An experienced professional with more than 20 years of experience in the field of bending machines said that he expressed his opinion on machine tool brands, with which I completely agreed. Therefore, I wanted to share your words. Hopefully this can bring a new perspective to those blindly searching for brands.
In his own words, he said:
“ When it comes to machine tools, don’t focus on the brand, but rather whether the seller is honest and conscientious. Some people, for the sake of money, will sell refurbished machines or replace inferior products with superior ones. For example, if you buy a branded computer for $10,000 or build a computer for the same amount, which do you think would be better? Which would be more practical? What brand could you attribute to the mount? I have been assembling machine tools since 2004, from after-sales to current sales, and I have seen a lot of equipment. They are really good, from the finish to the configuration, precision – I won't deny that. The price will also surprise you! Nowadays, domestically produced machine tools are very mature. You can buy equipment with the same performance as branded and imported equipment for less than half the price. So why chase the brand? I believe that practicality is the most realistic pursuit. This is just my personal opinion, so if you find it incorrect, please forgive me! “
I. What is a press brake?
A press brake , also known as a brake press, is a machine tool used to bend and form sheet metal and plate materials. It is an essential equipment in metallurgy, fabrication and manufacturing industries.
A typical press brake consists of a long base with a stationary lower beam and a movable upper beam. The upper beam, called the ram, holds the punches while the lower beam holds the corresponding dies fixed in place. The workpiece, usually a piece of sheet metal, is placed between the punch and the die.
During operation, a hydraulic or mechanical force is applied to the ram, pushing the punch into the die. As the punch presses into the workpiece, it conforms to the shape of the die, creating the desired bend or shape in the sheet metal. The angle and shape of the bend are determined by the design of the punch and die assembly used.
Press brakes are highly versatile and can perform a variety of bending and forming operations, including:
- V-fold: The most common type, using a V-shaped die to create angled folds
- U-bend: uses a U-shaped die to form channels or more complex shapes
- Box and pan folding: Multiple folds to manufacture box or pan-like parts
- Corrugation: Forming a series of alternating protrusions and grooves in sheet metal
- Hemming: Folding the edge of a sheet over itself to create a rounded edge
Modern bending machines are often equipped with CNC (computer numerical control) systems for precise control of the bending process. The CNC controller allows operators to program desired bending angles, bending sequences and ram positions. This automation increases productivity, ensures consistency and reduces setup times.
Press brakes come in a variety of sizes and tonnages to accommodate different sheet metal thicknesses and part sizes. Typical press brake capacities range from 20 to 2,000 tons of bending force and bed lengths from 4 to over 20 feet.
In summary, a press brake is a critical machine tool for bending and shaping sheet metal components in metallurgical industries. Its flexibility, precision and power make it an indispensable asset for manufacturing parts in sectors such as aerospace, automotive, construction and general manufacturing.
II. Types of press brake
Here are the main types of press brakes used in sheet metal manufacturing:
Mechanical press brakes
- Use a flywheel, clutch and crankshaft to generate the force needed to bend
- Consistent and reliable for high-volume production
- Slower than hydraulic brakes but require less maintenance
- Suitable for thicker and harder materials
Hydraulic presses
- Powered by hydraulic cylinders and pumps
- Provides greater flexibility and precision control over bending force
- Can handle a wide range of materials and thicknesses
- Faster cycle times than mechanical brakes
- CNC models allow for complex bends and quick configuration changes
Pneumatic press brakes
- Use compressed air instead of hydraulic fluid
- Compact, lightweight and portable
- Ideal for smaller parts, shorter runs and prototyping
- Limited tonnage compared to hydraulic and mechanical brakes
Electric servo press brakes
- Driven by high-torque servo motors instead of hydraulics
- Highly energy efficient and environmentally friendly
- Faster cycle times and more precise bend control
- Easily programmable for complex curves
- Higher initial cost but lower operating expenses
Hybrid press brakes
- Combine features of different brake types
- Example: hydraulic rams with servo-driven electric back gauges
- Aims to provide the best combination of speed, accuracy and flexibility
The choice of press brake type depends on factors such as production volume, part complexity, material properties, speed and accuracy requirements, as well as budgetary considerations. Many modern press brakes incorporate CNC controls and can be highly automated for optimal performance in different bending applications.
