipment.
To reduce the cost of laser cutting equipment, companies need to focus on improving their production processes and increasing efficiency.
An effective way to do this is to use air as an auxiliary gas in the laser cutting process. Using air as an auxiliary gas can reduce the cost of cutting by reducing the consumption of expensive gases such as nitrogen or oxygen.
Additionally, air is readily available and requires no special storage or handling, making it a cost-effective alternative.
In conclusion, using air as an auxiliary gas in laser cutting can help companies reduce their cutting costs, improve efficiency and increase their competitiveness in the market.
This strategy can be implemented as part of a larger effort to transform and update the production process and focus on higher value-added activities, such as process improvement, efficiency improvement and investment in R&D.
The influence of different auxiliary gases on cutting quality
First, let's look at the laser cutting process:
The laser generated by the laser generator is focused through a lens and converges to form a small, intense point of light. The distance between the lens and the plate is carefully controlled to ensure the stability of the laser spot in the direction of the material thickness.
At this point, the lens focuses the light at a point with high power density, typically reaching 106-109W/cm2. The material absorbs the energy from the light spot, causing it to melt instantly, and the molten material is then removed by a stream of auxiliary gas, completing the cutting process.
During the entire cutting process, the auxiliary gas has two main purposes: to provide the force necessary for cutting and to remove the molten material from the part.
In this process, different types of gases have different effects on materials and sections:
(1) Oxygen
When oxygen is used as an auxiliary gas, it not only removes molten metal, but also triggers an oxidation reaction that increases metal melting, allowing thicker materials to be processed. This significantly improves the processing power of the laser.
However, the presence of oxygen also leads to significant oxidation on the cutting surface of the material. Furthermore, oxygen has a quenching effect on the material surrounding the cutting surface, which improves its hardness and has positive impacts on subsequent processing.
(2) Nitrogen
As an auxiliary gas, nitrogen creates a protective atmosphere around the molten metal, preventing oxidation and preserving the quality of the cut surface. However, nitrogen does not have the oxidation capacity to improve heat transfer like oxygen, so it does not improve cutting ability.
Furthermore, the use of nitrogen as an auxiliary gas leads to high consumption, resulting in higher cutting costs compared to other gases.
(3) Air
Air, composed of 78% nitrogen and 21% oxygen, can be used as an auxiliary gas in laser cutting. However, the presence of oxygen in the air will result in oxidation in the cutting section, but the large amount of nitrogen in the air will prevent excessive oxidation and increase heat transfer.
Therefore, the effect of air cutting is intermediate between nitrogen cutting and oxygen cutting. The advantage of air cutting is its low cost, which is mainly due to the energy consumption of the air compressor and the cost of filter elements in the air pipeline.
The effect of different auxiliary gases on cost reduction
FIG. 1 illustrates the effect of cutting section of 1.5mm thick 304 stainless steel using nitrogen and air as auxiliary gas. As can be seen from the figure, when nitrogen is used as an auxiliary gas, the section is bright and shiny, while when air is used, the section is pale yellow.
A comparison of the cutting costs of air and nitrogen as auxiliary gases for 1.5 mm thick 304 stainless steel is presented in Table 1. The comparison uses the latest generation of fiber laser cutting machines equipped with fiber laser generators. self-developed fiber.
Cost analysis reveals that using air as an auxiliary gas results in a 23.7% reduction in cutting costs per hour compared to using nitrogen. This reduction in cost savings can have a significant impact on reducing the plant's overall processing costs.
Furthermore, the energy consumption of the air compressor is analyzed as follows:
Many companies currently use non-variable screw air compressors. If a permanent magnet frequency screw air compressor is used, this can result in savings of up to 50% in electricity for the air compressor alone.
When air is used as an auxiliary gas, the cutting cost is 36.2% lower than when nitrogen is used.
