Whether you are a press brake manufacturer, end user, dealer or service provider, the following press brake terminologies will help you understand professional expressions.
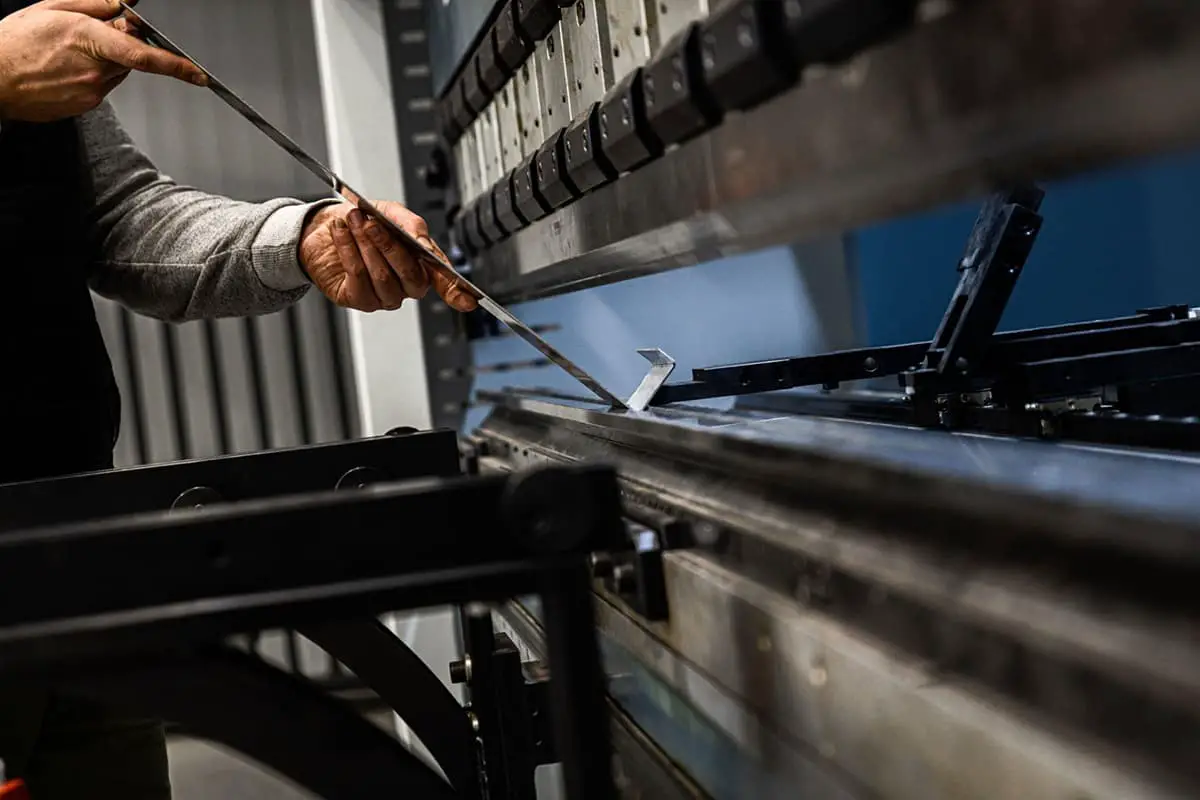
Back gauge
An adjustable stop, automated on modern CNC machines, that acts as a stop for the part by centering the bend line over the V-shaped opening of the die.
Origin of the rear meter
A predefined position for the back gauge, set from the center of the V-opening. The origin of the back gauge is typically 4” from the center of the V. This origin will determine all positioning of the back gauge, so it is crucial that it runs parallel The matrix.
Base
The stabilizing and supporting base is a critical component of any brake press. This feature is usually at ground level, although for some heavy-duty brakes and stamping machines, it is located below ground and isolated from the floor to minimize the transfer of vibration from the machine to the floor.
Bottom dead center
This is the position of the press brake when it is fully closed in the die. This position will be different for each set of dies.
Capacity / Tonnage
This will be the maximum force that the press brake can exert on the workpiece.
Clutch
Mechanism that activates the flywheel using a mechanical brake, transferring its energy through a gear coupled to the crankshaft, reducing the tonnage of the part.
CNC
An abbreviation for Computer Numerical Control, this is a term applied to computer-controlled press brakes.
