Laser welding is the process of using high-energy laser pulses to locally heat a small area of a material. The laser radiation energy is transferred into the material through heat transfer, causing the material to melt and form a specific molten pool, thus achieving the welding objective.
A laser welding machine is a device used for laser processing of materials. Based on its mode of operation, it can be classified into four types: laser mold welding machine, automatic laser welding machine, laser spot welding machine and optical fiber transmission laser welding machine.
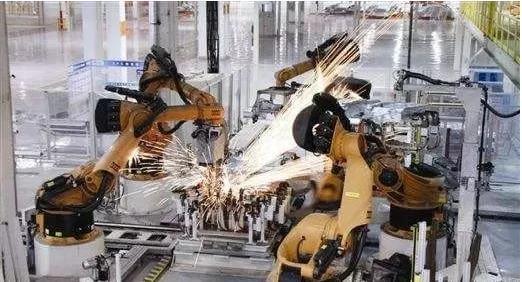
Weldable material
Die steel
The laser welding machine can be used to weld mold steel of S136, SKD-11, NAK80,8407,718,738, H13, P20, W302, 2344 and other models, and the welding effect is good.
C carbon steel
Carbon steel can be effectively welded using a laser welding machine, and the quality of welding depends on the presence of impurities. To obtain good welding quality, preheating is required when the carbon content exceeds 0.25%.
When welding steels with different carbon contents, the welding torch should be slightly inclined towards the low carbon material to ensure joint quality.
Due to the rapid heating and cooling speed of laser welding machines, as the carbon content increases, the susceptibility to welding cracks and notches also increases.
Both medium- and high-carbon steels and common alloy steels can be welded well using a laser, but preheating and post-weld treatment are necessary to relieve stress and prevent cracking.
S stainless steel
In general, welding stainless steel is easier to obtain high-quality joints than with traditional welding methods.
The high welding speed and small heat-affected zone of laser welding reduce the risks of overheating and the negative effects of the large coefficient of linear expansion when welding stainless steel, resulting in welds free from defects such as pores and inclusions.
Compared to carbon steel, stainless steel is easier to obtain deep and narrow penetration welds due to its low thermal conductivity, high energy absorption and efficient melting.
Welding thin plates with low-power lasers can result in visually appealing joints with smooth, beautiful welds.
Copper and copper alloys
Welding copper and copper alloys can result in incomplete fusion and penetration problems, thus requiring the use of high-powered, energy-concentrated heat sources and preheating measures.
When the part is thin or has low structural rigidity and without measures to prevent deformation, large deformations may occur after welding. Furthermore, when the welded joint is subjected to significant rigid constraints, welding stresses may occur.
Thermal cracking is also a common problem in welding copper and copper alloys.
Porosity is a frequent defect in welding copper and copper alloys.
Plastic
Laser welding technology can be applied to almost all thermoplastics and thermoplastic elastomers, including common materials such as PP, PS, PC, ABS, polyamide, PMMA, polyoxymethylene, PET and PBT.
However, other engineering plastics such as polyphenylene sulfide (PPS) and liquid crystal polymers cannot be directly welded using laser technology due to their low laser transmittance.
In general, carbon black is added to the bottom material to increase its ability to absorb energy, allowing it to meet the requirements of laser transmission welding.
Aluminum alloy laser welding
The main challenge in laser welding of aluminum and its alloys is their high reflectivity up to 10.8 µm CO 2 laser beams.
Aluminum is an excellent conductor of heat and electricity, and its high density of free electrons makes it an effective light reflector.
With an initial surface reflectivity greater than 90%, deep penetration welding must begin with less than 10% of the input energy, requiring high input power to guarantee the necessary power density at the start of welding. This results in the formation of small holes.
Laser welding of magnesium alloys
Mg alloys have a density 36% lower than Al, which makes them highly attractive as high specific strength materials.
To explore its welding potential, tests using pulsed YAG lasers and continuous CO 2 lasers were conducted.
For the alloy AZ31B-H244 (3.27% Al, 0.79% Zn) with a plate thickness of 1.8 mm, the best welding conditions with minimal defects were average power of 0.8 kW, pulse duration of 5 ms, frequency 120 Hz, speed 300 mm/s and focus size 0.42 mm.
Continuous CO 2 laser welding has been found to produce good penetrating welds.
High strength low alloy steel
For laser welding of low-alloy, high-strength steels, proper selection of welding parameters can result in joints with mechanical properties equivalent to those of the base metal.
HY-130 steel is a representative low-alloy, high-strength steel that, after quenching and tempering, has high strength and resistance to cracking.
Using conventional welding methods, the weld and heat-affected zone (HAZ) structures exhibit a mixture of coarse grains, some fine grains, and the original structure.
However, the toughness and resistance to cracking in the joint is lower than that of the base metal, and weld and HAZ structures are particularly susceptible to cold cracking in their as-welded state.
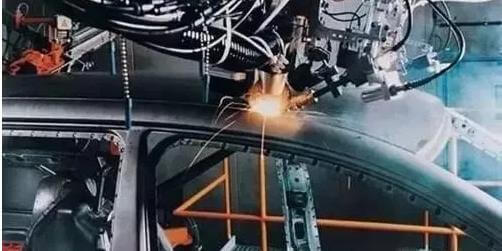
S summary
Laser welding can be used to join a wide variety of materials and can even be used to weld dissimilar metals.
Studies have shown that laser welding can be performed between various combinations of different metals, such as copper-nickel, nickel-titanium, copper-titanium, titanium-molybdenum, brass-copper, and low-carbon steel-copper, under certain conditions. .