You can scroll directly to the bottom of the page to download the PDF version of the operation manual for the following press brake control systems: Estun E21, E200P, E200+, CybTouch 8, CybTouch 12, Esa S630, Delem DA41, DA52S, DA53T, DA58T, DA66T, DA69T.
Introduction!
We strongly recommend that all users and operators read this press brake operation manual completely before using the press brake machine.
This manual is intended for specialized and qualified personnel and includes diagrams and all necessary documentation for lifting, moving and positioning the machine, as well as instructions for safe use and maintenance.
Please note that all information contained in this manual is accurate at the time of printing. However, our company reserves the right to modify and improve specifications without prior notice.
To ensure proper performance, it is important to install the press brake as instructed and perform regular inspections and maintenance. Any incorrect or irresponsible use could result in irreparable damage to the machine and compromise operator safety.
We are not responsible for any inappropriate services, modifications or connections made by unauthorized personnel.
Further reading:
- Electro-hydraulic servo press brake operation manual
- Press Brake: the definitive guide
- Press Brake Bending Basics: The Ultimate Guide to Sheet Metal Bending
Pressure brake functions and working range
1.1 This press brake is of high efficiency and high precision in bending metal sheets.
The size of the V-groove opening in bottom dies is typically 8 times the sheet thickness and must be adjusted for sheets of varying thickness.
Different types of upper and lower dies can be used to bend a variety of workpieces (see Fig. 1).
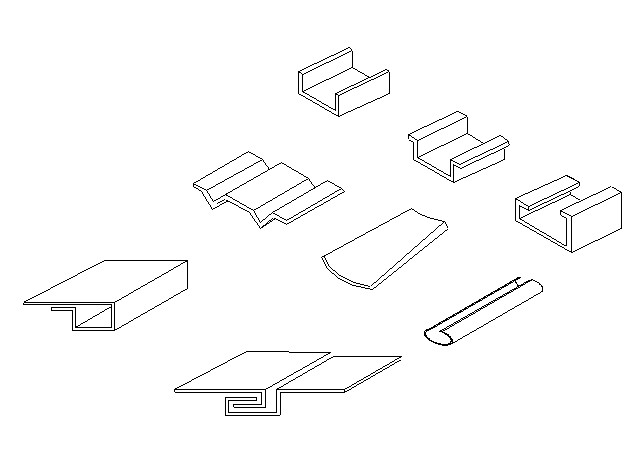
Figure 1
1.2 The press brake is made of steel plate with sufficient strength and rigidity.
The machine's hydraulic drive prevents serious overload operation accidents due to changes in sheet thickness or incorrect selection of the lower die cavity. This machine also offers stable performance, ease of operation and reliable safety.
The connection with the upper die is equipped with a compensation device, which compensates for the deflection of the worktable and slider during bending, ensuring high precision.
The mechanical block is equipped with an oil cylinder to ensure precise clamping when the slider reaches bottom dead center and maintain consistency in mass production.
1.3 It is equipped with hydraulic and electrical control, allowing the slider displacement to be adjusted freely and making it convenient for testing and adjustment with inch operation criteria.
1.4 This press brake is technologically advanced and has reliable performance, making it one of the ideal forming devices.
It is widely used in the aviation, automobile, shipbuilding and machinery industries due to its high production efficiency.
1.5 Operating condition:
- Temperature: 5 ~ 38 ℃ (working temperature)
- Ambient humidity: Relative humidity 20 ~ 80% RH。
- Keep away from strong vibrations and electromagnetic interference.
- No harmful and corrosive gases and no dust.
Press brake installation
Elevation
It is essential to ensure that the press brake is lifted for transportation or positioning using a crane that has sufficient lifting capacity to avoid the risk of the press brake falling.
Two steel cable slings and shackles must be used, using the appropriate holes located on the top of the machine.
