Understanding Curvature Tolerance
Curvature Tolerance Concept
Bending allowance is a critical parameter in sheet metal manufacturing that helps determine the precise flat length of sheet material required to achieve the desired dimension after bending. Refers to the arc length of the bend measured along the neutral axis of the material. The neutral axis is an imaginary line within the bending region where the material neither expands nor compresses during the bending process.
Calculation of bending tolerance depends on several factors such as sheet metal thickness, bending radius and bending angle. In SOLIDWORKS, users can define bend tolerance values to gain precise control over the development of sheet metal parts.
Meaning of Curvature Tolerance
Accounting for bend allowance is essential in the production of precisely bent sheet metal parts. Ensures that the developed size of the part matches the design intent and ensures that bends are made at the correct angles. This significantly reduces errors, material waste and rework in the manufacturing process.
Understanding and applying bend tolerance values allows designers and manufacturers to predict material behavior during bending and avoid common sheet metal problems such as over or under bending. Proper use of bend tolerance in SOLIDWORKS increases the efficiency of simulations and design of complex sheet metal parts.
Factors Influencing Curvature Tolerance
Material properties
Material properties play a significant role in determining bend tolerance in SolidWorks. Different materials have varying degrees of flexibility and resilience, affecting the bending tolerance value. For example, metals such as aluminum, steel and stainless steel have distinct elastic properties, leading to different bending tolerance values for each material.
Bending angle
Bending angle is another crucial factor that influences bending tolerance. As the angle increases, the bending margin generally increases as well. A larger bend angle requires more material to be deformed in the bending process, thus necessitating a larger bend tolerance. In SolidWorks, the bend angle can be adjusted to generate the desired bend tolerance value for the design.
Material thickness
Material thickness is directly related to bending tolerance, as thicker materials require more deformation and therefore a larger tolerance. Correct assessment of material thickness is essential in SolidWorks for accurate calculations and efficient sheet metal designs. Thicker materials also require higher forces for bending operations, resulting in greater equipment and tooling requirements.
Differentiating bend allowance and bend deduction
Curvature Deduction Definition
Bend Deduction, or BD, is a terminology used in sheet metal manufacturing. Refers to the difference between the bend tolerance and twice the external indentation of the material. This value is an important consideration when determining the overall flat length of sheet metal parts during the bending process. It helps manufacturers create precise sheet metal components that adhere to desired dimensions.
Curvature tolerance versus curvature deduction
When working with SOLIDWORKS, designers have options to choose between using bend allowance and bend allowance values in their sheet metal designs. Both are useful in determining the final flat pattern of the sheet metal part and are essential for accurate manufacturing.
Bend allowance is the arc length of the bend measured along the neutral axis of the material. Represents the length of the sheet being stretched or compressed during the bending process. The neutral axis refers to the region of the material where there is no stress or deformation.
Parameter | Description |
---|---|
Curvature tolerance | Bending arc length along the neutral axis of the material |
Curvature deduction | Difference Between Bending Tolerance and Twice External Indentation |
BD | Abbreviation for curvature deduction |
When using SOLIDWORKS, it is essential to enter the correct bend allowance or bend allowance value, depending on the method selected. This ensures that the final sheet metal part will have the desired dimensions and fit correctly into the assemblies.
Both methods have their benefits and considerations. Bending tolerance calculations provide a more accurate representation of the bending process and consider the behavior of the material during bending. Bend deduction simplifies the calculation process and is easier to understand for those new to sheet metal design.
In conclusion, understanding the differences between bend allowance and bend allowance is crucial for accurate sheet metal design in SOLIDWORKS. Accurately entering these values ensures that the final sheet metal component meets design specifications and fits perfectly into the desired assembly.
Method for calculating bending tolerance
You can directly use our bending tolerance calculator to calculate the bending tolerance. In addition, the manufacturing calculator can also help you calculate K factor, Y factor, bending allowance, bending deduction, etc.
You may be wondering what exactly bend tolerance is if you've never worked with sheet metal before.
When a sheet is bent in a press brake, the part of the sheet close to and in contact with the punch lengthens to compensate for the given bend.
If you compare the length of this piece before and after folding, you will see that they are different.
As an engineer, if you don't compensate for this variation, the final product will not have accurate dimensions.
This is most critical for parts where you need to maintain a tighter tolerance or accuracy.
In this post, I cover some of the basic issues and principles you must deal with on a regular basis when working with sheet metal.
Before we begin, I want to comment on something – there is really no scientific method or formula for determining the exact bend tolerance calculation, because there are many factors at play during the production of your sheet metal part.
