I. What type of steel is stainless steel?
Stainless steel” is a type of steel that contains less than 2% carbon and more than 2% iron and is strengthened by the addition of chromium, nickel, manganese, silicon, titanium, molybdenum and other alloying elements. This results in steel that is corrosion resistant, meaning it will not rust.
“Steel” and “Iron” are different terms and their properties and characteristics vary. The terms “304”, “304L”, “316” and “316L” are different types of stainless steel, each with unique properties and characteristics. It is important to understand these differences to determine the most appropriate grade for a specific application.
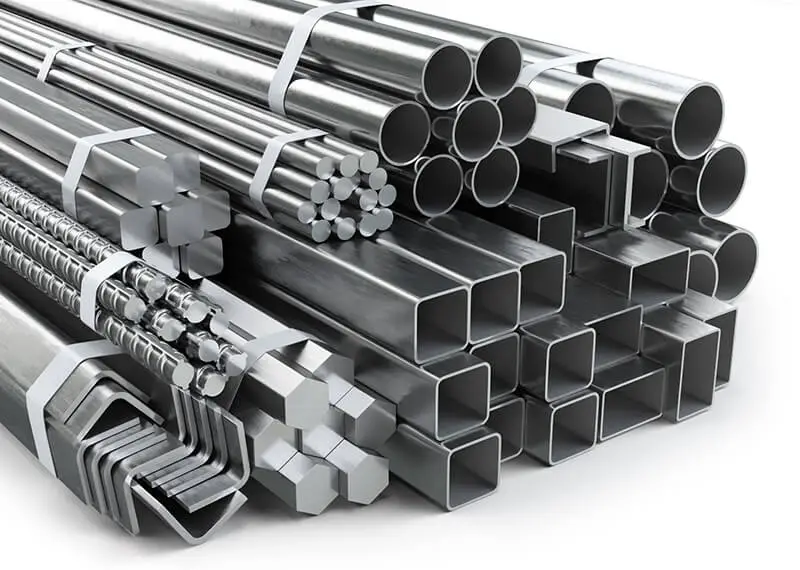
Steel:
A type of material that uses iron as the main element with carbon content (less than 2%) and other elements.
–GB/T 13304-91 Steel Classification
Iron:
A metallic element with atomic number 26.
Iron materials have strong ferromagnetic properties, excellent plasticity and thermal conductivity.
Stainless steel:
A type of steel with resistance to air, steam, water and other weakly corrosive media or properties of stainless steel.
Commonly used steel grades are 304, 304L, 316 and 316L, which are 300 series austenite steels.
II. Why does stainless steel have different qualities?
In the production of stainless steel, different alloys are added, leading to differences in its characteristics. To differentiate them, they are given different steel numbers. The following alloying element table is a common reference for different steel numbers in decorative stainless steel.
Chemical composition (mass fraction, %)
Steel Grade | W | Yes | Mn | P | s | Cr | No |
304 | ≤0.08 | ≤1.00 | ≤2.00 | ≤0.045 | ≤0.03 | 18-20 | 8-10 |
301 | ≤0.15 | ≤1.00 | ≤2.00 | ≤0.045 | ≤0.03 | 16-18 | 6-8 |
202 | ≤0.15 | ≤1.00 | 7.5-10 | ≤0.05 | ≤0.03 | 17-19 | 4-6 |
201 | ≤0.15 | ≤1.00 | 5.5-7.5 | ≤0.05 | ≤0.03 | 16-18 | 3.5-5.5 |
1304 stainless steel
Performance introduction
304 stainless steel is a widely used and common type of steel that has good corrosion resistance, heat resistance, low temperature resistance and mechanical properties. It is ideal for stamping and bending processes, as it does not undergo hardening heat treatment and remains non-magnetic. It can be used at temperatures between -196°C and 800°C.
Applicable range
304 stainless steel is commonly used in household appliances such as Class I and II tableware, cabinets, indoor plumbing, water heaters, boilers, and bathtubs. It is also used in automotive parts such as windshield wipers and mufflers, and in medical devices, building materials, the chemical industry, the food industry, agriculture, and ship components.
2. 304L stainless steel – (L is low carbon)
Performance introduction
As a low carbon steel, 304L has similar corrosion resistance to 304 in general. However, after welding or stress relieving, it exhibits excellent resistance to grain boundary corrosion. It can also maintain good corrosion resistance without heat treatment in a temperature range of 196°C to 800°C.
