Visión general
En febrero de 2011, el profesor Skylar Tibbits, director del Laboratorio de Autoensamblaje del Instituto Tecnológico de Massachusetts (MIT), en Estados Unidos, presentó el concepto de modelado a través del autoensamblaje de materiales durante una charla TED (Technology, Entertainment , Diseño ). —una organización sin fines de lucro con sede en Estados Unidos.
En 2013, el profesor Tibbits regresó al escenario TED, presentando al mundo el concepto de impresión 4D por primera vez. Su charla atrajo una amplia atención en todas las industrias, reconociéndolo como el inventor de la impresión 4D.
Desde entonces, la impresión 4D ha captado el interés mundial, haciendo avanzar rápidamente la tecnología y expandiéndose a aplicaciones más amplias. El profesor Tibbits y su laboratorio de autoensamblaje, en colaboración con Stratasys, continuaron la investigación y desarrollaron numerosos modelos físicos de impresión 4D, como se muestra en las Figuras 8-1 a 8-4.
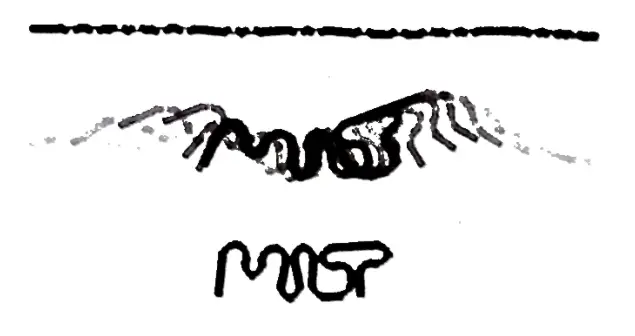
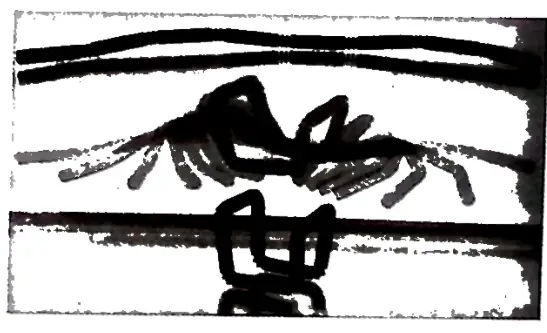

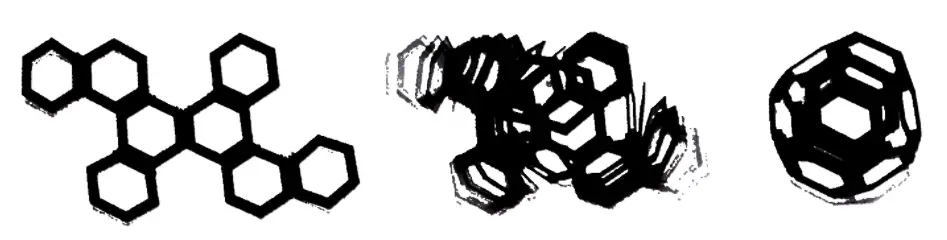
Actualmente, la tecnología de impresión 4D aún se encuentra en fase exploratoria y aún no ha alcanzado aplicaciones de producción a gran escala.
Sin embargo, tiene un enorme potencial para revolucionar la tecnología de producción, atrayendo la atención de varios países del mundo, especialmente Estados Unidos y China, con sucesivos resultados de investigación emergentes.
En 2011, el MIT inició una investigación sobre la tecnología de impresión 4D; en 2014, la empresa estadounidense Nervous System lanzó el primer vestido hueco impreso en 4D; en 2017, la NASA utilizó la impresión 4D para crear telas metálicas plegables, preparándolas para su uso en la fabricación de diversas naves espaciales; En 2016, un equipo de expertos del Hospital Xijing de la Cuarta Universidad Médica Militar de China, junto con un laboratorio nacional local, se convirtieron en los primeros en aplicar stents traqueales impresos en 4D para el tratamiento de bebés con cardiopatías congénitas complejas acompañadas de estenosis traqueal bilateral grave. .
En resumen, la impresión 4D está preparada para cambiar paradigmas, ampliar el pensamiento e inspirar anticipación y entusiasmo por el futuro.
El concepto y las implicaciones de la impresión 4D.
Desde que el profesor Skylar Tibbits introdujo por primera vez el concepto de impresión 4D en 2013, la definición ha sido interpretada por un número cada vez mayor de académicos, lo que ha dado lugar a una variedad de descripciones y cierto debate, sin llegar a un consenso. Vale la pena señalar que a medida que la tecnología de impresión 4D siga evolucionando, su contenido conceptual también se enriquecerá más.
En primer lugar, este libro proporciona una explicación completa de la impresión 4D tal como la describe el profesor Skylar Tibbits, que es la siguiente: La impresión 4D es un nuevo proceso que demuestra un cambio radical en la fabricación aditiva. Se trata de impresiones multimaterial con la capacidad de transformarse con el tiempo, o un sistema de materiales personalizado que puede cambiar de un formato a otro, directamente desde la plataforma de impresión.
Esta técnica ofrece un camino simplificado desde la idea a la realidad con una funcionalidad orientada al rendimiento integrada directamente en los materiales.
La cuarta dimensión se describe aquí como transformación en el tiempo, enfatizando que las estructuras impresas ya no son simplemente objetos estáticos y muertos; más bien, son programablemente activos y pueden transformarse de forma independiente. La impresión 4D es un primer vistazo al mundo de los materiales evolutivos que pueden responder a las necesidades de los usuarios o a los cambios ambientales.
En el corazón de esta tecnología se encuentran tres capacidades principales: la máquina, el material y el “programa” geométrico.
El profesor Skylar Tibbits explica la impresión 4D como un proceso fundamentalmente distinto de la impresión 3D (fabricación aditiva). La impresión 4D requiere un sistema en evolución de materiales múltiples o personalizados que, después de ser producidos mediante impresión 3D, puedan seguir evolucionando con el tiempo o transformarse de una forma a otra.