The steel cable must be adequately sized to lift the weight of the press brake and long enough, as its weight-bearing capacity decreases as the angle between the cables increases (see Fig. 2).
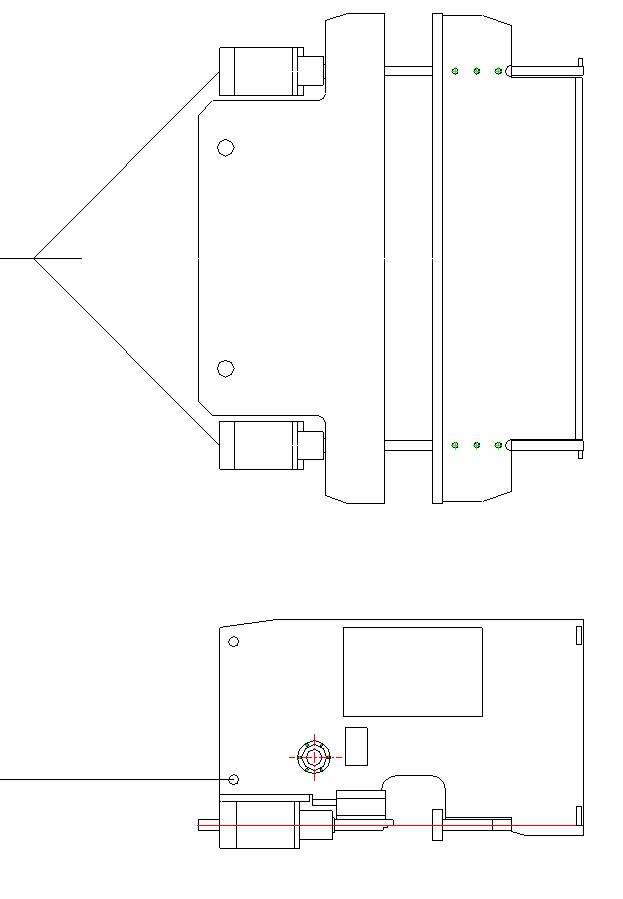
Figure 2
Transport
When transporting the press brake, remember that most of its weight is concentrated at the front. Make sure the top ram is fully lowered for any movement or transportation. When loading the press brake onto a truck, position the rear of the machine as close to the side of the vehicle as possible. Secure the press brake to the truck using steel ropes.
Installation
The base of the press brake
To ensure the proper functioning of the press brake and avoid disturbances caused by vibrations, it is important to check that the surface where it will be placed is firm and stable.
If necessary, a concrete foundation suitable for the specific terrain conditions must be prepared.
The detailed foundation drawing is provided as follows:
- Concrete foundation
- Technical specifications
Make sure there is adequate space around the machine once it is positioned. This is necessary to accommodate maintenance work and special tasks.
In addition, sufficient space on the left or right side of the press brake, equal to the length of the machine, must be available to facilitate tool changing operations.
All exposed surfaces of the machine are coated with rust protection, which can be easily removed with kerosene or solvent.
Leveling
To ensure the correct functioning of the press brake, it is necessary to properly level the machine. To check horizontal leveling, place a spirit level on the machine table.
For vertical leveling, place the spirit level on the machine table again. Any necessary adjustments can be made by adjusting the leveling screws located on the press brake feet.
The electrical diagram of the press brake
Here are the drawings:
- Electrical Diagram 1
- Electrical Diagram 2
- Electrical Diagram 3
- Electrical Diagram 4
3.1 The following steps must be carried out by specialized personnel and must be taken care of by the owner.
- Check the machine nameplate and make sure the press brake wiring is in good condition.
- Connect the press brake to the power source available at your facility.
- If the required power does not meet the machine's requirements, contact your electrical supplier.
- Make sure the power going into the bending machine is fused so that the machine can be fully disconnected for repair if necessary.
- Connect the power coming into the press brake to the RST clamps on the control cabinet.
