The press brake is a widely used bending machine that has achieved hydraulic efficiency. As a critical equipment for sheet metal processing, it is irreplaceable and plays a decisive role in determining product quality, processing efficiency and accuracy.
Typically, the press brake is an upper piston press composed of several components, including a frame, sliding block, hydraulic system, front loading rack, rear gauge, mold and electrical system, as illustrated in Figure 1.
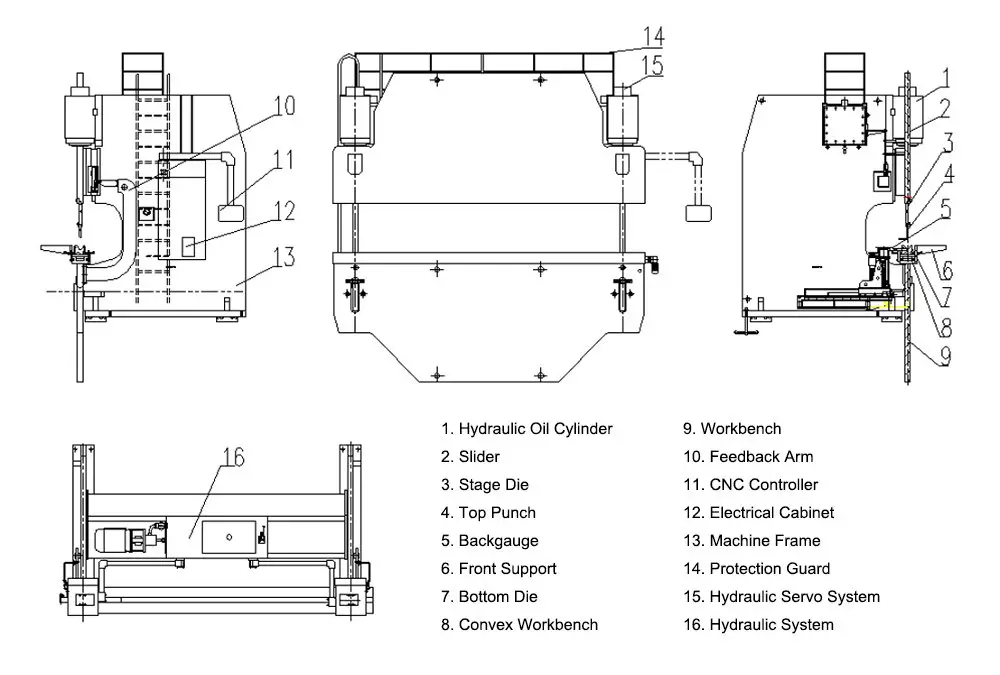
- Left vertically
- Left oil cylinder
- Oil tank
- Right hydraulic cylinder
- To knock
- Desktop
The hydraulic system of a press brake operates by forming vertical downward pressure through the use of two parallel working hydraulic cylinders. This pressure drives the die into the bending beam, allowing the bending process to complete.
The hydraulic control system, which acts as the “brain” of the press brake, is responsible for controlling the synchronized operation of the bending process and the positioning of the hydraulic cylinders during full loading of the press brake.
In this article, we will explore how the press brake hydraulic system works.
Hydraulic system
For each bending movement, the typical bending process of the upper bending beam includes:
(1) Starting the oil pump
The motor rotates in the direction indicated by the pump arrow, which is clockwise, driving the axial piston pump. The oil is then discharged through the piping and into the valve plate and electromagnetic overflow valve before returning to the tank. When valve number 19 is closed, the oil in the lower cavity of cylinder number 20 is maintained in a fixed position.
