I. Definición
La galvanoplastia es un tipo de proceso de electrodeposición de metales. Implica reducir la descarga de iones metálicos simples o iones complejos mediante métodos electroquímicos sobre la superficie de un sólido (conductor o semiconductor), lo que da como resultado la adhesión de átomos metálicos a la superficie del electrodo para formar una capa metálica.
II. Objetivo
La galvanoplastia altera las propiedades superficiales de los sólidos, alterando así su apariencia, aumentando la resistencia a la corrosión, la resistencia al desgaste y la dureza, y confiriendo propiedades superficiales ópticas, eléctricas, magnéticas y térmicas especiales.
III. Introducción a la galvanoplastia de terminales
La mayoría de los conectores y terminales electrónicos se someten a un tratamiento superficial, típicamente galvanoplastia, por dos razones principales: primero, para proteger el material del resorte del terminal contra la corrosión; en segundo lugar, optimizar el rendimiento de la superficie del terminal estableciendo y manteniendo la interfaz de contacto entre los terminales, especialmente en términos de control de la capa de película. En otras palabras, facilitar el contacto metal con metal.
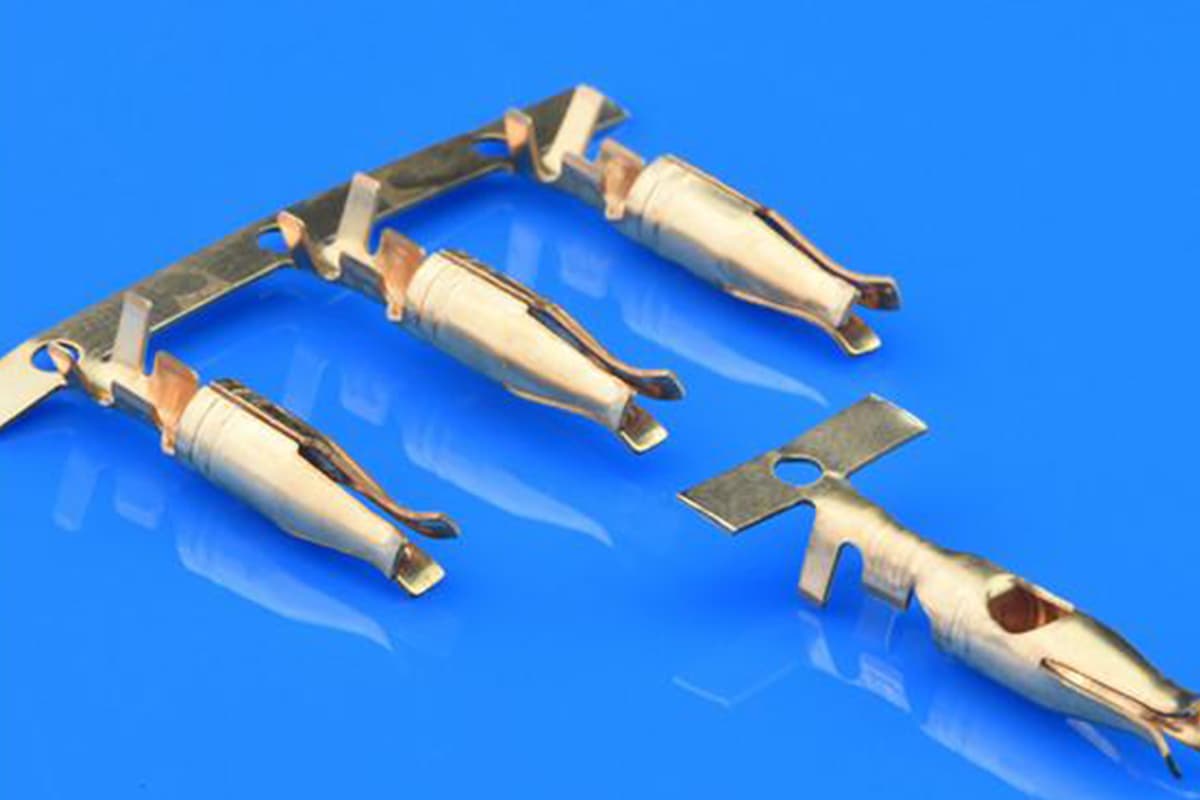
Prevención de la corrosión:
La mayoría de los resortes de los conectores están hechos de aleación de cobre, que puede corroerse en el entorno operativo, como oxidación y sulfuración. La galvanoplastia del terminal aísla el resorte del medio ambiente, evitando la corrosión. Los materiales de galvanoplastia deben ser resistentes a la corrosión, al menos dentro del entorno de aplicación.
