1. Laser welding gas
Shielding gas will be used in laser welding to improve the welding effect and prevent deposition on laser tools.
According to different uses, it can be divided into:
- Auxiliary gas (MDE gas)
- Shielding gas
- jet gas
2. Why do you need shielding gas?
Continuous laser welding is a process that uses high-energy laser beams as a heat source to melt the surface of a part and obtain an excellent welding joint.
During high-power laser welding, the laser heats the material and melts the part, but the high temperature also causes the metal to gasify, forming metal vapor plasma.
The plasma weakens the energy reaching the surface of the part and affects the stability of the molten pool.
To suppress plasma generation and ensure stability, a shielding gas with high ionization energy must be blown during the process. Shielding gas also isolates air and reduces welding spatter, resulting in a smooth, uniform weld surface.
3. The protective gas functions
In laser welding, the use of shielding gas will have an impact on the formation of the weld, its quality, penetration and width.
In most situations, blowing shielding gas will result in a positive effect on the weld, but it can also have unfavorable impacts.
3.1 Positive effects
(1) Suitable shielding gas can effectively protect the weld pool and reduce or even eliminate oxidation.
(2) It can also reduce spatter during welding.
(3) The weld pool will solidify evenly and have a uniform and attractive shape.
(4) Suitable shielding gas can also reduce the shielding effect of the metal vapor plume or plasma in the laser, leading to increased laser utilization.
(5) In addition, the correct use of shielding gas can reduce the porosity of the weld.
As long as the correct gas type, flow rate and blowing mode are selected, the desired results can be achieved.
However, incorrect use of shielding gas can have negative effects on welding.
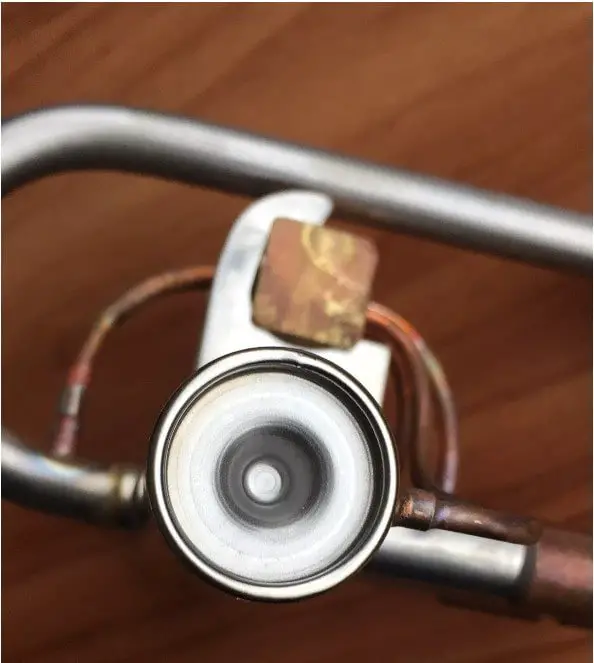
3.2 Negative effects
(1) Incorrect use of shielding gas may result in weld degradation;
(2) Choosing an inappropriate type of gas may cause cracks in the weld and also reduce the mechanical properties of the weld;
(3) Incorrect gas flow rate selection may lead to increased oxidation of the weld (whether the flow rate is too high or too low), or the weld pool metal may be severely disrupted by external forces, leading to collapse or irregular formation of the weld;
(4) Selecting an incorrect gas flow method may result in a lack of weld protection, or even have no protective effect, or have a negative impact on weld formation;
(5) The penetration of the welding seam will be affected by the flow of shielding gas, especially when welding thin plates.
4. Types of shielding gas
Shielding gases commonly used for laser welding are nitrogen (N2), argon (Ar), and helium (He). Their physical and chemical properties differ, so their effect on the weld also varies.
4.1N 2
The ionization energy of N 2 is moderate, with a value higher than that of Ar and lower than that of He.
Under the action of a laser, the ionization of N2 is generally moderate, which can reduce the formation of plasma clouds and increase the effective utilization of the laser.