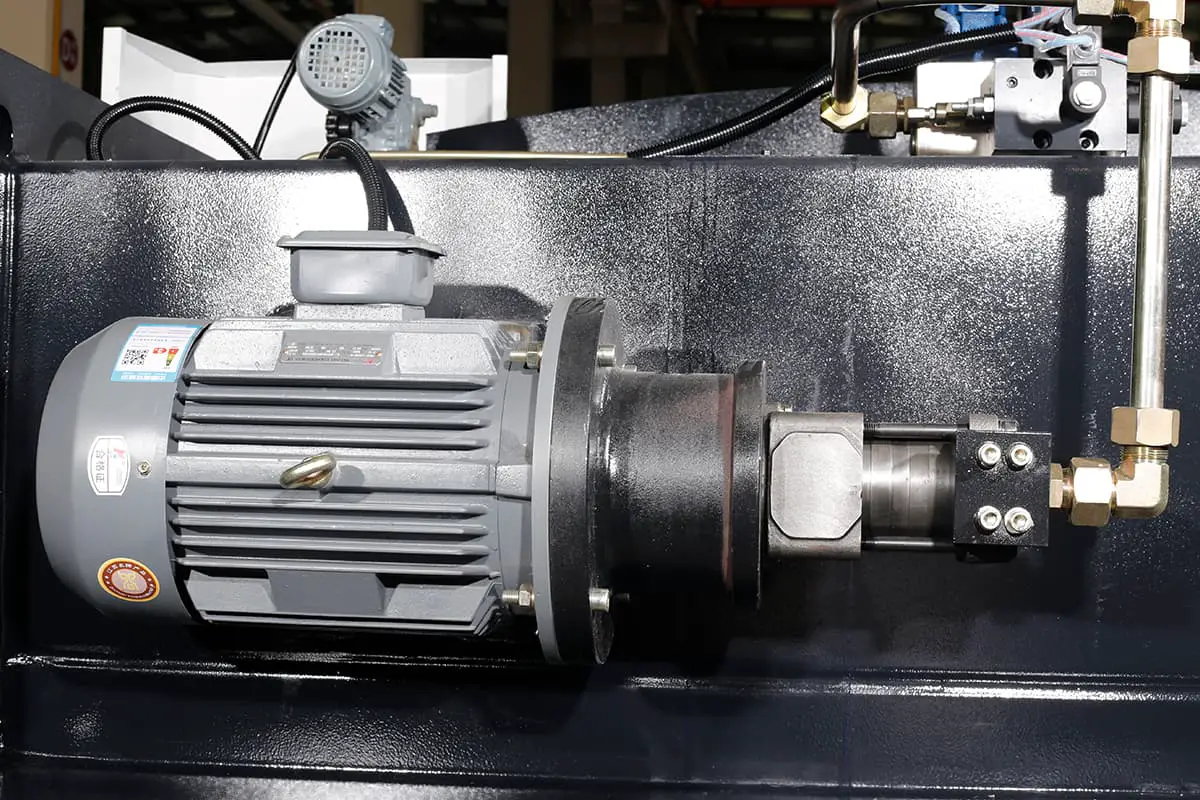
(2) Downward movement
The rapid downward movement of the press brake is generated by the bending beam, the self-weight of the accessories and the oil pressure. During this process, the hydraulic cylinder has no rod cavity through the filling valve, and any back pressure produced by the rod cavity causes the oil liquid to return quickly.
The rapid forward motion begins at top dead center, and after a brief period of deceleration, the ram decelerates a specific distance from the bending plate. The downward speed of the ram is adjusted by valve No. 18, and the rapid fall is initiated by the operation of electromagnets No. 9 YV1, No. 24 YV6, No. 13 YV4, and No. 17 YV5.
Oil from the lower chamber of cylinder number 20 enters the tank through valves 19, 18 and 17, while oil from the upper chamber of the same cylinder is injected through valve 21. When the ram reaches the limit switch, electromagnets number 9 YV1, No. 8 YV2, No. 11 YV3, No. 13 YV4, and No. 24 YV6 begin to operate, causing the ram to transition to its working speed.
If the ram is out of sync, valve number 15 will automatically correct it. The sliding block's falling position is restricted by the mechanical block inside the cylinder.
