Metal die casting is a systematic process used to produce a wide range of metal parts. This technique facilitates the production of strong, precise and lightweight metal components at a lower cost. Parts or components manufactured by the pressure casting process facilitate the production of consumer and industrial components.
Although metal pressure casting is a flexible production process, it is advisable to have a good understanding of the technique before applying it yourself or hiring companies that offer related services. What is pressure casting, how does pressure casting work, and what are the different types and benefits? Read more to find out.
What is pressure casting?
Pressure casting involves pressing molten metal into a mold under high pressure. A hydraulic press, which ensures that the closing surfaces meet almost perfectly and form a seal, compresses the hardened steel parts that make up the cavity.
Metal pressure casting allows the production of precision metal parts with excellent surface finish and precise dimensions. It is ideal for large-scale product manufacturing as it can be used to create complex parts.
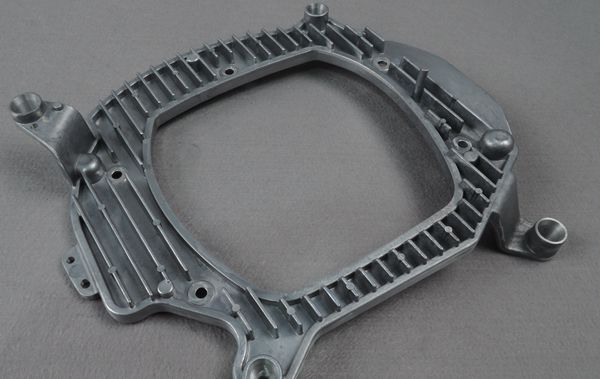
What metal materials are used in pressure casting?
The choice of metal for die casting depends on the requirements of the specific application. For example, aluminum is often used to manufacture automotive components due to its light weight and corrosion resistance. Let's look at the different metal materials used in die casting.
aluminum
Aluminum is a primary die casting metal used in alloys for the cold chamber die casting process. These aluminum alloys typically contain elements such as magnesium, copper and silicon.
Aluminum-based die casting alloys are an excellent choice for complex, detailed parts because they are lightweight and provide excellent dimensional stability. They are robustly resistant to temperature fluctuations, corrosion and electrical and thermal conductivity. Here are some commonly used aluminum alloys for die casting.
- Aluminum Alloy 380 : 380 is a general purpose aluminum alloy with a balance between castability and mechanical properties. It is widely used to make motor mounts, furniture, electronic enclosures, frames, handles, gears, power tools and more.
- B390 aluminum alloy : This alloy has exceptional resistance to vibration and wear. It is commonly used for pump casings, valve bodies and impellers.
- Aluminum alloy 413 : It has excellent casting properties thanks to its compressibility at high pressure. AL413 is widely used in the production of architectural parts, food machinery and hydraulic cylinders.
- Aluminum Alloy 443 : Of all the aluminum alloys used in die casting, AL443 offers the best ductility. This makes it perfect for consumer products, especially those that require plastic deformation after casting.
magnesium
Magnesium is another popular choice for die casting. Other elements in magnesium alloys include aluminum, zinc, manganese and silicon. In addition to being lighter than aluminum, it is also more machinable, making it suitable for objects that require additional machining or surface finishing after casting.
Cast magnesium alloys are easier to cast compared to metals such as aluminum, mainly due to their suitability for the hot chamber die casting process. Here are some typical magnesium alloys used in die casting.
- AZ91D : An ideal combination of high strength-to-weight ratio, great corrosion resistance and castability makes this alloy popular for powertrain components and mechanical parts.
- AM60 : A combination of strength, ductility, vibration damping and good moldability makes AM60 the first choice for automotive parts such as body panels and seat frames.
- AS41B and AE42 : These unique rare earth alloys exhibit high temperature resistance and offer excellent creep resistance, corrosion resistance and ductility. But they are expensive.
zinc
Zinc alloys make up a significant proportion of cast metals. They facilitate manufacturing, are suitable for casting in a hot chamber die casting machine and offer additional advantages such as impact resistance, ductility and suitability for coating. Here are some typical alloys used in zinc smelting.
- Zamac 3 : A general purpose zinc alloy known for its dimensional stability and ease of casting. Zamak 3 is used in the manufacture of hydraulic parts and ceiling fans.
- Zamac 2 : Enriched with additional copper, this alloy is slightly more expensive but offers greater strength.
- Zamak 5 : Zamak 5 is a zinc alloy similar to Zamak 3, but offers less ductility and greater tensile strength. Therefore, it is the preferred alloy for products such as wheel balancing weights.
Steps of the pressure casting process
In die casting, high pressure is essential for injecting molten metal into a die. The multi-stage processes in die casting are listed here.
1. Create a shape
First, computer-aided design (CAD) software is used to design the shape of the die. This software allows the creation of a three-dimensional (3D) model of the matrix shape. Once the design is complete, the actual shape of the matrix can be created. The shape is carved from a block of metal on a CNC machine. After cutting, the shape usually needs to go through a heat treatment process to harden it.