However, when nitrogen reacts with aluminum alloy or carbon steel at a certain temperature, it produces nitride, which can result in a decrease in the toughness and brittleness of the weld and have a negative impact on the mechanical properties of the welded joint.
Therefore, it is not recommended to use nitrogen as a shielding gas when welding aluminum alloys or carbon steel.
On the other hand, when nitrogen reacts with stainless steel, it can improve the strength of the welded joint and positively affect the mechanical properties of the weld.
As a result, nitrogen can be used as a shielding gas when welding stainless steel.
4.2 Air
The ionization energy of Air is relatively low and, under the action of a laser, its degree of ionization is relatively high, which can negatively impact the control of the formation of plasma clouds and the effective use of the laser.
However, Ar's low reactivity with common metals and its relatively low cost make it an attractive option. Furthermore, its high density allows it to effectively sink above the weld pool, providing a better protective environment.
For these reasons, Ar is commonly used as a conventional shielding gas.
4.3 He
The ionization energy of He is the highest and, under the action of a laser, its degree of ionization is very low, making it effective in controlling the formation of plasma clouds.
The laser can act effectively on metals, and its low reactivity and low activity make it a good shielding gas for welding.
However, He's high cost makes it unsuitable for widespread use in mass-produced products. It is typically used in scientific research or high-value products.
5. Shielding gas blowing mode
At present, there are two main shielding gas blowing methods: one is shaft side blowing shielding gas, as shown in Figure 1; the other is coaxial shielding gas, as illustrated in Figure 2.
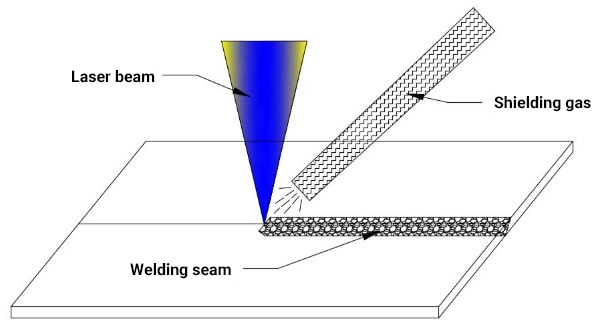
Fig. 1 Side of the lateral shaft blowing shielding gas
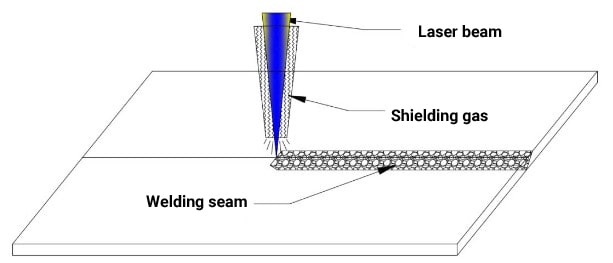
Fig. 2 Coaxial shielding gas
Choosing between the two shielding gas blowing methods involves a comprehensive consideration of many factors.
In general, it is recommended to use the shielding gas side blowing method.
6. Shielding gas blowing mode selection principle
First, it is important to note that the term “oxidation” of solder is simply a colloquial name.
Theoretically, it refers to the chemical reaction between harmful components in the air and the weld, which leads to a decrease in the quality of the weld.
The common cause of this is the reaction between the weld metal and elements such as oxygen, nitrogen and hydrogen in the air at high temperatures.
To prevent the weld from being “oxidized”, it is necessary to reduce or eliminate contact between the weld metal and these harmful components at high temperatures.
This high-temperature state encompasses not only the molten pool metal, but also the entire process, from the moment the weld metal is melted to the moment it solidifies and cools below a certain temperature.
For example, titanium alloys can readily absorb hydrogen at temperatures above 300°C, oxygen at temperatures above 450°C, and nitrogen at temperatures above 600°C.
Therefore, it is essential to protect the titanium alloy weld after solidification and the stage below 300°C, or it will become “oxidized”.