Al incorporar funciones impulsadas por el rendimiento directamente en el sistema de materiales, la impresión 4D ofrece un atajo del concepto a la realidad. La cuarta dimensión de la impresión 4D, que puede describirse como evolución en el tiempo, enfatiza que las estructuras creadas por la impresión 3D ya no son estáticas, sino que pueden programarse para una transformación autónoma.
Hay tres tecnologías principales en la impresión 4D: el hardware, los materiales y la “programación” geométrica.
Para comprender plenamente el concepto de impresión 4D explicado por el profesor Skylar Tibbits, es necesario comprender los siguientes matices:
La llamada cuarta dimensión se refiere a la evolución del sistema material evolutivo a lo largo del tiempo, lo que, según el profesor Tibbits, equivale al autoensamblaje, es decir, el sistema material puede cambiar a la forma deseada dentro de un período de tiempo definido. Basado en modelos definidos por software. .
La distinción fundamental de la impresión 3D radica principalmente en un cambio transformador en el enfoque de producción. La impresión 3D requiere un modelo tridimensional prediseñado y luego utiliza los materiales correspondientes para moldearlo, mientras que la impresión 4D incorpora el diseño del modelo tridimensional directamente en el sistema material, agilizando el proceso desde el "diseño" hasta el "objeto físico". ””.
Las tres principales tecnologías mencionadas son las siguientes: Para los equipos normalmente se pueden utilizar impresoras 3D convencionales directamente o con pequeñas modificaciones; En cuanto a los materiales, generalmente son compuestos multifásicos o materiales evolutivos, también conocidos como materiales inteligentes o materiales sensibles a estímulos.
Se refieren a materiales que pueden cambiar de forma autónoma sus propiedades físicas o químicas (incluyendo forma, densidad, color, elasticidad, conductividad, características ópticas, propiedades electromagnéticas, etc.) bajo estímulos predeterminados (como inmersión en agua o exposición al calor, presión, electricidad). , luz, etc.).
Actualmente, la atención se centra principalmente en cadenas filamentosas simples y materiales delgados en forma de láminas, y el próximo objetivo de la investigación será la creación de estructuras tridimensionales más complejas.
Actualmente, la impresión 4D es especialmente adecuada para imprimir cadenas de un solo filamento. En cuanto a la “programación geométrica”, se refiere a la relación de respuesta entre los estímulos materiales y las propiedades físicas mencionadas anteriormente, siendo el principal mecanismo de respuesta la generación de deformaciones características localizadas (o deformaciones por desajuste) dentro del objeto impreso durante o después de la impresión. . proceso.
Para el profesor Skylar Tibbits y su laboratorio de autoensamblaje, los equipos y materiales utilizados para la impresión 4D los proporciona Stratasys, mientras que la “programación” geométrica la proporciona el equipo de investigación y desarrollo de Autodesk. También desarrollaron un nuevo software llamado Cyborg. La Figura 8-5 ilustra la explicación del profesor Skylar Tibbits sobre la impresión 4D de una manera más intuitiva.
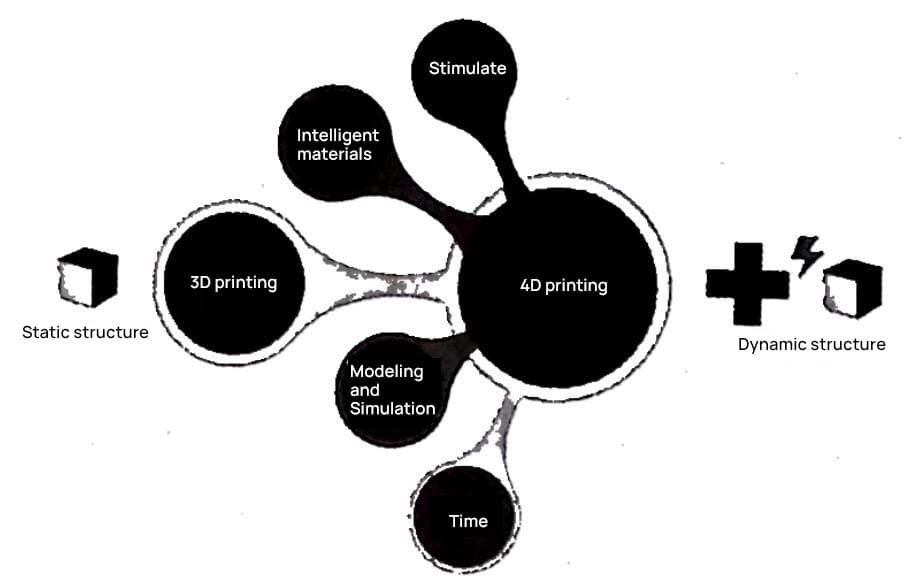
En 2014, el profesor Li Dicheng de la Universidad Xi'an Jiaotong ofreció un concepto conciso de la impresión 4D: la impresión 4D se refiere a la fabricación aditiva de materiales inteligentes, lo que significa que las estructuras hechas con tecnología de impresión 3D pueden cambiar su forma y estructura con el tiempo cuando se estimulan. por factores ambientales externos. La dimensión adicional que la tecnología de impresión 4D añade a la impresión 3D es el tiempo.
Así, el concepto inicial de impresión 4D puede entenderse simplemente como “impresión 3D + tiempo”, centrándose en cambiar la forma de los componentes a lo largo del tiempo con materiales inteligentes. Se cree que a medida que la investigación sobre la impresión 4D continúe profundizándose, su concepto y esencia se elevarán aún más.
materiales de impresión 4D
Un componente clave de la impresión 4D son los materiales inteligentes. A finales de los años 1980, inspirados por ciertas capacidades que se encuentran en la naturaleza, los científicos estadounidenses y japoneses introdujeron por primera vez el concepto de inteligencia en el campo de los materiales y las estructuras, proponiendo la idea innovadora de las estructuras materiales inteligentes.
