Due to rising labor costs and growing demand for high-quality products in the sheet metal processing industry, the profit margin for sheet metal processing has become narrower.
It is becoming difficult to increase efficiency and in some cases production may even result in losses.
Sheet metal manufacturing companies are turning to robotics or automated equipment to replace manual labor, with the aim of reducing processing costs and improving efficiency.
Although some companies have successfully implemented this strategy, they have had to pay a considerable cost.
However, after most companies started using robots and automation equipment, they discovered that not only were they unable to achieve the desired results, but they also faced problems with equipment breakdowns.
During the visit, the customer opened the door to receive their orders.
The main reason for most idle robots or automation equipment is not that they are difficult to use or cannot be used, but rather that sheet metal companies cannot thoroughly analyze the process and production of their products. Before purchasing robots or automation equipment, they do not understand the performance and limitations of the equipment.
To make a sale, automation equipment sellers tend to exaggerate the equipment's performance. Consequently, purchasing companies mistakenly assume that the automation equipment they purchase is capable of anything.
However, once automation equipment is put into production, only 30% of products can be produced automatically, while the remaining 70% still require manual production. As a result, the utilization rate of automation equipment is very low.
It is essential to carefully analyze the company's product process and batch and evaluate the performance and limitations of automation equipment before adopting it. This is because even the most advanced automation equipment has its limitations.
In conclusion, we should share the investment and selection of sheet metal process automation equipment, keeping in mind the importance of analyzing the process and product production and evaluating the performance and limitations of automation equipment before purchasing it.
Erase process
Currently, the main equipment for blanking is laser cutting machines and CNC punches. They are sophisticated CNC machines with a high degree of intelligence.
By incorporating automatic loading and unloading devices, fully automatic production can be achieved.
Laser charge and discharge selection
The cantilever suction cup is part of a semi-automatic feeding device that is economical and suitable for feeding thin plates with a thickness of less than 5mm and a weight of less than 20kg.
However, using the semi-automatic cantilever method to feed thick plates would be challenging to manually push the suction cup and is therefore not recommended.
The gantry type automatic feeding device is ideal for feeding thick and large plates, ensuring safety and high efficiency.
However, it is not recommended to use the automatic device for automatic laser suppression, as laser processing is mainly used for small batches and jobs of various varieties, and automatic suppression may reduce processing efficiency.
For large production batches, it is recommended to use a laser coil cutting production line to save materials and achieve high processing efficiency.
Blanking selection and NC loading
The advantages of the unilateral automatic loading and unloading device are:
Charging and discharging are carried out on the same side and a single charging and discharging cycle takes between 35 to 40 seconds.
The useful area of the warehouse is small.
The material warehouse can be expanded and additional storage capacity can be added without increasing the usable area.
The advantages of automatic loading and unloading devices on both sides are:
The charging and discharging efficiency is higher when compared to single-sided.
The loading and unloading cycle can be completed in 16 to 20 seconds, but requires a relatively large area, making it suitable for sheet metal companies with unrestricted locations.
For more than 3 CNC presses, it is recommended to add automatic loading and unloading devices.
In one case, a single person can operate three CNC presses with automatic loading and unloading devices, and one shift can reduce 3 to 4 operators, resulting in reducing the labor intensity of operators and freeing up repetitive mechanical loading and unloading work. discharge.
Operators will have more time to consider pre-processing preparation, such as die preparation, material preparation and optimization of processing procedures, significantly improving processing efficiency.
The automatic NC punching loading and unloading device is a mature scheme.
Training process
Press the brake forming
Press brakes are used by 98% of sheet metal forming factories. This equipment requires minimal investment and can be used for general processing purposes. However, manual operation is a requirement, which is its only drawback.
When processing parts with a length or width greater than 50 mm, one person may find it difficult to operate the machine, and at least two workers are required to cooperate in processing (see Fig. 1).
Furthermore, when working with sheets thicker than 2 mm, bending efficiency is low and industrial accidents are more likely to occur.
Bending work is physically demanding and takes time to learn and gain experience. Therefore, the salary for this type of work is higher than that for other types of work.
