Turning is a versatile machining process used to produce parts in most industries. This process uses a lathe to produce parts with extremely high tolerances and surface finishes. Therefore, the turning process is popular in the production of axisymmetric parts in various industries, including automotive, aerospace and other sectors.
In this article, we will look at the turning process, types of turning, materials suitable for this process and their applications in different sectors.
What's spinning?
Turning uses a cutting mechanism to remove material from a rotating part to create the desired shape or form. Turning involves holding raw materials and rotating them at high speeds while a cutting tool is inserted into the workpiece along one, two, or three axes of motion to create the desired width and depth. Furthermore, turning is carried out in two ways: manual and automatic.
In the past, the manufacturing industry relied more on manual turning. Manual turning required human operators to frequently adjust the workpiece and machine during operation. Nowadays, automatic turning has gained an advantage as it speeds up the turning process through a CNC (Computer Numerical Control) system.
This automatic turning process offers efficient and fast solutions. Although the machinist still needs to specify part specifications in a computer program, the machine effectively translates this data into turning operations.
How does the turning process work?
In this process, the cutting tool is moved linearly along the rotating surface of the part using a machine. This involves removing material from the workpiece until the desired shape or part is achieved. The turning procedure includes:
- Fix the part and, depending on the type of feed, fix it in the lathe with a roughing or finishing tool;
- Adjust the lathe to the correct speed and feed for the desired width and material to be cut.
- Start the lathe and make a light cut to the specified length on the right side of the workpiece.
- Stop the lathe, but do not move the cross-feed screw lever;
- Measure your work and calculate the material that can be removed;
- Finally, check the turned piece for irregularities and make corrections if necessary.
Types of Turning Operations
Various turning processes are used in various manufacturing industries to produce machine parts. This section explains turning processes used in various industries.
Turn
It is the most versatile process that removes excess material from the outer surface of the raw material. Turning is carried out continuously until the perfect design is achieved. The process carries out the work with great precision and finish.
Tedious
The process of removing material from a hole in a material. Hole machining is applied when a hole already exists. It is also used to correct a hole that is not perfectly round.
Touch
This process uses a tap to create threads that are inserted axially through the hole in the raw material. The tap is a cutting tool with multiple blades and the workpiece is rotated slowly while placed on a faceplate. The device then supports the tap on a tailstock spindle.
serrated
Serration creates a diamond-shaped pattern on the surface of the workpiece. It improves the adhesion of the machine part and makes it more attractive. In this process, the raw material is placed in contact and the teeth are wrapped around the piece.
To scrub
It is used to enlarge holes. The tool penetrates axially through the material to expand the existing hole to the diameter of the reamer. Friction creates a rounder hole by removing a small amount of material, resulting in a better inner surface.
To the next
The tool makes a progressive cut in the workpiece, passing through the vertical axis as the workpiece rotates. As the process continues, the cutting tool separates from the workpiece and falls when it reaches the center.
disguise
This process reduces the length of the workpiece and the facing inserts are the exact size of a workpiece. The workpiece ends perpendicular to the axis of rotation. The tool moves along the radius of the part to create the desired length.
piercing
The process is also known as constriction. Helps create a narrow piece. The width of the cutting tool determines the size of the cut. This process can create a narrow cut or remove material through radial movement.
Threading
This operation is a turning process that uses mechanical tools to cut threads. The tool moves along the side of the workpiece.
Stick
Typically, this is the first step in creating internal features that require more work to refine. Drilling is used to create a cylindrical hole in the workpiece from a material, usually metal.
Cutting parameters in turning
There are some parameters that affect the turning process, including:
- feed rate : Determines the tool cutting speed required for the part. The feed rate can affect the surface processing quality and production speed. A higher feed rate can have a negative effect on surface processing.
- depth of cut : The depth of a cutting tool varies with the radius of the workpiece during a turning operation. This factor affects the useful life of the part, the production rate and the finish. When determining the depth of cut, the type of material and hardness must be considered.