III. Top 10 Press Brake Manufacturers
Press brake manufacturing has seen significant advancements over the years, with numerous companies establishing a strong presence in this specialized market. Press brakes are crucial in the metal fabrication industry, enabling the precise bending of sheet metal, and selecting a press brake can significantly influence production quality and efficiency. Some manufacturers stand out for their long tradition of innovation, quality and service in this sector.
The leading manufacturers in this field are characterized by their extensive experience, robust engineering practices and commitment to technological development. For example, Amada, originally founded in 1946, pioneered the manufacture of sheet metal processing machines, including press brakes. Another notable leader is Trumpf, founded in 1923, recognized for its innovative high-tech solutions in machine tools, laser technology and electronics. These companies have a proven track record and are esteemed for their contributions to advances in manufacturing technology.
The industry benefits from a diversity of press brake manufacturers, each offering unique strengths and specializations. The best manufacturers offer a combination of reliability, advanced features and responsive customer service, aligning with diverse business needs and operational demands. When evaluating the key players in the press brake domain, several other significant names are considered, underlined by continuous improvement and adaptability to the demands of the modern metallurgical industry.
Note that the list is organized alphabetically and not by rank.
1. LOVED
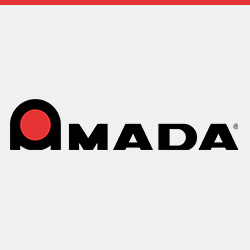
Amada, founded in 1946, is a multinational company specialized in the production of machines for processing sheet metal.
With a strong market presence, a diverse product portfolio, high-performance products and an effective management system, Amada has evolved into a publicly traded company offering a comprehensive range of services including product development, design, manufacturing, education and training, after-sales service and network marketing.
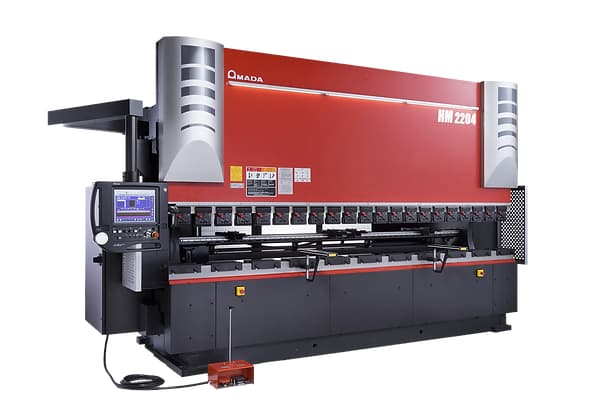
2. Accuracy
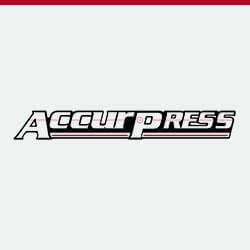
AccurPress, founded in Canada in 1973, is a leading provider of high-quality CNC machine tools in North America. They specialize in providing CNC bending and shearing machines and have six factories and a research and development center located in Canada, the United States and China.
In 2003, AccurPress established a wholly owned subsidiary in China to serve as a research and development, production and service center for the Asia-Pacific region. Since then, they have supplied more than 6,000 high-quality machine tools to customers in the Asia-Pacific region.
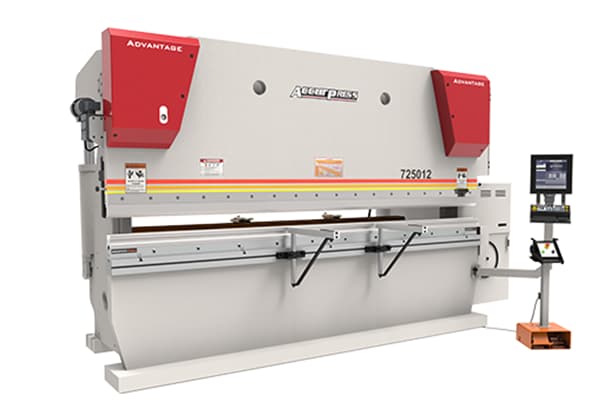
3. Bystronic
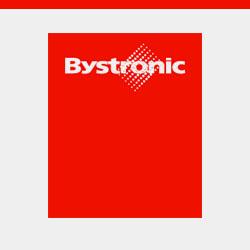
Bystronic, founded in Switzerland in 1964, specializes in automating the entire flow of materials and data for cutting and bending processes.
