Mold development progress plays a crucial role in the entire project timeline and is an important part of OEM production preparation.
In the following paragraphs, we will discuss the process and control of the mold development schedule, from body data release to final mold inspection and acceptance.
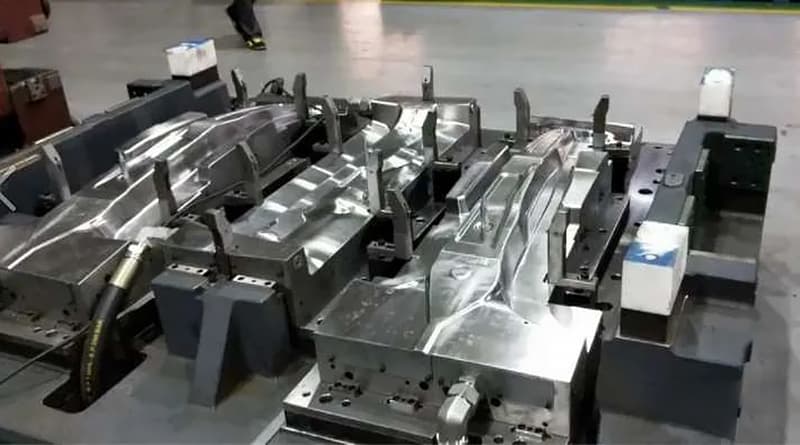
1. Release of body process data
The body design department releases product simulation models, and the engineering personnel in the engineering development department carry out process analysis and quotations based on the product simulation models (as comparative data for bidding).
The body process simulation model is used for mold bidding and corresponding process analysis. The bidding process will not be discussed in detail here. Next, we will briefly talk about mold development management after finishing the mold factory.
2. Feasibility analysis of body parts manufacturing process (mold developer and engineering development department)
After receiving the simulation model of the body process, the mold developer performs a feasibility analysis of the manufacturing process for each part. In principle, mold factories are required to carry out CAE analyzes (i.e. part formability simulation analyses) on all newly developed parts.
The role of CAE analysis:
- Through CAE analysis, we can observe the sheet metal forming process more intuitively.
- Shorten the mold design and analysis cycle.
- Anticipate the possibility of mold.
- Adopt optimized design to minimize the consumption of molds and steel materials and reduce manufacturing costs.
- Identify potential mold and part hazards before manufacturing.
- Ensure the rationality of mold design and reduce design costs.
- Based on the analysis of potential problems of parts, the mold factory can propose reasonable suggestions for design changes in a timely manner and promote development work more efficiently.
The development department can fully utilize the on-site production debugging experience and check whether the process parameters and supplementary elongation are reasonable based on the CAE analysis results of the parts provided by the mold factory.
In response to risks such as wrinkling or cracking of parts, the department can propose solutions in a timely manner.
3. DL diagram design and co-signing
After CAE analysis is completed, mold DL diagram design can be conducted in most cases.
DL diagram design refers to the analysis and design of the stamping process, also known as the mold process flow chart, which includes the size of the part sheet, the direction and angle of stamping, the arrangement of stamping processes, the feeding direction, the distribution and direction of scrap knives, illustration of scrap removal direction, CH hole, identification of left and right parts and labeling of each process.
In addition, the DL diagram should also reflect the stamping equipment for relevant processes, the mold height, the mold material, the working stroke of edge pressing rings or pressing plates, the sheet metal positioning method and pressure analysis of the completed process.
After the completion of the DL project, the internal audit must be carried out at the mold factory. Once the internal audit issues have been corrected, the design can be provided to the OEM development department and co-signed.
The co-sign of the DL diagram is critical, directly affecting subsequent mold design and having a significant impact on the mold development cycle and cost. If the DL diagram is changed later, it will cause considerable waste in terms of development cycle and cost.
The engineering development department mainly analyzes the workpiece process rationality, machine parameter accuracy, process supplement rationality, material utilization rate, and examines the convenience of feeding in conjunction with the press situation.
4. Mold structure diagram design and signature
The order of co-signing mold structure diagrams: co-signing drawing mold diagram – co-signing forming flange mold diagram – co-signing edging and punching mold diagram.
As the mold casting and processing cycle is inflexible, it is important to ensure the project progress by drawing the mold structure diagram step as early as possible to gain additional time for subsequent mold manufacturing.
Generally, the first sampling of the mold is a semi-manual sampling, only requiring forming, while the remaining edging and punching can be completed by wire cutting.
Therefore, the design of the stretching mold and flange mold diagrams should be carried out before designing the punching and edging mold diagram.
The mold factory designs the mold structure diagram based on the guidelines of the DL diagram, and after completion, it is also subject to internal review. After resolving any issues found during the review, it can be presented to the OEM development department for co-signing.
The OEM development department should focus on:
- Mold functionality
- Structural stability and strength
- Safety in mold production
- Consistency of mold parameters with mass production presses
- Debugging and production convenience
- Material consistency for key mold components with technical protocol requirements
For problems discovered during the review, the mold factory should be asked to correct them as much as possible. Some problems may not have a significant impact on product functionality, but may affect operational convenience or reduce production efficiency. To meet deadlines and schedules, the mold factory may not be very cooperative in making changes.
At this point, OEM development personnel (engineers) need to show courage and determination because changes during the design phase are always faster than changes later (after mold formation).