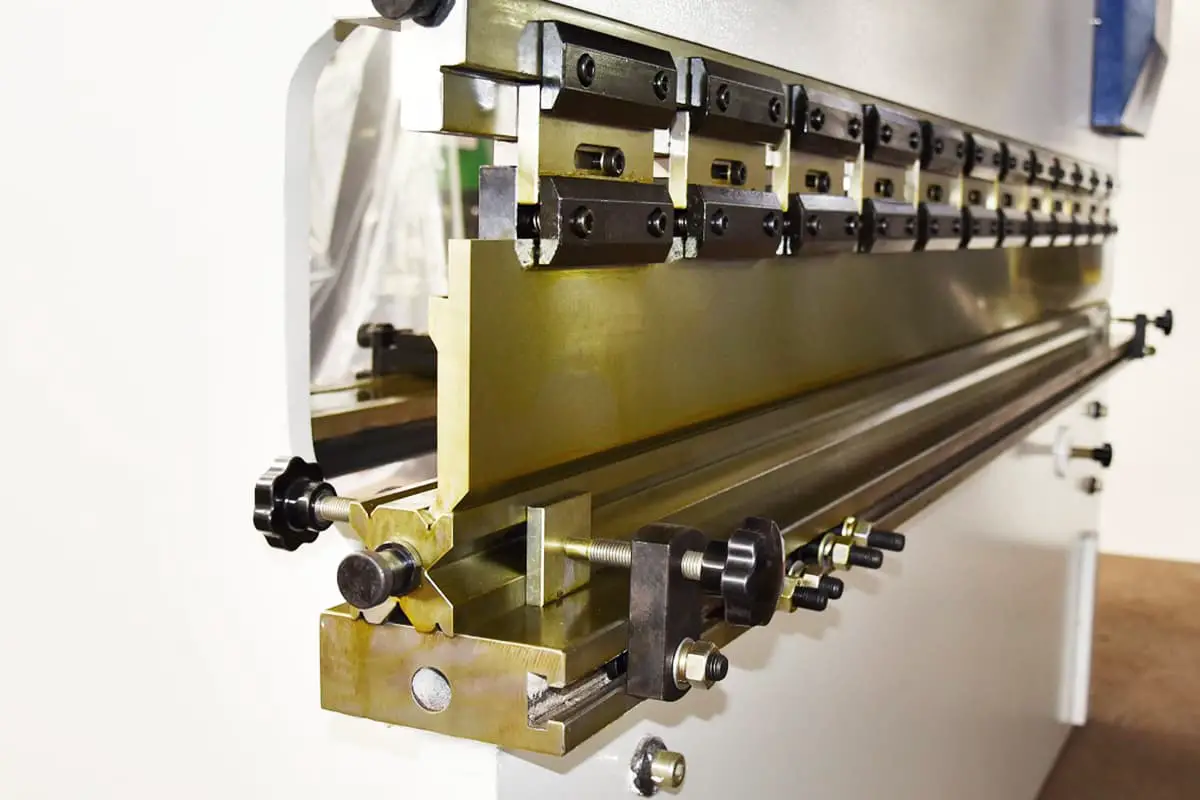
(3) Flexion
The bending phase begins with increasing pressure in the barless cavity.
The bending speed is limited by the amount of oil supplied by the oil pump. On the other hand, it can be adjusted by the proportional valve steering valve.
At the same time, the steering valve also controls the synchronous operation of the bending beam and the positioning of the bottom dead center.
The bending force is limited by the proportional relief valve to limit the pump pressure.
The corresponding speed, timing, positioning and pressure values are all from the CNC.
The pedal switch or button controls the working time of the electromagnet which includes No.9 YV 1 No.8 YV 2 No.11 YV 3 No.13 YV 4 and No.24 YV 6 which realizes the traveling distance when the sliding block falls.
The slide's falling speed is adjusted by valve 16.
The ram is controlled by No.11 YV 3 and No.24 YV 6 .
The working time duration of the same electromagnet can realize the moving distance of the ram.
(4) Pressure relief
Stress relieving of the barless cavity begins when it reaches the bottom of dead center, or after a brief holding time, allowing the material sufficient time to form and increasing the dimensional accuracy of the parts. Pressure retention and pressure relief are realized by the proportional directional valve, which is controlled by the numerical control device.
In an effort to improve processing efficiency, the time required for pressure relief should be minimized. However, to avoid the impact of flushing on the entire system, it is necessary to extend the flushing time as much as possible. In other words, the pressure relief curve must be as smooth as possible, avoiding sharp drops.
The optimization of the entire process is achieved through the use of the proportional directional valve.
