According to the report on the development of China's laser industry, in the domestic fiber laser market, the overall shipment of domestic low- and medium-power conventional fiber lasers has surpassed that of foreign products in the same power section due to the improvement Graduation of power and performance of domestic fiber lasers. This achievement demonstrates the success of import substitution.
Furthermore, the overall shipment of domestic ultra-high-power conventional fiber lasers above 10 kW is almost on par with that of foreign products in the same power section.
This indicates that domestic fiber lasers are gaining acceptance in the domestic market due to the continuous improvement of independent research and development strength.
Furthermore, industrial market demand for high-power 10,000-watt lasers increases every year as the processing of laser products demands higher standards. This trend has become increasingly prevalent.
Customers are faced with a wide range of 10,000 watt lasers on the national market and have many questions when choosing the appropriate equipment.
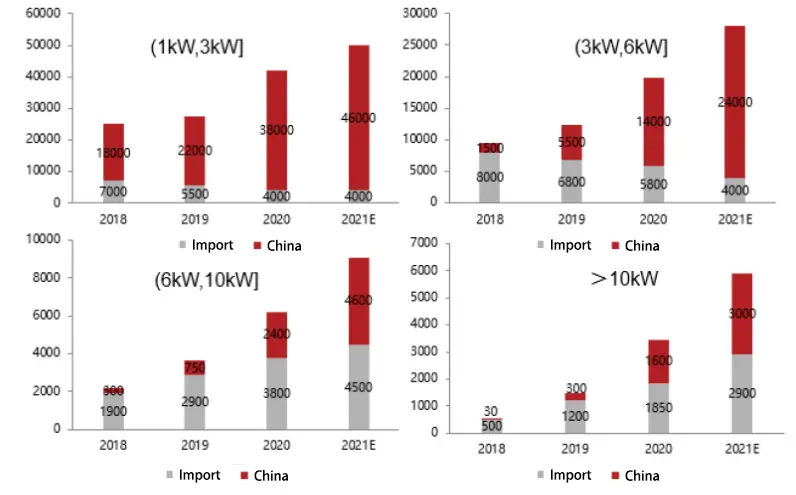
1. FAQ About Selecting Fiber Lasers
Q1: The higher the power, the higher the processing efficiency?
In recent years, high power has become more and more popular in the laser processing industry. Take the Raycus laser as an example. Last year, sales of laser products above 10,000 watts exceeded 2,380 units, an increase of 243% compared to 2020 and a total of 3,200 units sold throughout history. This number is much higher than that of other national brands. Raycus laser's continuous fiber laser products have reached 100 kW, setting a domestic precedent.
However, higher power does not necessarily mean higher processing efficiency of laser products.
Efficiency depends on the configuration of the laser's main components, such as active fiber, pump source, and high-power combiner, as well as the type and thickness of the plate being processed.
The configuration of the laser's core device plays a significant role in determining its processing efficiency. More advanced core devices and their matching can achieve higher processing efficiency than other brands of lasers with the same power.
In addition, the type and thickness of sheets processed by customers must also be considered when measuring processing efficiency. Furthermore, different applications such as welding and coating have additional factors that affect processing efficiency. Therefore, it is not appropriate to compare the processing efficiency of different lasers based on their power alone.
Lastly, we will examine the effects of the Raycus laser cutting process of carbon steel with different thicknesses of 12 kW, 20 kW and 30 kW.