It is evident from this that the use of shielding gas must protect not only the weld pool in real time, but also the newly solidified area of the weld.
As a result, shaft side blow shielding gas is generally used, as shown in Figure 1.
Compared to coaxial protection (Figure 2), this method offers a wider scope of protection, especially for the area where the weld has just solidified.
In practical applications, not all products can use the side shaft side blowing protection method.
For some specific products, only coaxial shielding gas can be used, and the specific choice will depend on the product structure and joint shape.
7. Selection of specific shielding gas blowing mode
7.1 Straight welding
As depicted in Figure 3, the product has a linear weld shape, with the joint shape being a butt joint, lap joint, inner corner joint or lap welding joint.
For this product, it is more favorable to use the side shaft side blow shielding gas method shown in Figure 1.
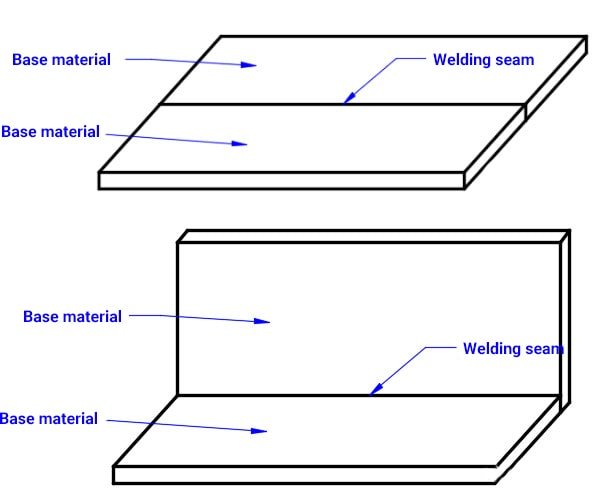
Fig.3 Straight welding
7.2 Closed flat graphic welding
As depicted in Figure 4, the product has a weld shape that is a flat circular shape, a flat multi-sided shape, a multi-segment flat linear shape or other closed shapes, and the joint shapes can be butt joints, lap joints, overlap . joints, etc.
Therefore, the product is more suitable for using the coaxial shielding gas method shown in Figure 2.
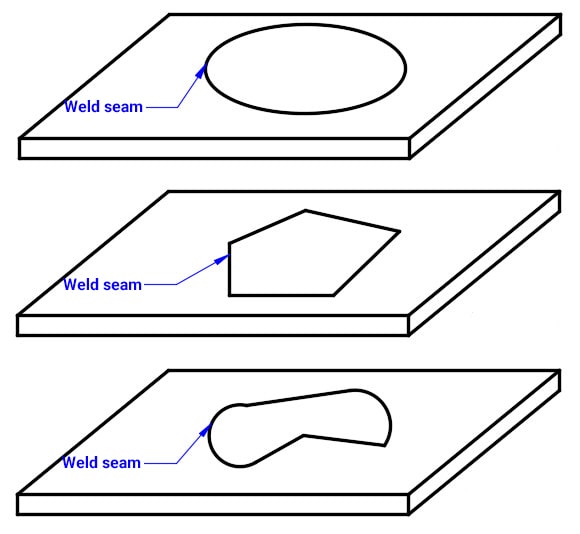
Fig. 4 Closed flat graphic weld
Shielding gas selection has a direct impact on the quality, efficiency and cost of welding production.
However, due to the diversity of welding materials, the selection of welding gas is more complex in actual welding practice.
To choose the most suitable shielding gas, it is important to take into account the welding material, welding method, welding position and the desired welding result.
The only way to determine the best option is to perform a test weld.
8. Effect of shielding gas on weld morphology
In addition to choosing the appropriate shielding gas based on the welding material, it is also necessary to examine the impact of shielding gas blowing angle, direction and flow rate on weld morphology.
Studies have been carried out to understand the influence of different shielding gas blowing angles on the weld, under the same welding conditions.
The experimental results show that, under the same control of other variables, the influence trend of weld morphology remains the same under different flow rates.
