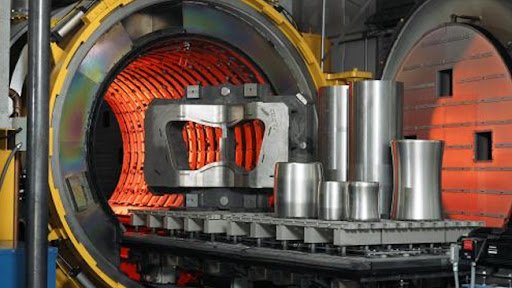
¿Cómo puede la dureza del acero H13 alcanzar los 58 HRC mediante tratamiento térmico?
Esto se puede lograr calentando y enfriando a temperaturas entre 1050 y 1100°C, seguido de un enfriamiento con aceite.
Sin embargo, no es necesario que el acero para matrices para trabajo en caliente tenga una dureza tan alta, ya que su rendimiento se reducirá significativamente con una dureza alta.
Normalmente, un rango de dureza de HRC46-50 proporcionará un buen rendimiento y durabilidad.
Después del tratamiento térmico del molde, ¿con qué se blanquea la superficie?
- Se puede lavar con ácido de acero inoxidable o ácido clorhídrico. También se puede adoptar un tratamiento de chorro de arena.
Si se utiliza una máquina rectificadora, el costo de procesamiento puede ser alto, la cantidad de material procesado puede ser grande, pero el tamaño del producto puede no cumplir con el estándar requerido.
Si el ácido clorhídrico no logra limpiar la superficie, es probable que esté utilizando acero con un alto contenido de cromo. ¿Es acero D2 o H13?
La capa de óxido en el acero con matriz con alto contenido de cromo es difícil de eliminar, pero se puede eliminar con un limpiador ácido para acero inoxidable. Estos limpiadores están disponibles en tiendas de moldes o acero inoxidable.
- La crema decapante de acero inoxidable funciona.
La capa de óxido de los aceros para moldes con alto contenido de cromo no se puede eliminar fácilmente con ácido clorhídrico. Sin embargo, existen métodos alternativos disponibles.
Después de pulir el molde con una piedra de aceite, la superficie quedará lisa. Puede utilizar una piedra de afilar gruesa o una cinta abrasiva para lijar antes del tratamiento térmico. Luego se puede volver a moler el molde con una piedra de aceite fina.
Otro método que utilizan algunas personas es lijar primero el molde con una rueda de fibra para eliminar eficazmente la película en blanco. Luego se procede al lijado y pulido o arenado.
¿Cómo trata la planta de tratamiento térmico el metal?
La planta de tratamiento térmico alberga una amplia gama de equipos, incluidos un horno discontinuo y un horno de pozo.
El horno discontinuo es el más utilizado y puede soportar diversos tratamientos térmicos como recocido, normalizado, templado y revenido. Es un horno calentado eléctricamente que se calienta a una temperatura predeterminada antes de colocar la pieza en su interior. Luego de alcanzar la temperatura deseada, la pieza se mantiene caliente por un tiempo y luego se retira o se enfría dentro del horno.
El horno de pozo se utiliza normalmente como equipo de cementación y se entierra bajo tierra. Una vez colocada en el interior, la pieza se sella y luego se sumerge en líquidos ricos en carbono, como queroseno o metanol, a altas temperaturas. El líquido se disuelve en átomos de carbono, que penetran en la superficie de la pieza.
El estanque de enfriamiento se usa para el enfriamiento y contiene una solución acuosa o aceite que se usa para enfriar piezas endurecidas en hornos de tipo discontinuo. El proceso consiste en colocar la pieza en el tanque y esperar un breve período antes de retirarla.
Otros dispositivos de la planta incluyen máquinas de alta frecuencia, que convierten una corriente eléctrica de 50 Hz en una corriente de 200 KHz. El modelo más común tiene una potencia máxima de 200Kw y tiene una batería de tubo de cobre con agua de refrigeración interna colocada en el exterior de la pieza. En cuestión de segundos, la superficie de la pieza se vuelve roja y, cuando alcanza la temperatura predeterminada, una camisa de agua rocía la solución de enfriamiento sobre la superficie para completar el proceso de enfriamiento.
En resumen, la planta de tratamiento térmico cuenta con una variedad de equipos, entre ellos los mencionados anteriormente.
¿Por qué los materiales Cr12 o Cr12MoV se rompen después del tratamiento térmico?