También conocidos como estructuras inteligentes o sensibles, estos sistemas integran elementos sensores, actuadores y circuitos de control y procesamiento de señales asociados dentro de la estructura del material. Están diseñados para responder a estímulos y controles mecánicos, térmicos, ópticos, químicos, eléctricos y magnéticos.
Estos materiales no sólo son capaces de soportar cargas, sino que también tienen la capacidad de reconocer, analizar, procesar y controlar, ofreciendo capacidades multifuncionales como el autodiagnóstico, la autoadaptación, el autoaprendizaje y la autorreparación.
Las estructuras de materiales inteligentes representan una frontera interdisciplinaria, que abarca una amplia gama de campos como la mecánica, la ciencia de los materiales, la física, la biología, la electrónica, la ciencia del control, la informática y la tecnología. Un número significativo de expertos en estas disciplinas en todo el mundo participan activamente en el avance de estos campos.
Existen numerosas clasificaciones para materiales inteligentes, que pueden clasificarse ampliamente según su función y composición en materiales con memoria de forma, polímeros electroactivos, materiales piezoeléctricos, fluidos electrorreológicos y materiales magnetoestrictivos, siendo los materiales con memoria de forma los más utilizados.
Los materiales con memoria de forma incluyen polímeros con memoria de forma (SMP), aleaciones con memoria de forma (SMA), hidrogeles con memoria de forma (SMH), cerámicas con memoria de forma (SMC) y compuestos con memoria de forma (SMC).
Los polímeros con memoria de forma (SMP), también conocidos como polímeros con memoria de forma, son materiales poliméricos que pueden cambiar y fijar su forma inicial bajo ciertas condiciones y luego recuperar su forma original después de la estimulación por condiciones externas como calor, electricidad, luz o productos químicos. inducción.
La tecnología SMP utiliza la teoría moderna de la física de polímeros, junto con técnicas de síntesis y modificación de polímeros, para diseñar y ajustar molecularmente la estructura molecular de materiales poliméricos comunes como polietileno, poliisopreno, poliéster, copoliéster, poliamida, copoliamida y poliuretano.
Estos materiales están dotados de una forma específica bajo ciertas condiciones (estado inicial), que pueden cambiar y fijarse (estado deformado) cuando varían las condiciones externas. Si el entorno externo vuelve a cambiar de una manera específica, pueden regresar reversiblemente al estado inicial, completando el ciclo de memorizar el estado inicial, arreglar el estado deformado y regresar al estado inicial.
Las SMP se clasifican según el tipo de estímulo al que responden, incluidas las SMP inducidas térmicamente, las SMP inducidas eléctricamente, las SMP inducidas por la luz y las SMP inducidas químicamente.
Polímero con memoria de forma, SMP
Las SMP inducidas térmicamente se deforman por encima de la temperatura ambiente y pueden corregir la deformación durante el almacenamiento a largo plazo. Cuando se calientan a una temperatura de respuesta específica, los componentes recuperan rápidamente su forma inicial.
Estos polímeros se utilizan ampliamente en diversos campos, como la atención sanitaria, los deportes, la construcción, el embalaje, la automoción y los experimentos científicos, incluidos dispositivos médicos, espuma plástica, cojines de asientos, medios ópticos de almacenamiento de información y alarmas.
La función de memoria de forma de los SMP inducidos térmicamente se origina principalmente a partir de dos fases incompatibles dentro del material: la fase fija que conserva la forma del producto moldeado y la fase reversible que se ablanda y endurece con los cambios de temperatura. La fase fija se encarga de memorizar y recuperar la forma original, mientras que la fase reversible permite que el producto cambie de forma.
Según las características estructurales de la fase fija, los SMP inducidos térmicamente se pueden dividir en categorías termoestables y termoplásticas. Además, existe un polímero con memoria de forma llamado “moldeo por deformación en frío”, que implica procesar en frío ciertas resinas termoplásticas por debajo de la temperatura T para obtener una alta deformación elástica y luego enfriar para obtener un estado deformado.
Cuando se recalienta por encima de la temperatura Tg, el material también puede volver a su forma original.
Los SMP inducidos eléctricamente están compuestos de materiales poliméricos con memoria de forma inducida térmicamente con sustancias conductoras como negro de carbón conductor, polvo metálico y polímeros conductores. Su mecanismo de memoria es idéntico al de los polímeros con memoria de forma inducida térmicamente. El material compuesto utiliza calor generado a partir de una corriente eléctrica para aumentar la temperatura del sistema e inducir la recuperación de la forma.
Por lo tanto, tiene propiedades conductoras y una excelente funcionalidad de memoria de forma, y se utiliza principalmente en electrónica, comunicaciones e instrumentación, como tubos electrónicos de rayos catódicos y materiales de blindaje electromagnético.
Las SMP fotorresponsivas incorporan grupos fotocromáticos específicos (PCG) en la columna vertebral y las cadenas laterales del polímero. Tras la exposición a la luz ultravioleta, los PCG sufren una reacción de fotoisomerización, provocando un cambio significativo en el estado de la cadena molecular.
Macroscópicamente, el material muestra una transformación de forma inducida por la luz. Cuando cesa la exposición a la luz, los PCG reaccionan de forma reversible, revirtiendo el estado molecular y el material a su forma original. Estos materiales se utilizan en impresión, grabación óptica, válvulas moleculares activadas por luz y sistemas de liberación controlada de fármacos.
Las SMP inducidas químicamente se activan mediante cambios en el medio circundante para permitir la deformación del material y la recuperación de la forma. Los estímulos químicos comunes incluyen cambios de pH, equilibrio de intercambio iónico, reacciones de quelación, transiciones de fase y reacciones redox.
Estos materiales incluyen poliacrilamida parcialmente saponificada, alcohol polivinílico y mezclas de ácido poliacrílico en forma de película y se utilizan en campos especializados como membranas de separación para proteínas o enzimas y motores químicos.
