Threaded connections, a widely used and removable fastening method, are simple in structure, reliable and easy to assemble and disassemble. They are one of the most widely used and widest connection methods in sheet metal product structures, possessing irreplaceable advantages.
Common riveting methods for threaded fasteners in sheet metal parts include pressure riveting, expansion riveting, and pull riveting.
1. Principles for Rivet Selection
1) Pay attention to the outer dimensions of the rivet to avoid interference.
2) Depending on the riveting method of the rivet, consider the direction of force applied to the rivet during assembly to avoid pullout incidents.
3) The length of the rivet section should be slightly less than the thickness of the sheet, determined based on the thickness of the sheet.
4) When choosing rivets, consider the riveting method and leave space for the riveting operation.
5) As the base plate deforms during press riveting and the connection deforms during expansion riveting, for stainless steel or materials with higher hardness, choose the expansion riveting method.
6) For base plates less than 1 mm thick, pressure riveting should be avoided. If there are special requirements, use the expansion riveting method.
7) Swell rivets are safer than push rivets and should be used unless there are special requirements.
8) For base plates thicker than 3.0mm, hexagonal head snap rivets should be avoided. Use round head rivets to ensure flatness after riveting.
9) When choosing press rivets, please note: M5 and below round head press rivets are suitable for riveting sheets with a thickness between 1.0 ~ 2.0 mm; M6 round head rivets are suitable for riveting sheets with a thickness between 2.0 ~ 2.5mm; M8 round head rivets are suitable for riveting sheets thicker than 2.5mm.
2. Structural Forms and Riveting Process of Riveted Components
Common structural shapes of riveted components include snap rivet nut columns, snap rivet nuts (studs), expandable rivet nuts (studs), pull rivet nuts, floating snap rivet nuts, and more.
(1) Press the rivet nut column
Also known as pressure rivet or nut column, it is a type of fastener widely used in sheet metal, thin plates, chassis and cabinets. There is no specific national standard for pressed rivet nut columns. The column base of the pressure rivet nut is hexagonal, and the other end is cylindrical, with a groove in the middle of the hexagonal base and the cylinder.
Press riveting is performed in a special press using a mold, applying a certain pressure to press the hexagonal head into a pre-defined hole in the plate (the diameter of the pre-defined hole is usually slightly larger than the outer diameter of the cylinder pressure rivet nut column).
This causes plastic deformation around the hole, with the deformed portion being compressed into the groove of the snap rivet nut post, thus riveting the snap rivet nut post firmly to the plate. This type of riveting generally requires the hardness of the pressure rivet nut column to be greater than the hardness of the thin plate.
Common low carbon steel plates (hardness less than 70HRB), aluminum alloy plates, copper plates, etc. are all suitable for pressed rivet nut columns. For stainless steel plates and high-carbon steel plates, due to their hard material, special high-strength pressed rivet nut columns are not only expensive, but also difficult to press, unreliable in riveting, and easy to fall off .
To ensure the reliability of riveting, it is often necessary to weld 2 to 3 points on the side of the pressed rivet nut column, so the process is poor. If the product is to be riveted with stainless steel and high carbon steel sheets, the hardness of the steel sheet should be less than 80HRB.
Therefore, sheet metal parts with columns of pressed rivet nuts should avoid using stainless steel plates. The same applies to pressure rivet bolts and pressure rivet nuts, which are not suitable for use on stainless steel plates. The press riveting process of the press rivet nut column is shown in Figure 9-1.
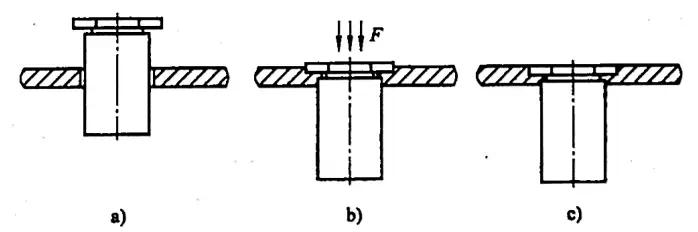
- a) Initial state
- b) Deformation process
- c) Completion of riveting
(2) Press the rivet nut
Pressed rivet nuts are also a type of fastener widely used in sheet metal, thin plates, machine housings and cabinets.
