Introducción
Las conexiones atornilladas y soldadas son las dos formas de ensamblaje más comunes en diversas estructuras mecánicas. Este artículo compara y contrasta principalmente estos dos métodos de conexión predominantes en estructuras de acero, resumiendo sus ventajas y desventajas.
Es necesario conectar entre sí secciones de componentes compuestos de acero, como placas o perfiles de acero. Toda la estructura de acero debe ensamblarse en un todo en los puntos de conexión. Por lo tanto, la calidad y costo-beneficio de una estructura de acero están directamente influenciados por la calidad del diseño de su conexión.
En el pasado, las estructuras de acero se conectaban mediante métodos como pasadores, tornillos, remaches y soldaduras. Sin embargo, las conexiones con pasadores y remaches ya no se utilizan en estructuras de acero nuevas, por lo que estos métodos no se analizarán más a fondo.
I. Conexiones soldadas
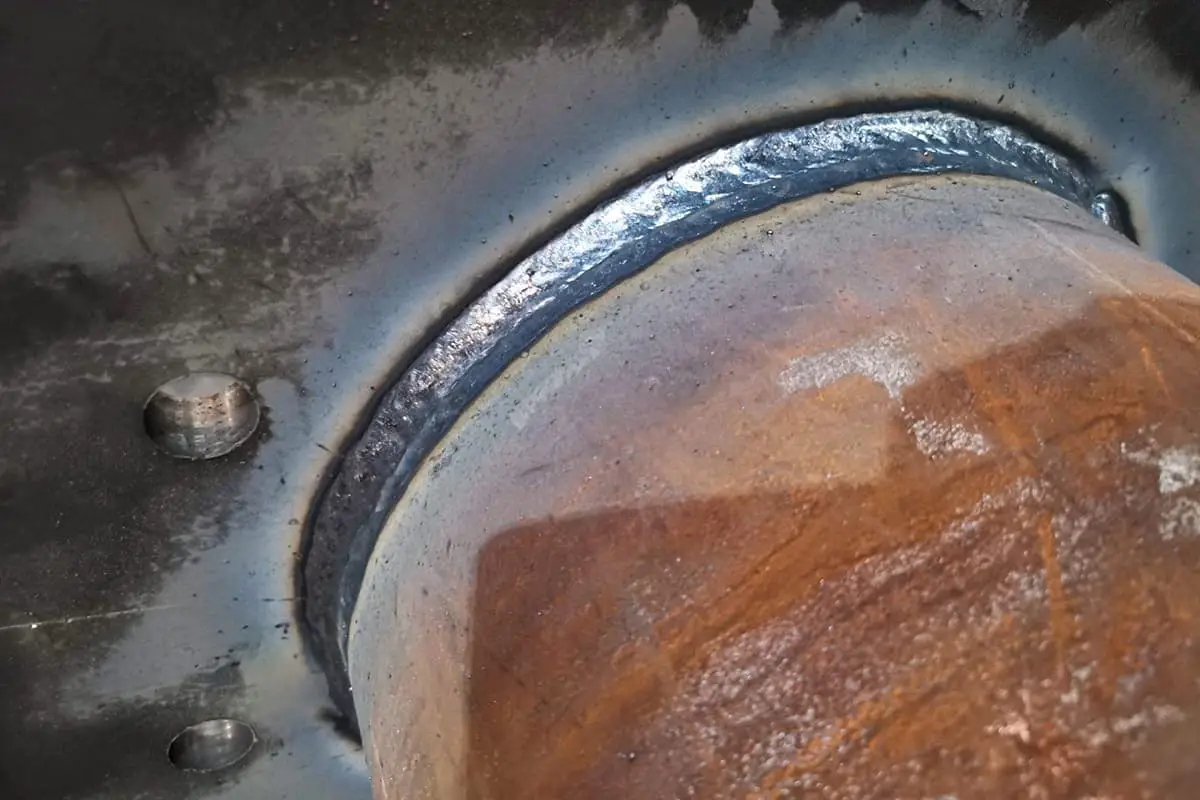
Las conexiones soldadas se forman fusionando la varilla de soldadura y las piezas a soldar con el calor generado por un arco eléctrico. Después del enfriamiento, estas piezas fundidas se solidifican formando un cordón de soldadura, integrando así las piezas en una sola unidad.