Their offerings include laser cutting systems, press brakes, and related automation and software solutions, making them a complete solution provider for sheet metal processing.
Bystronic has sales and technical service subsidiaries in more than 30 locations worldwide.
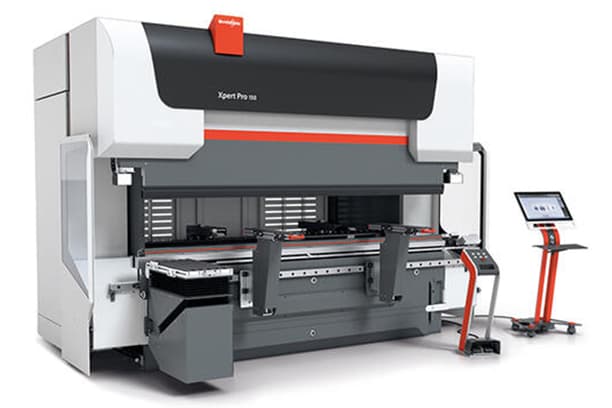
4. CINCINNATI
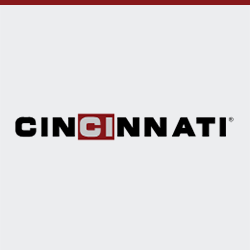
Located on an 80-acre campus near Cincinnati, Ohio, it operates a modern 500,000-square-foot manufacturing and technical center.
Its products, including laser cutting systems, automation, press brakes, shears, powder metal presses and additive manufacturing, are designed and built with the robustness required for the North American market.
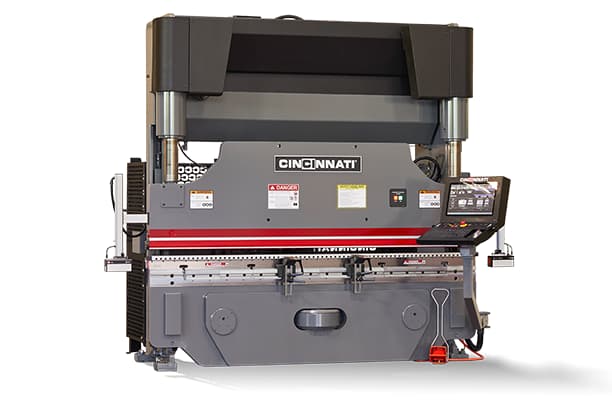
5. Durmazlar
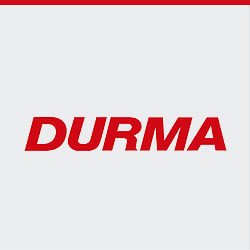
As the leader in its sector in Turkey, Durma is a global manufacturer of sheet metal processing machines with a team of 1,500 experts. They have a state-of-the-art production line covering 150,000 square meters.
Durma exports to 120 countries through 80 distributors and partners, with 80% of its machines sold to industrialized countries such as the USA, EU and Australia.
The remaining 20% is sold to companies in developing countries or to partnerships with foreign investors.
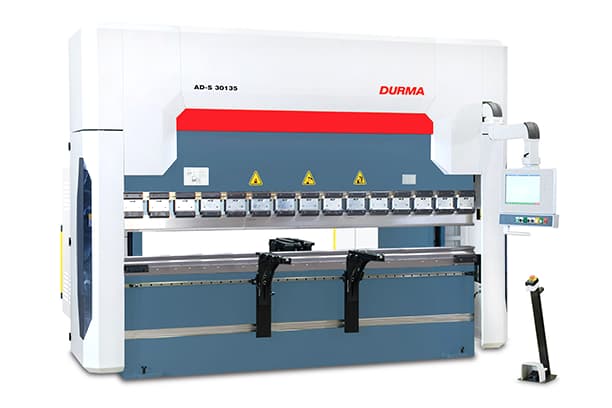
6. LVD
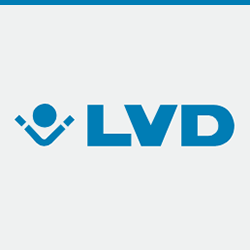
As a market leader in CNC bending/forming technology, LVD offers a wide range of press brakes, ranging from economical manual and CNC options to multi-axis machines featuring LVD's proprietary adaptive forming system and touchscreen control, as well as as customized designs.
