Type I forgings are common parts in the oil drilling industry, including wellhead devices, oil trees, throttling and pressure equipment, and there is a high market demand for them.
The shape of this type of forging has the following characteristics: the two ends of the flange and the intermediate cylinder are coaxial, and there is a difference in diameter between the flange and the intermediate connecting cylinder.
Forging process status and analysis
The current commonly used production process for I-shaped forgings involves two steps:
(1) The production process begins by directly forging large cylindrical forgings based on the approximate dimensions of the product flange diameter. These large cylindrical forgings are then processed through machining.
(2) In addition to the above process, a symbolic pulling and stretching process is used to form the small central cylindrical part.
However, both processes have the following shortcomings:
- Low use of raw materials, which in extreme cases can be less than 50%. For the products studied in this article, the raw material utilization rate using the direct free forging process was only 74% at most.
- Large quantities of spare parts for processing and high processing costs, resulting in high production costs and poor product profitability.
- Long production cycle and low customer satisfaction rate.
In this article, our focus is on the type of forging. Our objective is to break the limitations of the traditional production process and avoid the problems mentioned above, in order to reduce production costs, adapt to market rhythms and increase market competitiveness.
We mainly focus on the shape of such forgings, starting from split die design and using the tire die forging process for production to achieve the dimensional accuracy of forgings.
Process flow of I-shaped forgings
Because these forgings are primarily produced in small to medium batches, they are manufactured using the die forging process.
Due to excessive investments in workwear and high production costs, improving market competitiveness has become a challenge. Therefore, a comprehensive analysis is being considered. Research into the split die production process can provide dual benefits such as precision in forged products and the production of multiple small batches of tire die forging.
The specific process flow diagram is illustrated in Figure 1.
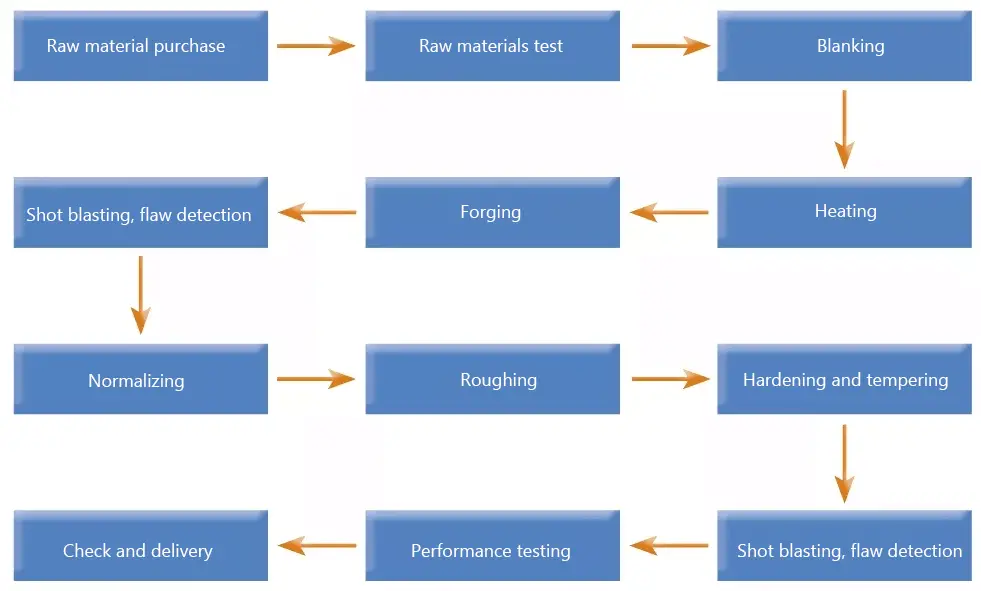
Figure 1: Process flow diagram
Forging design
The newly developed I-shaped parts weigh 101.96 kg in mass and 154 kg in forgings. The calculation of the forging process indicates a complexity factor S of 0.53.
As the free forging process already belongs to the complex class of forgings, the split die design requires higher standards.
Using the user-supplied part diagram, forgings are created based on the new process plan. This plane brings the forging process closer to balance, resulting in high dimensional accuracy. Figure 2 displays the part and forging diagrams.
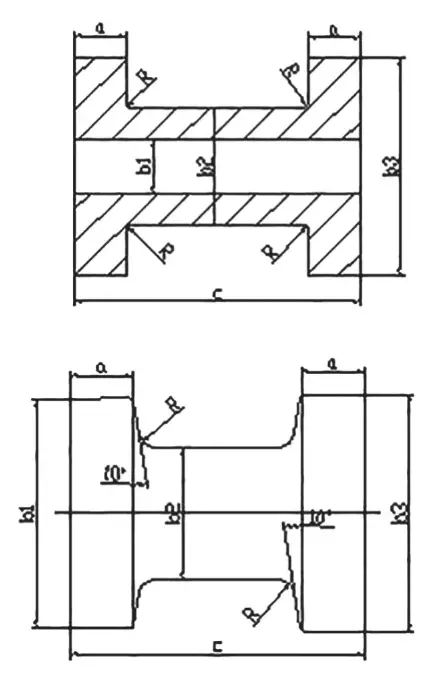
Figure 2 Parts and forgings diagram
Forging process development
The production plan for the forging process is as follows: first, the billet is drawn, and then the flange is formed by cutting out one end of the tire die, followed by forming the other flange using the combination of the parting insert and of the outer tube die.