Applicable range
304L is commonly used in outdoor equipment in the chemical, coal and petroleum industries that require high resistance to grain boundary corrosion, as well as in heat-resistant parts of construction materials and components that are difficult to heat treat.
3. 316 stainless steel
Performance introduction
Due to the addition of molybdenum, 316 stainless steel has excellent corrosion resistance, atmospheric corrosion resistance and high temperature resistance, making it suitable for use in harsh conditions. Its work hardening properties are also excellent (non-magnetic).
Applicable range
Marine equipment, chemicals, dyes, paper, oxalic acid, fertilizers and other production equipment; camera, food industry, installations in the coastal area, ropes, CD rods, screws, nuts.
4. 316L stainless steel – (00Cr17Ni14Mo2)
Performance introduction
As it is a low-carbon 316 stainless steel series, it has the same characteristics as 316, but has excellent resistance to grain boundary corrosion.
Applicable range
Products with special requirements for resistance to grain boundary corrosion.
Enriched with Mo (2-3%), it presents exceptional corrosion and corrosion resistance and excellent creep resistance at high temperatures.
Features and practical applications:
Difference | SUS316(L) |
Characteristics | –Excellent resistance to crystalline corrosion |
Use | –Piping for boilers, marine structures |
Chemical Composition: (Unit:% by weight)
Specification | W | Yes | Mn | P | s | Cr | No | Other |
SUS316 | ≤0.08 | ≤1.00 | ≤2.00 | ≤0.045 | ≤0.030 | 16.0~18.0 | 10.0~14.0 | Mo:2~3 |
SUS316L | ≤0.03 | ≤1.00 | ≤2.00 | ≤0.045 | ≤0.030 | 16.0~18.0 | 12.0~15.0 | Mo:2~3 |
Mechanical properties:
Specification | YS(Mpa) | TS(Mpa) | EL(%) | Hv |
SUS316 | ≥205 | ≥520 | ≥40 | ≤200 |
SUS316L | ≥175 | ≥480 | ≥40 | ≤200 |
III. Performance comparison
1. Hemic composition
Due to the presence of molybdenum, 316 and 316L stainless steels have excellent corrosion resistance and high temperature resistance. With superior performance compared to 310 and 304 stainless steels, 316 stainless steel is widely used in harsh conditions including high temperatures and sulfuric acid concentrations between 15% and 85%.
Additionally, its resistance to chloride attack makes it a popular choice for marine environments. With a maximum carbon content of 0.03, 316L stainless steel is ideal for applications that do not require post-weld annealing and maximum corrosion resistance.
Chemical composition of 316L stainless steel
Grade: 00Cr17Ni14Mo2
Material name | Chemical Composition (Mass Fraction%) | |||||||
W | Yes | Mn | P | s | No | Cr | Mo | |
316L | ≤0.03 | ≤1.00 | ≤2.00 | ≤0.035 | ≤0.03 | 12.0-15.0 | 16.0-18.0 | 2.0-3.0 |
Chemical composition of 304 stainless steel
Grade: 0Cr18Ni9
Material name | Chemical Composition (Mass Fraction%) | |||||||
W | Yes | Mn | P | s | No | Cr | N | |
≤ | ≤ | |||||||
SUS304 | 0.07 | 0.75 | 2:00 | 0.035 | 0.030 | 8.0-11.0 | 6pm-8pm | 0.10 |
2. Corrosion resistance
1. Corrosion resistance of 316L
316L stainless steel is a type that contains molybdenum. Its corrosion resistance surpasses that of 304 stainless steel, demonstrating robust resistance during pulp and paper production. Additionally, 316 stainless steel is resistant to corrosive marine and industrial atmospheres.
In terms of heat resistance, 316L stainless steel has good oxidation resistance in intermittent use below 1600 degrees and continuous use below 1700 degrees.
For the range of 800-1575 degrees, it is advisable not to use 316L stainless steel continuously; however, this steel exhibits remarkable heat resistance when operated continuously outside this temperature range.
The resistance of 316L stainless steel to carbide precipitation is higher than that of 316 stainless steel, suitable for use in the mentioned temperature range.
As a low-carbon version of 316 steel, 316L not only maintains the same characteristics as 316 steel, but also offers greater resistance to intergranular corrosion.
This makes 316L particularly suitable for applications within the 316 steel range that require special resistance to intergranular corrosion.
2. Corrosion resistance of 304
304 stainless steel has excellent corrosion resistance and good resistance to intergranular corrosion.
