What is a laser cutting head lens?
The laser cutting head lens is one of the precision components of a laser cutting head, forming an integral part of the optical system of the laser cutting head. The installation and condition of the laser cutting head lens significantly affect the quality of laser cutting. Therefore, we must pay attention to this component.
Why does the laser cutting head lens have black spots?
Black spots on the laser cutting head lens usually result from slag splashing and adhering to the quartz lens during the drilling and cutting process.
Black dots on the laser cutting head lens can make normal cutting operations difficult. This occurs because the black dots grow continuously during the laser emission process, gradually eroding the protective lens. This eventually leads to focal point shift due to thermal lens effect due to overheating in the center of the lens. Essentially, this reduces the focal length, preventing normal cropping.
Why do black spots/burns appear on the lower protective lens of the laser cutter?
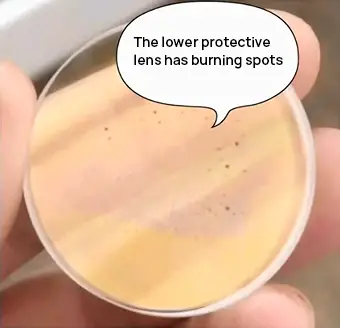
Reason 1: Excessive negative focus during drilling, causing drilling slag to return to the laser cutting machine lens.
Solution: Increase the focus of the piercing.
Reason 2: Inadequate drilling energy, drilling time too close to limit, or explosive drilling.
Solution: Reduce working cycle, increase drilling time.
Reason 3: Cutting parts with co-edge layout, deformation of sheets causing difficulty in connecting the cuts.
Solution: Add perforation in the co-edge cutting position or increase micro-connections in the part layout.
Reason 4: Contamination by metallic particles in the airway piping.
Solution: Clean or replace piping, identify and replace the source of metal dust (e.g., piping joint connections).
Why does oil/dust or moisture appear on the lower protective lens of the laser cutter?
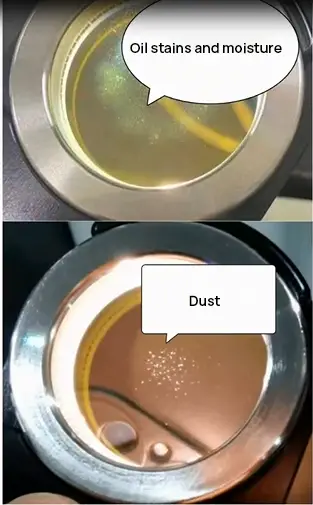
Reason 1: The air compressor filter does not meet usage standards.
Solution: Check whether the air compressor filter core is ineffective or upgrade the filter level.
Reason 2: The airway tubing is dirty.
Solution: Disconnect the air inlet pipe from the cutting head, wash the air inlet of the machine tool with high-purity alcohol under atmospheric pressure, clean the pipeline 3-4 times, or replace the airway pipeline.
Reason 3: The air inlet seat filter of the fiber laser cutting machine is blocked by raw materials or other foreign objects.
Solution: Disassemble the air intake seat and check whether the air intake seat filter is blocked by foreign objects.
How can we prevent the occurrence of black spots?
The focusing lens of the fiber optic laser cutting machine, located on the cutting head, is quite expensive. Therefore, a protective lens is designed to protect you. Consequently, replacement of the protective lens is routine. However, if the replacement frequency accelerates, it is necessary to identify the problem.
Black spots often occur due to the adhesion of molten slag splashed during the drilling and cutting processes onto the quartz lenses. As these black dots continually grow and corrode the protective lens during the light emission process, the center of the lens may experience focal shift due to the effect of overheating expansion thermal lens. This actually reduces the focal length, making cropping impossible, and cleaning up those black spots is quite challenging.
There are two types of lenses on the laser cutting head: the focusing lens and the protective lens. Its main function is to concentrate the laser beam; therefore, it is essential to keep these lenses clean and translucent.
When black spots appear, what should we do?
- The lens material of the laser cutting head is zinc oxide, which is brittle and difficult to fall off. Care must be taken during disassembly and assembly: avoid pulling hard or colliding with hard objects. The surface of the lens has an anti-reflective film, which is sensitive to pollution, humidity, grease and scratches. Therefore, dry and degreased air must be provided during work. Never handle the lens directly with the laser cutting head to protect it, as oils from your skin can permanently damage the lens surface. Instead, you can operate it with gloves and special glove devices. For smaller lenses, optical tweezers or vacuum tweezers are more convenient. Regardless of the method used to hold the laser cutting machine to protect the lens, it should only be clamped along the non-optical surface such as the edge of the mirror.
- Generally, the protective condition of the laser cutting head lens needs to be checked before and after use and cleaning. Because most contaminants and surface defects are relatively small, we often need to use magnification equipment when inspecting lenses. In addition to magnifying equipment, sometimes we also need to illuminate the optical surface with a brighter beam to improve the mirror reflection of surface contaminants and defects, making them easier to detect.
- When cleaning the laser cutting head to protect the lens, clean cleaning paper and optical solvent are generally used to avoid damage caused by other contaminants. The cleaning paper must be moistened with the appropriate solvent and must not be dry. Considering mildness, available cleaners include pure cotton gauze paper or cotton balls, lens paper, cotton swabs, etc.
The lens of the laser cutting head is the core and needs good protection to effectively utilize the performance of the laser cutting head.
Suggestions for dealing with black spots on laser welding head lenses
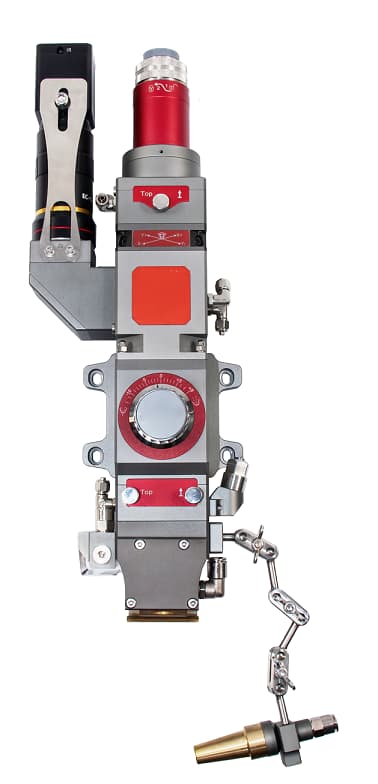
How to deal with black spots on laser welding head lens?
Cleaning these blackheads can be a challenge, mainly for the following reasons:
- Impure black stains have infiltrated the protective lens.
- The protective lens has been damaged.
What to do if there are black spots on the lens of the laser cutting and welding head?
Since it is difficult to deal with black spots on the laser cutting head lens, direct lens replacement is recommended. To prevent black spots from appearing on the laser cutting head lens, it is crucial to take preventive measures.
Finally, how to choose the lens for the laser cutting head?
- Size and shape compatibility, which is quite simple to understand.
- Material: Depending on the power of the laser and considering the cost, you can opt for K9 or quartz. In practical applications, professional manufacturers divide these two materials into different grades. Customers can choose the necessary specifications based on their practical requirements.
- Coating: Laser anti-reflective film. Depending on the operating environment, different coating technology parameters must be used.