Transmisión neumática
La transmisión neumática implica la transferencia de energía mediante presión de gas o fluido a través de gas comprimido como medio de trabajo.
El sistema de transferencia de energía implica transferir gas comprimido a través de tubos y válvulas de control al actuador neumático, que transforma la presión del gas comprimido en energía mecánica.
El sistema de transmisión de información implica el uso de elementos lógicos neumáticos o elementos de chorro para realizar operaciones lógicas, también conocido como sistema de control neumático.
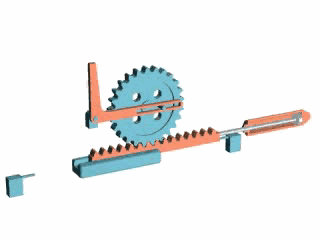
Características de la transmisión neumática.
Con una presión de trabajo baja, en promedio de 0,3 a 0,8 MPa, los sistemas neumáticos tienen una baja viscosidad del gas y pérdidas mínimas en las tuberías, lo que los hace ventajosos para suministrar y transportar gas a distancias moderadas. Estos sistemas también son seguros de usar ya que no presentan riesgos de explosión o descarga eléctrica y tienen funciones de protección contra sobrecargas. Sin embargo, cabe señalar que los sistemas neumáticos requieren un suministro de aire comprimido.
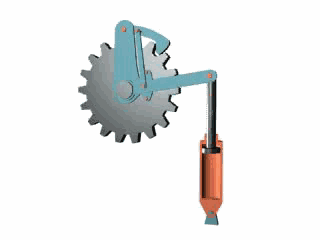
Composición de la transmisión neumática.
La transmisión neumática comprende una fuente de aire, un actuador neumático, una válvula de control neumática y accesorios neumáticos.
Las fuentes de aire normalmente son suministradas por compresores.
El actuador neumático convierte la presión del gas comprimido en energía mecánica para accionar piezas funcionales como cilindros y motores neumáticos.
La válvula de control neumática ajusta la dirección, la presión y el flujo de aire y se clasifica en válvulas de control direccional, válvulas de control de presión y válvulas de control de flujo.
Los accesorios neumáticos incluyen purificadores de aire, lubricadores de aire, silenciadores de ruido y juntas de tuberías, entre otros.
Los sensores aerodinámicos también se utilizan para detectar y transmitir información en sistemas de transmisión neumática.
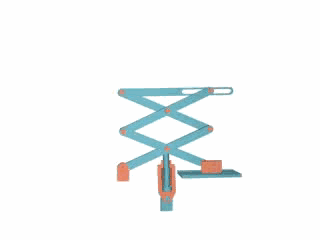
Ventajas de la transmisión neumática.
La transmisión neumática utiliza como medio el aire, que es una fuente inagotable y de fácil acceso que puede descargarse directamente después de su uso sin contaminar el medio ambiente. Además, la tubería no es compleja ya que no es necesaria una tubería de retorno.
El aire tiene baja viscosidad y disipación de energía del flujo, lo que lo hace adecuado para el suministro centralizado de gas y el transporte de larga distancia.
La transmisión neumática es segura y confiable, no requiere protección contra incendios o explosiones y puede operar en ambientes con altas temperaturas, radiación, humedad, polvo y otras condiciones.
La transmisión neumática es rápida y la estructura de los componentes neumáticos es simple, lo que los hace fáciles de procesar y mantener con una larga vida útil. La tubería no está sujeta a obstrucciones y el medio no tiene problemas de reemplazo metamórfico.
Desventajas de la transmisión neumática.
La alta compresibilidad del aire puede afectar negativamente a la estabilidad dinámica de los sistemas neumáticos, lo que tiene como resultado un impacto significativo en la velocidad de trabajo debido a los cambios de carga.
La baja presión de los sistemas neumáticos dificulta la producción de gran potencia y par.
La transmisión de señales de control aéreo es más lenta que la de los sistemas electrónicos y de la velocidad de la luz, lo que la hace inadecuada para sistemas de transmisión complejos y de alta velocidad.