In the case of oxidizing acids, experiments have shown that 304 stainless steel demonstrates strong corrosion resistance in nitric acid solutions with a concentration ≤65% below the boiling temperature.
It also exhibits good corrosion resistance in alkaline solutions and most organic and inorganic acids.
A high-alloy steel capable of resisting corrosion in air or chemically corrosive media, stainless steel has an attractive surface and good corrosion resistance.
Without the need for surface treatments such as coating, it takes advantage of the inherent surface properties of stainless steel. This versatile type of steel, commonly called stainless steel, is used in many applications.
The mechanism for preventing rust in stainless steel is that the alloy elements form a dense oxide film, isolating contact with oxygen and preventing further oxidation. However, stainless steel is not “stainless” in the absolute sense.
The occurrence of rust in 304 material may be due to several reasons:
(1) Presence of chloride ions in the environment.
Chloride ions are widely present, for example, in table salt, sweat, sea water, sea breeze, soil, etc. Stainless steel corrodes quickly in an environment with chloride ions, sometimes even faster than regular low-carbon steel.
Therefore, the environment in which stainless steel is used needs to be considered, with regular cleaning required to remove dust and maintain cleanliness and dryness.
(2) Lack of solution treatment.
If the alloying elements are not dissolved in the matrix, the base structure will have a low alloy content, resulting in poor corrosion resistance.
(3) This type of material, which lacks titanium and niobium, has an inherent tendency to intergranular corrosion.
The addition of titanium and niobium together with stabilization treatment can reduce intergranular corrosion.
In pulp and paper production, 316 stainless steel has better corrosion resistance compared to 304 stainless steel. It is also resistant to aggressive marine and industrial atmospheres.
Generally, there is little difference in terms of chemical resistance between 304 and 316 stainless steel, although there are differences in certain specific media.
304 stainless steel, being the first stainless steel developed, is more susceptible to pitting corrosion (PC) under certain conditions.
The addition of 2-3% molybdenum reduces this sensitivity, leading to the creation of 316. Furthermore, the extra molybdenum also decreases the corrosion of specific hot organic acids.
316 stainless steel has become the industry standard material for the food and beverage industries; however, due to the worldwide shortage of molybdenum and the higher nickel content in 316, it is more expensive than 304 stainless steel.
Pitting corrosion occurs mainly due to the deposition of corrosion on the surface of stainless steel resulting from the inability to form a protective layer of chromium oxide due to lack of oxygen.
In most types of aqueous media (distilled water, drinking water, river water, boiler water, sea water, etc.), the corrosion resistance of 304 and 316 stainless steel is almost the same, unless the content of chloride ions in the medium is very high, in which case 316 stainless steel is more suitable.
In most cases, the corrosion resistance performance of 304 and 316 stainless steels is not significantly different, but in some cases there may be a large difference, which requires a specific analysis of each case.
Valve users must have a clear understanding of their requirements as they will choose the material for their vessel and pipe based on the medium. Recommending materials to users is not recommended.
See too:
- 304 vs 316 stainless steel: what's the difference?
3. H eating resistance
316 stainless steel has good oxidation resistance when used intermittently below 1600°C and continuously below 1700°C.
It is best not to use 316 stainless steel continuously within the temperature range of 800-1575°C, but it has good heat resistance when used continuously outside this range.
316L stainless steel has better resistance to carbide precipitation than 316 stainless steel and can be used in higher temperature ranges.
4. H eating treatment
316 stainless steel needs to be annealed in the temperature range of 1850-2050 ó C, so it anneals and cools quickly because it cannot be hardened by overheating.
5. Weldability
316 stainless steel has good welding properties and can be welded using all standard welding methods. Depending on the application, a 316Cb, 316L or 309Cb stainless steel filler rod or electrode can be used for welding.
For optimal corrosion resistance, post-weld annealing is necessary for the welded cross-section of 316 stainless steel. However, post-weld annealing is not necessary if 316L stainless steel is used.
1. Weldability of 316L
316L stainless steel is an ultra-low carbon pure austenitic stainless steel with good weldability and resistance to intergranular corrosion.
However, due to the low thermal conductivity and high coefficient of linear expansion of stainless steel, significant tensile stresses can form in the welded joint during cooling.
This, combined with high heat input and slow cooling rates, can lead to heat cracking, corrosion cracking and warping.
316L stainless steel can be welded using all standard methods. Depending on the application, 316Cb, 316L or 309Cb stainless steel filler rods or electrodes can be used for welding.