All of these press brakes are designed to make programming easier, eliminate the need for trial bending, and provide accurate, consistent results.
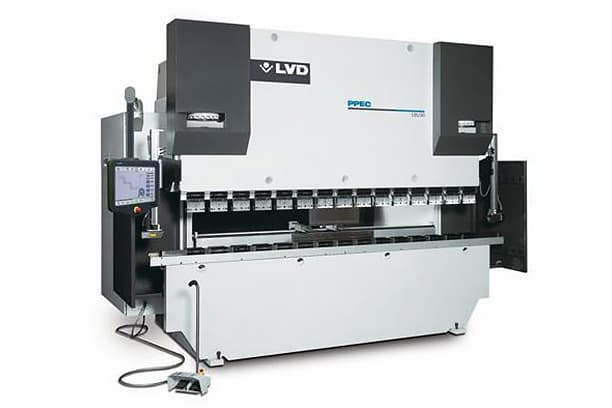
7. Primary Power
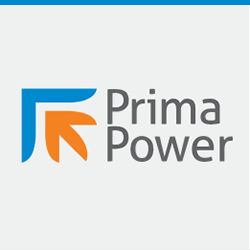
Prima Power is a division of the Prima Industrie Group, listed on the Milan Stock Exchange.
In 2017, the group celebrated 40 years of operation in the area of sheet metal working machines.
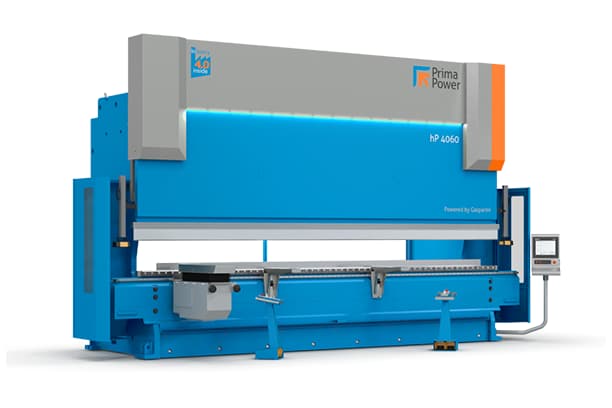
8. Salvagnini
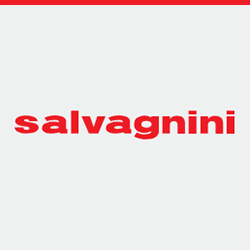
Flexible automation and process efficiency form the basis of the Salvagnini product range.
These products offer intelligent, autonomous and independent solutions that are easy to program and use.
They are automated and interconnected, communicating with each other and the surrounding environment to create a more agile production process for the efficient and effective production of multiple parts in sequence.
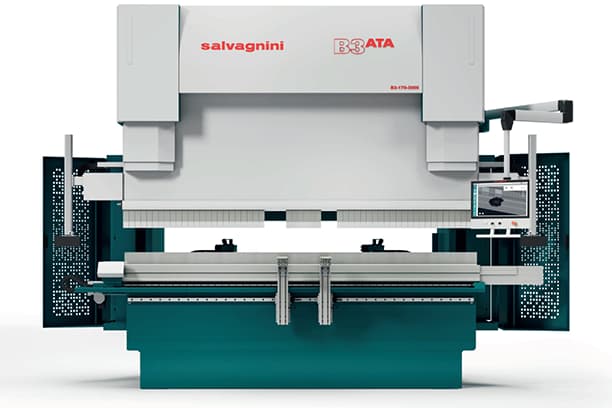
9. TRUMPF
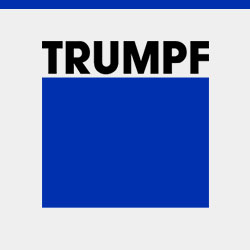
TruBend machines integrate extensive experience in press brake technology with pioneering innovations, allowing you to manufacture parts of any complexity with precision and economy.
They are particularly known for their versatility, exceptional quality of finished parts and good value for money.