To reduce labor costs, two automation schemes are used: robotic bending and servo-assisted bending.
(1) Robot bending.
By debugging the equipment in this way, it is possible to achieve fully automatic production without any shutdowns.
Long-term processing is more efficient than manual processing because a single commissioning personnel can operate multiple bending machines.
However, a major disadvantage of this method is that it requires a long debugging time and has relatively high requirements for operators. Furthermore, it is not suitable for processing multiple varieties and small batches as different products require replacement of the suction cup structure.
Many companies have invested in robotic folding; However, due to insufficient batch size of fixed product orders, operators are unfamiliar with the debugging process, resulting in idle equipment.
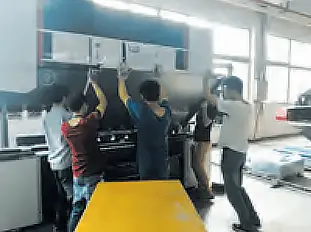
Fig. 1 Traditional push-up
(2) Bending is aided by the spreadsheet followers (Figure 2).
This method can be used for multiple variety production as well as large and small batch production.
The advantages of bending large parts and thick sheets are obvious: it reduces the need for auxiliary personnel for bending (Fig. 3), reduces labor intensity and provides great flexibility.
A single sheet follower can be used with multiple press brakes and the investment cost is relatively low.
The disadvantage of this method is that manual loading and unloading operations are required and automatic production cannot be fully realized.
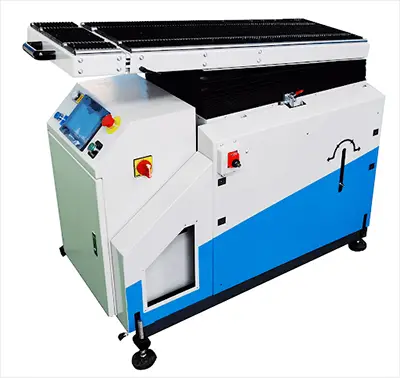
Fig. 2 Leaf follower
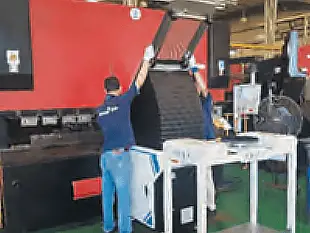
Fig.3 Bending with sheet follower
Panel bender
The panel bender features high processing efficiency, enabling fully automated production and is suitable for complex chassis processing.
However, it is important to highlight that the machine was not designed to bend thick sheets or products with hems greater than 300mm. Furthermore, it entails a high cost of inputs and maintenance expenses, making it inaccessible for large factories.
The profitability of sheet metal processing is low, making it difficult to recover the initial investment.
Tuning process
Sheet metal installers primarily engage in activities such as drilling, threading, and countersinking.
Certain sheet metal products require aluminum profile processing, with necessary steps such as avoiding blind holes and fisheye holes.
Conventional processing equipment employed in this field includes bench drills, tabletop threading machines, and milling machines.
Manual assembly line operation has a higher probability of quality accidents such as leaking holes and leaking teeth.
For more complex parts, several threading, reaming and reaming processes with different specifications may be required.
The processing of traditional equipment is relatively complicated, requiring coordination between multiple individuals and resulting in low efficiency.
To solve these problems, many sheet metal companies use drilling, tapping, and milling centers (Fig. 4).
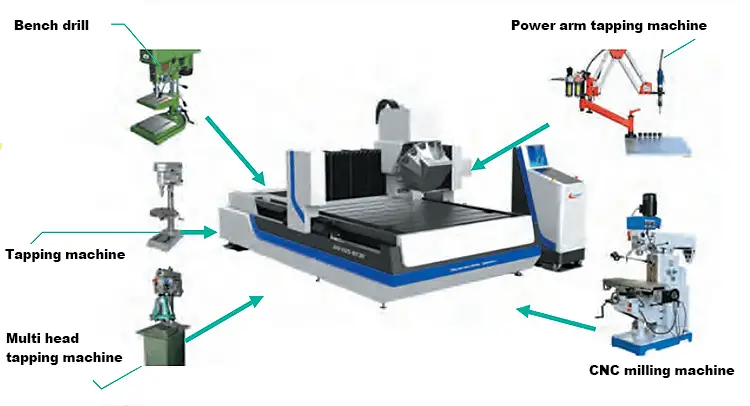
Fig. 4 Drilling and tapping center
A drilling, tapping and milling center is a type of numerical control equipment that integrates the functions of drilling, tapping and milling machines. It features offline programming and automatic tool changing with a multi-station tool library.