There is currently no specific national standard for pressed rivet nuts. They differ from snap rivet nut columns in that they have added serrated steps and inverted heads, appearing circular in shape. The riveting principle of pressing rivet nut is the same as that of pressing rivet nut column. The riveting process of the pressure rivet nut is shown in Figure 9-2.
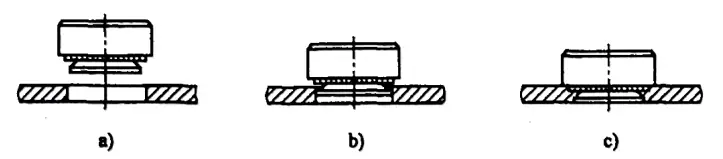
- a) Initial state
- b) Deformation process
- c) Completion of compression
(3) Swollen rivet nut
Expandable rivet nut is a type of fastener used in metal sheets, thin plates, machine cases and cabinets. Currently, there are no specific national standards for intumescent rivet nuts. There are two types of rivet nuts: hexagonal and round.
Before installing the expandable rivet nut, a bottom hole must be pre-defined in the sheet metal. Then the expandable rivet nut is inserted into the hole. In a special press, using a mold (with a cone in the upper head of the mold), a certain pressure is applied to expand part of the swollen rivet nut handle (causing part of the material to undergo plastic deformation).
This forms a certain taper, causing the swollen rivet nut to fit perfectly into the metal sheet, thus fixing the swollen rivet nut to the thin plate, completing the riveting. The swollen rivet nut generally does not need to be hardened to ensure its toughness, ensuring that it can be tightened without cracking.
The riveting process is relatively simple, but because the connection between the swollen rivet nut and the sheet metal is a deformed connection in the circumferential direction, it can withstand a larger expulsion force, but the torque it can withstand is smaller.
To compensate for this deficiency, it is recommended to use hexagonal corrugated rivet nuts with reverse buckles or round corrugated rivet nuts with serrations. The bite between the reverse or serrated buckle and the sheet metal increases the torque that the expandable rivet nut can withstand. The expansion process of the rivet nut is shown in Figure 9-3.
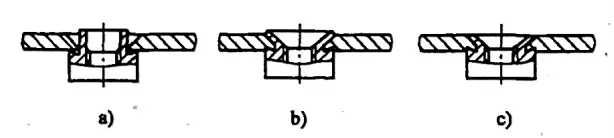
- a) Initial state
- b) Cold disruptive deformation
- c) Completion of stamping
(4) Rivet nut
Also known as rivet nut or rivet cap, it is commonly used to fasten various sheet metal parts. Riveting refers to the process in which the rivet nut, under the influence of external pulling force, locally undergoes plastic expansion deformation (generally in specially designed locations) to fix the sheet metal, thus achieving a reliable connection.
The riveting process method involves the use of a specialized riveting gun. The riveting gun drives the screw in its head to rotate through engagement with the internal thread of the rivet nut, leading to corresponding linear movement of the rivet nut and causing the thin-walled area of the rivet nut to expand and expand. deform until it holds the sheet.
When fixing the plate through local deformation, the rivet nut can withstand a large expulsion force and a certain amount of torque. Sometimes, to ensure the ability to withstand large torque, hexagonal or serrated rivet nuts may be used. The advantage of rivet nuts is the one-sided construction, not affected by the closing of the product. The riveting process of the rivet nut is shown in Figure 9-4.