Optimización de superficie:
La optimización de las propiedades de la superficie terminal se puede lograr de dos maneras. Uno es mediante el diseño del conector, estableciendo y manteniendo una interfaz de contacto estable. La otra es estableciendo contacto metálico, lo que requiere que cualquier película superficial sea inexistente o se rompa al insertarla. La distinción entre no tener película y romper la película diferencia el revestimiento de metales preciosos del revestimiento de metales no preciosos.
El recubrimiento de metales preciosos, como el oro, el paladio y sus aleaciones, es inerte y no tiene una capa de película inherente. Por tanto, para estos tratamientos superficiales el contacto metálico es “automático”. La consideración entonces pasa a ser cómo mantener la nobleza de la superficie terminal, protegiéndola de factores externos como la contaminación, la difusión del sustrato y la corrosión terminal.
El recubrimiento de los metales no preciosos, particularmente el estaño y el plomo y sus aleaciones, está cubierto por una película de óxido que se rompe fácilmente después de su inserción, estableciendo así una zona de contacto metálico.
(1) Recubrimiento terminal de metales preciosos
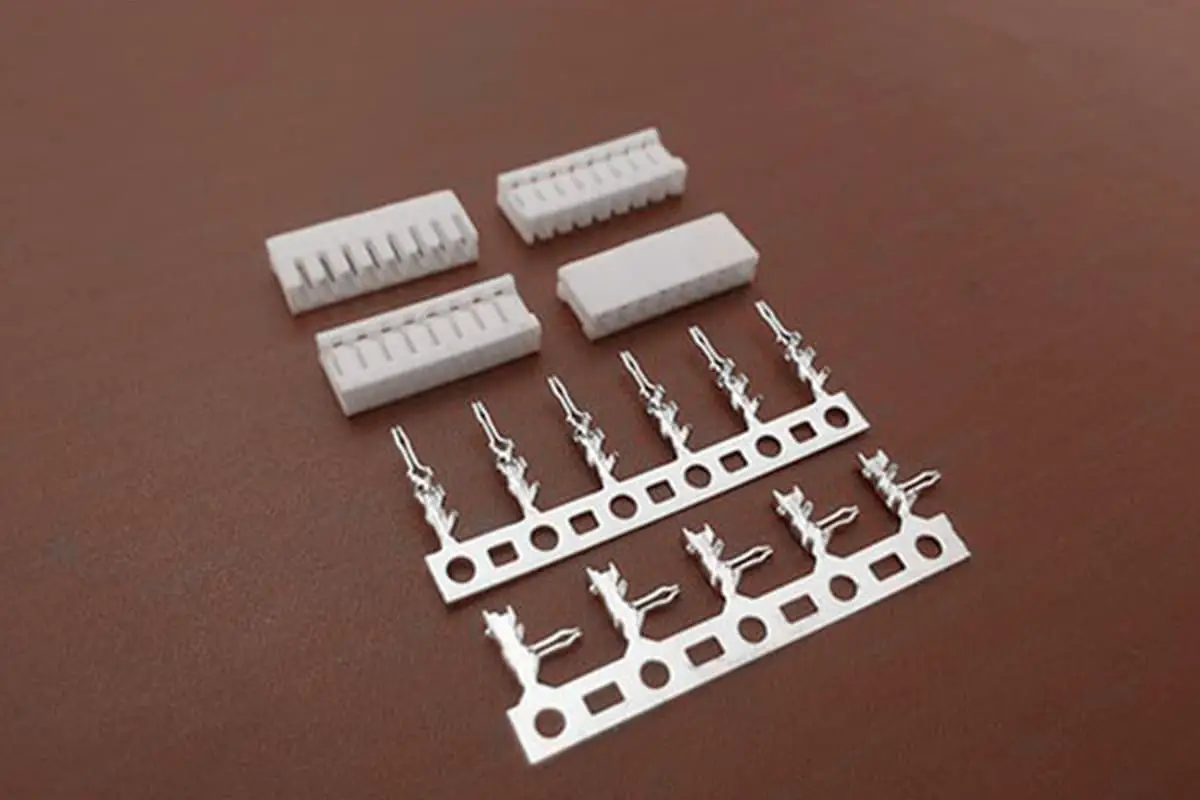
El revestimiento de extremos con metales preciosos implica cubrir la superficie subyacente, normalmente níquel, con un metal precioso. Los espesores de revestimiento de conectores estándar son de 15 a 50 micras para el oro y de 50 a 100 micras para el níquel. Los metales preciosos más utilizados para enchapar son el oro, el paladio y sus aleaciones.