(5) Master cylinder return
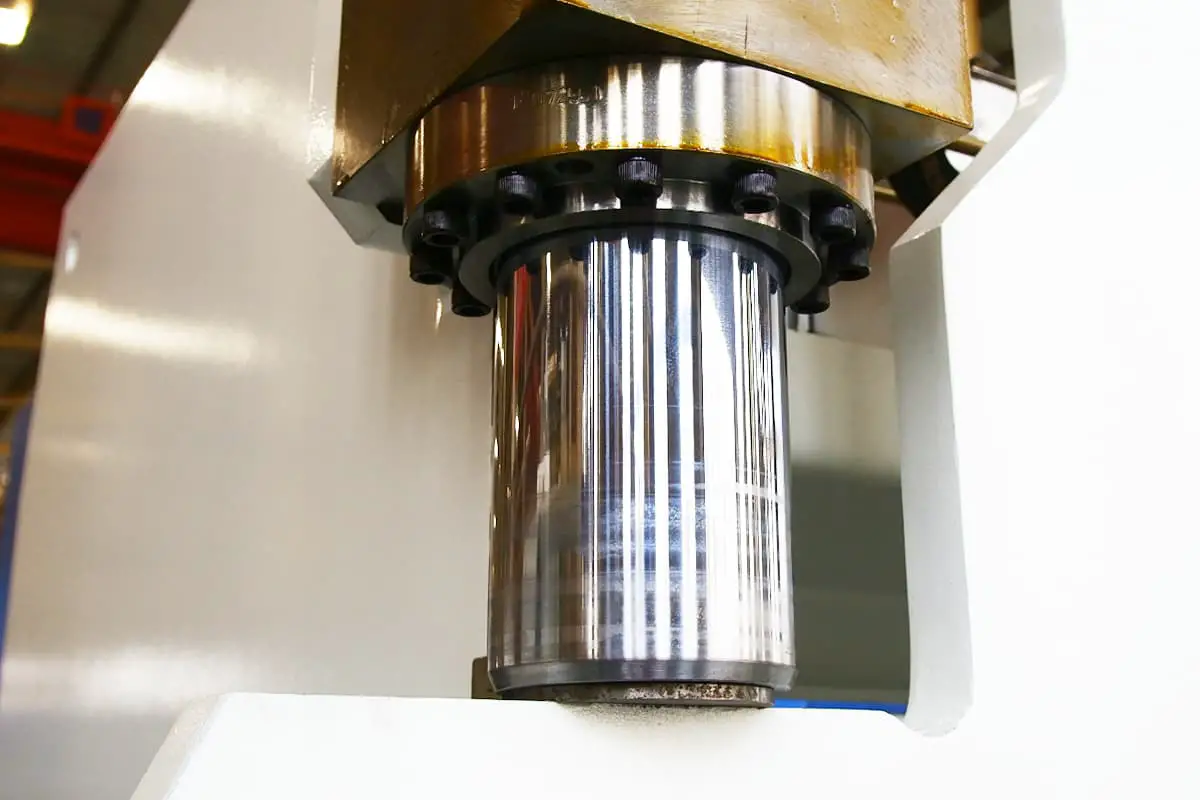
The pump flow and hydraulic cylinder have a pressure area in the bar cavity, which determines the maximum return speed, which is usually close to the fastest speed. The return process requires synchronous operation, starting with reducing the bar cavity pressure and ending at top dead center.
When returning, it is necessary to reset the pressure of electromagnet nº 8 YV2 for 2 seconds, then electromagnets nº 11 YV3 and nº 24 YV6 start working and the sliding block begins to return at constant speed.
(6) Press brake adjustment
Valves No. 6 and No. 11, the high-pressure overflow valve and the electromagnetic overflow valve respectively, are mainly responsible for maintaining the rated power of the press brake. Meanwhile, valve No. 14 regulates the return force of the machine to prevent damage caused by overload.
The pressure within the hydraulic system can be monitored using pressure gauge No. 7. The nitrogen pressure in accumulator No. 10 mainly controls the pressure required for the operation of valves No. 19 and No. 21.
Press brake hydraulic transmission principle
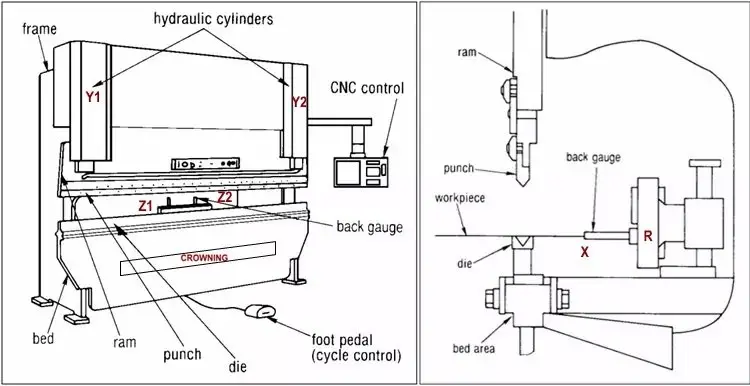
Each stroke of the press brake is divided into three working conditions, namely:
- Moving fast
- Working
- Turn back
There are three specific points that determine the initial and final positions of each working condition, namely:
- Top dead center
- Speed change point
- Bottom dead center
Correspondingly, the ram moves at three speeds, namely:
- No loading speed
- Working speed
- Return speed
In a press brake machine cycle, from top dead center to the speed change point, the ram moves downward rapidly at no-load speed.
