With the advent of large-scale equipment and the increasing use of steel instead of cast materials, ultra-thick sheets have become increasingly prevalent in equipment manufacturing.
Flame cutting is the initial step in the manufacturing and processing of structural components.
Given the irreversible nature of flame cutting, the CNC flame cutting process for ultra-thick sheets has become a crucial technology for large equipment manufacturers.
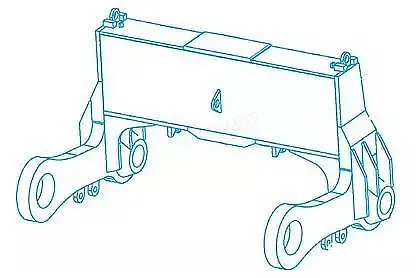
figure 1
1. Features of flame cutting of ultra-thick sheet metal
Oxygen and acetylene for cutting ultra-thick sheets
Cutting ultra-thick sheet metal parts requires a large amount of oxygen and acetylene, as these parts are generally larger. To ensure a smooth and efficient cutting process, it is crucial to have a continuous and stable supply of these gases.
Large size and weight of ultra-thick boards
For example, a sheet measuring 220 mm x 2,200 mm x 8,000 mm thick weighs approximately 30 tons. Furthermore, the weight of the individual parts can be quite substantial, with the number 9 steel plate of the upper connecting rod, for example, weighing over 4 tons (see Figure 1).
Risk of cutting defects
Ultra-thick sheets are more prone to cutting defects such as water-tight cutting compared to normal sheets.
Large loss of material scrap
The significant loss of material during the edging process of ultra-thick sheets makes it difficult to reuse the cut edges.
Cutting Distortion
The heat generated during the cutting process can cause deformation of the steel sheet and result in deviation from the desired dimensions. Furthermore, sudden rebound of the plate under high voltage can lead to safety hazards. To avoid these quality and safety issues, it is essential to consider cutting distortion when formulating the cutting process.
2. Ultra-thick sheet cutting section is prone to quality defects
(1) Cutting defects on the upper edge
The top edge of the cut crumbles or falls off in the form of melted threads, resulting in the rounded corners collapsing due to the top edge of the slit melting too quickly.
Possible Causes:
- Thick refractory scale on the steel surface;
- Slow cutting speed and excessive preheating flame;
- Incorrect height between the cutting nozzle and the workpiece, large size of the cutting nozzle and excess oxygen in the flame.
As illustrated in Figure 2.
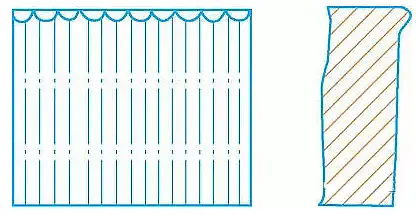
Figure 2
(2) Poor flatness of the cutting surface
① There is a concave defect under the edge of the cut section (see Figure 3). Furthermore, the upper edge shows varying degrees of melt collapse.
This can be attributed to high cutting oxygen pressure or excessive height between the cutting nozzle and the workpiece, as well as a clogged cutting nozzle that causes wind interference.
② The cutting section has excessive roughness.
This may be due to excessive cutting speed or impurities in the steel plate that impact its formation.
As shown in Figure 3.
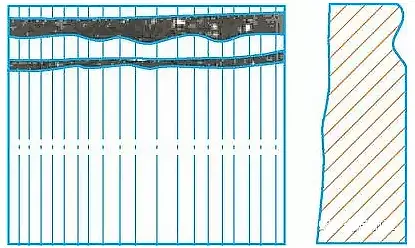
Figure 3
(3) Poor Verticality
① The width of the cutting seam varies, being narrow at the top and wide at the bottom or vice versa, due to a fast or slow cutting speed, a clogged cutting nozzle interfering with the wind line, and inadequate cutting oxygen or excessive which leads to insufficient or excessive burning of the metal.
② The cutting torch creates an oblique angle that is not perpendicular to the surface of the workpiece, or the wind line is incorrect.