Crankshaft
The component of a mechanical press brake that transfers energy from the flywheel to the ram.
Daylight through
Term used to describe the maximum open space that a brake can open given a specific die set.
Down action brake
A press brake where the upper beam moves the punch into the die.
Steering wheel
A large heavy wheel that is turned to store the energy needed to close and reopen a mechanical press brake.
Pedal
The part of a mechanical press brake that is used by the operator to engage the clutch.
Gibb adjustment
Fine-tune motion control for which beam will move.
High/low speed shifting
The point during the bending operation where the brake transitions from a high-speed motion to approach the workpiece to a low-speed motion to bend the workpiece is called the “slow bend point.” Bending is done more slowly to avoid dangerous movement of the workpiece.
Housing Support
A structural component of the upper beam that holds together the two drive cylinders of a press brake.
Hydraulic brakes
A press brake that is driven by transferring high-pressure fluid into a cylinder is called a hydraulic press brake. Hydraulic presses are known for their high precision and excellent control, and are the most commonly used type of computer-controlled precision brakes.
Hydromechanical Brake
A press brake that uses a flywheel to push fluid into a hydraulic cylinder, offering uniform tonnage throughout the stroke, an advantage over typical mechanical brakes.
Length
The total working length of the brake press extends from left to right.
Lower beam
The bottom part of a press brake that holds the die or rail in position.
Mechanical Brake
A press brake that relies on a flywheel and clutch mechanism to mechanically transfer energy to cycle the ram is known as a mechanical press brake. It is found on older machines and suffers from uneven tonnage application and poor vertical control.
Mechanical Stop
A physical stop that prevents excessive travel of older mechanical brakes and improves repeatability.
Pinch point
The moment the punch touches and begins to apply tonnage to the part.
At this point, the back gauge can retract to allow the workpiece to form upward freely.
Pit/pitless machine
If the machine requires a hole in the floor and a subsequent base to stabilize and secure the lower beam it is called a “Pit Machine”. Pit machines are typically much larger than “No Pit” machines.
To knock
The upper and lower rams are the driving or resistance components of the press brake. They are typically machined from large, strong steel plates and can be supplemented with internal hydraulic cylinders to resist deflection.
Repeatability
The precision with which the press brake is able to return to a specific position.
Stroke length
The maximum brake press opening size, i.e. the distance between the top of the lower beam and the bottom of the upper beam when the brake is fully open and no tools are installed.
Shake your fingers up
Special adaptation to the back gauge that allows the part to move upward without damaging the back gauge. These fingers are able to move freely with the piece and out of the way.
Tandem
Two or more press brakes controlled by the same controller that are used to bend extremely large parts.
Throat
The depth of the press brake before the vertical supports limits the flange length. Most press brakes are restricted only by the throat of a brake around the drive cylinders.
Top dead center
In addition to bottom dead center, this is the position of the press brake when it is opened to its maximum height.
Tonnage control
The machine's ability to regulate its tonnage up to the maximum tonnage is called tonnage control. This is even greater with modern hydraulic brakes, which can control their tonnage very precisely.
Rising action brake
A press brake where the lower beam moves the die up the punch.
Upper Beam
The top part of a press brake that holds the punch holder.
X axis
The front-to-back movement of the back gauge is called the X-Axis. It controls the length of the flange, with positive movement moving the back gauge toward the operator and resulting in a smaller flange.
-
X1 Axis
The front-to-back movement of the left rear gauge is independent of the right rear gauge. -
X2 Axis
The front-to-back movement of the right rear gauge is independent of the left rear gauge. -
X1-X2
Tilting the back gauge creates an angled bend line relative to the back of the workpiece.
R axis
The vertical movement of the rear gauges.
-
Axis R1
The vertical movement of the left rear gauge is independent of the right rear gauge. -
Axis R2
The vertical movement of the right rear gauge is independent of the left rear gauge. -
R1-R2
Tilting the back gauge creates a vertical travel stop used for workpieces with odd flanges.
Z axis
The left-to-right movement of the rear gauge is called the Y axis. This is used when bending with multiple settings on the press brake, allowing the gauges to move with the operator as they move the workpiece from one setting to another .
-
Z1 axis
The left-to-right movement of the left back gauge. -
Z2 Axis
The left-to-right movement of the right back gauge. -
Y axis
The vertical movement of the moving beam. This does not mean the back gauge movement.