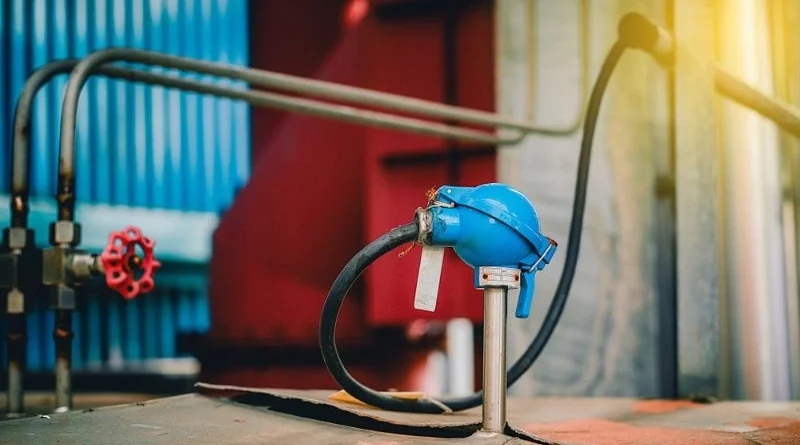
Resistance temperature detectors (RTDs) are incredibly accurate and stable solutions for temperature measurement. They are continually transforming industries, from food processing to aerospace. Have you ever wondered how this innovation works? Dive with us into the complex but fascinating world of RTDs! Let's find out how they work, explore why they've become a mainstay of temperature measurement, and explore how they can revolutionize your operations. Be prepared to redefine what you know about thermodynamics as we demystify how RTDs work.
The operating principle of an RTD is based on the property of electrical resistance, which changes with temperature. RTDs use metals such as platinum, copper or nickel, whose resistance increases or decreases as the temperature decreases. This change in resistance is measured and used to accurately determine temperature. MyTech-Info has an article that explains in detail the working principle of RTDs and contains information on various configurations and signal conversion methods.
Understanding RTD Technology
One of the most commonly used technologies for accurate temperature measurement is the resistive temperature detector (RTD). To understand how it works, we need to understand its underlying principles. Basically, an RTD is based on the assumption that the electrical resistance of metals changes with temperature. This principle is based on the fact that as the temperature increases, the electrical resistance of certain metals such as platinum, copper and nickel also increases. Likewise, its resistance decreases as the temperature decreases.
Resistive temperature detectors can provide reliable, high-precision temperature measurements in a variety of applications. They are often used in industrial processes where precision is critical, such as: B. in factories, refineries and scientific laboratories. By understanding how RTDs work, we can see their importance in different industries.
Platinum, copper and nickel in RTDs
Among the metals used in RTDs, platinum is popular due to its excellent stability and linear response to temperature changes. It exhibits minimal drift over time and provides high accuracy over a wide temperature range. These desirable properties make platinum RTDs suitable for demanding applications where accuracy is of utmost importance.
Copper and nickel are also used in RTDs, but are less common than platinum. Copper has a wider temperature range than platinum, but can be susceptible to corrosion in harsh environments. Nickel, on the other hand, offers economical alternatives for lower temperature applications, but can result in greater measurement errors.
Each metal contributes its unique properties to the performance of an RTD sensor. The choice of material depends on factors such as cost considerations, desired temperature range, stability requirements, and environmental conditions of the application.
For example, a platinum-based RTD would be best suited for an industrial environment with extreme temperatures or corrosive materials due to its robustness and accuracy. In contrast, a copper or nickel RTD could be chosen for less critical applications where cost efficiency is prioritized over maximum accuracy.
Understanding the advantages and limitations of these metals in RTDs is critical to selecting the right sensor for specific temperature measurement needs. It is always recommended to consult experts or consult manufacturers' technical specifications to make informed decisions.
Common RTD Settings
When it comes to RTDs, there are a few commonly used configurations that meet different temperature measurement needs. The most popular include 2-wire, 3-wire, and 4-wire configurations.