Table 1 Comparison of cutting costs
Item | SUS304-1.5 | SUS304-1.5 |
---|---|---|
Processing speed (mm/min) | 35,000 | 35,000 |
Auxiliary Gas | Air | Nitrogen |
Air Pressure (Mpa) | 0.8 | 0.8 |
Auxiliary gas flow (NL/min) | 296.7 | 296.7 |
Processing time per meter (sec) | 1.7 | 1.7 |
Electricity cost (Yuan/hour) | 14,675 | 14,675 |
Air compressor electricity cost (Yuan/hour) | 12:25 p.m. | 5.25 |
Auxiliary gas cost (Yuan/hour) | 0 | 15,347 |
Subtotal (Yuan/hour) | 26,925 | 35,272 |
Electricity cost (Yuan/m) | 0.012 | 0.012 |
Air compressor electricity cost (Yuan/m) | 0.006 | 0.002 |
Auxiliary gas cost (Yuan/m) | 0 | 0.015 |
Total (Yuan/m) | 0.018 | 0.029 |
Observation:
(1) The aforementioned cost analysis was calculated with the following assumptions:
- The operation rate of the machine tool was assumed to be 70%.
- The electrical load was assumed to be 1 yuan/KW.
- The cost of nitrogen was calculated based on the liquid nitrogen price of 1.5 yuan/kg.
(2) The power consumption of the air compressor when cutting with air was calculated for a non-variable screw air compressor with a capacity of 17.5kW, a pressure of 1.26MPa and a flow rate of 2.3m 3 /min.
(3) When nitrogen is used as an auxiliary gas for cutting, the air compressor still needs to supply gas to the machine, which results in electricity costs.
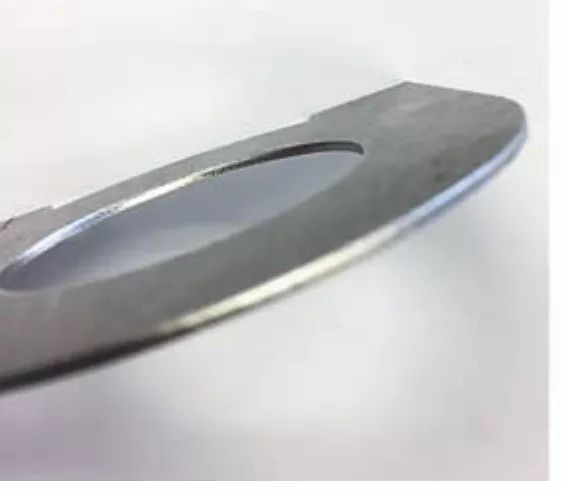
(a) The cutting section when nitrogen as auxiliary gas
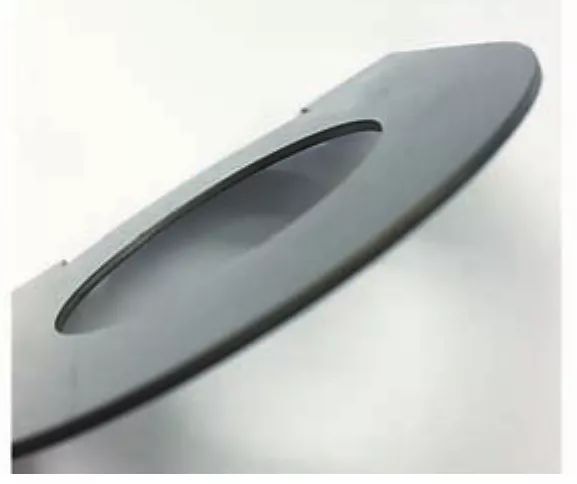
(b) The cutting section when air as auxiliary gas
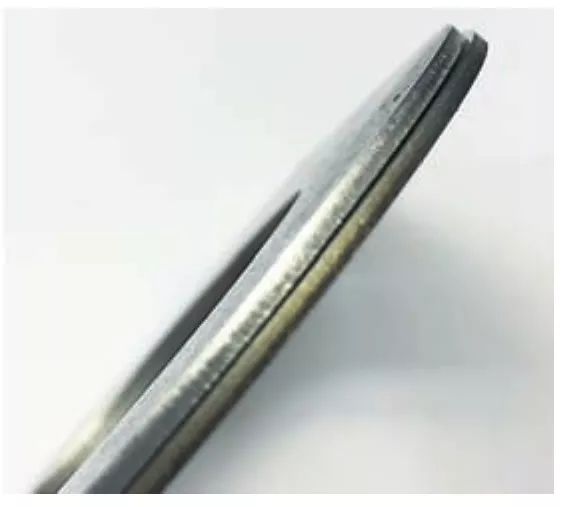
(c) Comparison of two-part section (nitrogen on the left and air on the right)
Fig.1 Effect of cutting section when using nitrogen and air as auxiliary gas
The application range when using air as auxiliary gas
(1) Carbon steel plate /Q235 steel plate
When the plate thickness exceeds 1.5mm, a certain amount of burr will be generated in the cutting section. However, the burrs are not sharp enough to scratch the paper.