Sin información sobre el tamaño y la forma de las piezas, los requisitos de tratamiento térmico y las técnicas de tratamiento térmico adoptadas, identificar las causas puede resultar un gran desafío.
Ambos tipos de acero pertenecen a la misma categoría de acero lepidolita con alto contenido de cromo, que tiene tendencia a agrietarse en condiciones de frío. La técnica de tratamiento térmico necesaria para este acero también es compleja.
Según mi experiencia, se pueden utilizar las siguientes técnicas de tratamiento térmico:
Para obtener dureza térmica y alta resistencia al desgaste, el acero se puede templar a 950-1000°C y enfriar con aceite, lo que da como resultado un HRC>58. Para obtener mejores resultados, la temperatura de enfriamiento se puede aumentar a 1115-1130 °C y luego enfriar el aceite.
Para moldes delgados y delgados, se puede usar enfriamiento por aire y, para reducir la deformación, se recomienda enfriamiento con solución salina a una temperatura entre 400 y 450 ℃.
El templado no debe realizarse por debajo de 300-375 °C, ya que esto puede reducir la dureza de la herramienta y provocar fragilidad del templado. Es importante condimentar inmediatamente después del atemperado.
Si el enfriamiento se realiza a una temperatura superior a 1100°C, se recomienda revenir dos o tres veces por debajo de 520°C.
Es fundamental tener en cuenta que las altas temperaturas de enfriamiento pueden provocar la descarbonización. Por tanto, es aconsejable realizar un pretratamiento térmico (recocido esferoidal) antes del enfriamiento.
¿Cómo distinguir las piezas tratadas térmicamente de las no tratadas térmicamente?
Adicional:
“El trabajador mezcló accidentalmente una pieza en bruto sin calentar con un lote de piezas bien tratadas térmicamente. Ambos fueron sometidos a un tratamiento de voladura inferior, por lo que fue imposible diferenciarlos por el color. Además, su dureza está en el rango de HRC35-45, lo que dificulta distinguirlos también en función de la dureza. Entonces, ¿cómo podemos diferenciarlos? Por favor no sugerir cortar la pieza para observar la estructura metalográfica, ya que esto dañaría el producto”.
Respuestas:
Si no puede identificar la dureza o los colores oxidantes del tratamiento térmico, le sugiero que los identifique reproduciendo el sonido.
La estructura metalográfica de una pieza fundida y de una pieza después del templado y revenido es diferente. También existe una diferencia en el consumo interno, que puede determinarse por el tono del sonido.
¿Qué significa sobrecalentamiento en el tratamiento térmico?
Si se excede la temperatura de calentamiento especificada, el grano se hinchará y se deteriorarán diversas propiedades mecánicas, como mayor fragilidad, menor tenacidad, fácil deformación y agrietamiento.
Para evitar el sobrecalentamiento, es fundamental controlar la temperatura de calentamiento.
Si el acero está demasiado quemado, no se puede reparar mediante tratamiento térmico o mecanizado.
¿Causas y medidas preventivas para eliminar grietas en los moldes?
Causas:
- Existe una severa segregación de carburo en los materiales del molde, lo que puede causar varios problemas.
- El mecanizado mecánico o la tensión de deformación plástica en frío pueden afectar el rendimiento del molde.
- Un tratamiento térmico inadecuado, como calentar o enfriar demasiado rápido, usar un medio de enfriamiento de enfriamiento inadecuado, establecer la temperatura de enfriamiento demasiado baja o el tiempo de enfriamiento demasiado largo, pueden causar problemas.
- Los moldes complejos, los espesores irregulares, los ángulos agudos y los agujeros roscados pueden provocar una tensión térmica y estructural excesiva.
- Una temperatura de calentamiento del enfriamiento del molde demasiado alta puede causar sobrecalentamiento o quemaduras excesivas.
- Un templado inadecuado o prematuro después del enfriamiento también puede afectar el rendimiento del molde.
- Calentar el molde nuevamente sin un recocido intermedio después del enfriamiento puede ser perjudicial.
- Los procesos de molienda inadecuados durante el tratamiento térmico también pueden causar problemas.
- El mecanizado por electrochispa después del tratamiento térmico puede crear altas tensiones de tracción y microfisuras en la capa endurecida.
Medidas preventivas:
- Es esencial un estricto control de calidad de los materiales del molde.
- Es necesario mejorar la tecnología de forjado y recocido esferoidizado para eliminar los carburos reticulares, en bandas y en cadena y mejorar la uniformidad del tejido esferoidizado.