Los sistemas neumáticos generan mucho ruido de escape.
Transmisión Hidráulica
La transmisión hidráulica es la transmisión de potencia y control utilizando líquido como medio de trabajo.
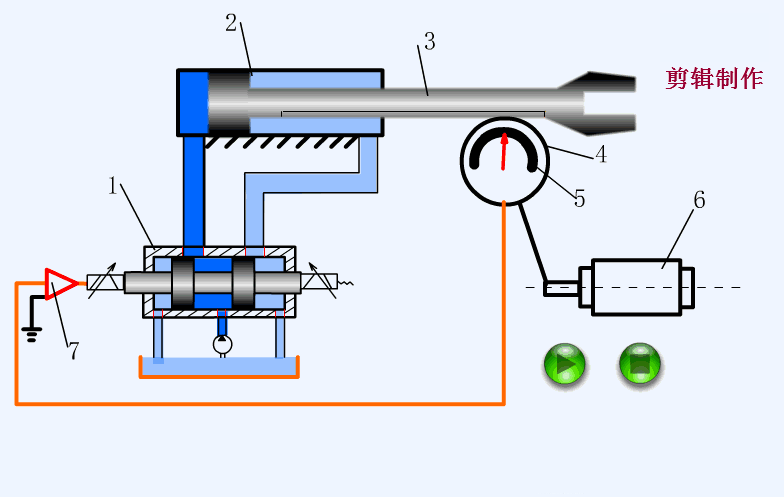
El principio básico de la transmisión hidráulica.
Las bombas hidráulicas convierten la energía mecánica en energía de presión del líquido, que luego se transfiere mediante cambios en la presión del líquido. Se utiliza una variedad de válvulas y tubos de control para transmitir potencia a actuadores hidráulicos, como cilindros o motores hidráulicos, que convierten la presión del líquido en energía mecánica para impulsar el mecanismo de trabajo, permitiendo el movimiento alternativo y giratorio en línea recta.
El líquido utilizado se denomina medio de trabajo y habitualmente se utiliza aceite mineral para este fin.
La función de la transmisión hidráulica es similar a la de los elementos de transmisión de la transmisión mecánica, como correas, cadenas y engranajes.
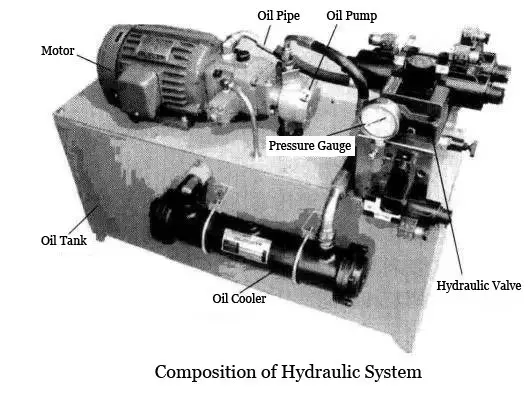
Sistema de transmisión hidráulica
El sistema hidráulico consta de una bomba hidráulica, una válvula de control hidráulico, actuadores hidráulicos (como cilindros y motores hidráulicos) y piezas hidráulicas auxiliares (incluyendo tuberías y acumuladores, entre otros).
Las plegadoras son un ejemplo de un sistema que utiliza transmisión hidráulica.
Componentes del sistema de transmisión hidráulica.
El sistema hidráulico comprende varios componentes, incluidos componentes de potencia (como bombas hidráulicas), actuadores (incluidos cilindros hidráulicos y motores hidráulicos), elementos de control, componentes auxiliares (como tanques de combustible, filtros de aceite, tuberías y juntas, refrigeradores, manómetros). y el medio de trabajo (es decir, aceite hidráulico).
Los componentes de potencia, como la bomba hidráulica, convierten la energía mecánica en energía cinética del fluido (presión y flujo) y suministran aceite bajo presión al sistema hidráulico, actuando como fuente de energía del sistema.