Aleación con memoria de forma, SMA
Las aleaciones con memoria de forma (SMA) son materiales compuestos por dos o más elementos metálicos que exhiben efecto de memoria de forma (SME) a través de transformaciones de fase termoelástica martensítica y su inversa.
Los SMA ofrecen el mejor rendimiento con memoria de forma entre los materiales con memoria de forma. La martensita termoelástica, una vez formada, continúa creciendo a medida que disminuye la temperatura y disminuye al calentarse, desapareciendo en un proceso completamente reversible. La diferencia de energía libre actúa como fuerza impulsora para la transformación de fase.
Los SMA se clasifican en tres clases según sus características de deformación:
Efecto de memoria de forma unidireccional: los SMA se deforman a temperaturas más bajas y recuperan su forma original al calentarse, exhibiendo un efecto de memoria de forma solo durante el proceso de calentamiento.
Efecto de memoria de forma bidireccional: ciertas aleaciones recuperan su forma de fase de alta temperatura al calentarse y vuelven a su forma de fase de baja temperatura al enfriarse.
Efecto de memoria de forma completa: después del calentamiento, el material recupera su forma de fase de alta temperatura y, después de enfriarse, pasa a una forma de fase de baja temperatura con la misma geometría pero con orientación opuesta.
Hasta la fecha se han descubierto más de 50 tipos de aleaciones con efectos de memoria de forma. En 1969, el efecto de memoria de forma de la aleación de níquel-titanio se aplicó industrialmente por primera vez, lo que llevó a la creación de un dispositivo de acoplamiento de tubos único.
Al agregar otros elementos a la aleación de níquel-titanio, se han desarrollado e investigado nuevas aleaciones con memoria de forma basadas en níquel-titanio, como níquel-titanio-cobre, níquel-titanio-hierro y níquel-titanio-cromo. Además, existen otros tipos de aleaciones con memoria de forma, incluidas las aleaciones a base de cobre-níquel, cobre-aluminio, cobre-zinc y hierro (Fe-Mn-Si, Fe-Pd).
Los SMA se utilizan ampliamente en diversos campos, como el aeroespacial, la electrónica mecánica, la ingeniería biomédica, la construcción de puentes, la industria automotriz y en la vida cotidiana.
Hidrogeles con memoria de forma (SMH)
Los hidrogeles son un tipo de gel de red tridimensional altamente hidrófilo que puede hincharse rápidamente en agua y retener un volumen significativo de agua sin disolverse en el estado hinchado. La absorción de agua está estrechamente relacionada con el grado de reticulación; cuanto mayor es la reticulación, menor es la absorción de agua. Los hidrogeles se pueden clasificar en hidrogeles tradicionales e hidrogeles ambientalmente sensibles en función de su respuesta a estímulos externos.
Los hidrogeles tradicionales no son sensibles a los cambios ambientales como la temperatura o el pH; se adaptan alterando el entrecruzamiento de macromoléculas para capturar y liberar agua (proporcionando estimulación), logrando así contracción y expansión para facilitar las transiciones estructurales.
Los hidrogeles ambientalmente sensibles, por otro lado, son capaces de detectar pequeños cambios o estímulos en el ambiente externo (como temperatura, pH, luz, electricidad, presión, etc.) y responder con cambios significativos en las propiedades físicas y químicas, incluso abruptos. transformaciones. . La característica de estos hidrogeles es el cambio notable en su comportamiento de hinchamiento en respuesta a factores ambientales.
Partiendo de los diferentes mecanismos de respuesta de estos dos tipos de hidrogeles, se han desarrollado hidrogeles con memoria de forma que pueden utilizarse como sensores, interruptores de control, etc.
Cerámica con memoria de forma (SMC)
Los SMC exhiben efectos de memoria de forma que difieren de los SMP y SMA en las siguientes formas: primero, los SMC tienen una menor capacidad de deformación; en segundo lugar, los SMC experimentan diversos grados de deformación irreversible con cada memoria de forma y ciclo de recuperación, y a medida que aumenta el número de ciclos, aumenta la deformación acumulativa, lo que finalmente conduce a la formación de grietas.
Los SMC se pueden clasificar según el mecanismo de generación del efecto de memoria de forma en cerámicas viscoelásticas con memoria de forma, cerámicas con memoria de forma de transformación de fase martensítica, cerámicas ferroeléctricas con memoria de forma y cerámicas ferromagnéticas con memoria de forma.
Las cerámicas viscoelásticas con memoria de forma incluyen óxido de cobalto, óxido de aluminio, carburo de silicio, nitruro de silicio y cerámicas de vidrio de mica. Cuando estos materiales se calientan a una determinada temperatura, se deforman bajo carga y la fuerza externa mantiene la deformación. Tras el enfriamiento y posterior recalentamiento a una temperatura determinada, la deformación de la cerámica recupera su estado original.
Los estudios sugieren que las cerámicas viscoelásticas con memoria de forma contienen dos estructuras (cristalina y vítrea) y que la energía elástica que impulsa la recuperación de la forma se almacena en una de estas estructuras, mientras que la deformación se produce en la otra.
Las cerámicas martensíticas con memoria de forma, como ZrO 2 BaTiO 3 KNbO 3 PbTiO 3, se emplean principalmente en elementos actuadores de almacenamiento de energía y materiales funcionales especializados.
Las cerámicas ferroeléctricas con memoria de forma se refieren a cerámicas que exhiben características de memoria de forma cuando su orientación cambia bajo un campo eléctrico externo. Las regiones de fase de las cerámicas ferroeléctricas con memoria de forma incluyen sustancias paraeléctricas, ferroeléctricas y antiferroeléctricas, con tipos de transición de fase como transformaciones paraeléctricas-ferroeléctricas y antiferroeléctricas-ferroeléctricas.
Estas transiciones de fase pueden ser inducidas por un campo eléctrico o por la conmutación o reorientación de dominios magnéticos polares. Aunque las cerámicas ferroeléctricas con memoria de forma tienen deformaciones más pequeñas en comparación con las aleaciones con memoria de forma, tienen tiempos de respuesta rápidos.