However, as the flow rate increases, the effect on weld penetration becomes more noticeable, while the impact on the weld surface and width decreases.
To specifically study the effect of blowing angle, the flow rate was maintained at 5 L/min, while other variables were controlled, and only the blowing angle was changed.
The test results are shown in Figure 5, with a metallographic diagram of the weld cross-sectional morphology displayed in Figure 6.
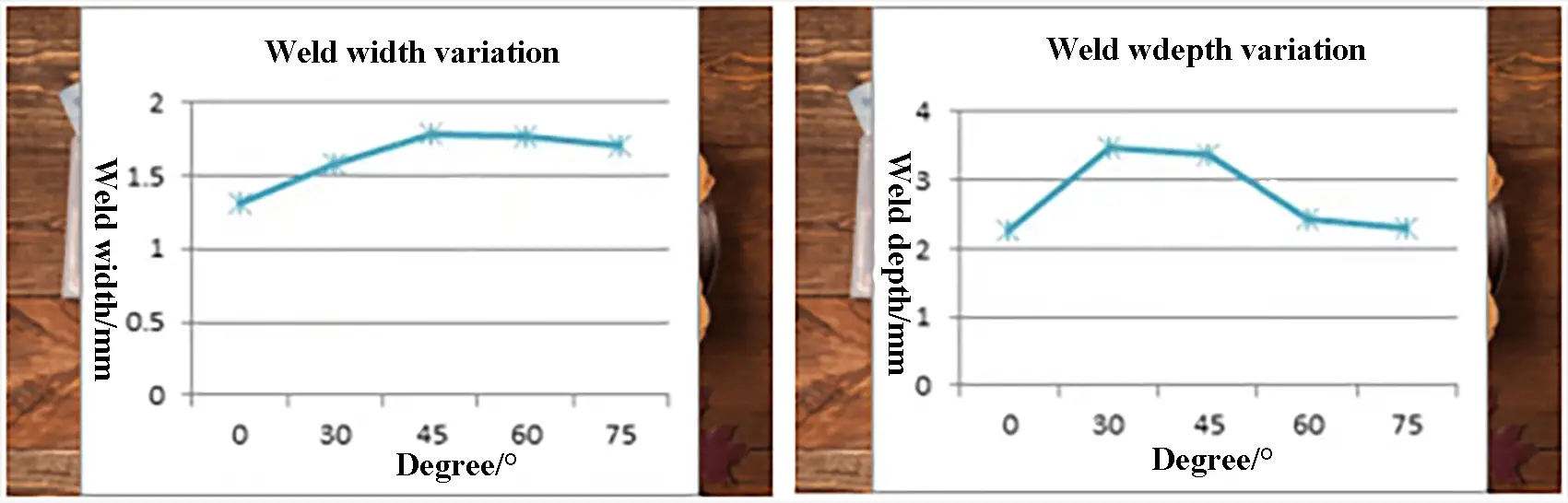
Fig. 5 Effect of different blowing methods on weld penetration and width
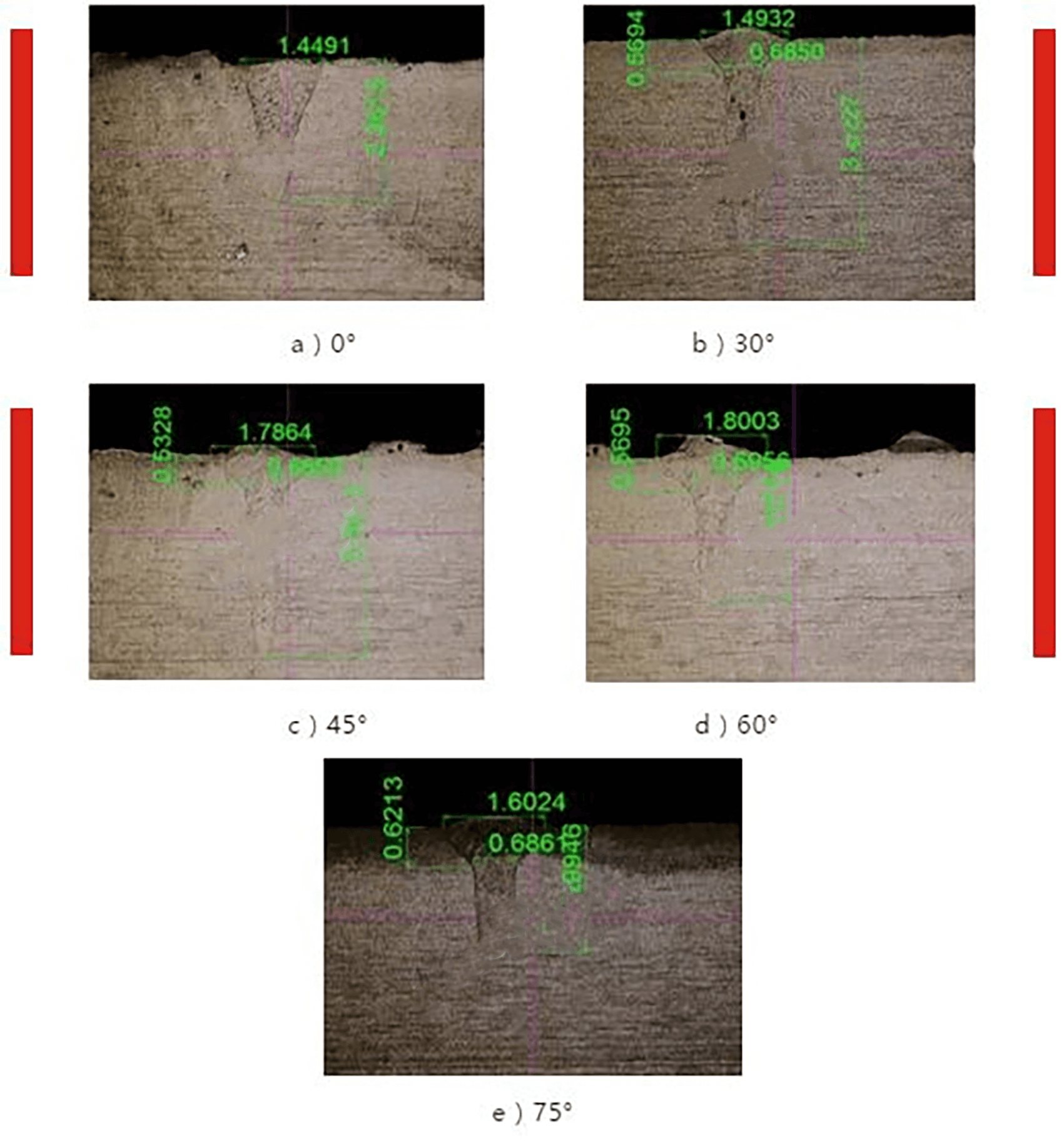
Fig. 6 Weld morphology at different blowing angles
According to the experimental data, the weld penetration initially increases and then decreases as the blowing angle increases.
At 0° or above 45°, penetration decreases significantly. Maximum penetration is achieved at a blowing angle of 30°.
The width of the weld is determined by the reduction in laser intensity caused by the plasma and the effect of gas flow on the weld pool.
With a blowing angle of 0°, the casting width is the smallest. As the blow angle increases, the casting width increases, but there is little change in the weld width when the angle is above 45°.
Results analysis
The impact of the shielding gas on the weld morphology is mainly controlled by adjusting the plasma size, which determines the laser power density that reaches the part surface.
Based on the metallographic diagram of the weld cross section, it can be seen that the weld morphology tends toward thermal conduction welding at 0° or 75°, while deep penetration welding is evident at 30° and 45°.
To conclude, under the same welding process parameters, it is recommended to use a blowing angle of 30° for greater penetration, 45° for a larger surface width and 0° or 75° for a smaller and larger fusion width.