For example, the actual thickness of the material, an infinite variety of tool conditions, forming methods, and so on.
There are many variables here, and in reality, many methods are used to calculate bend tolerance.
Trial and error is probably the most popular method, while bend tables are another commonly used technique.
Bending tables are typically available from metal suppliers, manufacturers, and engineering books. Some companies develop their own bending tables based on their standard formulas.
Now, let's go back to Solidworks. How exactly does Solidworks calculate bend tolerance? Solidworks uses two methods: bend allowance and bend deduction.
Bending tolerance
I will explain what these methods are and show how they are used in Solidworks.
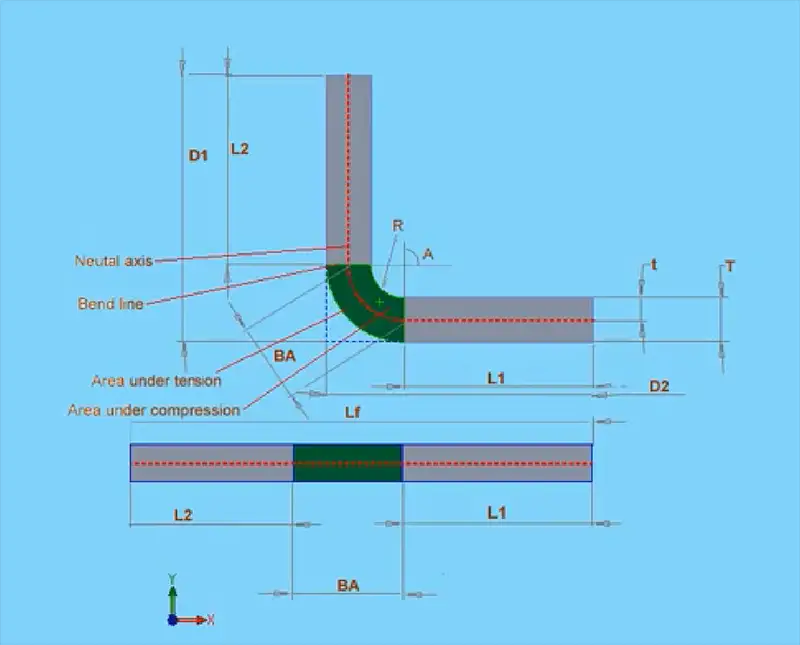
The bend tolerance method is based on the formula that appears in my diagram.
- Lf = L1 + L2 + BA
- BA = bend tolerance
The total length of the flattened sheet is equal to the sum of L1 (the first length), L2 and the bending allowance.
The bend tolerance region is shown in green in my diagram. This is the region where all deformation occurs during the bending process.
Generally, the bending tolerance will be different for each combination of material type, material thickness, bending radius, bending angle and different machining processes, types, speeds and so on. The list of potential variables is extensive.
The bending allowance value from sheet metal suppliers, manufacturers and engineering textbooks is provided in bending tables. A bend table looks like the following Excel spreadsheet.
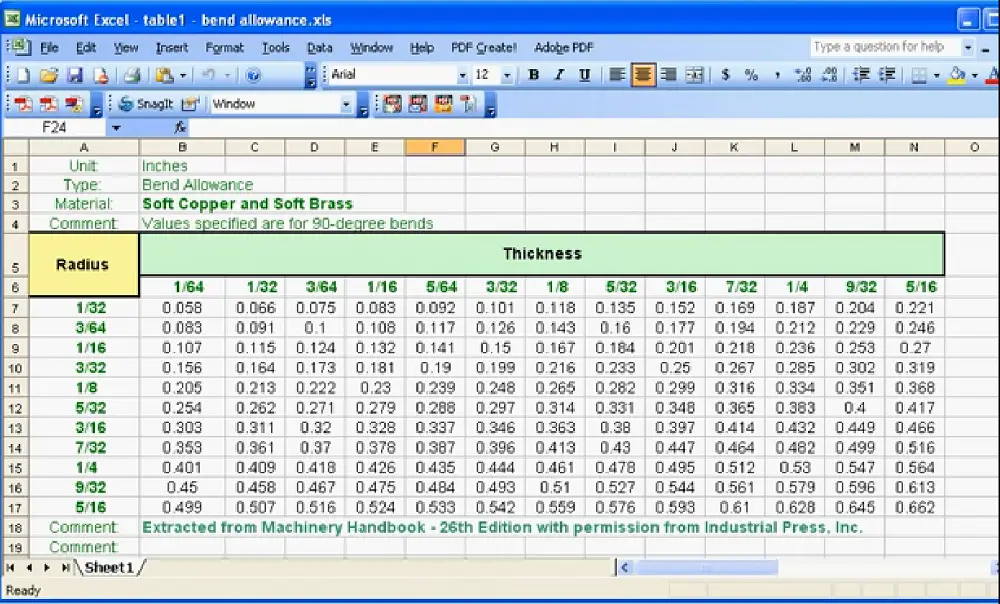
The bend table approach is probably the most accurate method for calculating bend tolerance.