Las conexiones soldadas son el método principal para conectar las estructuras de acero actuales, siendo la soldadura por arco manual y la soldadura por arco sumergido automática (o semiautomática) los métodos de soldadura más utilizados.
Beneficios
En comparación con las uniones atornilladas, las estructuras soldadas tienen varias ventajas:
(1) Las conexiones soldadas no requieren perforación, por lo que no se debilita la sección transversal. Tampoco se necesitan componentes de conexión adicionales, lo que simplifica la construcción. Como resultado, las conexiones soldadas pueden ahorrar mano de obra y materiales, generando beneficios económicos. Estas pueden considerarse sus ventajas más significativas.
(2) Las estructuras soldadas ofrecen un buen sellado, alta rigidez y excelente integridad. Además, algunas uniones, como las conexiones en forma de Y y T entre tubos de acero, son difíciles de lograr con conexiones atornilladas u otros métodos, lo que hace que la soldadura sea la opción preferible.
Desventajas
Las uniones soldadas tienen las siguientes deficiencias:
(1) Se ven afectados por las altas temperaturas durante el proceso de soldadura;
(2) Las costuras de soldadura a menudo contienen varios defectos y el metal base cerca de la costura de soldadura puede volverse quebradizo, lo que puede provocar concentración de tensiones y aumento de grietas en la estructura;
(3) Debido a la rigidez de la estructura soldada, las grietas localizadas pueden extenderse fácilmente a toda la estructura. Como se mencionó anteriormente, las estructuras soldadas son propensas a volverse quebradizas a bajas temperaturas;
(4) Después de la soldadura, la contracción desigual inducida por el enfriamiento puede provocar tensiones residuales de soldadura dentro de la estructura. Esto puede causar que algunas secciones entren prematuramente en plasticidad cuando se cargan, reduciendo la estabilidad crítica de las tensiones cuando se comprimen;
(5) Después de soldar, la expansión y contracción desiguales pueden causar deformación residual de la soldadura, como causar deformación en una placa de acero plana.
Dadas estas limitaciones de las uniones soldadas, se deben tomar medidas para evitar o reducir su impacto negativo durante el diseño, fabricación e instalación.
Simultáneamente, la calidad de las soldaduras debe ser inspeccionada y aceptada de acuerdo con la norma nacional “Especificación de aceptación de calidad para ingeniería de estructuras de acero”.
Prestar atención a la selección del material, el diseño del cordón de soldadura, el proceso de soldadura, la técnica del soldador y una inspección mejorada del cordón de soldadura puede evitar que se produzcan fallas en el cordón de soldadura frágil.