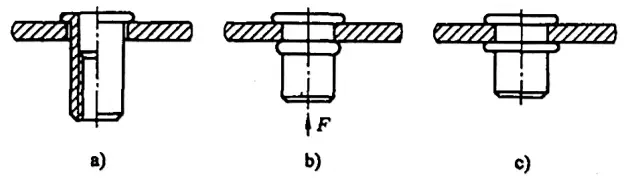
- a) Initial state
- b) Deformation under tension
- c) Completion of Riveting
1) Common materials for rivet nuts include steel, aluminum alloy and stainless steel. Varieties include flat head rivet nuts (GB/T17880.1-1999), countersunk rivet nuts (GB/T17880.2-1999), small countersunk rivet nuts (GB/T17880.3-1999), 120° small countersunk rivets (GB/T17880.4-1999) and flat head hexagonal rivet nuts (GB/T17880.5-1999).
2) The use of rivet nuts: if a product requires the nut to be mounted externally while the internal space is narrow, preventing the riveting machine head from entering for riveting, and methods such as flanging and threading cannot meet the requirements of resistance, then neither pressing nor expanding riveting will work, necessitating the use of tension riveting. Rivet nuts are suitable for connecting sheet metal parts with a thickness between 0.5 and 6m.
(5) Floating Rivet Nuts
Sheet metal products, such as cabinets and computer cases, are typically made up of many parts. Some sheet metal parts or components, due to the complex overall structure of the boxes or enclosures and large cumulative assembly size errors, result in significant deviations in the mounting position of the rivet nuts, making the assembly of other parts difficult, and in some cases, impossible.
Therefore, using floating rivet nuts in certain positions instead of other types of rivet nuts can significantly improve this situation. The riveting process of floating rivet nut is shown in Figure 9-5. There are currently no national standards for floating rivet nuts, only industry standards. When choosing to use them, the predefined hole size and installation space must be determined according to the manufacturer's product samples.
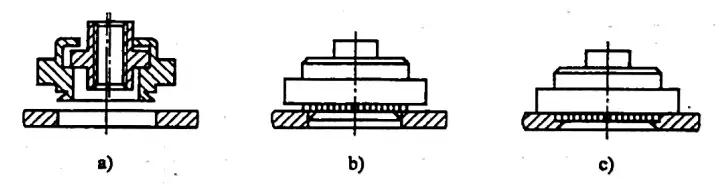
- a) Initial state
- b) Deformation Process
- c) Completion of Press Riveting
(6) Dimensions of the bottom hole of the riveted part and thickness of the applicable plate
1) For the bottom hole diameter of the pressure riveted nut pillar, see Table 9-1.
Table 9-1 Bottom hole diameter of pressure riveted nut pillar (Unit: mm)
Thread Specifications | Code name | Base hole diameter d |
M3×0.5 | (B)S0(0)(S)-M3-H | φ4.2 |
M3×0.5 | (B)S0(0)(S)-3.5M3-H | φ5.4 |
M4×0.7 | (B)S0(0)(S)-M4-H | φ6.0 |
M4×0.7 | (B)S0(0)(S)-3.5M4-H | φ7.2 |
M5 ×0.8 | (B)S0(0)(S)-M5-H | φ7.2 |
M6×1.0 | (B)S0(0)(S)-M6-H | φ8.7 |
Note: S0 S0S denotes columns of pressed rivet nuts without threads and with a through hole; S00 S00S denotes through-thread pressure rivet nut columns. Adding a B before the term indicates a blind hole; adding an S at the end means the material is stainless steel, and without an S it is steel. H represents the height of the nut column.
2) Refer to Table 9-2 for pressure riveted nut bottom hole diameter.
Table 9-2: Bottom hole diameter of pressure riveted nut (Unit: mm)
Thread Specifications | Code name | Base hole diameter d |
M2x0.4 | S(CLS)-M2-A(0,1,2) | φ4.2 |
M2. 5 × 0.45 | S(CLS)-M2.5-A(0,1,2) | φ4.2 |
M3x0.5 | S(CLS)-M3-A(0,1,2) | φ4.2 |
M4x0.7 | S(CLS)-M4-A(0,1,2) | φ5.4 |
M5×0.8 | S(CLS)-M5-A(0,1,2) | φ6.4 |
M6×1.0 | S(CLS)-M6-A(0,1,2) | φ8.7 |
Post: CLS means a rivet nut made of stainless steel; S represents a steel rivet nut; A (handle code) indicates the applicable thickness code for the rivet nut (0 indicates a thickness of 0.8-1.2 mm, 1 indicates a thickness of 1-1.5 mm, 2 indicates a thickness of 1 .5 ~ 2.5mm).