El oro es el material de recubrimiento ideal debido a su excelente conductividad y propiedades térmicas, así como a su resistencia a la corrosión en cualquier entorno. Debido a estas ventajas, el baño de oro se utiliza predominantemente en conectores para aplicaciones que requieren alta confiabilidad, aunque el oro es caro.
El paladio, también un metal precioso, tiene mayor resistencia, menor transferencia de calor y menor resistencia a la corrosión en comparación con el oro, pero ofrece una resistencia superior al desgaste. Las aleaciones de paladio-níquel (proporción 80-20) se utilizan generalmente en terminales de conectores.
Al diseñar un revestimiento de metales preciosos, se deben considerar los siguientes factores:
El. Porosidad
Durante el proceso de galvanoplastia, el oro se nuclea sobre numerosos contaminantes en la superficie expuesta. Estos núcleos continúan creciendo y extendiéndose por la superficie, eventualmente chocan y cubren completamente la superficie, lo que da como resultado una capa porosa.
La porosidad de una capa de oro está relacionada con su espesor. Por debajo de 15 micras, la porosidad aumenta rápidamente, mientras que por encima de 50 micras, la porosidad permanece baja y la tasa de disminución es insignificante. Esto explica por qué el espesor del revestimiento de metal precioso suele estar en el intervalo de 15 a 50 micras.
La porosidad también está relacionada con defectos del sustrato como inclusiones, laminación, marcas de estampado, limpieza inadecuada después del estampado y lubricación incorrecta.
B. Tener puesto
El desgaste de la superficie revestida puede provocar la exposición del material base. El desgaste o longevidad de la superficie recubierta depende de dos características del tratamiento superficial: el coeficiente de fricción y la dureza. A medida que aumenta la dureza y disminuye el coeficiente de fricción, mejora la vida útil del tratamiento superficial.
El oro galvanizado es generalmente oro duro y contiene activadores de endurecimiento como el cobalto (Co), el agente endurecedor más común, que aumenta la resistencia al desgaste del oro. La elección de un revestimiento de paladio y níquel puede mejorar significativamente la resistencia al desgaste y la longevidad del revestimiento de metales preciosos.
Normalmente, se aplica una capa de oro de 3 micras sobre una aleación de paladio-níquel de 20-30 micras, lo que proporciona buena conductividad y alta durabilidad. Además, a menudo se utiliza una capa inferior de níquel para prolongar aún más la vida útil.
w. Capa inferior de níquel
La capa posterior de níquel es una consideración primordial en el revestimiento de metales preciosos, ya que proporciona varias funciones importantes para garantizar la integridad de la interfaz de contacto del terminal.
Al proporcionar una capa de barrera eficaz a través de una superficie oxidada positivamente, el níquel reduce el potencial de corrosión de la porosidad y proporciona una capa de soporte rígida debajo del recubrimiento de metal precioso, aumentando así la vida útil del recubrimiento. ¿Cuál es el espesor adecuado para esta capa?