- Electrical drawings can be checked through the attached documents, as different controllers have different drawings.
Here are the drawings:
- Electrical drawing
The detailed description is as follows:
To operate the press brake machine, follow these steps:
- Connect three-phase power lines to the electrical box input terminals. Then plug in the footswitch socket located under the box and close the QF switch and electrical box door. When the HL1 lamp comes on, it indicates that the machine is on.
- Turn on the oil pump motor HL2 button on the operation panel for a short time and observe the direction of the motor. If the direction is incorrect, change the phase of the input lines, but never change the internal lines inside the electrical box. Then start the oil pump motor again.
- In jog mode, after several minutes of normal operation, place SA2 in jog mode, press the “up” pedal. The ram will rise and when you loosen the pedal, the slider will stop. To raise the ram further, continue to step on the foot switch until you reach limit switch SQ1 and stop. To lower the ram, go “down”. The ram will fall quickly and then, due to the effect of limit switch SQ2, the ram will slowly descend to add pressure. When you loosen the pedal, the ram will stop.
- In single shift mode, turn SA2 to “single time” and then press “down” on the pedal. The ram will first descend quickly, then slowly maintaining pressure, and finally the ram will automatically rise to the upper limit switch SQ1. To adjust the working time of the KT1 time relay, make sure it meets the bending pressure requirements of the workpiece. Additionally, adjust the pressure holding time of the KT2 time relay.
- In continuity mode, set SA2 to “continuity” and step on the pedal to repeat the single shift mode. You can adjust the circulation waiting time using the KT1 time relay.
Note: The above steps must be carried out by specialized personnel. To ensure safety, CE certified press brakes do not have continuity mode.
The hydraulic system of the press brake
Clean the hydraulic oil
To ensure the quality of the hydraulic system, it is important to maintain the cleanliness of the hydraulic oil. Cleaning the oil tank is crucial.
When changing the hydraulic oil, it is necessary to remove the tank cap.
Wipe the bottom of the tank with a clean towel (do not use cotton) and then wash with cleaning gasoline.
Due to the limited reach of the arm, the corners of the tank can be difficult to clean. Wrap a towel around a stick or bamboo to clean these areas.
Loosen the leaking plug or brake valve to drain the dirty oil.
Dry the sides and bottom of the tank with a clean towel until they are completely clean.
If necessary, use a tool such as a roller to remove any dirt that may have accumulated in welding seams or hard-to-reach areas, then replace the cover.
Choose hydraulic oil
The nominal value of hydraulic oil corresponds to its average viscosity at a temperature of 40°C.
If the hydraulic system has higher working pressure and temperature and slower working speeds, a higher quality hydraulic oil should be chosen.
It is recommended to use ISO VG46# anti-wear hydraulic oil, which has an average viscosity of 46mm2/s at a temperature of 40°C.
If the machine operates at temperatures below 5°C for a long period, ISO VG32# hydraulic oil may be used.
It is not advisable to operate the machine at very low temperatures (below -5°C), but if this occurs, let the machine idle for a while. An oil heater can be added to the circuit if necessary.
Under normal working conditions, the oil temperature should not exceed 70°C. If necessary, an oil cooler can be installed for special conditions.
Fill the oil
The oil used must be clean. Tighten the air filter nut and fill it through the filter. If you are using filter filling equipment, you can open the oil tank cap and fill it directly.
Watch the oil gauge and when the ram stops at Top Dead Center, the hydraulic oil should fill about 80% to 90% of the internal space.
Run the machine first at idle speed and then at full stroke to remove any air bubbles in the hydraulic circuit.