II. Conexiones atornilladas
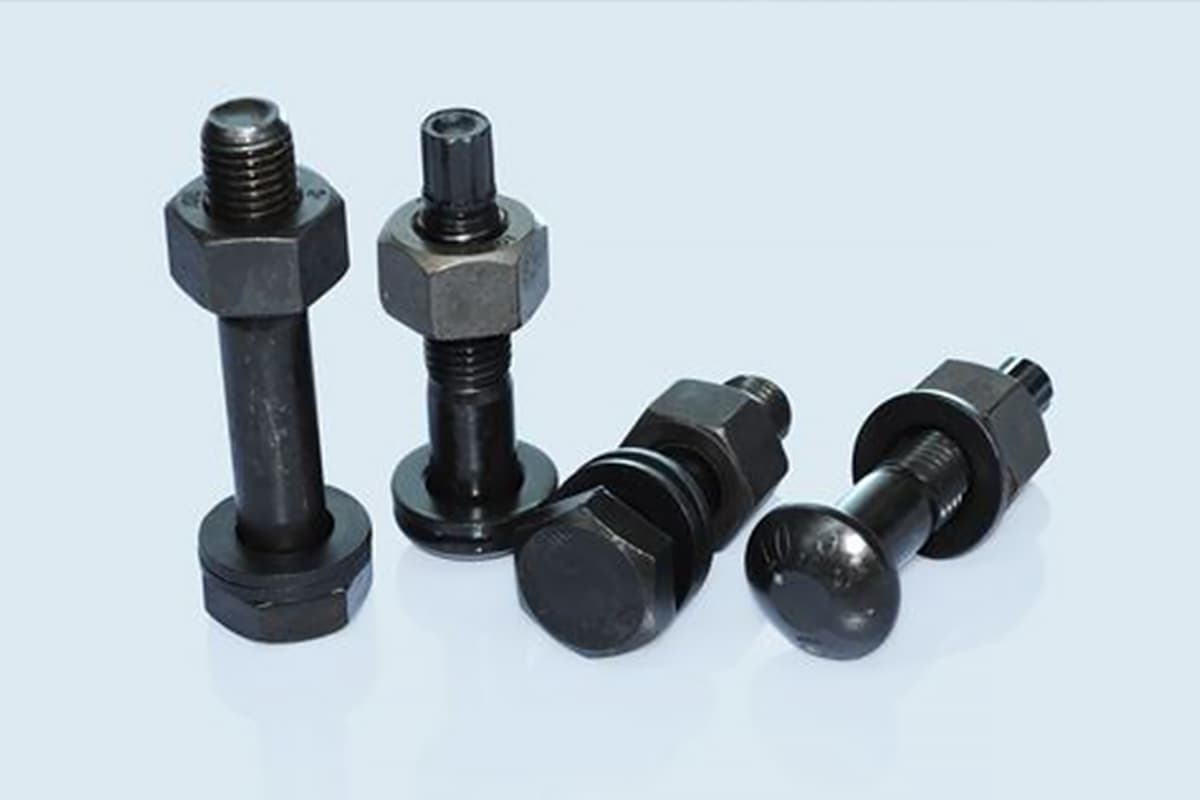
Las conexiones atornilladas unifican componentes mediante el uso de tornillos, un tipo de sujetador. Hay dos tipos de conexiones atornilladas: conexiones atornilladas estándar y conexiones atornilladas de alta resistencia.
1. Tipos de tornillos
Los pernos utilizados en las conexiones de estructuras de acero se clasifican como pernos estándar y pernos de alta resistencia. Los tornillos estándar suelen tener cabezas hexagonales y se clasifican como A, B y C.
Los pernos de grado C generalmente se pueden fabricar con acero Q235, formado a partir de acero redondo laminado en caliente. Se trata de tornillos gruesos, con requisitos relativamente bajos para la fabricación de orificios para tornillos, por lo que se utilizan ampliamente en conexiones de tornillos estándar.
Los tornillos estándar de grado A y B son tornillos de precisión que requieren estándares de fabricación más altos tanto para el tornillo como para el orificio del tornillo. La instalación de pernos estándar generalmente implica llaves manuales, sin un requisito específico de pretensar el perno.
Los tornillos de alta resistencia utilizados en estructuras de acero tienen un significado específico. Se instalan con una llave especialmente diseñada, lo que garantiza una pretensión preestablecida en el tornillo y, por lo tanto, una prepresión específica en la superficie de contacto de las placas conectadas.
Para alcanzar el valor de pretensión requerido, estos tornillos deben estar fabricados con acero de alta resistencia.
Aunque los tornillos estándar de Clase A y B también están hechos de acero de alta resistencia, todavía se les llama tornillos estándar.
Los grados de rendimiento de tornillos de alta resistencia incluyen 8,8 y 10,9. Los tornillos de alta resistencia están hechos de materiales como acero con contenido medio de carbono o acero aleado, que se tratan térmicamente (templados y revenidos) para mayor resistencia.
La resistencia a la tracción (fub) de los tornillos de alta resistencia de grado 8.8 no es inferior a 800 N/mm2, con un índice de límite elástico de 0,8. La resistencia a la tracción de los tornillos de alta resistencia de grado 10,9 no es inferior a 1000 N/mm2, con un índice de límite elástico de 0,9.