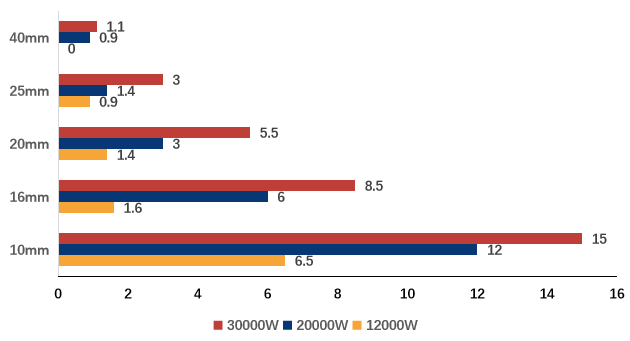
Mild steel thickness | 10mm | 16mm | 20mm | 25mm | 40mm |
12,000W | 6.5m/min | 1.6m/min ( O2 ) |
1.4m/min (O 2 ) |
0.9m/min (O 2 ) |
/ |
20,000W | 12m/min | 6m/min | 3m/min | 1.4m/min (O 2 ) |
0.9m/min ( O2 ) |
30,000W | 15m/min | 8.5m/min | 5.5m/min | 3m/min | 1.1m/min (O 2 ) |
Efficiency improvement | 25% | 41.70% | 83.30% | 114.30% | 22.20% |
The table shows three multimode groups with powers of 30 kW, 20 kW and 12 kW, all used to cut carbon steel during process measurement. The auxiliary gas used for all three is air, although this is not marked in the table.
When examining the table, it is evident that the efficiency of the 30 kW multimode group for cutting 10 mm thick carbon steel using auxiliary air is 25% higher than that of the 20 kW group.
Although there is an improvement in efficiency, it is not very significant. However, the advantage becomes more evident when cutting 25 mm thick carbon steel, with the 30 kW multimode group showing an efficiency 114.3% higher than the 20 kW group (which uses auxiliary oxygen).
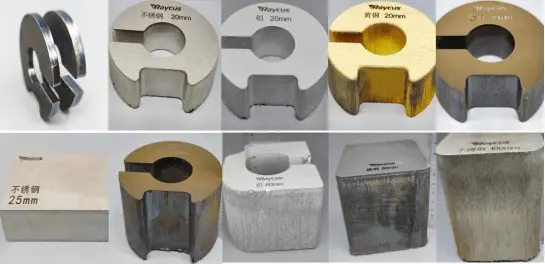
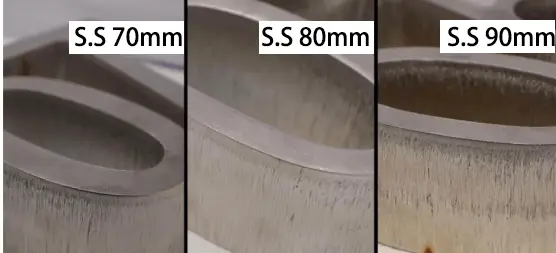
Product application cases
In terms of practical application, customers should select high-power products that are most suitable for their own processed sheets based on their type and thickness.
If the majority of the customer's processing involves thin sheets, they should select products at the 10,000-watt level to maximally meet their processing efficiency needs.
On the other hand, if medium and thick plates comprise most of the processing or the processing volume is large, customers should choose higher power 10,000 watt laser products.
Many customers opt for equipment equipped with a 30 kW Raycus laser due to the large processing volume. This equipment can satisfy the comprehensive requirements of cutting speed and section quality of thin, medium and thick sheets.
It has significant advantages in air cutting of medium and thick sheets, which substantially improves the processing efficiency of the factory. This, in turn, reduces overall operating costs and leads to faster returns.
Q2: Under the same power, the smaller the fiber core, the better?
As we all know, the current advancement of laser technology is focused on high power and high brightness.
Some laser manufacturers have misguided customers to believe that “a small core represents high brightness. However, this is a misconception.
The quality of a high-brightness laser is closely related to the BPP (beam parameter product) value, which is calculated using the beam waist radius (ω₀) and the far-field divergence angle of the laser beam (θʀ) . A lower BPP value indicates better beam quality.
Brightness is defined as the power per unit area and per unit solid angle. Thus, to achieve high brightness, two preconditions must be met: improving laser power and improving beam quality.
Individual and joint improvements can lead to an increase in laser brightness. However, improving beam quality is not the same as reducing the fiber core diameter.
This occurs because the core diameter cannot be equal to the beam waist diameter. When reducing the core diameter, the far-field divergence angle of the beam should not increase to reduce the BPP value and obtain better beam quality.