(4) Lower Edge Cut Defects
① There is a depression near the bottom edge, and the bottom edge melts into rounded corners due to a fast cutting speed, a clogged or damaged cutting nozzle, and a blocked or deteriorated air line.
② Removing slag on the cutting surface or bottom edge is difficult due to factors such as fast or slow cutting speed, small cutting nozzle, low cutting oxygen pressure, excess gas in the preheating flame, plate surface corroded or dirty steel, excessive height between the cutting nozzle and the workpiece and a strong preheating flame. Additionally, a high alloy content can result in slag formation in the cross section and bottom edge (see Figure 4).
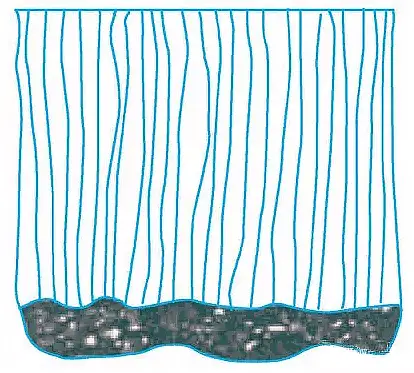
Figure 4
(5) Cracks
Microcracks appear in the cutting section or heat affected zone due to high carbon equivalent in the steel plate which results in high crack sensitivity along with lack of adequate preheating and slow cooling measures.
(6) Deformation
Local heating of the steel sheet during cutting causes deformation due to material displacement, leading to dimensional deviation of the cut pieces and affecting their quality.
As illustrated in Figure 5.
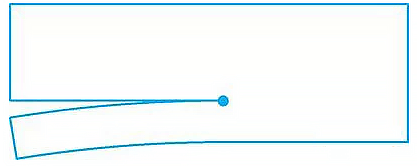
Figure 5
3. Cutting process
(1) Cutting off the gas supply system
To maintain a consistent and reliable supply of oxygen and acetylene gas, several gas cylinders can be used in parallel. This will ensure a stable and uninterrupted flow of acetylene gas.
A parallel gas supply package can be created as shown in Figure 6. A φ100 mm steel tube is used as an airbag and both ends are securely welded with steel plates.
Six air inlet tubes and one air outlet tube are drilled into the steel tube, taking care to ensure proper welding quality and preventing air bag leaks.
A gas-tight ball valve and connecting device must be added to each air inlet and outlet.
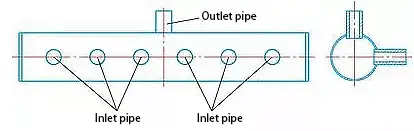
Figure 6
(2) Cutting support structure
Due to the large size and weight of the thick plate, which has a maximum weight of 30 tons, and the substantial size and weight of the individual parts, with a maximum weight of 4 tons, the supporting structure of the original CNC cutting machine cannot meet the cutting requirements as it provides insufficient support for the slats (as shown in Figure 7a).
To ensure stable support of the structure, modifications to the supporting structure are required. After careful analysis, research and discussion, it was decided to use H-shaped waste steel as the thick plate support structure.
(A) Support structure before transformation
(B) Support structure after transformation
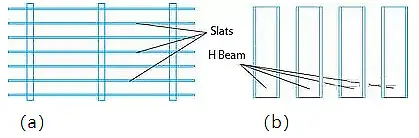
Figure 7
(3) Cutting Program Optimization
Initially, exit point processing is introduced.
The biggest challenge when cutting ultra-thick plates (up to 220mm) is ensuring a quality cut, especially in positioning the entry and exit points of the pieces, which often leads to cutting defects.
As illustrated in Figures 8a and 8b, the cutting points of thick plates are often not vertical.
When the cutting point coincides with the entry point, if the cutting line rotates at this time, the root will not be cut, causing defects due to fractures due to the weight of the parts.
To prevent such defects from occurring, optimizing the input and output in the cutting process can be an effective solution.