You can enter your data manually into a bend angle and radius matrix. If you are unsure of the bend tolerance value, you can run some tests.
You need to take a piece of exactly the same sheet metal that you will use to manufacture your part, and then bend it using the same processes that you will use during machining. Just take a few measurements before and after folding and based on the same information you can adjust the required fold allowance.
Curvature deduction
Another method used by Solidworks is the bend deduction method.
The formula is as follows:
- Lf = D1 + D2 – BD
- BD = Double Deduction
The flattened length of the pieces, Lf, is equal to D1 plus D2 minus the bend deduction.
Like bend tolerance, bend deduction comes from the same sources: tables and manual testing.
As you can see, it is easy to understand how these values are related to each other based on the information provided by these formulas.
- L1 + L2 + BA = D1 + D2 – BD
K Factor
Another method for calculating bend tolerance uses the K factor.
K represents the displacement of the neutral axis.
The general principle of this formula is this: the neutral axis (shown in red in my diagram) does not change during the bending process. During the bending process, the material inside the neutral axis will be compressed and the material outside the neutral axis will be stretched. The neutral axis will be closest to the inner curve (indicated in blue in the diagram). The more the part bends, the closer the neutral axis will be to the inside of the part.
The bend tolerance calculation formula with K factor is shown below:
BA = 2πA(R+KT)/360
- π=3.14
- A=Angle (degrees)
- R = radius of curvature
- K=Neutral axis displacement (K factor) t/T
- T = Material Thickness
- BA=Bending allowance length
The K factor is equal to t, which is the travel distance to the neutral axis, divided by large T, which is the thickness of the material.
In this formula, the bend tolerance is equal to 2 times pi multiplied by A (the angle) multiplied by the sum of R (the bend radius) and the K factor multiplied by T (the thickness of the material). So, you divide all of this by 360.
In theory, the K factor can be between 0 and 1, but for practical purposes, it is typically between 0.25 and 0.5.
- K Factor = 0 – 1 (in theory)
- K Factor = 0.25 – 0.5 (practical)
For example, hard materials like steel have a higher K-factor, like 0.5, while soft materials like copper or brass will have a lower K-factor, closer to 0.
And don't worry, this is the last formula we'll look at in this lesson. It may seem a little confusing now, but with some practice it will become second nature.
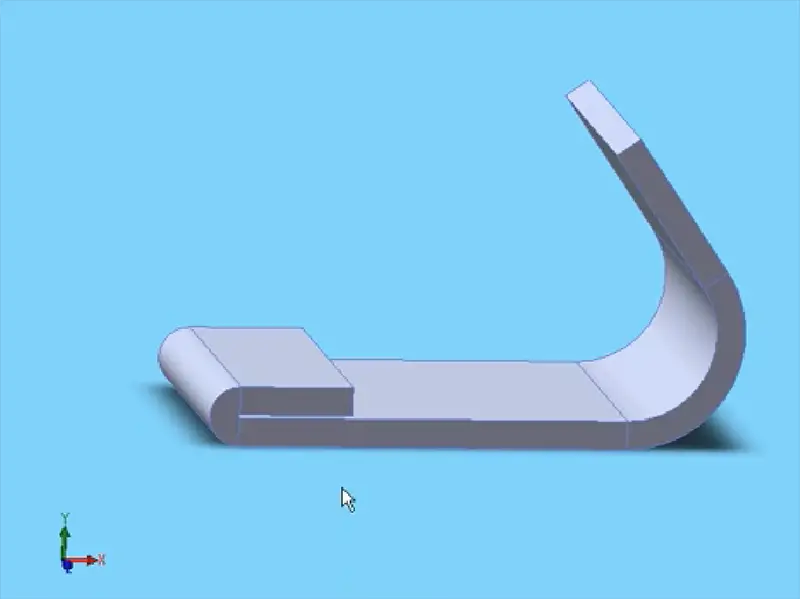
One last point: let's take a look at the example. There is a sheath on this part that has a K factor of about 0.3. On the other hand, a smooth curve, like the gradual curve on the other side of this piece, has a higher K-factor of about 0.5. And this concludes our lesson on bend tolerance.
Further reading:
- How to calculate bending tolerance, bending deduction and K factor?