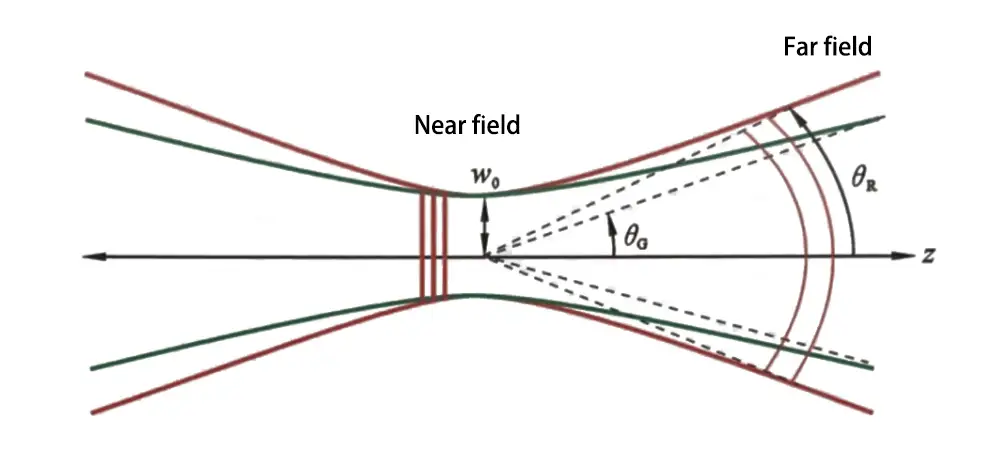
BPP=ω₀*θʀ,ω ₀is the waist radius, θʀ is the beam divergence angle
In the application scenario of ultra-high-power fiber lasers, customers demand improvements in benefits, which can be achieved from two aspects:
Firstly, by increasing the electro-optical conversion efficiency of fiber lasers, it is possible to save electricity and money.
Secondly, by improving the comprehensive processing efficiency, the objective of increasing efficiency and profitability can be achieved.
Laser processing is a systematic project that requires multidimensional coordination and complementarity of machine tools, systems, gas paths, processing heads, laser sources, boards and processing technology. Only then can the system utilization rate be genuinely increased and optimal yield generated.
Raycus laser Wanwa series fiber lasers have an electro-optical conversion efficiency of over 40%, and the divergence angle is largely optimized, making them compatible with cutting heads and systems with different optical configurations of all available brands in the market. This allows for better consideration of customer cutting needs for thin, medium and thick sheets.
Q3: How to choose single-mode group and multi-mode group under the same power?
The composition of fiber laser modules is divided into two groups: single-mode and multi-mode. In cutting applications, the quality of the cut is greatly affected by the focus point.
The 10,000-watt single-mode laser uses a single fiber amplification to reach the 10,000-watt level. The beam has an almost Gaussian distribution and the energy is relatively concentrated.
Typically, the mode conversion method is used to obtain the beam homogenization effect, which is greatly influenced by the consistency of the devices.
10,000-watt multi-mode lasers generally combine several 2,000~6,000-watt optical modules to produce the beams, which overlap to naturally form homogenization effect and good consistency.
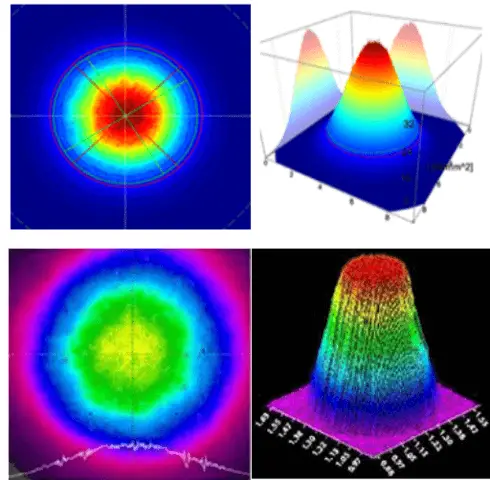
Comparison of beam patterns of 10,000-watt single-mode and multimode fiber lasers
The top two images represent single-mode fiber lasers, while the bottom two show multimode fiber lasers.
