It is well known that almost all sheet metal processing companies use sheet metal bending machines.
However, those who have experience operating press brakes understand that, regardless of whether it is an ordinary press brake or a CNC press brake, whether it involves large, heavy parts in the distribution cabinet and elevator door industry or small parts in appliances. kitchen and air conditioning industry, and whether it involves parts produced primarily in batches or custom one-offs, using a press brake can be taxing both mentally and physically.
As a result, in today's sheet metal processing industry, it is common for no one to want to be a press brake operator. Even when the role is offered as an apprenticeship and the company offers higher salaries than technical CNC drilling workers, few individuals are willing to take on the role.
This led to the emergence of CNC panel bending machines.
This post will analyze and introduce the CNC press brake in reference to the press brake.
Panel Bending and Press Brake Features
CNC panel bending machine differs from bending machine in principle and offers superior guarantee for bending accuracy and sheet metal protection. Furthermore, tool replacement is smarter and more convenient, and there is less demand for operators with high proficiency.
Bending principle of panel bender and press brake
The press brake adjusts the downward stroke of the upper punch to control the bending angle.
During bending, the short side is on the inside, so the operator needs to support most of the material on the outside. Furthermore, the operator needs to hold the plate during the bending process to follow its upward movement.
To bend large parts, two or more employees are required.
If there are bending demands in different directions for all one-edge bending processes, it will be necessary to manually turn the material repeatedly.
The panel bender works by placing the sheet on the work table, fixing it with the edge pressing beam and bending it by turning the beam up or down.
The panel bender eliminates the need for manual positioning, auxiliary positioning and reversing in all single edge bending processes.
Bending precision and consistency
(1) Dimensional accuracy.
The accuracy of the dimensions controlled by the press brake is the accuracy of the short side dimension of the backstop positioning. Once the bending process is complete, any errors are accumulated and carried to the next bending step, resulting in an accumulated error that is concentrated in the final dimension of the forming.
On the other hand, the precision of the dimensions controlled by the panel bender is based on the fact that the outer edge serves as a reference point for each folding operation. Any dimension errors tracked are concentrated only in the first fold and have no impact on the other dimensions.
(2) Angle accuracy.
The bending angle in the press brake is determined by the downward stroke of the upper punch, which is directly related to the thickness of the material.
On the other hand, the panel bender directly controls the bending angle and the thickness of the material has minimal impact on it.
(3) Consistency.
The dimensional accuracy of each side of the press brake is ensured by the positioning of the backstop, but this accuracy can be inconsistent due to various external factors.
The angle of the workpiece is determined by the position of the ram. Ram control positioning accuracy and hydraulic system temperature conditions have a significant impact on angle accuracy.
The servo motor of the press brake controls the positioning accuracy and angle processing of the workpiece, ensuring consistent size and angle processing.
Protection against scratches on metal sheets
During operation of a press brake, material moves relative to the plate, which can result in indentations if the plate surface is not protected. Furthermore, when one side of a large part requires multiple processing techniques or bending, it needs to be turned and moved several times, which can cause scratches.
However, when using a panel bender, there is no relative movement between the pressing beam die or bending beam die and the plate. As a result, superficial scratches can be avoided.
Furthermore, when working with multiple processing techniques on one side or when bending large parts, the sheet metal can be placed horizontally on the work table for processing. After the first positioning, all necessary processing can be carried out on one side of the part without having to move it, completely avoiding surface scratches.
Tool configuration
As the bending die is used to create the fixed bend line and form the angle of the parts, it is necessary to change the tool or machine when bending different materials, thicknesses, angles and even special structures.
Furthermore, when edging is required or when the bending process impacts bending, multiple sets of dies with different lengths are required to complete the processing of the same workpiece (see Fig. 1).
In these cases it is necessary to replace and readjust the mold, or even replace the machine tool.
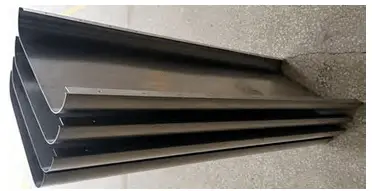
Fig. 1 Bending of the part affected by the sequence
The panel bender uses two sets of molds to achieve fold line fixing and angle formation respectively. The spacing between the two sets of molds can be automatically adjusted to realize angle forming for various materials, plate thicknesses and R-angles.