This forging process ensures that the first upsetting process serves as the molding process for the second upsetting process, thus allowing control over the eccentricities of the forgings and the dimensional accuracy of the blanks.
After careful calculations, it was determined that the quality of the forgings and the quality of the cutting die combined weigh more than 600 kg. Therefore, to ensure optimal results during the final cutting die forging process, a 3t free forging hammer should be used as forging equipment.
Mold design
Tire mold design base, split insert and sleeve mold
Tire mold design basis: cold forging diagram → hot forging parts → tire mold. The dimensions of hot forgings are calculated according to formula (1).

In the formula, Lt represents the forging size at the final forging temperature (mm); L denotes the size of the cold forged part (mm); α represents the expansion coefficient of the material line (1/C); t represents the final forging temperature (°C).
For forging materials in the petroleum industry, mainly AISI4130 and 410SS, the initial forging temperature is generally 1150°C, and the final forging temperature is at or above 860°C. As this forging process is relatively long and the final forging temperature is low, the cold shrinkage rate is appropriately reduced to 1.2% – 1.4%.
The subpackaging design is based on the tire mold design process, with emphasis on assembling the sleeve mold during the design process. This approach helps to avoid situations where assembly is impossible or difficult.
Tire mold design and split mold
Based on the established forging production process, the tire mold (as shown in Figure 3), split inserts (as shown in Figure 4) and sleeve mold (as shown in Figure 5) were designed by incorporating the elements of tire mold design. .
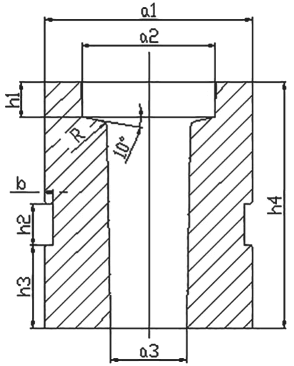
Figure 3 Tire Mold
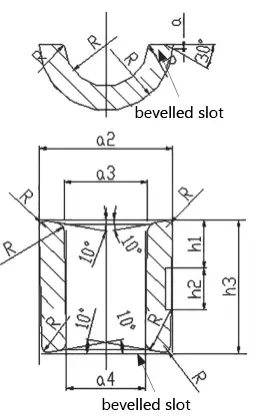
Figure 4 Split Insert
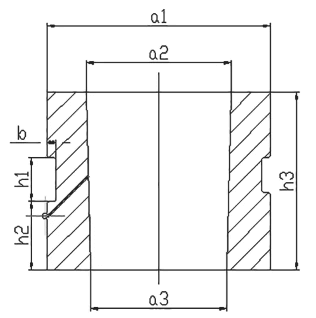
Figure 5 sleeve pattern
Figure 3 shows the first settlement die, which required an accurate calculation of the weight of the forged part during the initial design phase. Failure to do so may result in back filling during free forging after upsetting.
The split inserts are illustrated in Figure 4. The design must take into account that the split insert is located in the intermediate cylinder of the forged part after forging forming. To facilitate removal, a beveled groove is made at the interface of the split die. This groove allows for easy removal of the split insert after forging.
At the same time, a local optimization project was carried out. The design of the end face in contact with the inside of the flange was inclined by 10°. The internal chamfer was R20mm, and the contact chamfer between the external part and the second matrix of the turned sleeve was R15mm.
The general slope of the outside of the mold is the same as the slope of the inner cavity of the holding mold shown in Figure 3. The diameter is reduced by 1 mm on one side to facilitate placement in the cavity of the sleeve model shown in Figure 5 .
The sleeve die, shown in Figure 5, is designed to ensure the flange size after pressing. A2 and A3 sizes are designed for the size of the hot forged part, with a slope-free transition of the cavity. Figure 6 shows a composite split die with split inserts and sleeve module.
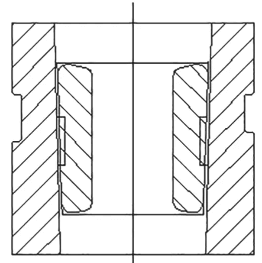
Figure 6 Split Matrix
The tire mold is matched and forged using 3TZ, which results in significant rolling force during the forging process. Consequently, in the design phase, the thickness of the glove mold is increased overall to compensate for this.
Conclusion
After verifying the actual small batch production, the split die forging process plan proves to be successful and feasible. It also has the ability to guarantee the mass production process.
This paper introduces a new process method for producing I-shaped forgings, which saves 23% of raw materials compared with direct free forging. The new scheme effectively produces I-shaped forgings that meet the desired process target value.
Forgings made using this method exhibit the same level of technology as die forging. Compared to die forging or direct free forging, this process saves 20% to 40% of raw materials, reduces production costs and increases process flexibility.