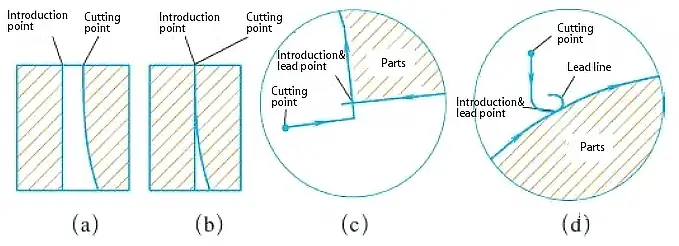
Figure 8
Secondly, if proper care is not taken with the direction during the cutting process, it may cause deformation of the parts. This is because the expansion force will push the part apart, leading to inconsistencies in part size and program size.
To solve this problem, our analysis suggests that when cutting steel sheets, the light weight results in low pressure and minimal friction with the support structure, causing the part to be pushed by the expansion force. On the other hand, the heavy weight produces high pressure and significant friction with the support structure, preventing it from being pushed by the expansion force.
It is important to take this into account when writing the program. During the cutting process, the part must be as closely connected to a heavy part as possible.
Based on this principle, the unloading, cutting sequence and cutting direction of the upper connecting rod are depicted in Figure 9.
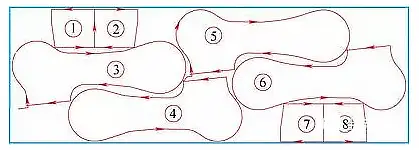
Figure 9
Finally, optimizing the layout can save greater costs by optimizing the size.
When designing the program, more time can be allocated to optimizing the layout. It is best to use any remaining material, and multiple people can collaborate to check the size of the part and generate the program after confirming its accuracy.
To cut thicker parts, the torch model, cutting nozzle number and oxygen pressure must be increased.
The oxygen pressure and thickness of the cutting piece, cutting torch model and ultra-thick sheet cutting parameters should be selected based on field equipment, cutting experience and the attached table.
Parameters for oxyacetylene flame cutting of ultra thick plate
Thickness | Cutting nozzle diameter | Oxygen pressure | Acetylene pressure | Preheating time | Cutting speed | gas flow |
---|---|---|---|---|---|---|
mm | mm | MPa | MPa | It is | mm/min | L/min |
180 | 5 | 1.0-1.4 | 0.09-0.11 | 30-35 | 145-165 | 17-20 |
200 | 5 | 1.0-1.4 | 0.09-0.11 | 30-35 | 140-165 | 20-23 |
220 | 5 | 1.0-1.4 | 0.09-0.11 | 30-35 | 135-155 | 22-25 |
(4) Cutting performance
Cutting the steel plate must be done correctly on the first try.
Start by cutting the discarded corners of the steel sheet, adjusting the cutting air line and ensuring that the cut section does not have any of the defects mentioned.
It is important to closely monitor the cutting process and quickly resolve any problems that arise.
4. Conclusions
With proper preparation and a well-defined cutting process, cutting ultra-thick slabs has consistently achieved success in a single attempt. The quality and appearance of the cut products meet the process requirements, resulting in the production of qualified parts (as shown in Figure 10).
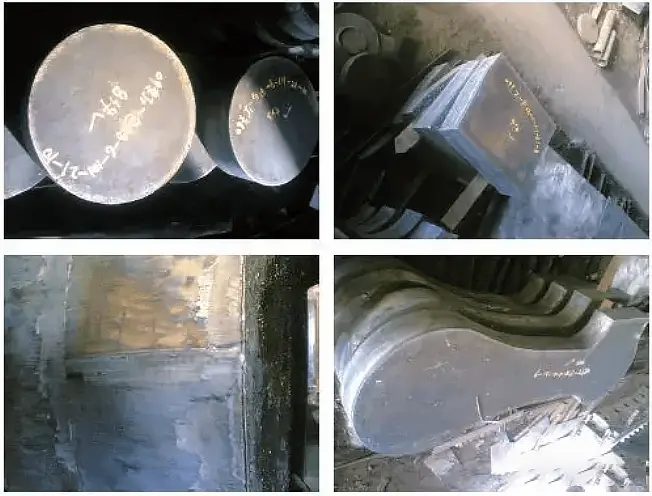
Figure 10
The process of producing ultra-thick steel sheets by flame using current equipment has been established, providing a technical basis for manufacturing similar products.