To obtain hems, bends with arbitrary angles, bend arcs and other requirements, different control programs can be selected. The cooperation between the two sets of pressing and bending dies facilitates the processing of the workpiece.
During the bending process, if the length of the die needs to be changed, the program can be adjusted at any time for automatic switching. There is no need for additional debugging after matrix replacement.
Operation requirements
Programming and operating a bending machine requires a high level of technical skill from benders, especially for parts with complex bending processes.
The panel folder program can be developed offline using programming software. By importing 2D or 3D graphics and using simple drag-and-drop configurations, machining code can be generated automatically.
During the programming process, the system can also provide automatic warnings for bending interference.
Once the program is transferred to the panel bender via a network cable or USB disk, operating the machine is a simple process of loading and unloading and pushing buttons.
Industrial application advantages of CNC panel bender
Industries such as switch cabinets and elevator door panels with large, heavy parts, as well as those with small, light parts, such as kitchen cabinets and air conditioners, are paying significant attention to panel bending machines.
According to preliminary statistics, CNC panel bender has been widely applied in various industries, including switch cabinets, elevators, household appliances, kitchen cabinets and medical equipment.
The following objective is to share the advantages of using panel bending machines in the electrical panel and cabinet industries, which are widely adopted.
Distribution cabinet industry
Switchgear products (as shown in Figure 2) are characterized by their large size, heavy weight and potential danger. Furthermore, there are specific accuracy requirements for the final dimensions of the formed products.
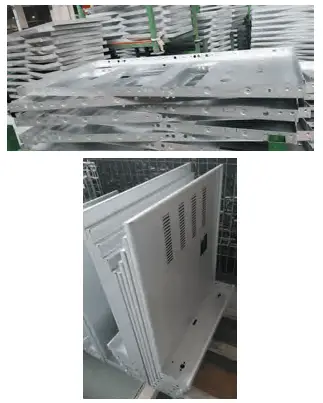
Fig. 2 Distribution cabinet parts
Using a conventional press brake for processing requires at least two operators to handle the workpiece and bend the iron plate one by one according to the speed of the machine. This method is very demanding on workers and can result in unstable error control. Furthermore, the heavy workload significantly limits daily production capacity and poses significant safety risks.
On the other hand, a panel bender requires only one person to operate, which can work together with automatic loading and unloading. The workpiece is placed flat on the working platform and the machine automatically performs edge changing and bending processing. This process is not affected by human factors and results in precise bending without deviation.
In short, the panel bending machine not only saves time and labor, but is also safer and more efficient.
cabinet industry
Cabinet products (Figure 3) are characterized by relatively thin sheets, but the processing requirements are more complex.
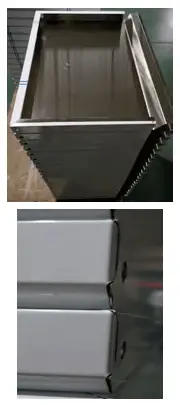
Fig. 3 Cabinet Product Parts
When using a press brake to bend, it is important to check the unfolding size of the parts according to the drawing specifications. After ensuring there are no errors, the appropriate tool needs to be selected for configuration and matching, followed by programming as needed.
This entire process requires a high level of work experience from workers.
Furthermore, for rounded edge packaging and special processes, multiple sets of tools or machines need to be changed when using a press brake, making it a time-consuming and labor-intensive task.
On the other hand, a panel bender simply requires input of the sheet metal size and forming size, and the programming software automatically generates a rational bending program.
The panel bender's universal bending tool can save significant time by reducing or eliminating the need to change bending tools. For kitchen utensils with various special process requirements, panel benders can easily complete processing and bend parts that meet the requirements more quickly and economically.
Panel folder development perspective
With its automatic production capabilities throughout the entire process, the CNC panel bending machine offers several advantages over multiple sets of bending machines alone. It can also achieve automatic production when connected to punch presses, laser cutting machines and other machine tools. In addition, it can be used with intelligent management software and multi-row material warehouses, providing customers with a complete set of intelligent chemical plant solutions.
Faced with today's challenges of “difficult employment” and “expensive employment”, an intelligent and efficient automatic production line can significantly reduce labor requirements and production experience. Customers can achieve greater production capacity and income while minimizing labor costs.