Mold factory designers need to think from the perspective of the production department and consider the problem from multiple angles.
Debatable pain points require objective discussion between many parties to find the best solution. During the mold diagram review process, engineering development technicians are required to have a firm stance and solid technical and debugging experience on site to reduce many problems later.
5. Release of Numerical Casting Model and Evaluation and Rectification of Realistic Foam Model (EPS)
After reviewing the mold structure diagram design, realistic foam models can be made. In the realistic foam model phase, the design team needs to release casting data to ensure the moldability of the real model.
The realistic foam model is a material formed by polystyrene foam at high temperature. It is processed by NC based on the mold structure diagram and considering appropriate mold processing tolerances (8-10 days) and foam shrinkage rate.
The production cycle for EPS foam generally lasts about a week. After production, it needs to undergo on-site evaluation to ensure consistency with the mold structure diagram.
It also checks whether problems identified in the mold structure diagram review have been corrected or whether there are new problems that were not discovered during the design review.
The evaluation of realistic foam models is an indispensable process in mold manufacturing because it is the last hurdle to structural changes to the mold. After entering the casting stage, it is difficult to modify the mold structure.
6. Die Casting
After grinding the EPS foam, it can be sent to the foundry for casting. The specific process will not be discussed here. The mold casting cycle is 15 to 20 days. After the mold casting is completed, it is transported back to the mold factory for casting inspection.
The main focus is checking for major casting defects, such as cracks inside the casting. Internal defects, such as sand inclusion, need to be machined before they are observed.
7. NC Numerical Model Release and NC Mold Machining
After mold casting is completed, NC machining can begin as long as the NC data has been released.
The mold factory can perform CNC programming based on the NC data of the product, and then perform NC machining of the mold. NC mold machining can be divided into: rough milling – assembly – semi-finishing – finishing.
During the NC machining process, defects such as sand inclusion or cracks inside the casting can be detected. After NC machining is completed, the mold needs to undergo heat treatment to achieve the required hardness.
The mold NC machining cycle is generally 20 to 25 days.
In situations where the design development time is short, it is important to organize the NC machining time reasonably. Engineering development personnel can carry out on-site progress control and supervise the mold factory in developing a reasonable machining plan.
It is important to avoid keeping CNC machining equipment idle to ensure progress.
8. Mold adjuster, debugging and sampling process
The mold assembly step includes: mold base alignment – mold closing – test molding – sampling, etc. After the mold is NC machined, there is still some room for later fitting.
Mold fitter debugging mainly checks the matching rate of upper and lower molds and the guiding rate to ensure that qualified stamping parts are produced.
Through the debugging of the mold installer, the quality of the mold can be identified and the size for cutting can also be determined.
9. Mold pre-acceptance
After the mold factory completes the entire mold manufacturing according to the plan and self-tests the mold to be qualified, it can apply for pre-acceptance from the OEM development department.
The mold factory needs to provide a mold self-inspection report and the qualification rate of stamped parts. The OEM development department arranges personnel to carry out pre-acceptance in the mold factory after receiving the pre-acceptance order from the mold factory.
The mold is mainly accepted from three aspects: mold statics, dynamic stamping part quality and mold function.
Static and dynamic inspections are carried out according to standards, while inspection of stamped parts is divided into surface quality, dimensional accuracy and rigidity.
In principle, problems encountered during the pre-acceptance process require rectification by the mold factory prior to packaging and shipping.
However, if some problems do not affect the quality of the product and the difficulty of rectification is small, they may remain so that the mold factory installers continue to rectify at the production site in cases where time is short.
10. Mold production site debugging and acceptance
Due to differences in machine tools and mold surface matching rates, to ensure product quality, after the mold has been pre-accepted, it needs to be debugged when transported to the production site.
Generally, the first round of stretching mold adjustment takes 1 to 2 months, and the entire mold debugging cycle can last half a year or more. The mold production site debugging process revolves around the following aspects:
- The stamped parts need to be clamped on the welding device to check the coordination of the mold, clamp, gauge, inspection tool and welding device.
- Ensure the accuracy of stamped parts by inspecting them on the inspection gauge. The qualification rate must generally be above 90%.
- Problems or defects found during stamping of parts in the inspection gauge or feedback from the welding and debugging process must be corrected by the mold factory.
- Check the mold function dynamic and static inspection items.
- The reliability of the mold in continuous production in the production press, that is, the scrap rate requirement in continuous production is less than 2%.
The mold debugging and grinding cycle is long. The above items need to be corrected, and the mold needs to be operated stably for three months before the OEM development department can organize the mold user, maintenance personnel, quality inspector, etc. approval report.
After final acceptance is completed, the mold development work is considered complete.
However, as long as the mold is not discarded, the mold's life cycle continues. The work of the OEM development department is then transferred to the production system and process department for use, management and maintenance.
With good use and maintenance of the mold, its useful life can be extended, the scrap rate reduced and production efficiency increased, bringing considerable economic benefits to the company.
1 comment
Hola muy buenos días ! Quería consultarle que soy una estudiante de una escuela técnica .. Y nos dieron un trabajo donde preciso usar su máquina! Y una de las consignas es hacer una ficha técnica.. Me podría adjuntar ests información así la realizo? Voltaje, HP, rpm, medidas, potencia, etc .. Gracias !