2. Clamps
Clamping is the first step in die casting. To ensure efficient injection and removal of the solidified product, it is important to pre-lubricate and clean the mold to remove all contaminants. Once cleaned and lubricated, apply strong pressure to secure and close the mold.
3. Occupation
To inject, molten metal must be poured into the injection chamber. This step varies depending on the process used. For example, in cold chamber pressure casting and hot chamber pressure casting. It is important to note that this step requires high pressure generated by a hydraulic system.
4. Cooling
After the casting has hardened, it must be cooled and removed from the mold. This step is important to maintain the structural integrity of the casting. At this stage of die casting, manufacturers typically use forced or natural cooling. However, the type of cooling generally depends on the size and complexity of the casting.
5. Expectoration
After cooling, manufacturers use ejector pins to eject the casting from the mold chamber and remove it from the mold. Make sure the final product is solid before ejecting it.
6. Cut
The final step involves removing any excess metal that may be present in the sprue and sprue of the finished product. Cutting can be done with a saw, grinder, cutting tool or other tools. The beauty of this process is that the removed parts can be recycled and reused. To avoid damage to the casting, great attention and care must be taken during this process.
Types of pressure casting and their variations
The two methods commonly used in die casting are hot chamber and cold chamber techniques. Each is unique and suitable for different scenarios. Below you will discover what these two categories of procedures include:
Hot chamber pressure casting
The hot chamber pressure casting process is ideal for low melting point materials such as magnesium, tin, zinc and lead alloys. This prevents the pump from being damaged, which can happen if it comes into contact with metals or alloys with a higher melting point. Molten metal is injected into the mold by applying pressure from a hydraulic system.
Cold chamber pressure casting
Cold chamber pressure casting is the ideal method when working with materials with a high melting point, such as aluminum. Because the high temperatures required to melt these materials can damage the pump system, this process is perfect for these metals.
This is a pressure casting process in which molten material is poured into a cold chamber and then injected into the mold. The hydraulic system used in a cold runner process is similar to that used in a hot runner process. However, higher pressure between 2,000 and 20,000 psi may be required.
Different variants of die casting
To correct defects, mishaps, distortions and other problems that may arise during the casting process, the following variations were adapted.
Semi-Solid Die Casting (SSDC)
In this process, also known as thixoforming, the discharge made up of small pieces is heated to the liquid-to-solid phase transition temperature (thixotropic state). This allows the material to be guided into the cavity using pressure. Because most of the melt expands during or shortly after the phase transition, this process minimizes shrinkage, reduces processing times, and increases accuracy due to the lower operating temperature.
Vacuum Casting
This is a special method to produce high-quality metal parts with greater precision. The charge is sucked into a tool placed above the melting vessel, with a vacuum being directed into the cavity. They remove air and gases from the mold before the hot metal is poured into it. This makes the parts better and more accurate.
Vacuum casting is commonly performed with aluminum and magnesium. It helps produce robust, detailed parts used in cars, planes and electronic devices.
cast
This process involves filling the tool and then squeezing it, forcing the filler into small cavities that are not normally easily filled. This casting is ideal for use with high viscosity metals such as zinc, nickel and copper.
Gravity or low pressure casting
This less complicated process reduces tooling costs and equipment complexity because parts with thicker sections can be cast using low-pressure gravity casting (or even by hand). Ideally, this process should be used with symmetrical, round cast aluminum components.
Advantages and limitations of the pressure casting process
Pressure casting is one of the fastest and most economical production methods. A single mold can produce hundreds of thousands of precise, dimensionally perfect parts. Below are some advantages and limitations of die casting.
Advantages of the pressure casting process
Good mechanical properties: Pressure casting produces parts with good mechanical strength, but not as strong as forged parts. Furthermore, parts can be produced with better conductivity, hardness and durability.
- Excellent finish : Pressure casting allows you to quickly produce complex parts with a smooth or textured surface, depending on your needs.
- Fast lead time : Once the mold is completed, the average die casting cycle is quite short, usually lasting just a few days, depending on the size and material properties.
- Cost-effective : Pressure casting is extremely cost-effective, especially when producing large quantities. The cost per part decreases significantly over time.
Limitations of the Die Casting Process
- Limited use of materials : The pressure casting process uses only metals with high fluidity, which limits the amount and type of materials that can be used in the process.
- Labor intensive : The process, especially during the cooling phase, requires constant monitoring and control.
- Immutable Dies : Since the dies are made of hardened steel, they cannot be changed or adjusted. They are also expensive to produce.
Factors to Consider When Designing Die Casting Geometry
The geometry of cast designs determines how parts are filled and cooled and how their shape affects porosity, grain, and stress. Here are the factors to consider when designing die casting geometries.
Sketch
In die casting, a draft is a slope or taper parallel to the direction of the mold. The taper on the inside of the mold walls must be greater than the taper on the outside walls because this allows the alloy to shrink and blend better with the casting as it cools and solidifies. When the internal draft is greater, the finished part is easier and needs to be ejected from the mold.