- Después del mecanizado en frío o de la deformación plástica, el molde debe someterse a un recocido antiestrés (>600°C) antes del templado.
- Para moldes complicados, se debe usar amianto para cubrir el orificio roscado, unir las secciones peligrosas y las paredes delgadas, y se debe adoptar un enfriamiento gradual o un enfriamiento isotérmico.
- Es necesario recocer o templar a alta temperatura al reparar o renovar el molde.
- El molde debe precalentarse antes del enfriamiento, preenfriarse durante el enfriamiento y se debe seleccionar un medio de enfriamiento adecuado.
- La temperatura de templado y el tiempo de calentamiento deben controlarse estrictamente para evitar el sobrecalentamiento y la quema del molde.
- El molde debe templarse de manera oportuna después del templado y el tiempo de conservación del calor debe ser suficiente. Los moldes complejos de alta aleación deben templarse de 2 a 3 veces.
- Elegir la técnica de rectificado y la muela abrasiva adecuadas es fundamental.
- Es necesario mejorar la técnica del mecanizado por chispa eléctrica y realizar un templado antiestrés.
¿Cómo calentar troqueles de estampado grandes, especialmente para troqueles de corte de bordes?
Para el tratamiento térmico de moldes, se recomienda optar por un tratamiento térmico al vacío para minimizar la deformación.
Para facilitar el tratamiento térmico, los moldes se pueden dividir en trozos pequeños y se debe utilizar un corte lento para asegurar una alta precisión, un buen acabado y una mínima deformación. Si se garantiza la holgura, las rebabas serán insignificantes. Es recomendable comprobar la precisión del dispositivo utilizado.
Además, es posible que la resistencia del molde convexo no sea suficiente. También puede haber tensión residual en la lámina de metal después del tratamiento térmico, lo que resulta en deformación durante el corte del alambre. Para mitigar esto, se sugiere considerar un fresado previo con orificios grandes para cortar alambre, seguido de un tratamiento de recalentamiento, dejando un margen de 3-4 mm.
¿Causas y prevención de puntos débiles en la superficie del molde?
Causas:
La superficie del molde presenta una capa oxidada, manchas de óxido y descarbonización parcial antes del tratamiento térmico.
Si el medio de enfriamiento no se elige correctamente, o si hay exceso o impurezas de envejecimiento en el medio de enfriamiento, puede causar problemas después de que el molde haya sido templado y calentado.
Medidas preventivas:
Antes del tratamiento térmico, es importante eliminar cualquier película de óxido y manchas de óxido. Además, es crucial proteger adecuadamente la superficie de la matriz durante el enfriamiento y el calentamiento. Para el calentamiento se recomienda utilizar un horno eléctrico de vacío, un horno de baño de sal o un horno de atmósfera protectora.
Durante el proceso de enfriamiento y calentamiento, es importante elegir el medio de enfriamiento adecuado. Si el medio refrigerante se utiliza durante un período prolongado, debe filtrarse o reemplazarse periódicamente.
¿Mala estructura antes del tratamiento térmico?
Causas:
La estructura original de los materiales de matriz de acero a menudo presenta una severa segregación de carburos.
Esto puede atribuirse a una tecnología de forjado deficiente, como el uso de altas temperaturas de calentamiento, deformación limitada, altas temperaturas de parada de forjado y bajas velocidades de enfriamiento, que dificultan la eliminación de los carburos reticulares, en bandas y en cadena.
Además, una tecnología de recocido de esferoides deficiente, como temperaturas de recocido excesivamente altas o bajas, o un tiempo de recocido isotérmico inadecuado, pueden conducir a una esferoidización irregular o deficiente.
Medidas preventivas:
Al seleccionar el material de acero para moldes, es importante considerar las condiciones de trabajo del molde, la cantidad de producción y la resistencia y tenacidad del material. Se recomienda elegir material de acero para moldes de alta calidad para garantizar un rendimiento óptimo.
Para mejorar el proceso de forjado, puede ser necesario adoptar un tratamiento térmico de preparación de normalización, que puede ayudar a eliminar cualquier falta de uniformidad de los carburos y carburos de la red y la cadena en las materias primas. En los casos en los que el acero con matriz con alto contenido de carbono presenta una segregación severa de carburos que no se puede forjar, se puede utilizar el refinado en solución sólida como método de tratamiento.