Los actuadores, como los cilindros hidráulicos o los motores hidráulicos, convierten la energía hidráulica en energía mecánica y son isotérmicos. Los cilindros hidráulicos impulsan mecanismos para realizar movimientos alternativos o lineales, mientras que los motores hidráulicos realizan movimientos de rotación.
Los elementos de control, que se refieren a varios componentes, se utilizan para controlar y ajustar la presión, el flujo y la dirección del fluido en el sistema hidráulico, asegurando que los actuadores funcionen de acuerdo con las especificaciones requeridas.
Los componentes auxiliares proporcionan las condiciones necesarias para el correcto funcionamiento del sistema y facilitan el seguimiento y control.
El medio de trabajo es fluido de transmisión, típicamente aceite hidráulico. El sistema hidráulico utiliza este medio de trabajo, que también lubrica las partes móviles de los componentes hidráulicos.
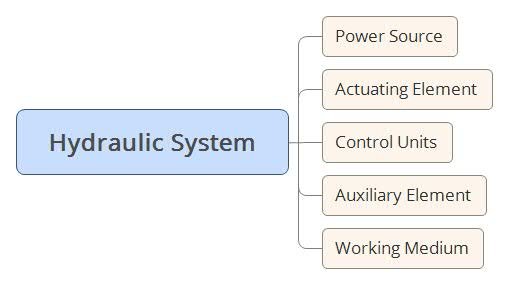
El principio de funcionamiento del sistema de transmisión hidráulica.
A continuación se muestra un ejemplo de un molinillo sencillo.
El motor acciona la bomba hidráulica para extraer el aceite del tanque, lo que transforma la energía mecánica del motor en energía de presión del líquido.
El medio hidráulico ingresa a la cavidad izquierda del cilindro hidráulico a través de la válvula de mariposa y la válvula de inversión, empujando el pistón para mover el lado derecho de la mesa. Luego, el medio hidráulico se descarga de la cavidad derecha del cilindro hidráulico y regresa al tanque.
Después de pasar por la válvula de inversión, el medio hidráulico ingresa a la cavidad derecha del cilindro hidráulico, lo que hace que el pistón se mueva hacia la izquierda y empuje la mesa hacia atrás.
La velocidad de movimiento del cilindro hidráulico se puede ajustar cambiando la apertura del acelerador.
La presión del sistema hidráulico se puede ajustar mediante la válvula de alivio.
Al dibujar un diagrama de un sistema hidráulico, se utilizan símbolos para representar los componentes hidráulicos para simplificar. Estos símbolos se llaman símbolos funcionales.
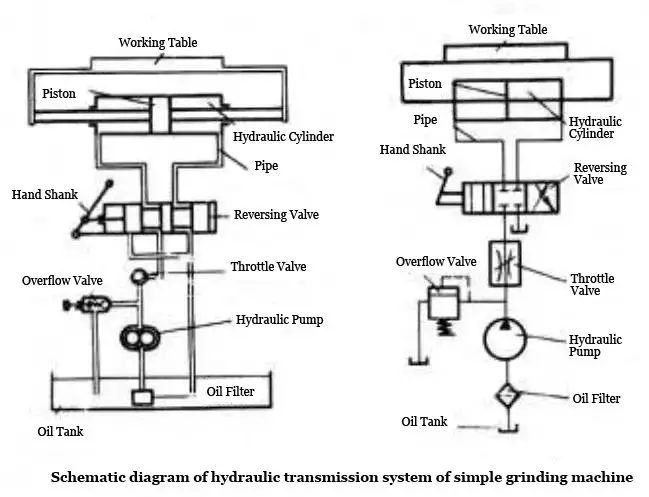
circuito básico
Un sistema de transmisión hidráulica típico comprende varios componentes hidráulicos que trabajan juntos para lograr funciones específicas.
Cualquier sistema de transmisión hidráulica se compone de varios circuitos básicos, cada uno con funciones de control específicas. Combinando estos circuitos básicos, se puede controlar la dirección del movimiento, la presión de trabajo y la velocidad de movimiento del actuador.