3) Refer to Table 9-3 for the bottom hole diameter of the recessed nut.
Table 9-3 Bottom hole diameter for recessed nut (Unit: mm)
Thread Specifications | Code name | Base hole diameter d |
M2x0.4 | F(S)-M2-A | φ4.3 |
M2.5×0.45 | F(S)-M2.5-A | φ4.3 |
M3x0.5 | F(S)-M3-A | φ4.3 |
M4x0.7 | F(S)-M4-A | φ$7.4 |
M5x0.8 | F(S)-M5-A | φ7.9 |
M6x1.0 | F(S)-M6-A | φ8.7 |
Note: “F” indicates a pressure nut; “S” means the material is bronze; “A” (handle code) represents the applicable plate thickness code for the lock nut.
4) Refer to Table 9-4 for proper plate thickness for lock nut.
Table 9-4: Applicable Plate Thickness for Pressed Nut (Unit: mm)
Handle code A | Thread Specifications | |||||
M2 | M2.5 | M3 | M4 | M5 | M6 | |
1 | 1.5-2.3 | 1.5~2.3 | 1.5-2.3 | 1.5-2.3 | 1.5-2.3 | |
two | 2.3-3.2 | 2.3-3.2 | 2.3-3.2 | 2.3-3.2 | 2.3-3.2 | |
3 | 3.2-3.9 | |||||
4 | 4~4.7 | |||||
5 | >4.7 |
5) For the diameter of the bottom hole of the stamped nut, see Table 9-5.
Table 9-5: Stamped nut bottom hole diameter (Unit: mm)
Thread Specifications | Code name | Base hole diameter d |
M2.5×0.45 | Z-(S)-M2.5-A | φ5.0/Reaming φ5.5×90° |
M3x0.5 | Z-(S)-M3-A | 5.0/Reaming φ5.5×90° |
M4x0.7 | Z-(S)-M4-A | φ6.0/Reaming φ7.0×90° |
M5×0.8 | Z-(S)-M5-A | φ8.0/Reaming φ9.0×90° |
M6x1.0 | Z-(S)-M6-A | φ9.0/Reaming φ10×90° |
M8×1.25 | Z-(S)-M8-A | φ11/Reaming φ12×90° |
Note: The addition of 'S' means the material is stainless steel, while the absence of 'S' indicates the material is steel. 'A' (handle code) represents the code for the applicable sheet thickness of the rivet nut.
6) The applicable plate thickness for round expansion rivet nuts is shown in Table 9-6.
Table 9-6: Applicable sheet thickness for round expansion rivet nuts (Unit: mm)
Handle code A | Thread Specifications | |||||
M3 | M4 | M5 | M6 | M8 | M10 | |
1.2 | 1.2 | 1.2 | ||||
1.5 | 1.5 | 1.5 | ||||
2.0 | 2.0 | 2.0 | 2.0 | 2.0 | 2.0 | 2.0 |
3.0 | 3.0 | 3.0 | 3.0 | 3.0 |
7) The applicable plate thickness for hexagonal rivet nuts is shown in Table 9-7.
Table 9-7 Applicable Sheet Thickness of Hexagonal Stamped Rivet Nut (Unit: mm)
Handle code A | Thread Specifications | |||||
M3 | M4 | M5 | M6 | M8 | M10 | |
1.5 | 1.5 | 1.5 | ||||
2.0 | 2.0 | 2.0 | 2.0 | |||
3.0 | 3.0 | 3.0 | 3.0 | 3.0 | ||
4.0 | 4.0 | 4.0 | 4.0 | 4.0 | ||
5.0 | 5.0 | 5.0 | 5.0 | |||
6.0 | 6.0 | 6.0 |
Note: Hex rivet nuts are primarily used for connections involving copper base plates.