In the 2-wire configuration, the RTD is connected in series with the meter, resulting in inaccuracy due to conductor resistance. This configuration is typically used for short distance applications where high accuracy is not critical.
The 3-wire configuration solves the problem of line resistance by introducing an additional wire that compensates for it. This configuration offers greater accuracy and is widely used in various industrial applications.
The 4-wire configuration further improves accuracy by using two additional conductors, creating a true bridge circuit that eliminates the effects of conductor resistance on the measurement. Consequently, this configuration offers the highest level of accuracy and is often used in demanding and precise temperature measurements.
The appropriate RTD configuration depends on the required accuracy, application limitations, and cost. Understanding these common configurations allows you to make informed decisions when configuring temperature measurement systems.
- According to the Institute of Electrical and Electronics Engineers, platinum-based RTDs can achieve an accuracy of up to 0.1°C.
- According to the American Society for Testing and Materials, the 3-wire configuration is the most commonly used RTD configuration in industrial environments, accounting for approximately 60% of RTD applications.
- According to a report by Allied Market Research, the global RTD market was valued at around $1.4 billion in 2020, with an estimated CAGR of 6.2% from 2021 to 2028, indicating its widespread use in temperature measurement processes around the world.
IDT working principle
To understand how an IDT works, we need to examine its working principle. RTDs work based on the fundamental concept that electrical resistance changes with temperature fluctuations. In other words, as the temperature increases, the resistance of certain metals used in RTD sensors, such as platinum, copper or nickel, also increases.
This relationship between temperature and resistance can be described mathematically using a basic equation known as the Callendar-Van Dusen equation: RT = Rref (1 + α (T – Tref)) . Here, TR represents the resistance at a given temperature ( T ), reference denotes the reference resistance at a reference temperature ( meeting ), and α denotes the temperature coefficient of resistance.
However, it is important to note that discrepancies may occur when comparing calculated resistance to RTD tables. The nonlinear characteristics of RTDs and variations in manufacturing processes can contribute to these variations, especially at Fahrenheit temperatures.
Although the Callendar-Van Dusen equation provides a useful temperature estimate based on resistance, it does not always result in an exact match. Therefore, the use of RTD tables or calibration devices is recommended for accurate temperature measurements.
For example, imagine an industrial process where temperature needs to be monitored within strict tolerances. An accurate understanding of the interaction between resistance and temperature is crucial in this context. By utilizing RTDs and the above principles, operators can ensure that sensitive processes function optimally.
Interaction between resistance and temperature
Understanding the interaction between resistance and temperature is critical to understanding how RTDs work. As mentioned earlier, RTDs are based on the fact that the electrical resistance of metals changes with temperature. More specifically, the resistance of metals increases as the temperature increases and decreases as the temperature decreases. This relationship is described by a mathematical equation, the Callendar-Van Dusen equation or a simplified version, the Alpha equation.
A commonly used material in RTD sensors is platinum because it has a stable and predictable resistance-temperature relationship. However, it is important to note that the change in resistance is not linear and can vary depending on the diffusion of impurities and gloss factors. Additionally, different manufacturers may use platinum of different purity, resulting in different alpha coefficients. Therefore, discrepancies may occur when comparing RTD measurements to standard tables or when using specific equations.
Consider this scenario : You have a platinum RTD sensor and you measure its resistance at two different temperatures with a multimeter. According to the alpha equation, a certain change in resistance is expected based on the temperature difference between these two points. However, when you compare your measurements to an RTD table, they don't agree perfectly. This discrepancy can be attributed to several factors, including uncertainties in manufacturing processes and variables that affect metal properties.
It's also worth mentioning that most industrial applications use three-wire configurations for their RTDs because they can minimize the effects of line resistance. The Wheatstone bridge circuit is critical for converting these resistance changes into measurable voltage or current signals. Temperature transmitters or devices such as PLC modules, DCS or PID controllers are generally used to process these signals and provide meaningful temperature values.