También pueden sufrir transiciones reversibles, como paramagnética-ferromagnética, paramagnética-antiferromagnética, o de estados orbitales ordenados a desordenados, típicamente acompañadas de deformaciones reticulares recuperables.
Aplicaciones de impresión 4D
Los objetos fabricados mediante impresión 4D son productos inteligentes que tienen capacidades adaptativas y de autocuración. Son ampliamente aplicables en diversas industrias, incluidos tejidos y órganos artificiales, dispositivos médicos, transporte automotriz, maquinaria de precisión, industria aeroespacial, industria de defensa, así como moda, muebles y construcción. Aquí hay siete ejemplos de aplicaciones específicas:
(1) Vestido de celosía estampado 4D
Nervous System, fundada en Estados Unidos en 2007 por Jessica y Jessie, ambas graduadas en el MIT, Jessica licenciada en arquitectura por la misma institución que la profesora Skylar Tibbits, comenzó a utilizar un tejido especial para crear vestidos mediante impresión 4D en 2014. El vestido, como se muestra en la Figura 8-6, consta de una estructura reticular formada por 2279 triángulos y 3316 puntos de articulación, como se ilustra en la Figura 8-7.
La tensión entre los triángulos y las bisagras se ajusta a la forma del cuerpo del usuario, asegurando que el vestido se ajuste bien incluso con cambios de peso. Este vestido no sólo soluciona problemas de ajuste sino que también se adapta a la forma del cuerpo del usuario. El vestido se crea utilizando tecnología de impresión 3D SLS, dejando caer polvo sin sinterizar después de la impresión, lo que da como resultado una estructura de fibras interconectadas.
Nervous System también ha desarrollado una aplicación que permite a los usuarios realizar un escaneo 3D de su cuerpo, elegir el tamaño y la forma de la tela y personalizar un vestido impreso en 4D único. Actualmente, este vestido impreso en 4D está coleccionado permanentemente por cuatro museos o galerías.
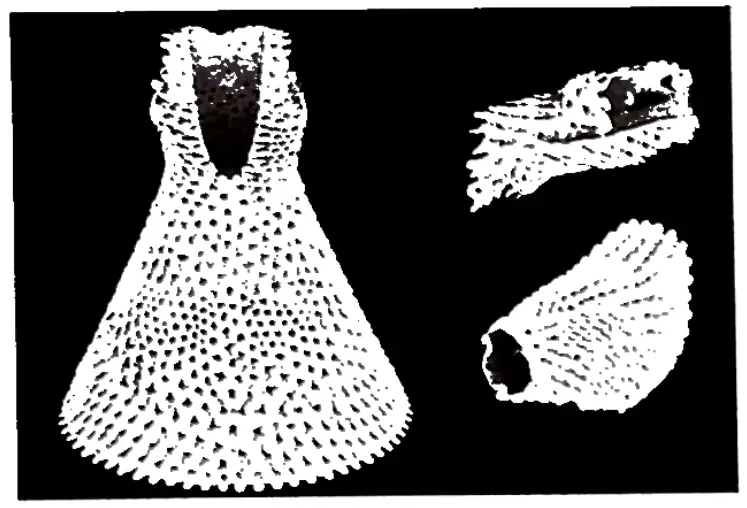
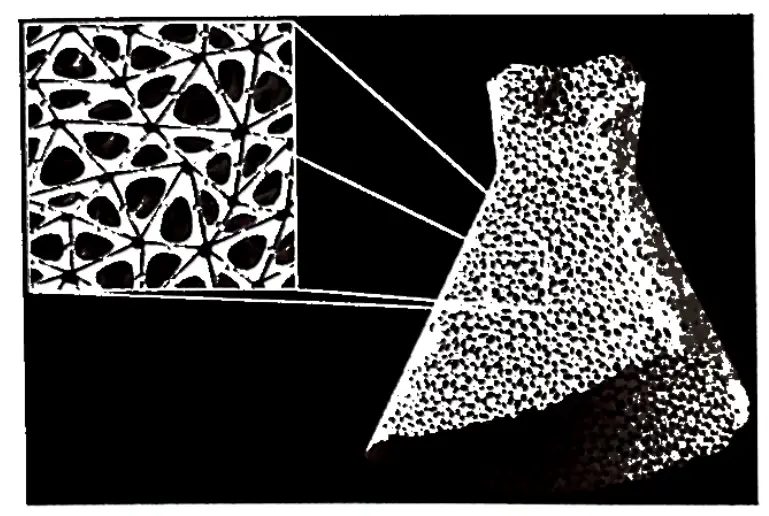
Tela metálica espacial impresa en 4D
En 2017, un equipo de investigación liderado por Raúl Polit Casillas del Laboratorio de Propulsión a Chorro de la NASA informó sobre la creación de una tela metálica plegable utilizando tecnología de impresión 4D, como se muestra en la Figura 8-8. La tela presenta pequeños cuadrados de metal plateado en el frente e hilos de metal negro en la parte posterior, como se muestra en la Figura 8-9.
Esta estructura aumenta significativamente su capacidad para resistir impactos externos y también está convenientemente diseñada para su aplicación en superficies de naves espaciales o trajes espaciales de astronautas. La estructura puede reflejar la luz (lado cuadrado de metal) y absorber calor (lado del alambre metálico), abarcando cinco capacidades: resistencia al impacto físico, capacidad de plegado similar a una tela, resistencia a la tracción similar al acero, refracción de luz intensa y gestión térmica pasiva.
La gestión térmica pasiva permite a la nave mantener un diferencial mínimo de temperatura con el ambiente externo, logrando un equilibrio dinámico cuando se utiliza este material como cubierta.
La NASA prevé que este tejido metálico se utilice en varios ámbitos, incluidas grandes antenas plegables y que cambian de forma, aislamiento térmico para naves espaciales que visiten planetas/lunas fríos y helados, así como esteras aislantes flexibles para astronautas, meteoritos en miniatura para naves espaciales y trajes espaciales.