8) The bottom hole diameter of the press riveting screw can be found in Table 9-8.
Table 9-8: Press Riveting Bolt Bottom Hole Diameter
(Unit: mm)
Thread Specifications | Code name | Base hole diameter d |
M2.5×0.45 | FH(S)-2.5-L | φ2.5 |
M3x0.5 | FH(S)-M3-L | φ3 |
M3x0.5 | NFH(S)-M3-L | φ4.8 |
M4x0.7 | FH(S)-M4-L | Φ4 |
M4x0.7 | NFH(S)-M4-L | φ4.8 |
M5x0. 8 | FH(S)-M5-L | φ5 |
M5x0.8 | NFH(S)-M5-L | φ6.8 |
M6 × 1.0 | FH(S)-M6-L | φ6 |
M6 × 1.0 | NFH(S)-M6-L | φ6.8 |
Note: 'S' indicates the material is stainless copper, while no 'S' implies the material is steel. 'FH' represents a round head, 'NFH' denotes a hexagonal head and 'L' means the total length of the screw.
9) For the diameter of the bottom hole of the pull rivet nut and the thickness of the applicable plate, please refer to the national standard: Flat head rivet nut (GB/T17880.1-1999), Countersunk rivet nut (CB/T17880 .2 -1999), Small Countersunk Rivet Nut (GB/T17880.3-199), 120° Small Countersunk Rivet Nut (GB/T17880.4-1999), Flat Head Hex Rivet Nut (GB/T17880 .5-1999).
(7) The minimum distance from the center of the bottom hole of the riveted part to the edge of the base plate.
1) The recommended minimum distance from the center of the bottom hole of the commonly used snap rivet nut stud to the edge of the base plate is shown in Table 9-9.
Table 9-9 Recommended minimum distance from the center of the bottom hole of the commonly used snap rivet nut stud to the edge of the base plate (unit: mm).
Thread Specifications | Code name | Minimum recommended distance from the center of the bottom hole to the edge of the base plate. |
M3x0.5 | (B)S0(0)(S)-3.5M3-H | 6.8 |
M4x0.7 | (B)S0(0)(S)-M4-H | 8.0 |
M5x0.8 | (B)S0(0)(S)-M5-H | 8.0 |
M6x1.0 | (B)S0(0)(S)-M6-H | 10 |
2) The recommended minimum distance from the center of the bottom hole of the commonly used rivet nut to the edge of the base plate is shown in Table 9-10.
Table 9-10 Recommended minimum height from the center of the bottom hole of the commonly used rivet nut to the edge of the base plate (units: mm)
Thread Specifications | Code name | Minimum recommended distance from the center of the bottom hole to the edge of the base plate. |
M3x0.5 | S(CLS)-M3-A(0,1,2) | 4.8 |
M4x0.7 | S(CLS)-M4-A(1,2) | 6.9 |
M5x0.8 | S(CLS)-M5-A(1.2) | 7.1 |
M6x1.0 | S(CLS)-M6-A(1.2) | 8.6 |
M8×1.0 | S(CLS)-M8-2 | 9.7 |
M10x1. 5 | S(CLS)-M10-2 | 13.5 |
3) The recommended minimum distance from the center of the bottom hole of the commonly used recessed nut to the edge of the base plate is given in Table 9-11.
Table 9-11 Recommended minimum distance from the center of the bottom hole of the commonly used recessed nut to the edge of the base plate (Unit: mm)
Thread Specifications | Code name | Minimum recommended distance from the center of the bottom hole to the edge of the base plate. |
M3x0.5 | F(S)-M3-1.5 | 6 |
M4x0.7 | F(S)-M4-2.5 | 6 |
M5x0.8 | F(S)-M5-2.5 | 7.2 |
4) The recommended minimum distance from the center of the bottom hole of the commonly used round expansion rivet nut to the edge of the base plate is shown in Table 9-12.