Ribs and projections
Generally, bosses are used as attachment points and spacers, while ribs are added to provide support without thickening the wall. Whenever possible, incorporate all necessary projections and ribs directly into the casting. This increases the overall strength of the product while reducing sharp corners.
Scholarships
Cast designs provide pockets when your piece needs to be lightweight. These pockets, also known as metal protectors, are essentially holes or open areas built into the die design. Well-placed pockets allow your finished piece to be lighter without compromising structural integrity.
Wall thickness uniformity
Ideally, the design should result in consistent wall thicknesses throughout the casting. This does not mean that the thickness must be the same everywhere, but significant differences in wall thickness must be minimized. A uniform thickness makes it easier to control the flow of metal in the mold and ensures complete filling.
fillets and corners
Fillets, the curved sections of casting where two surfaces meet, usually at an acute angle, are added to a casting to avoid unwanted sharp edges and corners in the finished product. Large inner and outer corner radii are an advantage for casting.
Tips for creating high-quality metal castings
Die casting involves injecting molten material into a mold. However, to obtain optimal quality of parts, consider the following tips.
Use high quality metals
The quality of your cast products largely depends on the materials used. Choose high-quality alloys suited to your application and ensure they are free from impurities and impurities. Additionally, for optimal performance and consistent material properties, properly calibrate your die casting machine.
Optimize array design
Optimizing your die design is one way to ensure high-quality products. Factors such as wall thickness, draft angles and fillets must be considered to ensure that your part can be easily ejected from the mold. Also consider the positioning of gates and runners to ensure that molten metal can easily enter the cavity and does not leave gaps or defects.
Quality control
Implement efficient quality control procedures in the production of high-quality pressure castings. This includes keeping an eye on process parameters, checking parts for errors, and acting accordingly if necessary. To identify trends and make data-driven decisions, you should also consider implementing statistical process control (SPC) techniques.
Surface Finish Options for Pressure Casting
To ensure longevity, protection or attractive appearance, castings must have a good external finish. Various finishing options are available for castings.
Powder coating
Powder coating involves applying charged particles to the surface of the casting. This method is ideal because it is uniform, provides greater control over thickness, and hides small imperfections in the cast surface.
Coating
Another way to give castings an attractive surface finish is coating. As with ceramic coating, the surface here consists of a thin layer. Both coating processes can improve the product's aesthetics and sometimes its conductivity.
Antiques
This type of surface treatment is best suited for zinc casting and gives the casting an aged appearance. This involves coating the casting with a colored material, such as copper sulfide, after it has been electroplated with copper or other alloys.
painting
For many materials it serves as additional protection or simply for decoration. Before applying the paint, the ideal is to clean the metal surface to remove impurities such as oil and apply a primer to improve adhesion.
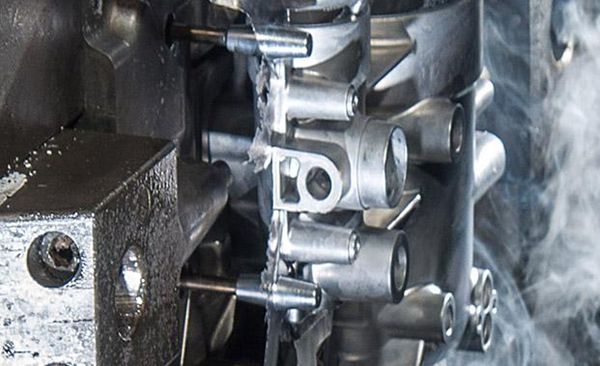
Die casting products in various industries
Die casting is a process used to create a variety of highly functional and truly unique parts. Here are some uses of these products.
- Automobile industry : This technology is used to produce gearboxes, miniature engines, gears, and other specialized parts needed by the automotive industry.
- Aerospace : The aerospace industry demands high-quality, lightweight metal components that meet strict quality standards. Die casting is a cost-effective way to meet this requirement.
- Consumer and industrial products : This process can be used to produce consumer parts such as heat sinks, connecting rods, compressor pistons, and kitchen sink faucets.
WayKen: Your Reliable Die Casting Service Provider
Concluding
Many of our products are manufactured using the die casting process. Die casting's ability to produce high-precision metal parts and components is beneficial to multiple industries.
Common questions
What types of pressure casting molds are there?
There are four types of die casting molds. These include single-cavity molds, multi-cavity molds, combination molds, and unitary molds.
What is the difference between injection molding and pressure casting?
A fundamental difference between these two processes is the materials used. Die casting is mainly used for metals such as zinc, aluminum and magnesium, while injection molding is often used for plastics, rubber and certain metals.
Can pressure casting be used for prototype manufacturing?
Yes, pressure casting can be used for prototype manufacturing. It provides a way to test the functionality of a part before full production, especially for parts made from low melting point metals.
How much does pressure casting cost?
Aluminum die casting prices can vary significantly depending on a variety of factors, including the complexity of the part, its size and production volume.