From the speed change point to bottom dead center, the ram moves downward at the working speed and the bending of the part is completed during this phase.
From bottom dead center to top dead center, the ram moves upward at return speed, completing one machine cycle.
The three speeds and the positions of the three specific points can be adjusted through the numerical control system.
For an electro-hydraulic synchronous CNC press brake, there is a specific point known as the clamping point, which corresponds to the upper surface of the sheet metal in the lower die. The part will be bent from this point, which is automatically calculated by the numerical control system.
The hydraulic transmission medium used is hydraulic oil and its quality directly affects the performance and useful life of the machine. In particular, the electro-hydraulic synchronous CNC press brake is equipped with a proportional servo valve, making the requirements for hydraulic oil more stringent compared with other bending machines.
Users are advised to filter hydraulic oil at least once a year.
1. Synchronous principle of synchronous torsion shaft press brake machine
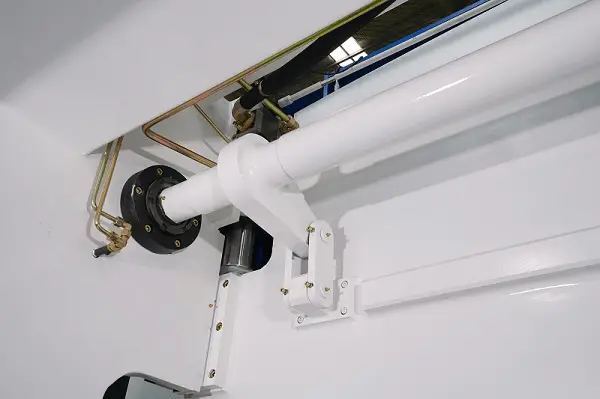
Torsion shaft forced synchronization control technology is used in the operation of the ram of a press brake.
The synchronous shaft is located on the left and right panels of the frame body and is connected to the ram via a connecting rod.
During operation, if one end of the ram moves faster, the ram drives the rocking arm of the synchronous shaft to rotate it through the connecting rod. The rigidity of the synchronous shaft generates a reverse force that reduces the speed of the ram, ensuring that the rams (Y1, Y2) work synchronously and maintain a state parallel to the work table.
Precise positioning of the ram is achieved through the Rigid Positioning Control Technology of the integrated mechanical block. There are mechanical stops on the left and right oil cylinders, which stop the downward movement of the piston rod after contacting the mechanical stop locating surface, controlling the end position of the oil cylinder stroke.
The mechanical stops of the left and right oil cylinders are synchronously adjusted through the connecting rod to control the relative parallel state of the rams (Y1, Y2) to the worktable.
2. Synchronous principle of CNC synchronous electro-hydraulic press brake machine
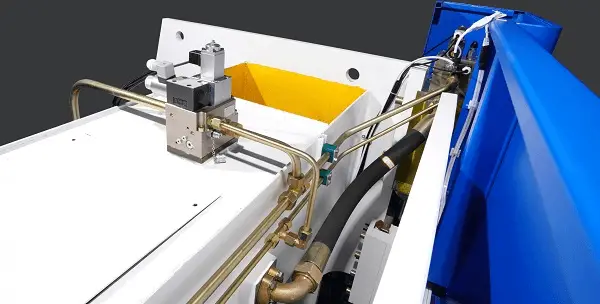
The press brake uses two oil cylinders to move the ram up and down, completing the bending process. Synchronization of the two cylinders and precise positioning of the bottom dead center are critical.
The Servo CNC Electro-Hydraulic Press Brake precisely controls the synchronization of the two oil cylinders and the precise positioning of the bottom dead center through the CNC system. This results in smooth ram movement and precise positioning at bottom dead center.