The maximum thickness that can be cut with air as an auxiliary gas varies depending on the power and type of laser generator.
(2) Stainless steel plate/SUS304 steel plate
The cutting section produces a layer of yellow oxide.
(3) Aluminum plate/A1050 plate and aluminum alloy plate/A5052 plate
The cutting burr will be reduced compared to using nitrogen as an auxiliary gas.
Table 2 shows the cutting range when air is used as an auxiliary gas for both carbon dioxide laser cutting machines and fiber laser cutting machines.
Table 2 Maximum sheet thickness is cut when air is used as auxiliary gas
Materials | Gas | 4KWCO 2 Laser Cutter | 4KW Fiber Laser Cutter |
---|---|---|---|
Q235 Steel Plate | Air | 3mm | 3mm |
Oxygen | 20mm | 22mm | |
SUS304 Steel Plate | Air | 3mm | 3mm |
Nitrogen | 12mm | 18mm | |
A1050 Aluminum Plate | Air | 6mm | 2mm |
Nitrogen | 6mm | 8mm | |
A5052 Aluminum Alloy Plate | Air | 6mm | 2mm |
Nitrogen | 10mm | 16mm |
The effect of air as an auxiliary gas in cutting
(1) For carbon steel plate
When air is used as an auxiliary gas during cutting, the cut sections will produce smaller burrs, but these burrs are not sharp and may be acceptable for parts with low burr requirements.
(2) For stainless steel sheet
When air is used as an auxiliary gas during cutting, the material will undergo oxidation, leading to defects such as slag and stoma in the welding section, which will negatively impact the quality of the welding seam and reduce the strength of the welding joint.
Therefore, it is necessary to remove the oxide layer from the welding section by polishing to improve the welding quality after cutting with air as the auxiliary gas.
Additionally, the cut section will develop a yellow oxide layer, which can be problematic for the external parts. This oxide layer also affects the welding process, making it necessary to polish before welding is carried out.
(3) For aluminum plate and aluminum alloy plate
Using air as an auxiliary gas can reduce the size of the cutting burr, while using nitrogen will result in larger cutting burrs.
Requirements for air supply device when using air as auxiliary gas
When air is used as an auxiliary gas, a pressure of 0.9 MPa is required. To meet this requirement, it is recommended to use a screw-type air compressor with a nominal working pressure of 1.26MPa and a flow rate of 2.3m3/min.
It is important to ensure the quality of the compressed air, with a drying rate of 99% and a moisture content of less than 1/100. To achieve this, it is necessary to use high-quality filter elements in the compressed air piping and replace them regularly.
To choose a dryer, two options are available: a regenerative adsorption dryer and a freeze dryer. Although both have their own characteristics, it is recommended to choose the regenerative adsorption dryer for its stability, ease of maintenance and long-term use.
When selecting the diameter of the compressed air piping and pressure reducer, it is important to consider the flow rate and compressor outlet pressure to maintain stable pressure when using compressed air.
It is important to note that screw air compressors with permanent magnetic frequency converter are available on the market, which can save up to 50% electricity compared to non-variable speed screw air compressors.
Conclusion
In today's highly competitive industrial environment, companies can gain a competitive advantage by improving their production processes, improving the level of design of their products, among other means.
Another effective way to gain a competitive advantage is to reduce processing costs within the existing process.
By using air as an auxiliary gas for cutting materials, companies can reduce cutting costs and increase profits, supporting their transformation and modernization efforts.