Practical RTD Circuit Design
When designing practical circuits for RTDs, considerations must be made to ensure accurate temperature measurement. The choice of RTD configuration, whether two-wire, three-wire, or four-wire, depends on the specific application requirements. Three-wire configurations are often preferred in industrial settings because they compensate for the effects of line resistance.
The Wheatstone bridge circuit is used to accurately measure a change in resistance. This bridge arrangement allows small changes in resistance to be detected by balancing an excitation voltage across the bridge legs. The voltage difference between certain points indicates the extent of the change in resistance and therefore the corresponding temperature.
Implementing an appropriate excitation voltage source, accurate bridge resistance values, and careful wiring techniques are essential factors contributing to reliable and stable measurements. Additionally, shielding may be necessary to minimize noise and interference that compromise signal integrity.
Now that we have developed an understanding of the interplay between resistance and temperature and examined practical circuit design considerations for RTDs, we can delve deeper into another crucial aspect: the role of the Wheatstone bridge circuit in enabling accurate temperature measurements.
Role of the Wheatstone Bridge
To understand how RTDs work, it is important to understand the role of a key component called the Wheatstone bridge. The Wheatstone bridge is a special electrical circuit that plays an important role in converting changes in the resistance of an RTD sensor into a measurable voltage or current. By using two sets of resistors in a balanced configuration, any change in resistance can be accurately detected and converted into a proportional electrical signal.
Think of the Wheatstone Bridge as a scale with two arms. The fixed reference resistor (Rref) is located on one arm; on the other hand, the variable RTD sensor resistance (RT). When heat affects the resistance of the RTD sensor and changes it, the bridge becomes unbalanced. The output voltage or current produced by this imbalance is then measured and interpreted to determine the corresponding temperature.
The Wheatstone bridge circuit is an important intermediary between the RTD sensor and temperature measuring devices such as temperature transmitters or PLC modules, enabling accurate and reliable temperature measurements.
Now that we understand the role of the Wheatstone bridge in RTD measurements, let's examine why RTDs are the preferred choice for temperature measurements and what advantages they offer.
- The Wheatstone Bridge is a crucial part of understanding how RTDs work. It converts changes in resistance in an RTD sensor into a measurable voltage or current. By using two sets of resistors in a balanced configuration, any change in resistance can be accurately detected and converted into an electrical signal. The Wheatstone bridge acts as an intermediary between the RTD sensor and temperature measuring devices, allowing accurate and reliable temperature readings to be determined. This knowledge helps us understand why RTDs are the preferred choice for temperature measurement and what advantages they offer.
Why choose RTDs? Advantages explained
When it comes to precise and accurate temperature measurements, RTDs offer several advantages over alternative methods such as thermocouples. An important advantage is its greater accuracy due to its stable and repeatable resistance characteristics. RTDs provide reliable and consistent readings, making them ideal for applications where accuracy is required.
Another significant advantage is its greater linearity compared to other temperature sensors. The change in resistance in an RTD follows a more predictable and linear relationship with temperature fluctuations. This makes calibration and offset compensation easier, ensuring more accurate temperature measurements over a wide range.
In contrast to other temperature sensors, RTDs exhibit excellent long-term stability. Materials commonly used in RTD elements, such as platinum, copper, or nickel, show minimal drift over time. This stability helps maintain the accuracy of temperature measurements over long periods of time, making RTDs a reliable choice for industrial processes that require continuous monitoring.
Additionally, RTDs are less susceptible to electromagnetic interference due to their low output impedance. This makes them suitable for environments with high electrical noise or close to other electronic devices, without causing signal degradation or inaccuracy.
Additionally, the availability of different RTD configurations (2-wire, 3-wire and 4-wire) allows users to choose the most suitable option based on their specific application requirements. For example, the 3-wire configuration is often used in industrial environments to balance the resistance of lead wires and improve measurement accuracy.
Choosing an RTD for temperature measurement is like choosing a reliable compass for navigating difficult terrain – it provides accurate, reliable guidance.