Cuanto más gruesa es la capa inferior de níquel, menor es el desgaste, pero en términos de coste y control de la rugosidad de la superficie, generalmente se elige un espesor de 50 a 100 micras.
(2) Revestimiento de metales no preciosos
El recubrimiento de metales no preciosos se diferencia del de metales preciosos en que siempre implica un cierto número de capas de película superficial. Para conectores cuyo objetivo es proporcionar y mantener una interfaz de contacto metálica, se debe tener en cuenta la presencia de estas películas.
Normalmente, para recubrimientos de metales no preciosos, se requiere una fuerza de contacto elevada para romper la película, asegurando así la integridad de la interfaz de contacto del terminal. La acción de fregado también es crucial para superficies terminales con capas de película.
Hay tres tipos de tratamientos superficiales distintos del oro en el revestimiento de terminales: estaño (aleación de estaño y plomo), plata y níquel. El estaño es el más utilizado, la plata sobresale en aplicaciones de alta corriente y el níquel se reserva para entornos de alta temperatura.
El. Tratamiento de superficie de estaño
El estaño también se refiere a aleaciones de estaño y plomo, especialmente la aleación 3 de estaño 93 y plomo.
El uso del tratamiento superficial con estaño surge del hecho de que la película de óxido de estaño se rompe fácilmente. Un recubrimiento de estaño tendrá una capa de película de óxido dura, delgada y quebradiza en su superficie. Debajo de la capa de óxido hay estaño blando. Cuando una fuerza positiva actúa sobre la película, el óxido de estaño, al ser delgado, no puede soportar la carga y, debido a su fragilidad, se agrieta con facilidad.
En estas condiciones, la carga se transfiere a la capa de estaño, que, al ser blanda y maleable, fluye fácilmente bajo presión. A medida que el estaño fluye, aumentan las grietas en el óxido. A través de estas grietas y la capa intermedia, el estaño sale a la superficie, proporcionando un contacto metálico. En las aleaciones de estaño y plomo, la función del plomo es reducir la formación de bigotes de estaño.
Los bigotes de estaño se forman como cables monocristalinos en la superficie del estaño chapado bajo tensión, lo que puede provocar cortocircuitos entre terminales. Agregar 2% o más de plomo puede reducir la formación de bigotes. Otra proporción común de aleación de estaño y plomo es 60:40, similar a la proporción de composición de soldadura (63:37), utilizada principalmente en conectores que requieren soldadura.
Sin embargo, la legislación reciente exige cada vez más la reducción del contenido de plomo en productos electrónicos y eléctricos, lo que lleva a un aumento en la demanda de recubrimientos sin plomo como el estaño puro, estaño/cobre y estaño/plata. El crecimiento de los bigotes de estaño se puede frenar recubriendo una capa de níquel entre las capas de cobre y estaño o usando una superficie de estaño opaca y no brillante.
B. Recubrimiento de superficie plateado
La plata se considera un tratamiento de superficie de metales no preciosos porque reacciona con azufre y cloro para formar una película de sulfuro. Esta película de sulfuro actúa como semiconductor y puede presentar características similares a las de un diodo.
La plata también es blanda, comparable al oro blando. Debido a que el sulfuro no se rompe fácilmente, la plata está libre de corrosión por contacto. Con una excelente conductividad eléctrica y térmica, la plata no se funde bajo altas corrientes, lo que la convierte en una excelente opción para tratamientos de superficies de terminales de alta corriente.
(3) Lubricación de terminales
La lubricación cumple diferentes funciones dependiendo del tratamiento superficial del terminal, cumpliendo principalmente dos funciones: reducir el coeficiente de fricción y proporcionar aislamiento ambiental.
Reducir el coeficiente de fricción trae dos beneficios: primero, reduce la fuerza de inserción requerida para los conectores; en segundo lugar, prolonga la vida útil del conector minimizando el desgaste. La lubricación terminal puede formar una capa protectora que previene o retrasa la degradación ambiental de la interfaz de contacto, proporcionando así aislamiento.