Among the commonly used welding methods, MIG and TIG welding have lower heat inputs.
The argon gas flow not only protects the metal from high temperature, but also has a cooling effect, increasing the crack resistance of the weld and reducing the deformation of the weld.
For 316L stainless steel, post-welding annealing treatment is not necessary (austenitic stainless steel generally does not undergo stress relief annealing after welding). The main reasons are:
1) Austenitic stainless steel has excellent plasticity and toughness, so there is no need to restore its properties through post-welding stress relief annealing.
2) The temperature range of 450~850°C is the sensitization temperature for austenitic stainless steel.
Prolonged heating in this range may degrade its corrosion resistance. If the solder contains ferrite, this can also lead to 475°C brittleness and sigma phase brittleness.
The annealing treatment for stress relief after welding is within this temperature range (except for solid solution and stabilization treatments).
In special cases, annealing treatment is necessary to relieve post-welding stresses:
1) To stabilize the geometry of equipment parts, it is necessary to eliminate welding residual stresses.
2) If the equipment operates in an environment prone to stress corrosion cracking, it is necessary to eliminate residual tensile stress.
2. Weldability of 304 stainless steel
Austenitic stainless steel, represented by 18%Cr-8%Ni steel or 304 stainless steel, generally does not require preheating or post-weld heat treatment. It has good welding performance.
However, high-alloy stainless steel with high nickel and molybdenum content tends to crack during welding.
Other problems include embrittlement of the σ phase (Fe-Cr intermetallic compound), ferrite-induced low-temperature brittleness, reduced corrosion resistance, and stress corrosion cracking.
After welding, the joint normally demonstrates good mechanical properties, but chromium carbides at the grain boundaries in the heat-affected zone can lead to a chromium-poor layer, which is prone to intergranular corrosion.
To avoid these problems, use grades with low carbon content (C≤0.03%) or grades with added titanium or niobium.
To prevent high-temperature cracking of welded metal, it is commonly considered effective to control δ ferrite in austenite, with a general recommendation to maintain at least 5% δ ferrite at room temperature.
For steel used primarily for corrosion resistance, opt for stabilized, low-carbon grades and apply appropriate post-weld heat treatment.
For steel used primarily for structural strength, post-welding heat treatment should be avoided to prevent deformation and embrittlement caused by precipitated carbides and the occurrence of the δ phase.
6. Mechanical properties
Type | UTS N/mm |
Harvest N/mm |
Compliment % |
Toughness HRB |
Comparable DIN number | |
---|---|---|---|---|---|---|
wrought | cast | |||||
304 | 600 | 210 | 60 | 80 | 1.4301 | 1.4308 |
304L | 530 | 200 | 50 | 70 | 1.4306 | 1.4552 |
316 | 560 | 210 | 60 | 78 | 1.4401 | 1.4408 |
316L | 530 | 200 | 50 | 75 | 1.4406 | 1.4581 |
In all types of steels, austenite has the lowest yield strength. Therefore, in terms of mechanical properties, austenite is not the most suitable material for use in valve stems.
This is because, to guarantee a specific resistance, the rod diameter must be increased. Yield strength cannot be increased through heat treatment, but can be increased through cold forming.
Comparison of Mechanical Properties Between 316L and 304 Stainless Steels
Note | Tensile strength (Mpa) |
Yield strength (Mpa) |
Elongation Rate (%) |
≥ | |||
0Cr18Ni9(304) | 520 | 205 | 35 |
00Cr17Ni14Mo2(316L) | 480 | 175 | 35 |
1. The main chemical difference between 316L and 304 is that 316L contains molybdenum (Mo).
The addition of molybdenum to austenitic stainless steel increases its heat and creep resistance, improving its resistance to pitting and intergranular corrosion.
Molybdenum can passivate the surface of steel in reducing and highly oxidative salt solutions, increasing the corrosion resistance of steel and preventing corrosion in chloride solutions.
The inclusion of molybdenum improves resistance to reducing acids and corrosion, while reducing carbon content increases resistance to intergranular corrosion and improves weldability. The addition of molybdenum better prevents corrosion.
304 is classified as low carbon stainless steel, while 316L is ultra low carbon stainless steel.
The lower carbon content can reduce the occurrence of intergranular corrosion. However, both 304 and 316L are sensitive to chloride ions.
304's resistance to chloride ions is significantly weaker than that of 316L, so 316L is generally chosen for high chloride environments.
