Ventilators and ECMO (artificial lungs) play a very important role in treating the Covid-19 pandemic. Nowadays, there is a great demand for various modern medical devices on the market, which has promoted the development of the medical device manufacturing industry and also the development of the medical device parts processing industry. Medical device prototyping is the foundation of the medical device design and development process.
What applications are there for CNC machining of medical parts?
The reasons for custom manufacturing of medical parts?
1. The required parts are not standard parts and cannot be purchased directly from the supplier.
For many reasons, parts are not available elsewhere. When engineers create a new production design, custom processing is often required and the individual components of the design cannot be purchased from the supplier or cannot be purchased at a reasonable price. These parts can be simple, such as gears or buttons with non-standard sizes or materials. But they can also be completely new inventions.
2. The required parts have unique features that are not present in the standard part.
For common parts that have special requirements, customized products such as individual adapters, additional functions or text engravings may be required.
3. Multiple elements can be combined into one piece.
In many cases, special machining is used to produce large parts or parts with multiple features. Because these parts are customized and ordered for specific projects, they can be heavily targeted toward a specific end use. Standardized or common components are not useful.
4. High-quality parts can be produced promptly in an emergency, and small quantities are also acceptable in machine shops.
Whether metal processing (aluminum, brass, stainless steel, etc.) or plastic processing, it offers all the traditional advantages and functions of CNC on demand. Even in emergency situations, high-quality parts can be produced quickly from digital files due to fast setup times and low minimum order quantities.
How can customer specific manufacturing be achieved in the medical industry?
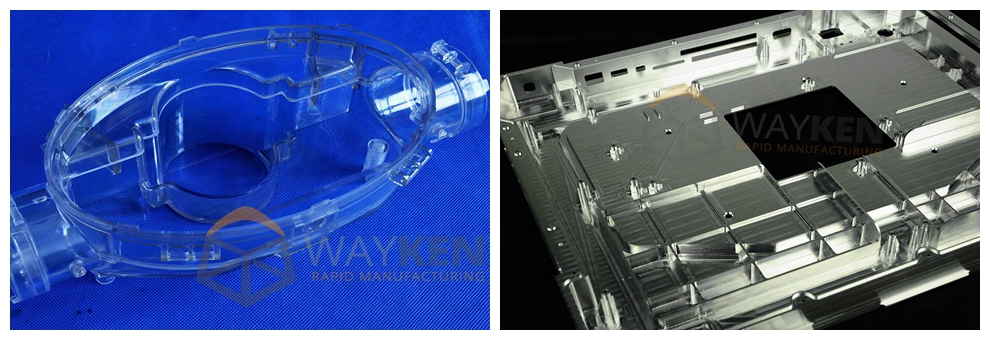
1. Material selection
There are many materials for CNC machining. What material should be selected for medical and dental equipment? When choosing the best materials for CNC medical components, one must take into consideration the load, strain, shock and temperature that the product must withstand, as well as the size, weight and other factors of the components. For example, materials used to make implants must meet strict biocompatibility and sterilization requirements.
The materials are best suited for various medical devices. For example, titanium alloys, cobalt-chromium alloys, stainless steel, PEEK, etc. are more suitable for implants. Ti alloys (Ti6Al4V), SUS alloys (SUS630, SUS420J2, SUS440C), Al alloys (A 2000 series, A 6000 series) and resins are suitable materials for surgical instruments. For more detailed material selection, simply upload your design files and contact us for professional advice.
2. Selection of CNC machining process
In short, custom machining includes all forms of CNC machining (CNC milling, CNC turning, electrical discharge, etc.) whose express purpose is to produce parts that do not exist elsewhere.
Milling is a machining process that uses rotating cutting tools with multiple blades to remove material from the part. In CNC milling, the CNC machine tool generally feeds the workpiece in the same direction as the rotation of the cutting tool, while in manual milling, the machine tool feeds the workpiece in the opposite direction to the direction of rotation of the cutting tool. The operational options of the milling process include face milling (cutting in the part with a flat, uniform surface and a flat-bottomed hollow chamber) and edge milling (cutting in the part with a deep hollow chamber, such as slots and threads).
Turning is a machining process that uses a single-edge cutting tool to remove material from a rotating part. In CNC turning, a CNC machine tool (usually a lathe or lathe) guides the cutting tool in a linear motion along the surface of the rotating part, removing material from the perimeter until the required diameter is reached to accommodate the internal functions of the parts. parts. to create external and internal cylinders, e.g. For example, grooves, cones and wires. The operational functions of the turning process include drilling, facing, grooving and threading.
3. Objective-based selection
Most of them Medical Device Housing are optical parts, generally need to be painted, sandblasted, screen printed, laser engraved, anodized, powder coated, etc. Some precision parts require machining to ensure fitment.
Case Study: Custom Casing Manufacturing for Medical Devices
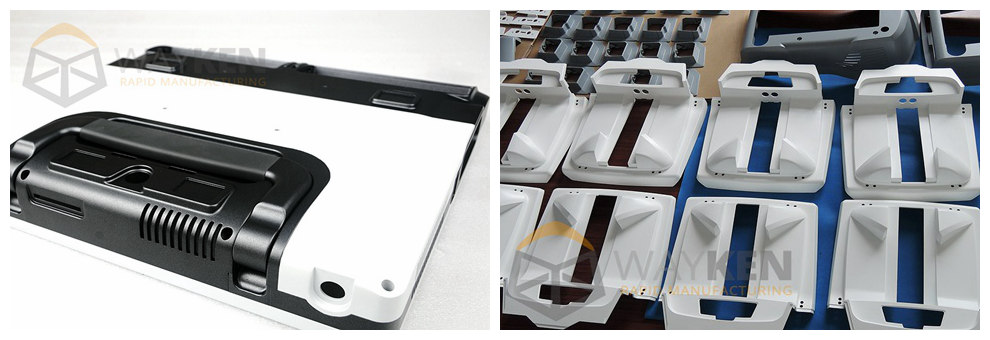
A small-volume medical device manufacturer wants its products to look as cool as the technology inside the packaging.
1. The challenge
A small-volume medical device manufacturer wants its products to look as cool as the technology inside the packaging.
2. The solution
We designed a two-piece case (top and bottom) made of durable ABS panels with cutouts for cables, sensors, electronic control panels, integrated hand holes and some exquisite design styles. We also integrate PEM nuts and threaded inserts into the housing to improve assembly quality and reduce assembly effort.
3. The result
Just like the expensive molded cases, they can all be assembled from very small parts. The customer was very impressed with the attractive appearance of the box and our quick service.
University Degree
Has this article given you some ideas about custom medical device parts so far? I hope so. If you have any questions, please don't hesitate to contact us via our website www.waykenrm.com or email us at info@waykenrm.com.