Para lograr el proceso de recocido esferoidizado deseado para palanquillas forjadas, es necesario formular especificaciones de proceso correctas basadas en el enfriamiento y el tratamiento térmico de enfriamiento y una técnica de recocido esferoidizado rápida y uniforme.
Además, es importante garantizar la uniformidad de la temperatura de la palanquilla en el horno mediante la implementación de una instalación razonable del horno.
Después del enfriamiento, la estructura del molde es grande, lo que hará que el molde se rompa cuando se use, lo que afectará gravemente la vida útil del molde.
Causas:
Mezclar el acero del molde es un error común. La temperatura de enfriamiento requerida para el material del molde es mucho más baja que la del acero real (por ejemplo, el acero GCr15 no debe tratarse como acero 3Cr2W8V).
La esferoidización inadecuada antes del enfriamiento es una de las principales causas de una esferoidización deficiente en el acero para moldes.
Tanto la temperatura de calentamiento de enfriamiento del molde excesivamente alta como el tiempo prolongado de conservación del calor pueden causar problemas.
La colocación inadecuada del molde en el horno puede provocar un sobrecalentamiento cerca del electrodo o de la unidad calefactora.
Los moldes con un cambio significativo en la sección transversal requieren una selección adecuada de los parámetros del proceso de enfriamiento y calentamiento para evitar el sobrecalentamiento en la sección delgada y el ángulo agudo.
Medidas preventivas:
Se debe realizar una estricta inspección del acero antes de ingresar al almacén para evitar mezclas y desorden.
Antes del enfriamiento, es importante realizar un forjado correcto y un recocido de esferoidización para garantizar una buena esferoidización.
Para garantizar un enfriamiento y calentamiento adecuados del molde, se deben seguir correctamente las especificaciones del proceso y se deben controlar estrictamente la temperatura de calentamiento del enfriamiento y el tiempo de conservación del calor.
Se deben realizar revisiones y correcciones periódicas del termómetro para garantizar que el instrumento esté funcionando correctamente.
Al calentar el molde en el horno, éste debe mantenerse a una distancia adecuada del electrodo o del grupo calefactor.
¿Cómo tratar térmicamente el acero Cr12MoV para fabricar moldes en frío?
Tratamiento de optimización de alta dureza, alta resistencia al desgaste y alta tenacidad:
- enfriamiento 980 ~ 1200 ℃;
- Enfriamiento con aceite (aceite de máquina)
- Enfriamiento a 400°C por una vez
- Enfriamiento a 240°C por una vez
- HRC57~61
¿Cuál es el motivo del agrietamiento del acero de matriz H13 después del tratamiento térmico (temperatura de enfriamiento 1100 ℃, enfriamiento del aceite)?
Se puede realizar un análisis metalográfico para determinar si hay alguna descarbonización en la superficie de los materiales. La descarbonización es una causa común de agrietamiento.
H13 es un material comúnmente utilizado para matrices de extrusión y el requisito de dureza para este material no es muy alto.
Recomiendo probar el tratamiento térmico en el rango de temperatura de 1030-1050°C.
¿Qué material se utiliza normalmente para la columna guía del molde y el manguito guía? ¿Qué tipo de tratamiento térmico se debe adoptar y qué tipo de rendimiento se debe lograr?
- Utilice acero estructural al carbono n.º 45 o acero para herramientas al carbono. La dureza del templado por tratamiento térmico es de alrededor de HRC45, inferior a HRC58~62. Se rompe fácilmente incluso con alta dureza.
- En términos generales, se utilizará SKD61 o SKD11 para requisitos elevados. La dureza de enfriamiento del acero H13 tratado térmicamente es de alrededor de HRC51.
¿Cuáles son los usos del tratamiento térmico en la fabricación de moldes?
Papel del tratamiento térmico en la fabricación de moldes:
- Aumentar la dureza y la resistencia al desgaste, mejorando así su vida útil;
- La resistencia se fortalece y la deformación se reduce para garantizar la precisión y la estabilidad del molde.
Análisis de las causas del fallo del molde.
La mayoría de las fallas de los moldes son causadas por fracturas, desgaste y deformaciones, siendo las principales razones un tratamiento térmico inadecuado y un mal mecanizado del molde. Por lo tanto, seleccionar cuidadosamente los materiales, formular correctamente el proceso de tratamiento térmico y mejorar la calidad del tratamiento térmico son cruciales para prolongar la vida útil del molde.