Normalmente, para los tratamientos superficiales de metales preciosos, se utiliza lubricación para reducir la fricción y aumentar la longevidad del conector. En el caso de los tratamientos superficiales con estaño, proporciona aislamiento ambiental para evitar la corrosión por contacto. Aunque se pueden aplicar lubricantes en el proceso de postgalvanización, esto es sólo una medida adicional.
Para los conectores que deben soldarse en placas de PCB, el proceso de limpieza de soldadura puede eliminar el lubricante. Los lubricantes atraen polvo que, en un ambiente polvoriento, puede aumentar la resistencia eléctrica y reducir la vida útil. Finalmente, la resistencia a la temperatura de los lubricantes también puede limitar su aplicación.
(4) Resumen de tratamientos de superficie terminal
Se supone que el revestimiento de metal precioso se coloca sobre una base de níquel de 50 micras. El oro es el material más común, cuyo espesor varía según los requisitos de vida útil, pero es susceptible a problemas de porosidad.
El paladio no se recomienda para situaciones que requieran protección de soldabilidad. La plata es sensible al deslustre y la migración y se utiliza principalmente en conectores de alimentación, pero su vida útil se puede mejorar significativamente mediante la lubricación. El estaño tiene una excelente estabilidad ambiental, pero se debe garantizar la estabilidad mecánica.
4. Las diez reglas estrictas del estañado de terminales
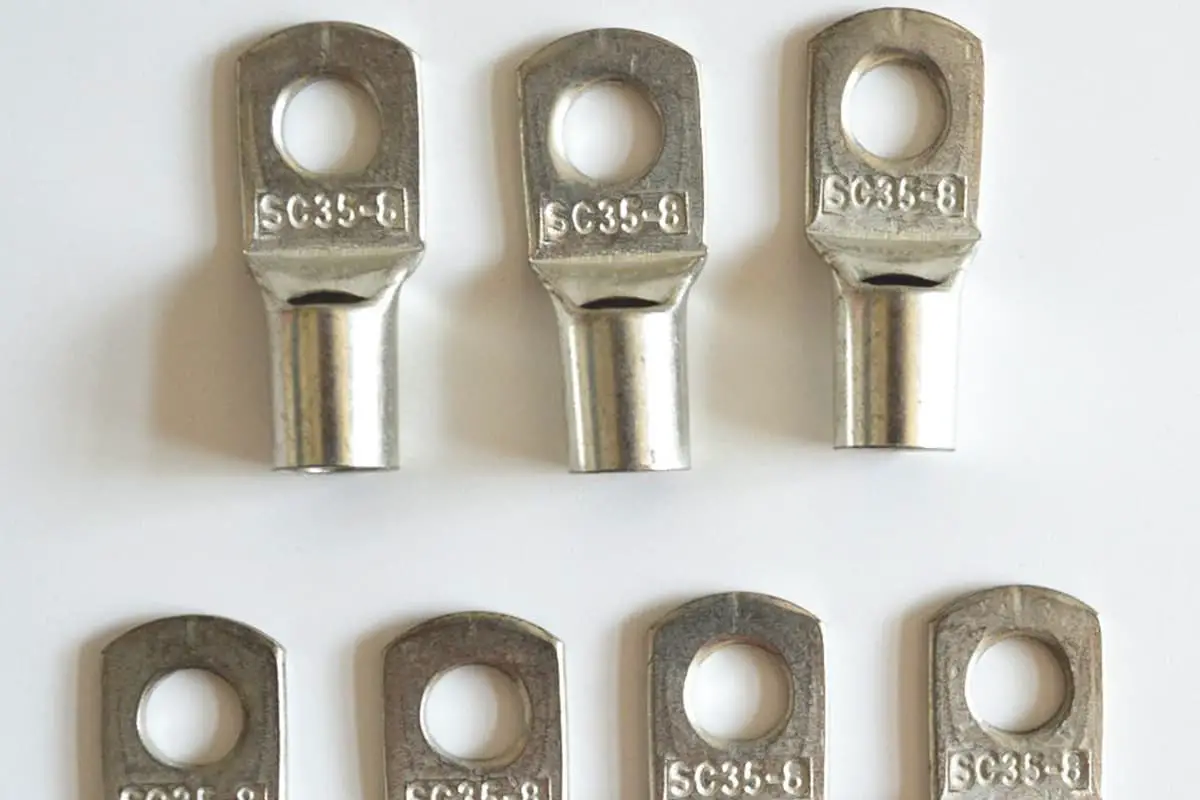
Los materiales de estaño o aleaciones de estaño se encuentran entre las mejores opciones para la galvanoplastia de terminales y ofrecen una solución económica con baja resistencia de contacto y excelente soldabilidad. Estos materiales cumplen con los requisitos de rendimiento de diversas aplicaciones, lo que los convierte en un reemplazo ideal para el oro y otros metales preciosos en el enchapado.