Table 9-12 Recommended minimum distance from the center of the bottom hole of the commonly used round expansion rivet nut to the edge of the base plate (Unit: mm)
Handle code A | Thread Specifications | ||||
M3 | M4 | M5 | M6 | M8 | |
1.2 | 4.8 | 6.9 | |||
1.5 | 4.8 | 6.9 | |||
2.0 | 4.8 | 6.9 | 7.1 | 8.6 | 9.7 |
3.0 | 7.1 | 8.6 | 9.7 |
5) The recommended minimum distance from the center of the base hole of the commonly used hexagonal rivet nut to the edge of the substrate is shown in Table 9-13.
Table 9-13 Recommended minimum distance from the center of the base hole of the commonly used hexagonal rivet nut to the edge of the substrate (Unit: mm)
Handle code A | Thread Specifications | |||||
M4 | M5 | M6 | M8 | M10 | M12 | |
1.5 | 6.9 | |||||
2.0 | 6.9 | 7.1 | ||||
3.0 | 6.9 | 7.1 | 8.6 | 9.7 | ||
4.0 | 7.1 | 8.6 | 9.7 | 13.5 | 15 | |
5.0 | 8.6 | 9.7 | 13.5 | 15 | ||
6.0 | 9.7 | 13.5 | 15 |
6) The recommended minimum distance from the center of the lower common rivet screw hole to the edge of the base plate is shown in Table 9-14.
Table 9-14 Recommended minimum distance from the center of the bottom hole of the common rivet screw to the edge of the base plate (Unit: mm)
Thread Specifications | Code name | Minimum recommended distance from the center of the bottom hole (round head) to the edge of the base plate. |
M3x0.5 | FH(S)-M3-L | 5.6 |
M4x0.7 | FH(S)-M4-L | 7.2 |
M5x0.8 | FH(S)-M5-L | 7.2 |
M6x1.0 | FH(S)-M6-L | 7.9 |
(8) Factors affecting rivet assembly quality
There are several factors that influence the quality of rivet assembly, including the properties of the base material, the bottom hole diameter and the riveting method.
1) Base material properties: When the hardness of the base material is appropriate, the riveting quality and load-bearing capacity of the riveted parts are optimal.
2) Bottom hole diameter: The size of the bottom hole directly affects the quality of the riveted assembly. A larger bottom hole results in a larger gap between the base material and the riveted parts. The effects of this gap on different riveting methods are as follows:
i) Impact on compression riveting: The base material cannot deform enough to fill the groove in the riveted part, resulting in insufficient shear force and directly affecting the thrust resistance of the compression rivet nut (or rivet).
ii) Impact on Expansion Riveting: If the bottom hole is too large, the compression force generated by plastic deformation during riveting decreases, directly affecting the thrust and torsional resistance of the expansion rivet.
iii) Impact on Tensile Riveting: If the bottom hole is too large, the effective friction between the two parts decreases after plastic deformation, affecting the quality of riveting.
Although a smaller hole can increase the load-bearing capacity of the rivet to a certain extent, it can lead to poor aesthetic quality, high riveting force, inconvenience in installation, deformation of the base plate, and decreased production efficiency and riveting quality .
3) Distance from the center of the bottom hole to the edge of the base material: If this distance is too short, it may cause deformation of the base material and affect the riveting quality.
(9) Rivet Assembly Process Principles
When preparing process sheets for sheet metal parts with riveted components, special attention should be paid not only to the rational arrangement of the riveting process, but also to the position of the rivet screw or nut.
Different positions support different loads and have different process requirements. Therefore, the structure of the riveted parts and the riveting process must be adapted to the riveting position. Improper selection may reduce the load range of the bolt or rivet nut, leading to riveting failure. The general principles for riveting screws and rivet nuts are as follows:
1) Do not rivet steel or stainless steel screws and rivet nuts before anodizing or treating the surface of aluminum plates.
2) The number of compression rivet bolts or rivet nuts riveted in the same row should be reasonable. If there are too many, the compressed material will have nowhere to flow, which can cause great stress, bending the part into an arc.
3) It is preferable to coat the surface of the parts before riveting the rivet screws and nuts.