2. The difference between 316L and 304 is substantial, particularly with regard to intergranular corrosion.
304 is classified as low carbon stainless steel, while 316L is ultra low carbon stainless steel. The higher the carbon content, the lower the steel's resistance to intergranular corrosion. Therefore, 316L surpasses 304 in resistance to intergranular corrosion.
3. 316L stainless steel has a maximum carbon content of 0.03, making it suitable for applications requiring post-weld annealing and maximum corrosion resistance.
Generally speaking, 316L has better corrosion resistance and intergranular corrosion resistance than 304. In terms of weldability, due to its low carbon content and other factors combined, 316L surpasses 304.
Regarding mechanical properties, the resistance of 304 is higher than that of 316L. In terms of machining capacity, the 316L has superior cutting capacity.
7. Magnetic properties
Due to the widespread use of austenite, a false perception has been created that all stainless steels are non-magnetic.
It is generally understood that austenite is non-magnetic and hardened forged steels are indeed so.
However, 304 that has undergone cold forming can be somewhat magnetic. On the other hand, 100% austenite cast steel is non-magnetic.
4. Low carbon stainless steel
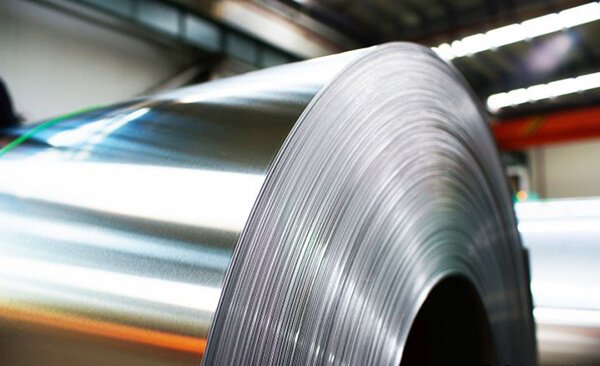
Austenite's corrosion resistance comes from the protective layer of chromium oxide that forms on the surface of the metal.
If the material is heated to high temperatures of 450°C to 900°C, the structure of the material changes and chromium carbide is formed along the edge of the crystal, preventing the formation of a protective layer of chromium oxide on the edge of the crystal. crystal. and resulting in a reduction in corrosion resistance.
This corrosion is called 'intergranular corrosion'.
To combat this corrosion, 304L and 316L stainless steels with lower carbon content have been developed, meaning there is no chromium carbide or intergranular corrosion.
It should be noted that greater sensitivity to intergranular corrosion does not mean that non-low carbon materials are more susceptible to corrosion, and this sensitivity is also greater in environments with high chlorine content.
Note that this phenomenon is due to high temperatures (450°C – 900°C) often caused by welding.
For a conventional soft-seated butterfly valve, there is no need to use low-carbon stainless steel as we do not weld the valve plate, although most specifications require 304L or 316L stainless steel.
V. Why does stainless steel rust?
Why does stainless steel still rust?
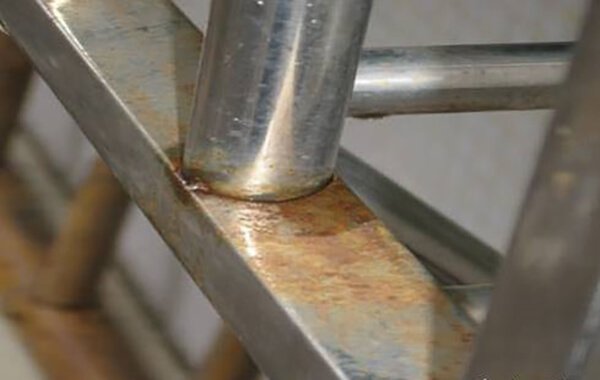
When brown rust spots appear on the surface of a stainless steel pipe, it can be surprising as many people have the misconception that stainless steel does not rust.
However, stainless steel can corrode under certain conditions as it has the ability to resist atmospheric oxidation, but it also has the ability to corrode in media containing acids, alkalis and salt.
The corrosion resistance of stainless steel varies depending on its chemical composition, protection status, conditions of use and type of environmental environment.
For example, 304 steel pipes have excellent corrosion resistance in a dry, clean atmosphere, but can rust quickly in salty coastal areas containing large amounts of salt.
On the other hand, 316 steel pipes perform well in these conditions. It is important to note that not all stainless steel is resistant to corrosion and rust in all environments.