A continuación se presentan diez reglas constantes, aunque a medida que surgen nuevas aplicaciones, quedan más principios por descubrir.
- Cuando utilice materiales estañados, asegúrese de que los terminales macho y hembra mantengan una buena estabilidad mecánica una vez conectados.
Evite el uso de terminales estañados en ambientes vibrantes. La expansión térmica diferencial (DTE) entre los metales de los extremos puede provocar corrosión por fricción dentro de un rango de 10 a 200 micrómetros, dañando el recubrimiento, exponiendo el material base y aumentando significativamente la resistencia de contacto debido a la oxidación.
- Para mantener un contacto estable entre los terminales estañados, aplique una fuerza mínima de 100 gramos en la dirección axial.
- Los terminales estañados requieren lubricación.
Siguiendo la segunda regla, al aumentar la presión axial, se hace necesaria una lubricación adecuada para reducir la fricción. Se deben lubricar los terminales macho y hembra, o al menos un extremo.
- Los materiales estañados no se recomiendan para ambientes continuos de alta temperatura.
Las altas temperaturas aceleran la formación de compuestos intermetálicos entre el cobre y el estaño, lo que da como resultado capas intermedias quebradizas y duras que afectan la funcionalidad. Se recomienda una capa de niquelado como intermedio, ya que los compuestos intermetálicos de níquel-estaño crecen más lentamente.
- Varios procesos de estañado tienen un impacto mínimo en el rendimiento eléctrico.
El revestimiento de estaño brillante es estéticamente agradable; El estaño mate debe mantener una superficie limpia para no afectar la soldabilidad. El estañado de latón debe incluir una capa inferior de níquel para evitar la pérdida de zinc del material base, lo que degradaría la soldabilidad.
- Busque un espesor de estaño de entre 100 y 300 micropulgadas.
Los espesores inferiores a 100 micropulgadas se utilizan normalmente para productos sensibles a los costos con requisitos de soldabilidad más bajos.
- No se recomienda la combinación de terminales estañados y dorados.
Esta práctica conduce a una mayor oxidación y corrosión. El estaño migra a la superficie del oro, provocando eventualmente una acumulación de óxidos de estaño en el sustrato de oro más duro. Es más difícil atravesar el óxido de estaño en el oro que penetrar directamente en la capa de óxido de estaño. Sin embargo, la corrosión por fricción entre el estañado y el plateado es similar a la de los terminales recubiertos con estaño en ambos extremos.
- Es recomendable conectar inicialmente los terminales estañados dos o tres veces.
Este procedimiento elimina la capa de óxido del estañado, lo que garantiza un contacto fiable entre metales. Esto también se recomienda para terminales ZIF (Fuerza de inserción cero).
- Los terminales estañados o de aleación de estaño no son adecuados para aplicaciones con interrupciones frecuentes del circuito.
Debido al bajo punto de fusión del estaño, no es aconsejable utilizar estos materiales en situaciones propensas a la formación de arcos, como puntos de contacto.
- Los terminales estañados se utilizan mejor en circuitos secos y aplicaciones con requisitos moderados.