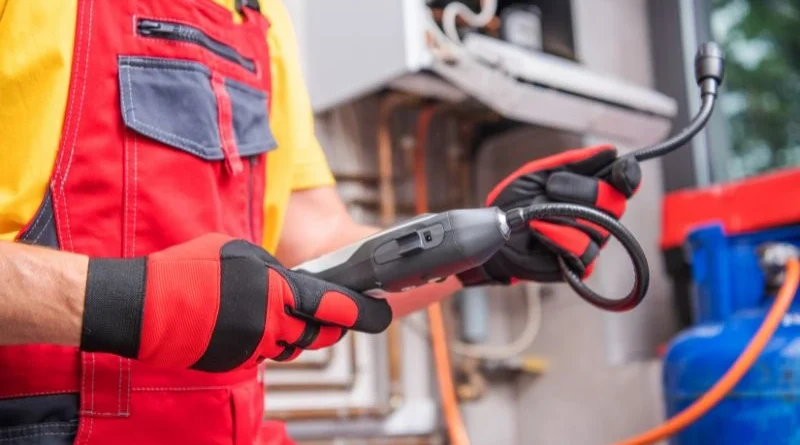
In the world of temperature measurement and control, accuracy is key. Whether you are monitoring the temperature of industrial processes, ensuring food safety in a commercial kitchen, or performing measurements in a scientific laboratory, you need a reliable and accurate method for measuring temperature. The Resistance Temperature Detector (RTD) is a proven technology. In this article, we'll delve into the details of RTDs and examine how they work, their benefits, and their common applications.
What is a Resistance Temperature Detector (RTD)?
A resistance temperature detector (RTD) is a sophisticated temperature sensor that uses the change in electrical resistance of a pure platinum element to accurately measure temperature. This technology offers exceptional precision and stability, making it the ideal choice for applications where temperature control is critical. Understanding how RTDs work is fundamental to realizing their potential in various sectors, from industrial processes to scientific research.
The basic
A resistance temperature detector (RTD) is a type of temperature sensor that measures temperature by correlating the resistance of the RTD element with the temperature. RTDs consist of a coil of wire or an applied film of pure platinum that exhibits a predictable change in electrical resistance as temperature changes. The platinum element is often wound into a thin wire and encapsulated in a protective casing.
Working principle
The fundamental principle behind RTDs is the relationship between electrical resistance and temperature. As the temperature increases, the electrical resistance of the platinum element also increases in a highly linear and repeatable manner. This relationship is described by the Callendar-Van Dusen equation, which allows accurate temperature calculations based on resistance measurements.
Advantages of RTDs
RTDs offer several advantages that make them the preferred choice for many temperature measurement applications:
precision
One of the biggest advantages of RTDs is their accuracy. They can provide highly accurate and repeatable temperature measurements over a wide temperature range. With their linear resistance-temperature relationship, RTDs offer greater accuracy than many other temperature sensors.
stability
RTDs are known for their long-term stability. They can maintain accuracy and performance over long periods of time, making them suitable for critical applications where consistency and reliability are essential.
Wide temperature range
RTDs can operate over a wide temperature range from -200°C to 850°C and even higher for special designs. This versatility makes them suitable for a variety of industries, from cryogenic applications to high-temperature processes.
Interchangeability
Thanks to standardized calibration methods and the Callendar-Van Dusen equation, RTDs are highly interchangeable. This interchangeability simplifies maintenance and reduces the need for labor-intensive recalibrations.
Low self-heating
RTDs have minimal self-heating effects, meaning they do not significantly affect the temperature they measure. This property is particularly important in applications where self-heating can cause errors.
Common Applications of RTDs
Due to their accuracy and stability, RTDs find application in various sectors. Some common uses include:
Industrial process control
In the petrochemical, pharmaceutical and food processing industries, precise temperature control is critical. RTDs monitor and control temperature in various processes, ensuring product quality and safety.
HVAC Systems
Heating, ventilation, and air conditioning (HVAC) systems rely on temperature measurements for effective climate control. RTDs monitor and maintain optimal conditions in residential, commercial and industrial buildings.
Laboratory and scientific research
Scientific laboratories need accurate temperature measurements for experiments and research. RTDs are popular in this environment due to their high accuracy and reliability.
Automotive and aviation industries
RTDs are used in the automotive and aerospace industries to monitor and control temperatures in engines, exhaust systems, and critical components. Its accuracy is essential to guarantee the safety and performance of these systems.
Choosing the Right RTD for Your Application
When considering RTDs in your temperature measurement system, it is important to select the correct type of RTD for your specific application. Here are some factors you should consider:
Temperature range
Different RTDs are designed to operate in specific temperature ranges. Make sure the RTD you choose can withstand the temperatures expected in your application. Some special RTDs can withstand extreme temperatures, like those used in the aerospace industry.
Environmental conditions
Consider the environmental conditions your RTDs will be exposed to. If your application will be exposed to chemicals, moisture, or other potentially corrosive elements, choose an RTD with an appropriate protective cover or housing material.
Accuracy Requirements
The level of accuracy required for your temperature measurements is a crucial factor. RTDs offer high accuracy, but there are differences in accuracy between different models and brands. Make sure the RTD you choose meets the accuracy requirements of your application.
Calibration and maintenance
RTDs need to be calibrated regularly to maintain their accuracy. Consider ease of calibration and availability of calibration services for your chosen RTD model. Regular maintenance is essential to ensure consistent performance.
reaction time
The response time of an RTD can vary depending on the project. Some applications require rapid response to temperature changes, while others can tolerate slower response times. Be sure to evaluate your application's response time requirements.
Installation and maintenance of RTDs
For optimal performance and longevity of RTDs, proper installation and maintenance are essential:
installation
- Make sure the RTD is installed correctly and that the sensing element is in direct contact with the medium whose temperature you want to measure.
- Use appropriate connectors and cables to avoid interference or signal loss.
- Secure the protective cap to prevent damage to the RTD element.
maintenance
- Calibrate RTDs regularly according to your application requirements and industry standards.
- Inspect the RTD for any physical damage or wear to the jacket and replace if necessary.
- Keep connectors clean and free from corrosion or contaminants that affect accuracy.
Conclusion
In summary, resistance temperature detectors (RTDs) are reliable, high-precision temperature sensors that are widely used in various industries. Their accuracy, stability and suitability over a wide temperature range make them an excellent choice for applications where temperature control and measurement are critical. Understanding how RTDs work and the benefits they provide will help you make informed decisions about implementing them in your temperature monitoring systems.
Common questions
1. Are RTDs more accurate than thermocouples?
RTDs are generally considered to be more accurate than thermocouples. While thermocouples have advantages such as a wider temperature range, RTDs offer greater accuracy and better long-term stability. They are the preferred choice when accuracy is of utmost importance.
2. Can RTDs be used in harsh environments?
RTDs can be used in harsh environments as long as they are adequately protected. The protective cover or housing around the RTD element can be selected to resist corrosive chemicals, high temperatures, or other demanding conditions. This adaptability makes RTDs versatile for various industrial applications.
3. How often should RTDs be calibrated?
The frequency of RTD calibration depends on the specific application and industry standards. In many cases, RTDs are calibrated annually. However, critical applications may require more frequent calibrations to ensure accuracy and regulatory compliance.