Hydraulic Diagram
Here are the drawings:
Hydraulic Diagram
Standard Control Equipment
5.1 | home button | To start the main engine and control circuit. |
---|---|---|
5.2 | stop button | To stop the operation of the main motor and control circuit. |
5.3 | Automatic/manual mode selector switch | Select work mode |
In Auto mode | -The ram will automatically increase when the preset pressure is reached and the dwell time is over. | |
In manual mode | -The ram is lowered and raised by pressing the pedal. | |
5.4 | Pedal | Press and hold to command the ram to descend to reach the flexion point, release when the ram is rising in AUTO mode. |
Press to command the ram to lower and press to command the ram to raise in Manual mode. |
Starting the press brake machine
Before turning on the machine, be sure to carry out the following checks:
- Clean and lubricate the guides.
- Inspect the hydraulic system for leaks.
- Check the oil level at the level gauge on the side of the tank with the top ram in the fully raised position. Top up the oil if necessary.
- Check the direction of rotation of the engine by observing the direction of the cooling fan. The fan must rotate clockwise or in the direction of the arrow. If this is not the case, swap two wires in the power line, but be sure to run the motor by advancing slowly as you do so.
Turn on the machine
- Turn on the main switch.
- Change the selector to automatic.
- Start the main engine by pressing the green button.
Turn off the machine
The press brake must always be switched off when it is not used for a few hours. When disconnecting, do the following:
- Select manual mode.
- Lower the ram by pressing the pedal down to get the upper tool as close to the V-die as possible.
- Press the stop button.
- Turn off the main switch.
Upper and lower tool configuration
(Check out the drawings of the press brake tools)
Before starting any bends, make sure the top tool and the selected V-opening are aligned to ensure a good result. Also, make sure the V-die base and table surfaces are clean before proceeding with the steps.
- Lower the system pressure by turning the pressure regulator knob counterclockwise.
- Set the mechanical depth gauge to the lowest position, either manually or electrically.
- Select MANUAL MODE and press the pedal down to lower the ram until the upper tool is as close to the V-die as possible.
- Align the upper and lower tool by adjusting the V-die clamping screws.
- After alignment is correct, tighten all V-die pinch screws securely.
- Raise the ram by pressing the UP pedal.
We advise the following:
- Regularly check the tool clamp fixing screws.
- Store the tool on a rack near the press brake to prevent damage to the upper tool.
- Remember that each tool has a maximum force capacity.
Tool change procedure
÷SUPERIOR TOOL
When the upper tool needs to be changed, do the following:
- Turn the mode dial to manual.
- Lower the ram as close to the V-die as possible.
- Turn off the machine.
- Loosen all tool clamp fixing screws.
- Remove the tool from the side of the machine.
- Mount the new top tool by sliding it from the same side.
- Tighten all tool clamp fixing screws.
- Turn on the machine and check that the mode selector is in the manual position.
Lower the ram to seat the upper tool in the V-die while reducing system pressure by turning the pressure regulator knob counterclockwise to prevent damage to the tool.
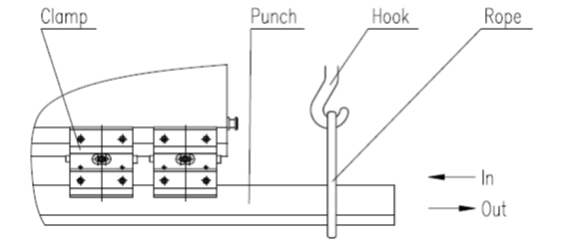
÷BOTTOM TOOL
To change a different V matrix in your multiple matrix configuration, follow these steps:
- Unscrew all clamping screws to release the V-die.
- Change the mode selector to manual.
- Turn on the machine.
- Lower the ram as close to the V-die as possible.
- Secure the V-die to the ram at both ends using the appropriate chains.
- Raise the ram by stepping on the UP pedal to a height where the V-die can rotate.
- Turn the desired V-die face up.
- Lower the ram by stepping on the DOWN pedal so that the die rests on the machine table and the chains can be disengaged.
- Center the V-die relative to the top tool.
- Lock the V-die in place by tightening the screws.
÷FRONT SUPPORT ARM
The press brake comes standard with two front support arms. These support arms are used to hold the board in place during the bending process. They can be adjusted vertically and along the length of the press brake.