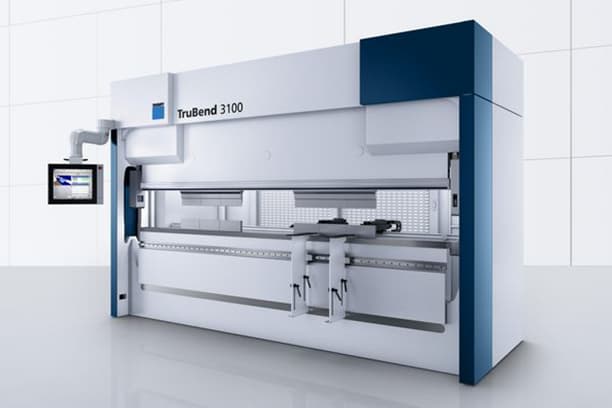
10. USSRVIKEN

Ursviken provides power and productivity for working with heavy sheet metal, as well as ensuring efficiency, precision, flexibility and high quality when working with lighter materials. All of its machines are designed to meet the demanding needs of its customers.
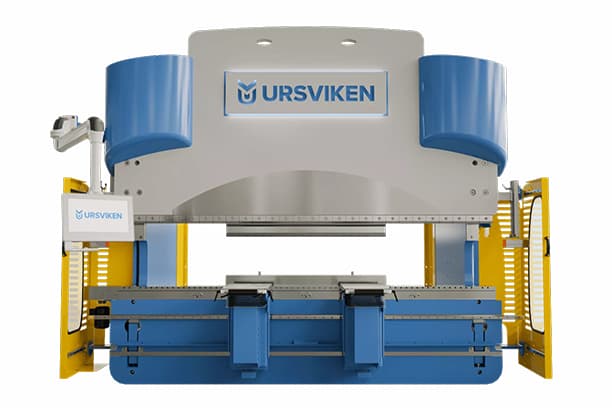
4. Key considerations when selecting a press brake manufacturer
Here are some important considerations when selecting a press brake manufacturer to ensure you get a high-quality, reliable machine that meets your specific needs:
Experience and reputation
- Look for an established manufacturer with many years of experience designing and building press brakes. Longevity in the industry is a good sign that they produce reliable machines.
- Research the company's reputation by reading customer reviews, case studies, and testimonials. A pattern of positive customer feedback is important.
Machine quality and capabilities
- Evaluate the quality of the manufacturer's press brakes in terms of construction, components, accuracy and reliability. Well-built machines with quality parts will have a longer lifespan.
- Make sure the manufacturer offers press brakes with the tonnage, bed length and features needed for your specific bending materials and applications.
Technology and inovation
- Look for a manufacturer that incorporates the latest press brake technologies to improve performance, accuracy, efficiency and ease of use. This includes features like CNC controls, laser angle measurement, automatic crowning, etc.
- Evaluate whether the manufacturer is investing in R&D and continually improving its press brake designs.
Service and support
- Select a manufacturer that provides fast, experienced technical service to minimize downtime if you experience problems with your press brake.
- Make sure they offer convenient access to spares and replacement parts.
- See what operator training and resources the manufacturer offers to help you optimize equipment use.
Price and Value
- Compare prices among top manufacturers, but don't sacrifice quality and features to save money upfront. Investing in a reliable, high-quality press brake will pay off in the long run.
- Assess the total value in terms of performance, efficiency gains and uptime that a quality machine delivers.
By carefully evaluating press brake manufacturers based on these key factors, you can select the right partner to provide a machine that will deliver high-quality bending results and reliable performance for years to come. Take the time to research and compare options to make an informed investment in your business.
V. Final Considerations
Many people are curious about the world's top CNC press brake manufacturers or top 10 CNC press brake manufacturers. However, few of them will choose the best bending machine in the world due to its high cost. The high cost of a press brake does not necessarily indicate its quality. The high price is usually due to factors such as high labor costs, steel prices, and component prices.
If you are on a tight budget or looking for an economical option, I recommend considering press brake manufacturers in China. They not only offer good quality but also competitive prices. This is due to China's dominance in steel production, machine tool consumption and machine tool manufacturing.
In fact, many well-known press brake brands are manufactured in China, either through their factories or through OEM agreements with Chinese manufacturers. Therefore, regardless of whether you buy a press brake from Germany, Italy or China, you will receive the same quality product.
However, buying from non-Chinese manufacturers or so-called famous brands often carries a higher price.
When choosing a press brake machine, there are several factors to consider, and this buying guide aims to provide information on how to make an informed decision.
Additionally, the press brake die guide can help you choose the right punches and dies for your sheet metal manufacturing needs.