4) After riveting, M5, M6, M8 and M10 rivet nuts generally need to be spot welded to increase their strength. Larger nuts require greater strength and can be arc welded. For M4 (including M4) and below, it is best to use expansion rivet nuts.
5) When riveting nuts on a bent edge, to ensure the riveting quality of the nut, please note the following:
① The distance from the edge of the rivet hole to the edge of the bend must exceed the deformation zone of the bend.
② The distance L from the center of the riveted nut to the inner side of the bent edge must be greater than the sum of the radius of the outer cylinder of the riveted nut and the inner radius of curvature, that is, L>D/2+r.
6) For substrates less than 1 mm, the reliability of press riveting is low and therefore not recommended. If there are special requirements, it can be changed to expandable riveting, and 2-3 points should be reinforced with argon arc spot welding (or spot punching 2-3 points) on a surface that does not affect the threads.
3. Projection weld nuts
Projection welding nuts, also known as spot welding nuts, are widely used in sheet metal products. However, during actual application, problems often arise due to an incorrectly designed hole diameter, resulting in the inability to accurately position the projection weld nut.
National standards include two types of projection weld nuts: square weld nuts (GB13680-1992) and hexagonal weld nuts (GB13681-1992). Square welded nuts have irregular positioning, not only resulting in significant positioning errors, but often requiring threads after welding.
In contrast, hexagonal welded nuts have a self-positioning structure, offering greater precision and more convenient welding operations. Therefore, it is advisable to use hexagonal welded nuts.
A schematic diagram of welding a hex nut to a base plate is shown in Figure 9-6. Recommended values for base plate hole diameter D and plate thickness t are presented in Table 9-15.
Figure 9-6: Schematic diagram of hex weld nut welded to base plate
Table 9-15: Recommended values for base plate hole diameter D and plate thickness t
(Unit: mm)
Thread Specifications | D | t | ||
M4 | 6 +0.075 | 0.75~3 | ||
M5 | 7 +0.09 | 0.9~3.5 | ||
M6 | 8 +0.09 | 0.9~4 | ||
M8 | M8×1 | 10.5 +0.11 | 1-4.5 | |
M10 | M10×1 | M10x1.25 | 12.5 +0.11 | 1.25-5 |
M12 | M12x1.5 | M12×1.25 | 14.8 +0.11 | 1.5-5 |
M14 | M14x1.5 | 16.8 +0.11 | 2~6 | |
M16 | M16×1.5 | 18.8 +0.13 | 2~6 |
4. Flanging and Threading
Flanging and tapping, also known as drilling and tapping, is mainly used on sheet metal parts to establish connections between them. Since the base of the sheet metal part is thin, hitting it directly would result in a thread that is too short, which can slip out easily.
Therefore, a bottom hole is first drilled into the sheet metal part (determined by thread specifications). Then, using a dedicated flanging (hole pulling) die in a press, a vertical edge is pulled out (draw height is determined by thread specifications and plate thickness). Finally, the thread is tapped, achieving the purpose of increasing the effective length of the thread.
5. Performance comparison of puffed rivet nuts, pressed rivet nuts, pull rivet nuts and flanging and threading
Swollen rivet nuts, pressed rivet nuts, pulling rivet nuts, and flanging and threading have their advantages and disadvantages. The performance comparison can be seen in Table 9-16.
Table 9-16 Performance Comparison of Swollen Rivet Nuts, Pressed Rivet Nuts, Pull Rivet Nuts, and Flange and Thread
Connection method | Stamping Nut | Pressure nut. | Riveted Nut | Flanging and Threading |
Machinability | Good | Good | Good | Average |
Substrate material | Stainless steel rivets tend to fall out easily | Riveting of stainless steel is poor, requiring the use of specially manufactured locknuts and spot welding. | Good | Thin plates and soft copper and aluminum materials are prone to thread slippage. |
Precision | Good | Good | Good | Average |
Durability | Good | Good | Good | The quality of copper and aluminum materials is inferior, and other materials with more than three wires are preferable. |
Cost | High | High. | Average | Low |
Quality | Good | Good | Good | Average |