Además, este material innovador podría usarse en aviones en lunas/planetas de hielo, creando "pies" flexibles que se adaptan a superficies planetarias rugosas, ayudando a prevenir ciertos daños físicos y facilitando la recolección de muestras.
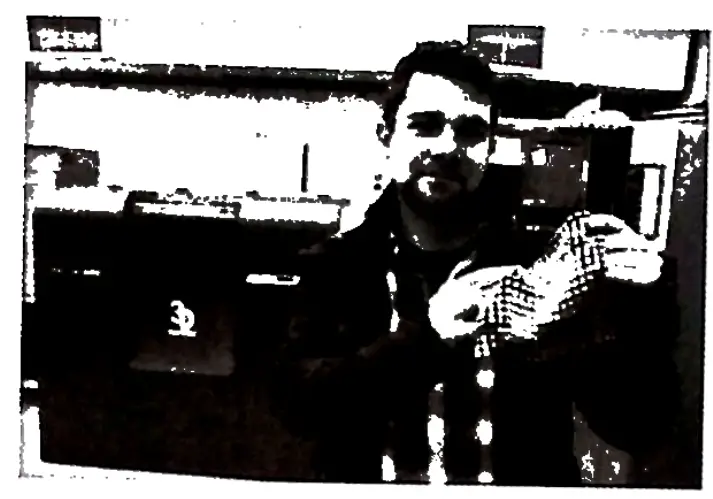
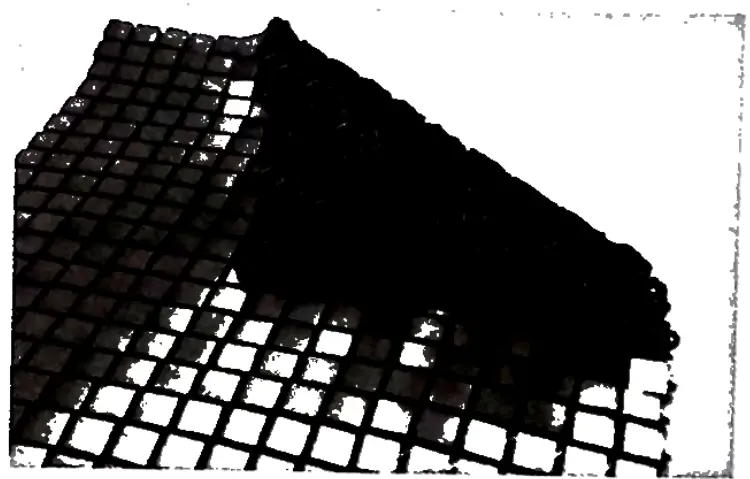
Stent traqueal biodegradable impreso en 4D
El 28 de marzo de 2016, los cirujanos torácicos del Hospital Tangdu, afiliado a la Cuarta Universidad Médica Militar, utilizaron tecnología de impresión 4D de vanguardia para aliviar el sufrimiento de un paciente con traqueomalacia causada por tuberculosis endobronquial traqueal. El segmento traqueal afectado superó la longitud máxima permitida para la resección, por lo que fue imposible su extirpación.
La implantación de un stent tradicional puede provocar complicaciones como dificultad para expectorar. A nivel internacional, la Universidad de Michigan informó un caso similar en The New England Journal of Medicine, donde los expertos desarrollaron una suspensión de stent externo para un paciente con una enfermedad del bronquio izquierdo que abarcaba solo 1-1,5 cm, mientras que este paciente tenía una lesión de 6 cm. la tráquea, lo que representa un desafío mayor.
Después de un análisis cuidadoso de las características de la enfermedad, el Dr. Li Xiaofei, el subdirector Huang Lijun y el Dr. Medical University, crearon un modelo traqueal impreso en 3D.
Después de una evaluación exhaustiva, decidieron proceder con la cirugía de suspensión del stent externo. También se asociaron con el equipo del profesor He Jiankang de la Universidad Xi'an Jiaotong para fabricar un stent traqueal biodegradable impreso en 4D para el paciente, como se muestra en la Figura 8-10.
Utilizando el stent traqueal biodegradable impreso en 4D para envolver la tráquea debilitada y suturarla en su lugar, se sostuvo la tráquea colapsada y se abrieron las vías respiratorias estrechas. Se llevó a cabo una comunicación preoperatoria completa con el paciente y su familia, como se ilustra en la Figura 8-11.
La cirugía fue un éxito y el paciente se recuperó bien después de la operación.
El período de degradación del stent se puede regular controlando el tipo y el peso molecular del biomaterial, permitiendo que se degrade gradualmente y sea absorbido por el cuerpo durante los próximos 2 a 3 años, ahorrándole al paciente el dolor de una segunda cirugía para retirar el stent. stent.
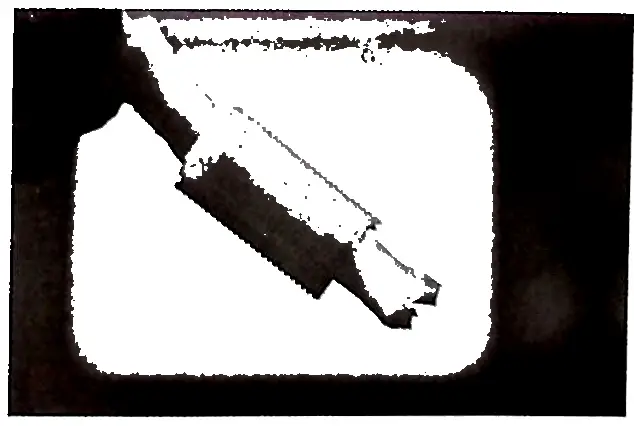
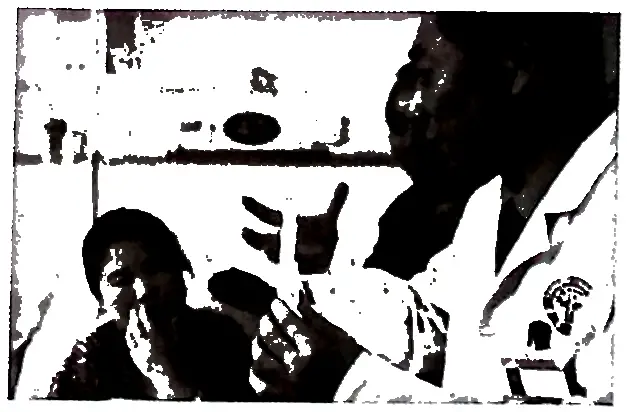
Esta cirugía fue la primera de su tipo a nivel internacional e implicó la suspensión de un stent externo en un segmento blando extremadamente alargado de la tráquea. Además, en septiembre de ese año, médicos del Hospital Xijing de la Cuarta Universidad Médica Militar se unieron al equipo de He Jiankang de la Universidad Xi'an Jiaotong.