Support arms often need to be adjusted when using a different size bottom tool or when bending a larger or smaller size board.
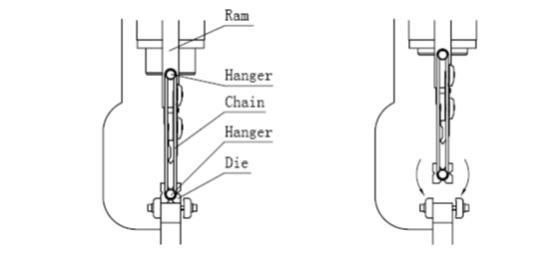
DANGEROUS!
If the punch and die are not placed correctly, do not turn on the machine at any time. Also, do not insert your hands or any part of your body into the space between the punch and the die as it is extremely dangerous.
Mechanical depth stop setting
Do not attempt to adjust the mechanical depth stop setting when the ram is in the lowered position as this may cause unnecessary damage to the machine.
- The depth setting determines the bend angle.
- The mechanical depth stop can be adjusted manually or electrically.
Pressure Setting
Typically the bending table is fixed to the side of the machine and a copy is attached. The bending force is a function of:
- The thickness of the board
- The width of the die opening. (8 x board thickness)
The required bending force can be calculated from the formulation in Table 1.
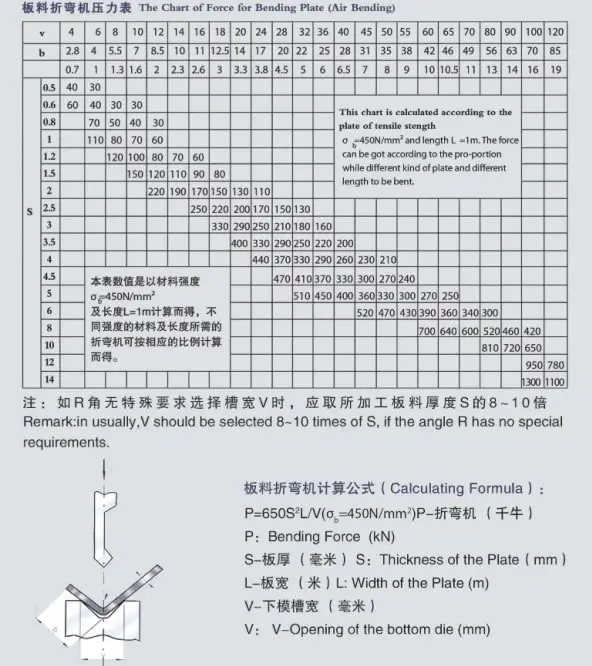
Note: This formula and table values are based on carbon steel plates with tensile strength of Qb=450KN.
For stainless steel plates, multiply the P value from the table by 2.
For aluminum plates, multiply the P value from the table by 0.7.
You can also calculate the bending force of the press brake using our tonnage calculator specially designed for press brakes.
> Click to use press brake tonnage calculator
Parallelism control and configuration
Ram parallelism is controlled by a solid anti-torsion bar that is connected to both side oil cylinders.
The upper ram is calibrated parallel to the V matrix at the factory, but if recalibration is necessary, follow these steps:
- Locate the torsion bar link connected to the upper ram on the rear (left side) of the machine.
- Loosen the screw (M8/M10) on the torsion bar.
- Use the appropriate wrenches to turn the outer flat part 15° to 30° clockwise or counterclockwise, which will rotate the inner eccentric pin.
- Tighten the screw (M8/M10) and check the parallelism of the upper ram using a test curve.
- Repeat the procedure until you obtain the desired precision.
Pressure Brake Troubleshooting
Press the brake The machine cannot start
- Check the input power supply.
- Check whether the Emergency Stop is enabled.
- Check for broken fuses.
- Check the transformer output.