This equipment can clamp multiple parts simultaneously and automatically process all necessary drilling, tapping, gap milling and other processes according to the program. Furthermore, it can attach and disassemble parts without the need to stop, resulting in high efficiency (40-60 holes per minute). In addition, it can also process profile radiator products.
However, one of the disadvantages of this equipment is that it requires programming and tools, making it unsuitable for testing or processing product samples.
Welding and grinding process
We will not delve into welding with manipulators as it is a well-established automation technique.
Grinding constitutes the process bottleneck for most sheet metal companies.
The grinding process is essential for sheet metal processing, but it is a laborious, dirty and unpleasant task carried out in a challenging environment.
Recruiting skilled grinding workers is a significant challenge.
Most mill workers are in the post-60s and post-70s age group and it is difficult to attract younger people to the job. As a result, the labor cost of grinding remains high.
In an attempt to solve this problem, some sheet metal companies have experimented with robotic polishing, leveraging experience gained from automating hardware polishing. However, most of these attempts ended in failure.
We recommend you the relatively mature five-axis CNC grinding workstation (Figure 5). This equipment is used to grind welding scars on the surface of sheet metal parts, suitable for grinding and polishing the surface of boxes, cabinets, door panels and internal structural parts.
This machine is mainly used in communication equipment, power equipment, medical equipment, environmental protection equipment, electronic equipment rack, body insurance and related industries, replacing traditional manual grinding and improving factory processing efficiency, shortening the time of sheet metal processing.
The workstation has manual movement of materials, with the part fixed on the bench, and the X/Y/Z/B/C servo is positioned and rotated, which greatly improves the accuracy and response speed of the equipment. The platform uses a large diameter threaded guide rail, which ensures precision and improves the stability of the bench.
The 5-axis CNC system, combined with bus service and intelligent manual teaching technology, solves the problem of professional programming in sheet metal enterprises and reduces the skill requirements of operators. It is simple, fast and has great punctuality in product transformation.
One of its shortcomings is that it is not suitable for grinding small batch products, and tool accessories need to be manufactured (grinding tool accessories are relatively simple and low-cost). In addition, the inside and small corners of some products cannot be polished.
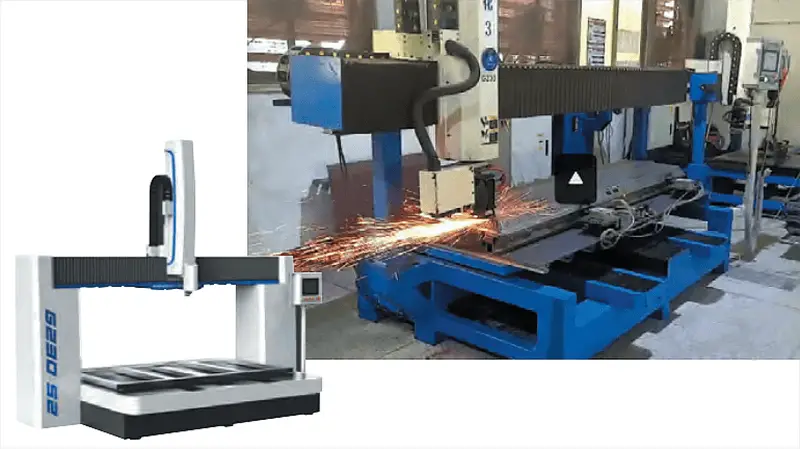
Fig. 5 Five-axis grinding workstation
Conclusion
Selecting sheet metal automation equipment doesn't have to be expensive.
While imported automation equipment may not be easy to use, the cheapest option may not be the easiest to use either.
Sheet metal companies should select automation equipment based on the characteristics of their own products, which adds value.