Utilizando un stent traqueal absorbible impreso en 4D similar, realizaron una cirugía de suspensión del stent en un niño de 5 meses que padecía una cardiopatía congénita compleja combinada con una estenosis bronquial bilateral grave, curando con éxito la enfermedad: otra primicia mundial.
Oclusores SMP impresos en 4D
En 2019, el profesor Liu Liwu del Instituto de Tecnología de Harbin colaboró con expertos clínicos del Primer Hospital Afiliado de la Universidad Médica de Harbin para incrustar partículas magnéticas de Fe3O4 en una matriz de ácido poliláctico con memoria de forma. Diseñaron e imprimieron en 4D un oclusor SMP biodegradable y personalizable que podría implementarse de forma remota y controlada bajo una intensidad de campo magnético específica.
También realizaron experimentos de viabilidad in vitro con el oclusor SMP impreso en 4D para probar la simplicidad de su proceso de implantación, como se muestra en las Figuras 8-12. El oclusor SMP se puede empaquetar, colocar y liberar fácilmente mediante un catéter; el proceso de implementación se completa en 16 segundos.
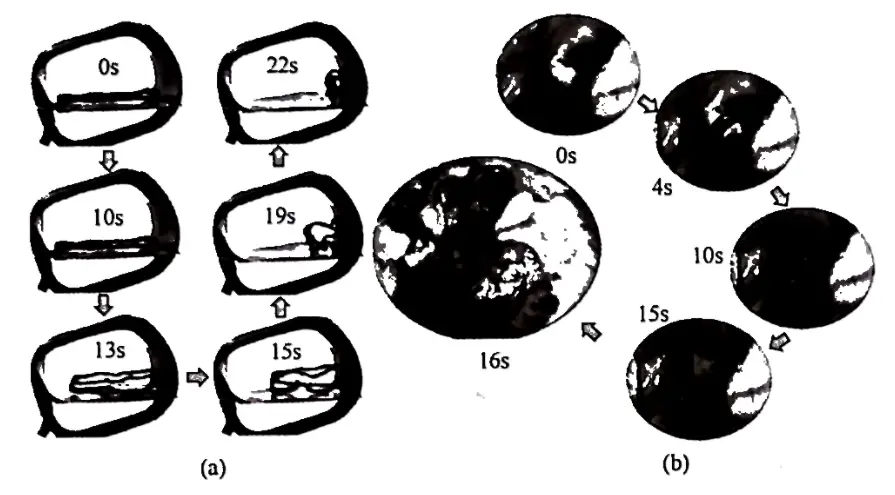
Sistemas robóticos de autoensamblaje impresos en 4D
En la Conferencia Internacional IEEE sobre Robótica y Automatización de 2013, Samuel M. Felton, del Instituto de Ingeniería de Inspiración Biológica de la Escuela de Ingeniería y Ciencias Aplicadas de Harvard, presentó un sistema robótico autoensamblable fabricado con tecnología de impresión 4D.
El campo de la robótica, que exige un alto rendimiento estructural, automatización e inteligencia, ve a menudo efectos sorprendentes cuando se combinan polímeros con memoria de forma, siendo especialmente significativo el sistema robótico de autoensamblaje. Este sistema de autoensamblaje impreso en 4D fusiona materiales planos rígidos con SMP, logrando acciones secuenciales de flexión, control de ángulo y ranurado tras estimulación externa.
Las Figuras 8-13 (a) representan un robot con forma de gusano equipado con un sistema robótico de autoensamblaje impreso en 4D capaz de plegarse en una forma funcional que se mueve bajo una corriente eléctrica adecuada; La figura 8.13(b) muestra el mismo robot con forma de gusano demostrando autopropulsión a una velocidad de 2 µm/s. Estos robots autoensamblables pueden reducir los costos de material, procesamiento y transporte y tienen perspectivas prometedoras para explorar áreas confinadas.
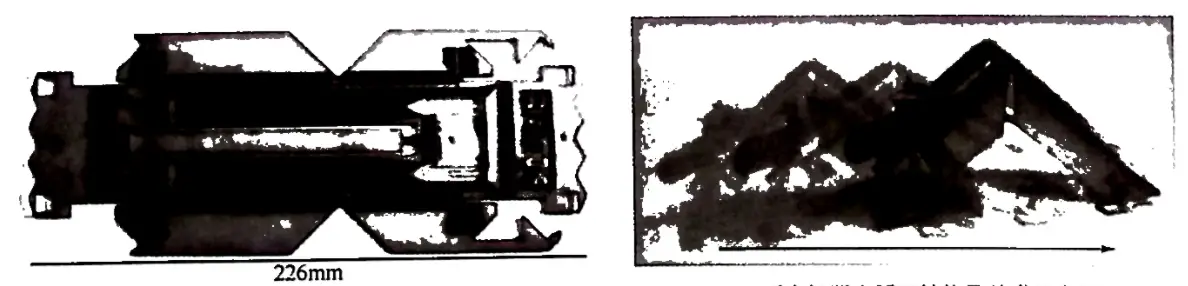
(a) Robot parecido a un gusano con sistema robótico de autoensamblaje impreso en 4D
(b) Estructura desplegada y diagrama de progresión del robot con forma de gusano.