The position of the ram is detected in real time by grid rulers installed on both sides of the machine and fed back to the CNC system. The numerical control system compares the feedback data of the two grid rulers and adjusts the proportional servo valve in the synchronous valve groups, controlling the size of the valve opening and the oil inlet of the oil cylinder to maintain the operation of the ram within an acceptable error range. This ensures that the plungers (Y1, Y2) run synchronously and maintain a state parallel to the worktable.
The numerical control system also compares feedback data from the grid ruler with the system-defined bottom dead center to confirm that bottom dead center has been achieved.
The press brake uses full closed-loop electro-hydraulic servo control technology for its synchronous control, with the ram position signal fed back to the numerical control system by the grid rulers on both sides. The numerical control system then controls the opening size of the synchronous valve and adjusts the oil inlet of the oil cylinder, ensuring that the rams (Y1, Y2) work synchronously and maintain a state parallel to the work table.
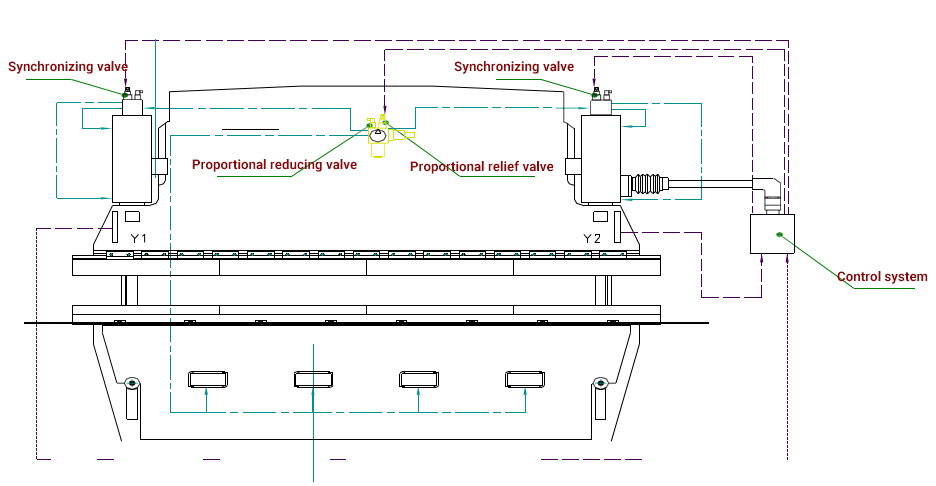
Synchronous schematic diagram of electro-hydraulic synchronous CNC hydraulic press brake machine
If there is any positioning error on both sides of the ram, the numerical control system will send correction instructions to the two synchronous valves to maintain the parallel state of the ram with the work table.
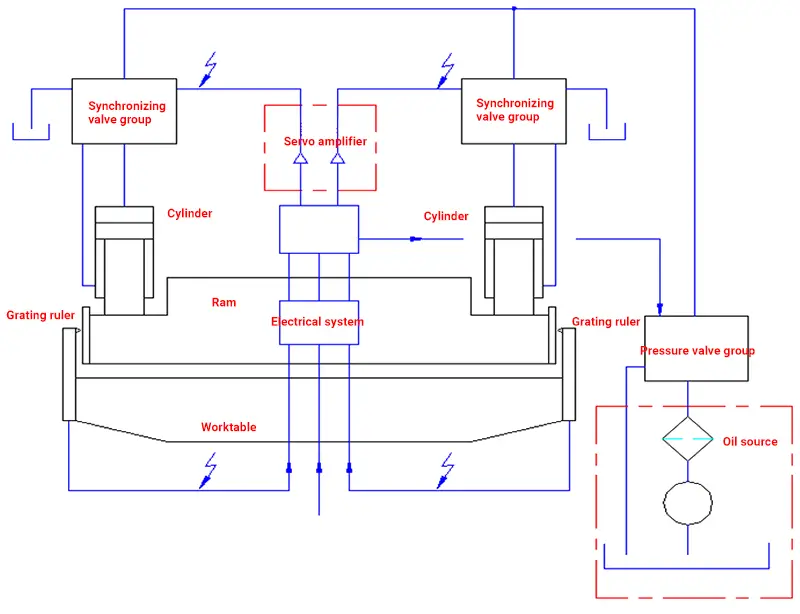
The diagram describes the components of the press brake synchronous system, which mainly consists of hydraulic oil control and electrical signal transmission.