- cutting speed : This is the speed of the surface material as it moves toward the cutting tool. The speed depends on the type of material, the cutting tool and the diameter of the workpiece at the cutting point. The productivity of the turning process is also influenced by this parameter.
Other factors include metal removal rate, tool shape and machine power requirement.
Comparison between rough turning and finish turning
Grinding in the turning process removes a significant amount of excess material from the part. It is the first stage of the filming process. In addition, shapes are created that are closely related to the required geometry of the part, making the process easier and more efficient.
The advantage of roughing is that empty tolerances are quickly removed, which affects the surface and dimensional characteristics of the product. Although this process increases productivity, it produces components that do not have high precision.
During finish turning, part material is slightly removed to refine the surface. Final machining is performed to achieve dimensional tolerances and surface quality. Tool wear, built-up edges and chip type can affect surface quality.
Furthermore, turning is carried out to meet the standard machining characteristics of flatness, roughness, thickness and tolerance.
Main characteristics of roughing and finishing cuts
For a better understanding, here are the distinguishing characteristics of roughing and finishing cuts:
- Roughing requires a high material removal rate, while finish turning requires a lower material removal rate.
- Finish turning produces a good surface finish, while rough turning produces a poor surface quality.
- With rough cuts, tight tolerances are poorly maintained, while with finish cuts, tight tolerances are maintained well.
- During roughing, a higher chip load occurs on the cutter, while during finishing, a lower chip load occurs.
Turning tools commonly used in the turning process
Different types of turning tools are used in manufacturing parts, and each type has its own structure, material composition and function. Turning tools are classified according to specific processing. That includes:
- Facing Tool : This tool has a side cutting edge. There are two types: a right-hand cutting tool works on the right side of a workpiece and a left-hand cutting tool works on the left side.
- Chamfering Tool : It is made of carbide and high-speed steel. There are subtypes of chamfering: single-angle, variable-angle, and reversible chamfering tools.
- Thread cutting tool : There are two types: internal and external. The former creates a thread in a hole, while the latter creates a thread in the workpiece.
- molding tool : This tool is suitable for precision CNC machining. Molding tools are used to produce parts that require high precision and accuracy.
- Taper Turning Tool : This tool is suitable for increasing and decreasing the diameter of a part. Cone tools are used in various industries to make shafts, cones and nozzles.
- Groove cutter : These are suitable for making grooves on the surfaces of a cylindrical part. Grooving tools come in different shapes depending on the turning process.
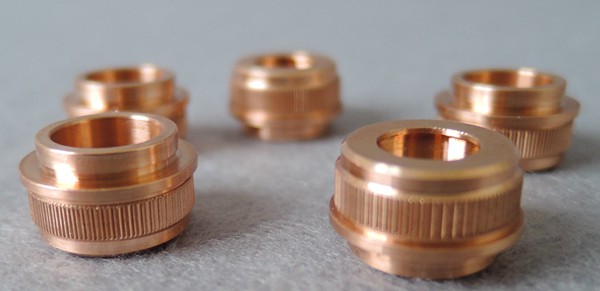
What materials are suitable for turning?
There are suitable materials that are ideal for turning processes. The most common materials are mainly metals, some are plastics. Metallic materials include steel, brass, aluminum, nickel alloys and titanium, while plastics include polycarbonate, PEEK, PEI and PP.
Turning is done based on the machinability of the material and the desired surface finish. Sturdy workpieces such as steel require a special cutting tool such as the single edge cutting tool made of high speed steel and carbide. This is ideal for high performance operations or certain cutting forces.
Additionally, some materials such as aluminum and titanium can be machined to create smooth surfaces and are flexible enough to form complex shapes and sizes.
Advantages of the turning process
The turning process offers many advantages, but let's look at the advantages of this machining process:
- High precision and tolerance : The turning process adds precise rotational characteristics to the parts whose shape it is designed for. Furthermore, accuracy and tolerance levels are effectively optimized.
- Fine surface quality : Turning operations can improve surface finish by increasing cutting speed and adjusting a geometric angle that improves finish quality.
- Efficiency in mass production : Parameters are effectively imputed to allow production of many parts at greater speed.