El tratamiento térmico del molde comprende el tratamiento de precalentamiento y el tratamiento térmico final, con el objetivo final de obtener una buena calidad superficial, resistencia, plasticidad y tenacidad en el molde.
Las razones de la caída de piezas de acero con matriz Cr12mov después del tratamiento térmico
Posibles Causas:
Durante el enfriamiento, si la temperatura excede el límite recomendado, puede provocar un sobrecalentamiento, lo que resulta en diversos problemas, como granos gruesos, descarbonización severa, martensita grande, fractura de granos gruesos, baja tenacidad y plasticidad reducida.
Las altas temperaturas de calentamiento y el tiempo prolongado de conservación del calor también pueden causar una descarbonización severa de la superficie del material, una estructura de grano grueso, una fuerza de unión débil y una reducción significativa de la plasticidad. Por tanto, es fundamental mantener la temperatura y el tiempo adecuados durante el proceso de templado para evitar este tipo de problemas.
Sugerencias:
- Revisar el equipo de calefacción;
- Ajustar la temperatura y el tiempo de enfriamiento y revenido;
- Realizar pruebas del proceso de tratamiento térmico de muestras y realizar análisis de pruebas de rendimiento requeridos.
¿Ventajas del tratamiento térmico en baño de sal?
Beneficios:
- Calentamiento uniforme, pequeña deformación.
- Una pequeña cantidad de descarbonización sin oxidación.
- El calentamiento rápido puede transformar rápidamente la estructura interna de la pieza de trabajo.
- Buen aislamiento térmico y uniformidad de calefacción.
- Puede calentarse mediante tratamiento con solución sólida.
- Amplia aplicabilidad
- Capaz de realizar una manipulación de entrega aproximadamente libre de oxidación.
Desventajas:
- El ambiente de trabajo es deficiente y la pieza de trabajo está corroída hasta cierto punto.
- La vida útil es relativamente corta.
- El espacio de trabajo es pequeño y la potencia es grande.
- La sal residual contamina el medio ambiente
¿Qué método se utiliza para comprobar el efecto del tratamiento térmico?
- Sólo comprueba la dureza de la superficie.
- Verifique la profundidad de la capa endurecida, la dureza del centro, el grado de estructura de la metalografía endurecida y el grado de estructura de la metalografía templada.
El valor crítico de dureza de la profundidad endurecida = dureza mínima endurecida × 0,8。
¿Cuál es el papel del tratamiento de enfriamiento profundo del material del molde?
El tratamiento de enfriamiento profundo es la continuación del proceso de enfriamiento de la pieza después del enfriamiento.
La aplicación en la industria del molde es principalmente en acero para moldes en frío, acero de alta velocidad, acero para rodamientos, moldes en frío y accesorios para moldes.
El enfriamiento profundo cambiará algunas propiedades mecánicas relacionadas. Las funciones principales son las siguientes:
- Mejorar la dureza y resistencia de la pieza de trabajo.
- Garantizar la precisión dimensional de la pieza de trabajo para mejorar la resistencia al desgaste de la pieza de trabajo.
- Mejorar la resistencia al impacto de la pieza de trabajo.
- Mejorar la distribución de tensiones internas de la pieza de trabajo.
- Aumentar la resistencia a la fatiga
- Mejorar la resistencia a la corrosión de la pieza de trabajo.
¿Cuáles son las razones de la explosión del tratamiento térmico Cr12MoV?
- ¿El medio refrigerante se está enfriando demasiado rápido (no se puede utilizar agua salada, agua pura, etc.)?
- Antes del enfriamiento, es posible que no esté recocido adecuadamente, lo que resulta en una tensión interna excesiva.
- Metalurgia de materiales deficiente (inclusión no metálica, estructura en bandas, carburo eutéctico)
- Durante el enfriamiento, la temperatura del horno aumenta muy rápidamente.
- Temperamento inadecuado
¿Qué es el fortalecimiento sin tratamiento térmico?
Tratamiento de superficies:
Como cromado duro para aumentar la resistencia al desgaste de las piezas.
Refuerzo de shot peening:
La resistencia a la fatiga de las piezas se puede mejorar enormemente bajo tensiones alternas.
Laminación:
La herramienta rodante se utiliza para aplicar presión a la superficie de piezas metálicas a temperatura ambiente. Esto provoca deformación plástica y modifica la forma microgeométrica de la superficie metálica. Al hacerlo, se mejoran la suavidad de la superficie, la resistencia a la fatiga, la resistencia al desgaste y la dureza de las piezas.