Ram couldn't be lower
- Check the pedal cable for possible broken wires.
- Check that limit switch.
- Check whether the engine rotation is incorrect.
- Check that the microswitch inside the pedal is working.
The bend angle is not uniform over the entire length of the bend
- Upper tool or lower tool worn.
- The surface of the machine table and the bottom of the V-die are dirty.
Upper and lower tools not aligned correctly.
Failure | Reasons | Troubleshooting |
---|---|---|
The system does not work without pressure | 1. Negative engine rotation | Change the direction of engine rotation |
2. Main overflow valve blocked | Clean the main overflow valve | |
3. The electromagnetic valve does not work | Check electrical and electromagnetic coils | |
Ram Slider Cannot Go Up | Stuck valves | Clean electromagnetic valves |
Slider automatically declines | Stuck valves | Clean electromagnetic valves |
Going up and down normally, but there is no strength in the flexion | Stuck valves | Clean electromagnetic valve |
Leak in components, piping connections and oil cylinder | Sealing parts are aging. | Change sealing rings |
Press brake maintenance
Anyone operating and maintaining this press brake must read and completely understand this manual. Only by strictly following the instructions can ideal results be achieved.
A designated person must be assigned to the machine and operators must have working knowledge of machine operation and production safety.
The bending force applied to the workpiece must not exceed the nominal force. To extend the life of molds, it is important not to damage them due to inadequate bending width, especially when bending narrow sheets. In these cases, the working pressure must be reduced appropriately. For each length of 630mm, the bending load should not exceed 400KN.
The sheets to be bent must be centered in the machine and must not be loaded unevenly, as this can compromise the precision of both the parts and the machine. If a workpiece needs to be bent on one side only, the load should not exceed one-quarter of the rated force and bending should be performed on both sides.
The hydraulic oil in the tank should be changed after the first month of use and changed again within a year. The oil must be maintained at a temperature between 15-60°C (if the temperature is too high, a cooler must be installed).
This press brake requires periodic lubrication, which must be carried out according to the working conditions and at all designated lubrication points.
The user must always have maintenance accessories on hand.
After any heavy repairs, the machine's accuracy must meet factory standards.
Hydraulic oil
Regularly check the oil level in the tank.
Change the oil for the first time after 500 working hours and then every 2,000 working hours.
Use oil that meets the characteristics of the specified oil type.
The brand value of hydraulic oil is equal to the average viscosity when the temperature is 40°C.
If the working pressure and temperature of the hydraulic system are higher and the working speed is slower, choose a higher brand hydraulic oil.
It is also recommended not to use the machine at very low temperatures (below -5°C), but if this happens, leave the machine running at idle speed for a while. An oil heater can be installed in the circuit if necessary.
Under normal working conditions, the oil temperature should not exceed 70°C. Under special conditions, an oil cooler may be required.
It is recommended to use ISO VG46# anti-wear hydraulic oil (with an average viscosity of 46mm2/s at 40°C). If the machine operates below 5°C for a long time, you can choose ISO VG32# hydraulic oil.
Refill or replace only with the same type of oil as follows:
- FIAT-HTF 46, ENERGOL HLP 46, ESSO NUTO H46, SHELL-TELLUS S46, TOTAL-AZOLLA 46
Oil filter
- Regularly clean the oil filter by rinsing and brushing with solvent.
- The oil filter must be changed when cleaning is not possible or when it is damaged.
- Use the same type of oil filter when replacement is necessary.
Lubrication
Regularly check the lubrication points and lubricate them weekly with high-quality grease. For parts exposed to wear and that do not have lubrication points, they must be lubricated twice a week. (For more information, see the lubrication diagram.)
Electrical terminal
Regularly inspect all connections on the main panel and electrical switches and tighten screws as necessary. Replace any faulty fuses and signal lights.
