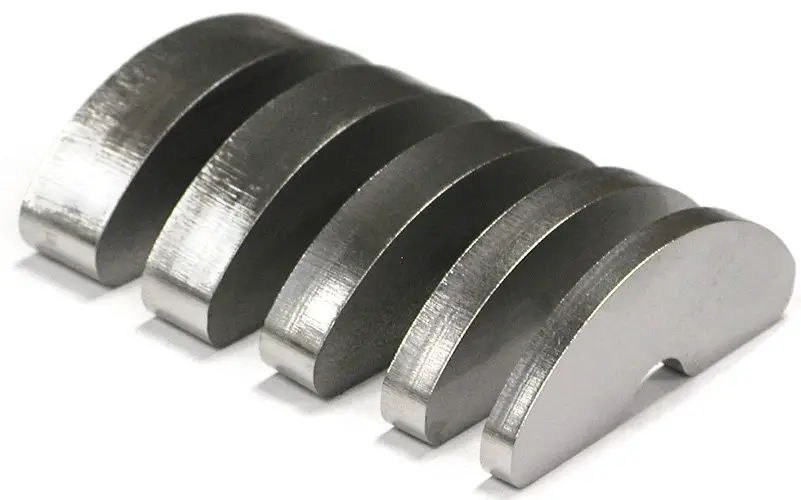
The quality of a laser cutting machine is mainly determined by the cutting quality, which is the most direct way to evaluate the machine. When purchasing a laser cutting machine, new customers typically ask to see a sample of the cutting process performed by the machine.
See too:
- How to choose fiber laser cutting machine?
The cutting speed of laser cutting equipment is important for customers to consider. Furthermore, they should also focus on the quality of the sample cut.
So how do you assess the quality of laser cutting and what should you pay attention to? Let me provide some more details.
It's important to keep the following nine standards in mind.
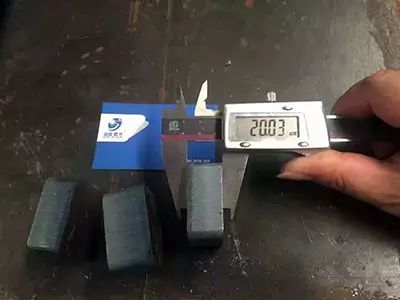
Roughness
Laser cutting produces vertical lines and the depth of these lines determines the roughness of the cutting surface.
The lighter the line, the smoother the cutting section will be.
Roughness affects not only the appearance of the edge but also the friction characteristics.
In most cases, roughness should be minimized as much as possible and therefore the clearer the lines, the higher the quality of the cut.
Perpendicularity

If the sheet thickness exceeds 10 mm, the vertical degree of the cutting edge becomes very important.
The laser beam diverges when away from the focus, causing the cutting width to increase up or down depending on the focus position.
The cutting edge may deviate a few millimeters from the vertical line. The more vertical the edge, the higher the quality of the cut.
cutting width
The width of the notch, in general, does not affect the quality of the cut, except when the contours of the parts are formed with particular precision. In these cases, the cutting width will be affected because it determines the minimum internal diameter of the outlined shape.
When the board thickness increases, the cutting width also increases.
Therefore, to ensure the same high precision regardless of the cutting width, the working area of the part in the laser cutter must remain constant.
See too:
- Things You Should Know About Laser Cutting

Lines
When cutting thick plates at high speed, molten metal will not accumulate in the incision below the vertical laser beam, but will be sprayed at the end of the laser beam.
This results in the formation of curved lines on the cutting edge that follow the moving laser beam.
To solve this problem, reducing the feed rate at the end of the cutting process can significantly reduce the formation of these curved lines.
Burr
Burr formation is a crucial factor that determines the quality of laser cutting, as burr removal requires additional work.
Therefore, the severity and quantity of burrs are the most important factors in evaluating the quality of the cut.
Deposited material
Before melting the perforation, the laser cutter sprays a special layer of oily liquid onto the surface of the part.
During the cutting process, the vaporization of various materials requires the customer to use airflow to remove the incision. However, this can also cause deposition to form on the surface in an upward or downward direction.
Depression and corrosion
Curvature and corrosion can have an adverse effect on the surface of the cutting edge, thereby affecting the appearance of the workpiece.
In general, these are cutting errors that should be avoided.
Thermal Zone
In laser cutting, the area near the incision is heated and, as a result, the structure of the metal changes.
For example, some metals will harden during this process.
The depth of the region where the internal structure changes is known as the region of thermal influence.
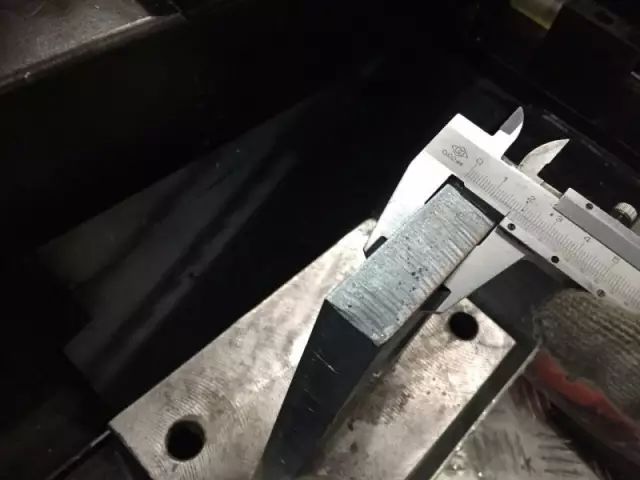
Deformation
If the cutting process causes the part to heat up quickly, deformation may result.
This is especially significant in fine processing, as contours and connections are often only a few millimeters wide.
Controlling laser power and using short laser pulses can help reduce heat generated in parts and prevent warping.