The advantage of using a 10,000 watt single-mode laser is its cutting speed for medium and thin sheets. When compared to the Raycus 12000 single-mode and 12000 multi-mode lasers, the cutting efficiency of the 12000 single-mode laser is better than that of the 12000 multi-mode fiber laser when cutting stainless steel with thicknesses below 20 mm, and when assisted by nitrogen or air.
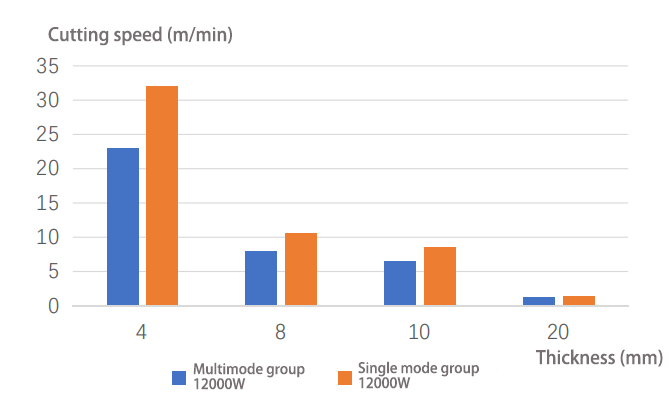
Mild steel thickness | 4mm | 8mm | 10mm | 20mm |
Multimodule12000W | 23m/min | 8m/min | 6.5m/min | 1.2m/min |
Single module 12000W | 32m/min | 10.5m/min | 8.5m/min | 1.4m/min |
Efficiency improvement | 39.13% | 31.25% | 30.77% | 16.67% |
12,000 W single-mode group and 12,000 W multi-mode group
Comparison of the effect of measured data of stainless steel cutting process
The 10,000 watt multimode laser has better beam homogenization effect, which makes the advantage of thick plate cutting quality more obvious.
Some customers have extremely demanding processing requirements and therefore opt for multimode fiber lasers.
In essence, singlemode and multimode groups cannot be compared directly. Both are fiber laser setups, similar to those in cars.
Cars are designed for roads, while off-road vehicles are built for mountains. However, cars can navigate in mountains, and all-terrain vehicles can also operate on roads.
Consequently, the selection of a multimode or single-mode fiber laser depends on the customer's specific processing needs.
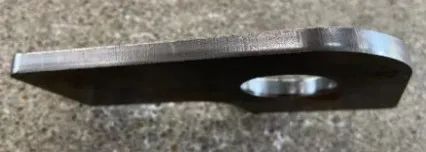
Single 12,000W module cutting 6mm carbon steel effect
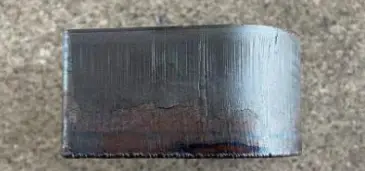
12,000W Multimode Group Cutting with 30mm Carbon Steel Effect
2. How to choose the right laser products above 10kW?
Choosing the right products depends on the application needs of the market.
For most user companies, it is crucial to select a laser with high cost performance based on specific application scenarios.
Customers can comprehensively evaluate products based on three aspects: processing demand, cost demand and service demand.
Firstly, different users have different requirements for cutting thickness, sheet metal processing speed and efficiency. Therefore, when selecting laser products, it is essential to consider the actual thickness and daily cutting plate processing demand of the factory.
Secondly, product cost is also a crucial factor in laser selection under the condition of maximizing the current processing demand. The cost of using laser can be comprehensively compared based on electro-optical conversion efficiency, shutdown cost, purchase price and other factors.
Finally, lasers are bulk products with high unit price and long service life, regardless of product performance parameters such as beam quality, electro-optical conversion efficiency, stability and sheet cutting demand. Users should also focus on product quality assurance and after-sales services, making it the best choice to opt for a reputable brand of lasers.