Mechanical parts
It is recommended to check the following at least once a month:
- The torsion bar bearing is properly secured
- Slides are not worn
- The cylinder rod is properly secured
- The upper ram is properly secured
Safety guarantee and main construction of bending machine
Observation:
This section applies to the press brake machine with specific requirements and is for reference only for other machines.
To ensure the safety of personnel and equipment, safety equipment has been designed. The operator must not alter, remove or disable safety equipment.
Light beam/laser beam
The machine is equipped with a light beam or laser (according to customer request). If the operator interferes with the light curtain, the safety module will activate.
The ram will not be able to descend, preventing the operator from being injured.
Security grid
The machine has a safety grille on the side and rear.
This network keeps the operator away from dangerous areas and is connected to the electrical system via a safety switch. When the safety grille is opened, the electrical system is activated and the machine cannot operate.
Emergency stop
There is an emergency stop button located on the handle control station and the overhead control station.
In case of operation error or any other accident, pressing the emergency stop button will cause the machine to stop all actions.
Hydraulic system
A falling ram is extremely dangerous. To prevent this, the system is equipped with a safety lift valve.
The valve cores of the switching valve and safety lift valve have a monitoring signal.
If the valve core is abnormal, the monitoring signal will stop the electrical system to prevent injury from falling ram.
If the shift valve and safety lift valve cores cannot be reset, inspect the valve.
Problems solution
Normal operation is safe.
In case of unusual accidents, or during maintenance or repair of the machine, lock the safety grille, press the emergency stop button located inside the uprights and seek help.
If your hands or any other part of your body is trapped by the punch or sheet, press the emergency button, inspect the situation and restart the machine.
Change the operating mode to the “inch” position.
Then press the handle return button and the ram will return, pulling the attached parts.
General drawings of the press brake
Here are the drawings:
- Press the brake Drawing 1
- Press the brake drawing 2
- Press the brake Drawing 3
- Press Brake Drawing 4
piece number | Name | Amount |
1 | Control Panel | 1 |
two | Bearing block | two |
3 | Torsion bar | 1 |
4 | pendulum pole | two |
5 | cylinder base block | two |
6 | Connect the pole | 4 |
7 | Oil Cylinder | two |
8 | Guide rail | two |
9 | cylinder cover | 1 |
10 | Single Control Valve | 1 |
11 | Tube Connector | 1 set |
12 | pipe | 1 set |
13 | Oil tank | 1 |
14 | Manometer box | 1 |
15 | Coupling | 1 |
16 | gear pump | 1 |
17 | Main engine | 1 |
18 | Level meter | 1 |
19 | Filter 4-50 | 1 |
20 | Filter 250 | 1 |
21 | Close valve | 1 |
22 | FWMBM | 1 set |
23 | Travel Switch Saddle | 1 |
24 | Travel switch | two |
25 | Travel switch pole | 1 |
26 | Connection plates | 16 sets |
27 | Die inferior | 1 |
28 | Upper punch | 1 set |
29 | press plate | 52 |
30 | Star strap | 4 |
31 | Back gauge motor | 1 |
32 | Ball screw | two |
33 | Guide rail | two |
34 | Stop the beam | 1 |
35 | Stop your finger | 2 sets |
36 | Foundation screw | 4 |
37 | Controller system | 1 set |
38 | Electrical system | 1 set |
39 | valve system | 1 set |
Download the Installation and Operation Manual PDF file:
- ESA S630 Installation and Operation Manual
- Estun E21 Installation and Operation Manual
- Estun E200+ Installation and Operation Manual
- Estun E200P Installation and Operation Manual
- CybTouch 8 Installation and Operation Manual
- CybTouch 12 Installation and Operation Manual
- Delem DA41 installation and operation manual
- Delem DA52S installation and operation manual
- Delem DA53T installation and operation manual
- Delem DA56 installation and operation manual
- Delem DA58T installation and operation manual
- Delem DA66T installation and operation manual
- Delem DA69T installation and operation manual