2. Tipos de conexiones atornilladas
Las conexiones atornilladas se prefieren por su eficiencia en tiempo y mano de obra, la simplicidad del equipo de instalación requerido y los requisitos de habilidades menos exigentes para los trabajadores de la construcción en comparación con los soldadores.
Ocupan el segundo lugar después de las conexiones soldadas en uso en conexiones de marcos de acero. Las conexiones atornilladas se dividen en conexiones atornilladas estándar y conexiones atornilladas de alta resistencia.
Dependiendo de la situación de tensión, cada uno de ellos se divide en tres tipos: conexiones atornilladas resistentes al corte, conexiones atornilladas resistentes a la tracción y conexiones atornilladas que resisten simultáneamente el corte y la tensión.
Los tornillos de rosca gruesa (tornillos de grado C) se utilizan comúnmente en conexiones atornilladas estándar. Su resistencia al corte depende de la resistencia al corte del eje del tornillo y de la resistencia a la compresión de la pared del orificio.
La resistencia a la tracción depende de la resistencia a la tracción axial del perno. Las conexiones atornilladas de rosca gruesa, que generalmente solo se usan en componentes secundarios que no soportan directamente cargas dinámicas, como soportes, tiras de fricción, montantes de pared, pequeñas armaduras y estructuras removibles, resisten las fuerzas de corte.
Por otro lado, debido a la resistencia superior a la tracción del perno, se usa comúnmente en conexiones de nudos en sitios de construcción que colocan el perno bajo tensión.
En términos de conexiones atornilladas convencionales, se utilizan pernos de rosca fina (pernos de grado A y B) debido a su alta calidad para conexiones de alta resistencia al corte.
Sin embargo, debido a que la fabricación de tornillos es compleja, los requisitos de instalación son altos (el diámetro del orificio y el diámetro del eje del tornillo son casi idénticos) y el precio es caro, a menudo se reemplazan por conexiones de fricción de tornillos de alta resistencia, que serán más resistentes. se discutirá más adelante.
Las conexiones tipo cojinete de perno de alta resistencia tienen los mismos requisitos de instalación de construcción, material de perno y precarga que las conexiones de tipo fricción.
La diferencia es que su capacidad de carga máxima se basa en superar la fricción, donde las placas conectadas se deslizan entre sí y el perno falla debido al corte y la compresión de la pared del orificio.
Por tanto, su capacidad de carga es mayor que la de las conexiones por fricción con tornillos de alta resistencia, ahorrando materiales de conexión. Sin embargo, este tipo de conexión tiene una aplicación limitada debido a la deformación por deslizamiento que se produce tras superar la fricción.
Está especificado para su uso únicamente en estructuras que soportan cargas estáticas o soportan indirectamente cargas dinámicas. Los requisitos de tratamiento superficial para las superficies de contacto de los componentes conectados son menores que para las conexiones de fricción, y solo requieren la eliminación del aceite y el óxido flotante.
El rendimiento de las conexiones tipo cojinete es idéntico al de los pernos estándar, pero debido a la precarga en el eje del perno y la aplicación de acero de alta resistencia, el rendimiento excede el de las conexiones atornilladas estándar.
3. Ventajas y desventajas de las conexiones atornilladas.
Ventajas de las conexiones atornilladas: Ofrecen un proceso de construcción sencillo y una fácil instalación, lo que las hace especialmente adecuadas para el montaje en obra.
También son convenientes para el desmontaje, lo que los hace ideales para estructuras que necesitan ser ensambladas y desensambladas, así como para conexiones temporales.
Desventajas de las conexiones atornilladas: Requieren agujeros en las placas y emparejados durante el montaje, lo que aumenta la carga de trabajo de fabricación. Además, se requiere una mayor precisión en la fabricación.
Los orificios para pernos también debilitan la sección de los componentes, y las piezas conectadas a menudo necesitan superponerse o requieren placas de conexión auxiliares adicionales (o ángulos de acero), lo que hace que la estructura sea más compleja y aumenta el consumo de acero.