Steel rolling refers to the pressure processing process of changing the shape of steel ingots or steel billets between rotary rolling mills. It can be divided into hot rolling and cold rolling.
Hot rolling requires heating the raw material to 1100-1250 ℃ and implementing high-temperature rolling production.
Hot rolled steel strip is a typical hot rolling production process.
At present, the control technology for hot-rolled steel strip is mature, the instrument configuration is advanced, and the product quality is relatively stable, with high production line operation rates.
However, due to the complexity of the lamination process, the functioning of each process and the condition of the equipment can affect the quality of the product, leading to defects in the final product.
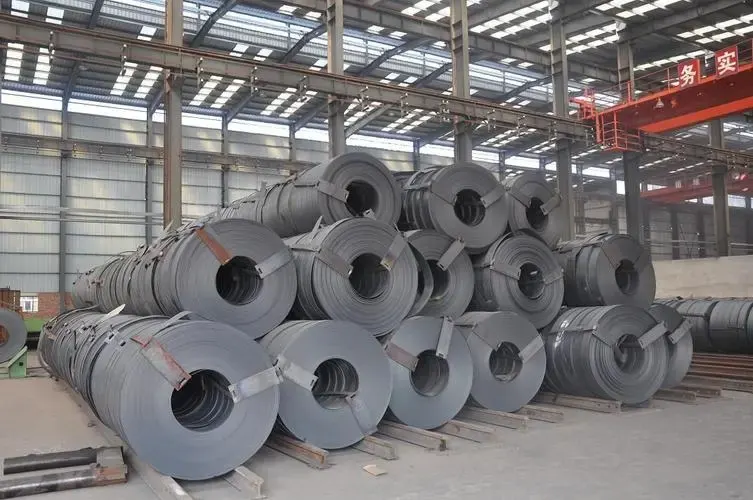
Common Defects of Hot Rolled Steel
I. Pressed oxide scale

- Defect characteristics
Pressed oxide scale is a surface defect formed by the compression of oxide scale on the surface of the steel strip during hot rolling. Depending on its cause, it can be divided into furnace-generated oxide scale (primary), rolling-generated oxide scale (secondary), or roll surface oxide scale that comes out and is compressed into the steel strip (secondary).
- Causes
①Severe longitudinal cracks on the surface of the steel billet;
②Inadequate heating process or heating operation of the steel billet, making it difficult to remove the primary scale;
③Low pressure in high pressure descaling water or nozzle blockage during the rolling process, resulting in the production of oxide scale being compressed on the surface of the steel strip;
④Very fast rolling pace or insufficient cooling of the rolls, causing the oxide film on the surface of the roll to peel off and be compressed on the surface of the steel strip.
- Dangers
It affects the surface quality of the steel strip and the coating effect.
- Prevention and elimination methods
①Strengthen steel billet quality inspection. Billets with severe longitudinal cracks on the surface must be cleaned and qualified before use;
②Develop a reasonable heating process for the steel billet and heat it according to specifications;
③Regularly check the equipment of the high-pressure descaling water system to ensure the pressure of the descaling water and avoid nozzle blockage;
④Reasonably control the rolling rhythm, ensure the cooling effect of the rollers, and prevent the oxide film on the roller surface from peeling off.
II. Scar

- Defect characteristics
The scar is an irregularly shaped raised metal sheet fixed to the surface of the steel strip, shaped like a leaf, feather, bar, fish scale, tip of a tongue, etc.
There are two types of scars: one is attached to the steel body and bends on the surface of the plate, not easy to fall off; the other is not connected to the steel body, but is glued to the surface of the plate and is easy to fall off, forming a relatively smooth hole after falling.
- Causes
①The original scar or heavy skin defect on the surface of the billet was not cleaned and remained on the surface of the steel strip after rolling;
②Flame cleaning residue on the surface of the billet, which was pressed onto the surface of the steel strip during rolling.
- Dangers
This may cause peeling or pitting of the metal during processing and subsequent use.
- Prevention and elimination methods
Strengthen billet quality inspection and clean any scars or flame cleaning residue on the billet surface before washing.
III. Bubbles

- Defect characteristics
Bubbles are circular or elliptical protuberances on the surface of the steel strip that are irregularly distributed. Its outer edge is relatively smooth. After the bubbles are crushed, the surface of the steel strip may appear cracked or peeling.
Some bubbles do not protrude and have a shiny surface after being flattened, and the cut surface has a layered structure.
- Causes
①A lot of gas is accumulated inside the billet due to poor deoxidation or inadequate nitrogen blowing;
②The billet has been in the oven for a long time and the subcutaneous bubbles are exposed and accumulate.
- Dangers
May cause poor layering or welding during processing and subsequent use.
- Prevention and elimination methods
①Strengthen billet quality inspection and avoid using billets with exposed blister defects;
②Strictly follow the specifications for heating the billet and avoid keeping it in the oven for a long time.
4. Rolling crush

- Defect characteristics
The phenomenon of multiple layers overlapping or rolled, perforated, torn, etc. on the surface of the steel strip is called rolling crushing.
- Causes
①Improper adjustment of the roller gap or poor correspondence between the shape of the roller and the shape of the input billet, resulting in uneven extension of the steel strip;
②Irregular local heating temperature of the billet or uneven temperature of the rolled part;
③The opening degree setting of the finishing side guide plate is unreasonable;
④The flow rate during precision rolling is inconsistent.
- Dangers
Steel plate with rolling crush defects cannot be used due to interruption of the rolling process.
- Prevention and elimination methods
①Configure the roll shapes reasonably and pay attention to adjusting the roll gap;
②Strengthen billet heating temperature control and ensure uniform temperature of rolled part;
③Reasonably set the opening degree of the finishing side guide plate;
④Maintain a consistent flow rate during continuous rolling.
V. Roll mark

- Defect characteristics
Roll marks are concave-convex defects with irregular shapes that are periodically distributed on the surface of the steel strip.
- Causes
The rolls are cracked, have localized chips, or have foreign objects adhered to their surface, resulting in a concave-convex surface on the roll, which is pressed onto the surface of the steel strip during rolling or finishing processing, forming concave-convex defects.
- Dangers
Convex roll marks can cause bending defects during subsequent rolling processes, while concave roll marks can cause holes during subsequent rolling processes.
- Prevention and elimination methods
①Regularly inspect the surface quality of the rollers and deal with rollers with chips or foreign objects in a timely manner;
②During the rolling process, check the surface quality of the rolls in time when abnormal situations such as steel jamming, tail throwing and bearing crushing occur, and avoid damage to the roll surface or adhesion of foreign objects;
③Immediately stop the machine to check the surface quality of the rollers when roller marks are found.
SAW. Flattening

- Defect characteristics
The phenomenon of oval-shaped steel coils is called flattening.
- Causes
①The steel coil is subject to excessive impacts during handling;
②The tension of the steel coil during winding is very low, and the coils are stacked horizontally or with multiple layers.
- Dangers
It affects the packaging and handling of steel coils, and coils that are too flat cannot be used.
- Prevention and elimination methods
①Handle steel coils carefully;
②Reasonably set the winding voltage, control the number of horizontal stacking layers, and use vertical stacking if necessary.