- Different cylindrical shapes and geometries : The turning process can produce parts with different angles and cylindrical shapes for different industries.
Limitations of turning processing
Although there are advantages to the turning process, there are also limitations.
- Equipment is expensive : Rotators are expensive and require additional attachments and accessories, which increases costs.
- Requires frequent tool changes : Turning tools perform specific and unique functions. This can slow down the process as tools need to be changed at certain times for efficient operation.
- Cylinder components only : The lathe is designed for axial movement. Limits the shape of the part created per feature.
Building Tips for Optimal Results When Spinning
To meet manufacturing expectations, turners need to keep important things in mind. Below you will find tips for optimal design.
- Try to maintain uniform wall thickness : Choosing uniform wall thickness for your parts can impact the cost and speed of the turning process. It can also affect the functionality of the part.
- Avoid complex designs : Construction should be as simple as possible to avoid difficulties during turning.
- Select standard rotary screw size : helps reduce the time and additional cost of filming operations.
- Can be processed in one configuration : Because tools are used for specific machining operations, remember that different parts may require different turning tools. Therefore, opt for designs that suit a single setting.
Turning applications in various sectors
Turning operations represent a technological revolution in several industries. Their accuracy, tolerance and flexibility are valuable and make them applicable in diverse industries.
Let's take a closer look at the application of the turning process:
- Automotive industry : CNC turning service supports the automotive industry in the production of engine parts, transmission components, gearboxes, wheels and brakes.
- Aerospace industry : This industry requires high-precision, high-performance components, including satellite and rocket components, aircraft engine compartments, and landing gear components.
- Medical Industry : Turning is used to produce precise and compatible devices and equipment from biocompatible materials. CNC turning can be used to produce sharp surgical instruments as well as dental and orthopedic implants.
- Military and Defense Industry : Precision equipment components and customized vehicles like military equipment are designed with the turning process in mind.
What are the differences between a turning center and a lathe?
Turning centers are a more advanced process than lathes. Both machining tools rotate the part components, allowing the cutting tool to remove material from the part.
On the one hand, turning centers feature turret-style cutting tools for automatic changeover, efficient chip removal and internal coolant management. Multi-axis turning centers are much more versatile in their cutting capabilities and exceed the performance of a traditional lathe.
On the other hand, the lathe is a versatile and basic turning device. It rotates the part around its axis while the stationary cutting tool gives the complicated part a precise shape. An experienced operator is required to minimize possible deviations and errors.
Lathes do not have a protective cover around the machine and also do not offer great production capacity compared to turning centers. Additionally, cutting tools are fed parallel or perpendicular to the workpiece axis.
Alternative technologies to the turning process
There is no doubt that there are other technologies that can produce cylindrical parts. These alternative methods include:
Grind
During milling, material is removed from stationary parts using rotating tools. For example, tubular or cylindrical components as well as contour surfaces can be created in a single operation.
Although turning and milling have similar operation, the main difference between the two machines is rotation. When turning, the part rotates, while when milling, the cutting tools rotate. However, turning is more effective than milling for machining cylindrical components.
Grind
Grinding is a machining process that uses a grinding wheel to remove material from a part. The grinding wheel removes material from the surface to create parts with flat, cylindrical or conical surfaces.
Furthermore, it processes a wide range of materials, from hard to soft. In contrast to other processing methods, precision grinding can also create complex shapes and contours.
Turn your project into reality: choose WayKen for your turning solutions
Concluding
Turning is a versatile field that offers advantages to many industries in terms of surface processing and tolerances. These operations and application types continue to adapt to advanced innovations, increasing productivity and economic relevance in the environment.
Common questions
How much does turnover cost on average per hour?
CNC turning cost per hour can vary. However, in general, expect to pay between $50 and $100 per hour for the service.
Which turning process produces a narrow cut?
The groove creates narrow cuts of fixed depth on the inside and outside of the workpiece.
Are turning and drilling the same process?
Rotary cutting tools remove material from outer surfaces, while auger cutting tools remove material from the inner surfaces of a workpiece.