The pressurized oil is controlled by the two groups of synchronous valves and enters the two oil cylinders to drive the synchronous movement of the ram. The position of the ram's movement is detected in real time by grid rulers on both sides and sent back to the CNC system.
The CNC system analyzes and calculates the data, controlling the two groups of synchronous valves through the servo amplifier. The proportional servo valve spool position feedback signal is also received and analyzed, forming a closed-loop dynamic control.
Throughout the movement of the ram, the numerical control system sets the parameters according to the program, using the grid ruler and the spool position feedback signal of the proportional servo valve to dynamically control the synchronous valve group and achieve synchronized operation and precise positioning of the lower dead center.
Therefore, the synchronous control system of electro-hydraulic synchronous CNC press brake mainly consists of CNC system, grid ruler and proportional valve.
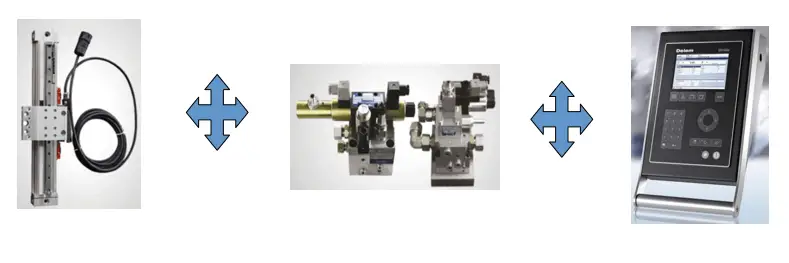
As shown above, the bending principle of the electro-hydraulic synchronous bending machine is similar to that of a normal bending machine, which controls the bending angle by adjusting the pressing depth of the sheet in the lower mouth of the die through the upper punch, or by pressing the workpiece at the same angle as the die.
The only difference is the ram control mode, which is controlled by the numerical control system through the electro-hydraulic proportional valve and the grid ruler feedback. This forms a complete closed-loop digital control mode for bending depth.
The difference between two types of bending machine synchronous mode
The standard press brake machine relies on the torque tube to ensure that the ram moves in synchronization, while the synchronization of the electro-hydraulic press brake machine is achieved through balance in the hydraulic oil circuit.
It is important to note that the torsion shaft press brake operates using open-loop control, while the electro-hydraulic press brake uses closed-loop control.
Electro-hydraulic synchronous press brake machine has the following obvious advantages
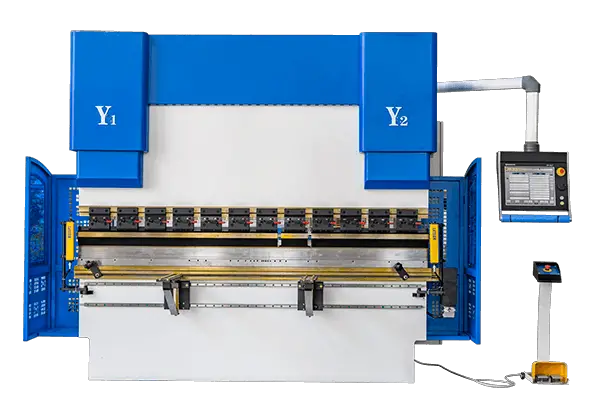
The fully closed loop control system in the electro-hydraulic press brake allows continuous monitoring and control of the cylinder stroke. As soon as the cylinder begins to tilt, the system immediately issues commands based on readings from scales located on both sides of the cylinder, which then prompt the proportional valves to make adjustments to keep the cylinders in sync.
In the electro-hydraulic press brake, it is possible to have one cylinder working at full load while the other operates at zero pressure in a pressurized state without load.
Furthermore, the electro-hydraulic synchronization system allows the ram to be tilted at various angles, making it possible to bend parts at different angles, which is not possible with traditional bending machines.
The pressure in the electro-hydraulic synchronous system is automatically regulated in each operating condition by the proportional pressure valve based on the system parameters.
This system can also make a smooth transition from fast to slow speed, reduce hydraulic impact and improve system stability.
Precise control of the cylinder position in the electro-hydraulic press brake makes it possible to bend the same die at different angles, making it a highly flexible machine tool.
Furthermore, automatic control of the entire process reduces errors caused by human factors, and each working condition can be adjusted and corrected through CNC parameters.
In conclusion, the electro-hydraulic press brake improves production efficiency, increases part precision and transforms the machine into a tool that works for the operator.