(6) Ropa deportiva sensible a la humedad impresa en 4D
En 2017, el profesor Zhao Xuanhe del Instituto de Tecnología de Massachusetts depositó microbios genéticamente manejables en un material inerte a la humedad mediante un proceso de impresión 3D, creando una película biohíbrida con una estructura multicapa de densidad microbiana desigual. Utilizando los comportamientos higroscópicos y bioluminiscentes de las células vivas, esta película biohíbrida puede responder a los gradientes de humedad ambiental en segundos.
Cambia reversiblemente la forma de la estructura multicapa y la intensidad de la bioluminiscencia, formando aletas de ventilación abiertas en ambientes de alta humedad, como se ilustra en la Figura 8-14. Esta película biohíbrida se transformó en ropa deportiva sensible a la humedad para mejorar la experiencia atlética, como se ilustra en la Figura 8-15.
Dado que la deposición de esta estructura multicapa constituye una producción aditiva de materiales inteligentes sensibles a la humedad, este proceso de impresión 3D también puede denominarse impresión 4D.
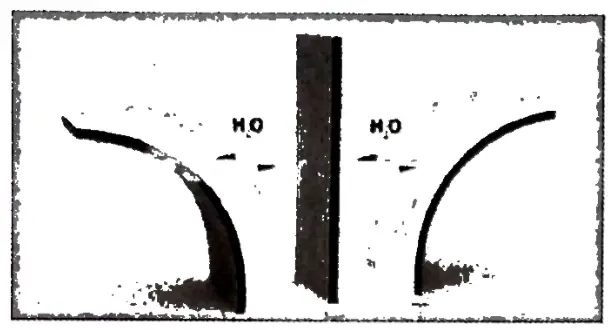
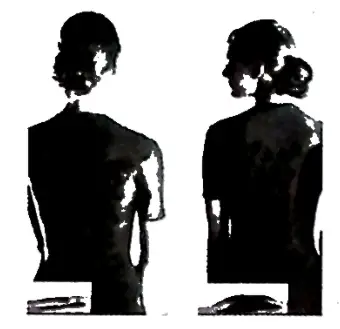
(7) Estructuras autotransformadas de gran módulo y gran deformación
En 2020, el equipo del profesor H. Jerry Qi en el Instituto de Tecnología de Georgia demostró un método para diseñar y fabricar estructuras autotransformables capaces de sufrir grandes deformaciones y un módulo elevado. Imprimieron las estructuras diseñadas utilizando procesos DIW multimaterial con tintas compuestas que consisten en una fracción de alto volumen de solvente, resinas fotopolimerizables, fibras de vidrio cortas y sílice gaseosa.
Durante la impresión, las fibras de vidrio se alinearon mediante una orientación inducida por cizallamiento a través de la boquilla, lo que dio como resultado propiedades mecánicas altamente anisotrópicas. Luego se evaporó el disolvente, provocando una contracción anisotrópica de las fibras de vidrio alineadas en direcciones paralelas y perpendiculares. Un paso de poscurado posterior aumentó aún más la rigidez del material compuesto de aproximadamente 300 MPa a aproximadamente 4,8 GPa.
El proceso de impresión y deformación, ilustrado en la Figura 8-16, se describe arriba. Se desarrolló un modelo de análisis de elementos finitos para predecir los efectos del disolvente, el contenido de fibra y la orientación de la fibra en los cambios de forma.
Los resultados confirmaron que la contracción volumétrica anisotrópica podría actuar como una bisagra activa, permitiendo la autotransformación de estructuras complejas con gran deformación y alto módulo. Estas estructuras muestran aplicaciones potenciales en estructuras livianas con capacidad de carga.
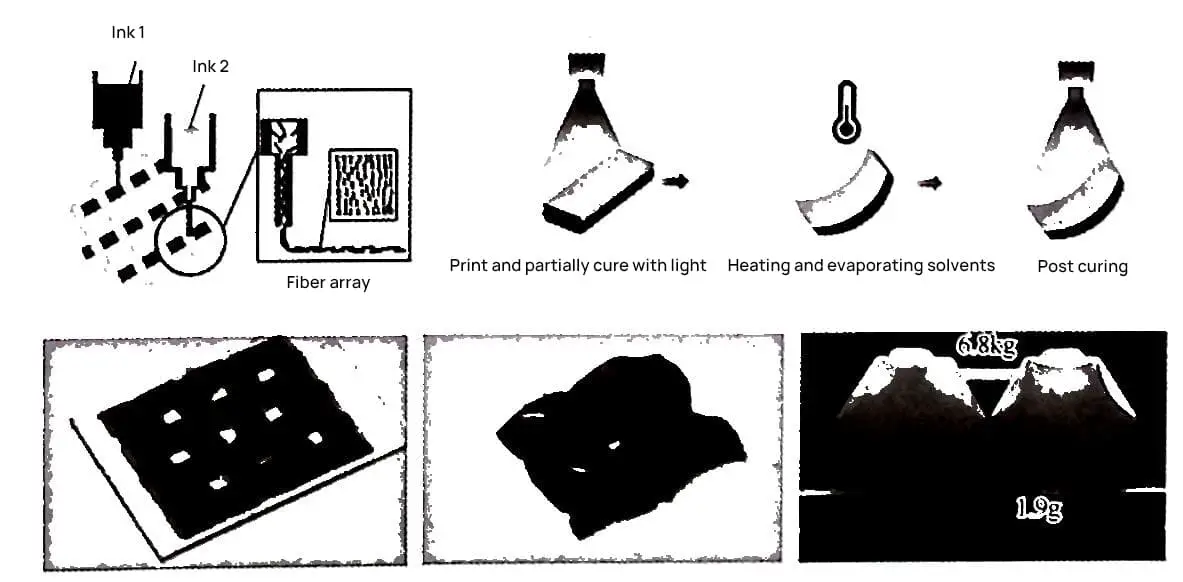