Según su función de control, el circuito básico se divide en tres tipos: bucle de control de presión, bucle de control de velocidad y bucle de control de dirección.
1. Circuito de control de presión
La válvula de control de presión se utiliza para controlar todo el sistema o un circuito de presión de rango local.
Según su función, el circuito de control de presión se puede dividir en cuatro circuitos: ajuste de presión, cambio de presión, liberación de presión y estabilización de presión.
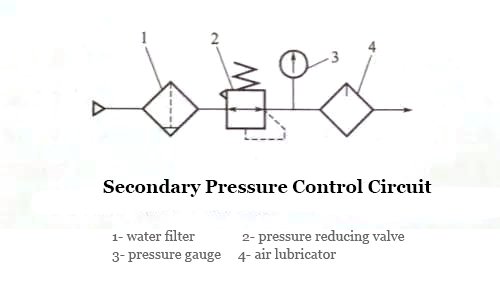
2. Bucle de control de velocidad
Este circuito controla el flujo del actuador regulando el flujo del medio hidráulico. La función del bucle de control de velocidad se divide en dos partes: el circuito de regulación de velocidad y el bucle de sincronización.
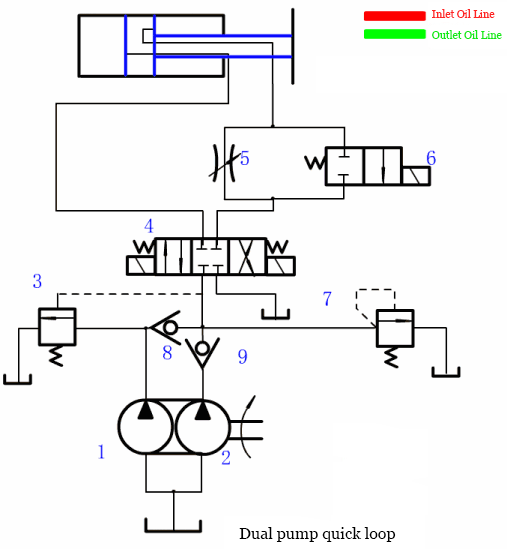
3. Bucle de control de dirección
Este circuito controla la dirección del flujo del medio hidráulico. La válvula de control direccional controla la dirección del movimiento de un solo actuador, permitiéndole moverse o detenerse en dirección positiva y negativa, lo que se conoce como circuito conmutador.
Cuando el elemento actuador se detiene, el circuito que evita fugas externas debido a la carga u otros factores externos se denomina circuito de enclavamiento.
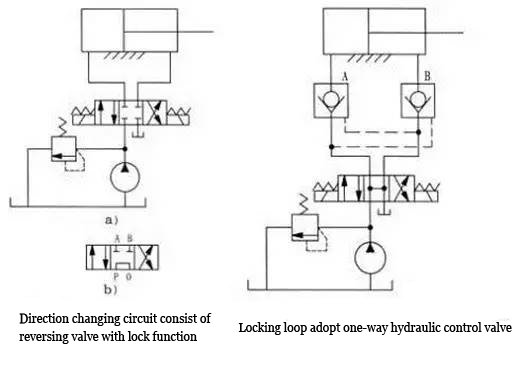
Accionamiento Hidráulico
La transmisión hidráulica implica la transferencia de energía a través de energía cinética neta, utilizando líquido como medio de trabajo.
El impulsor convierte la velocidad de rotación y el par de entrada de un motor (como un motor de combustión interna, un motor, una turbina, etc.) y acciona las piezas de trabajo de la máquina a través del eje de salida.
El fluido y el impulsor interactúan entre sí en el eje de entrada, el eje de salida y la carcasa, produciendo un cambio en el impulso para transmitir potencia.
La transmisión hidráulica difiere significativamente en principio, estructura y rendimiento de la transmisión hidráulica basada en presión de fluido.
El eje de entrada y el eje de salida del accionamiento hidráulico solo están conectados al medio de trabajo a través de líquido, y el contacto indirecto entre los componentes da como resultado una transmisión no rígida.
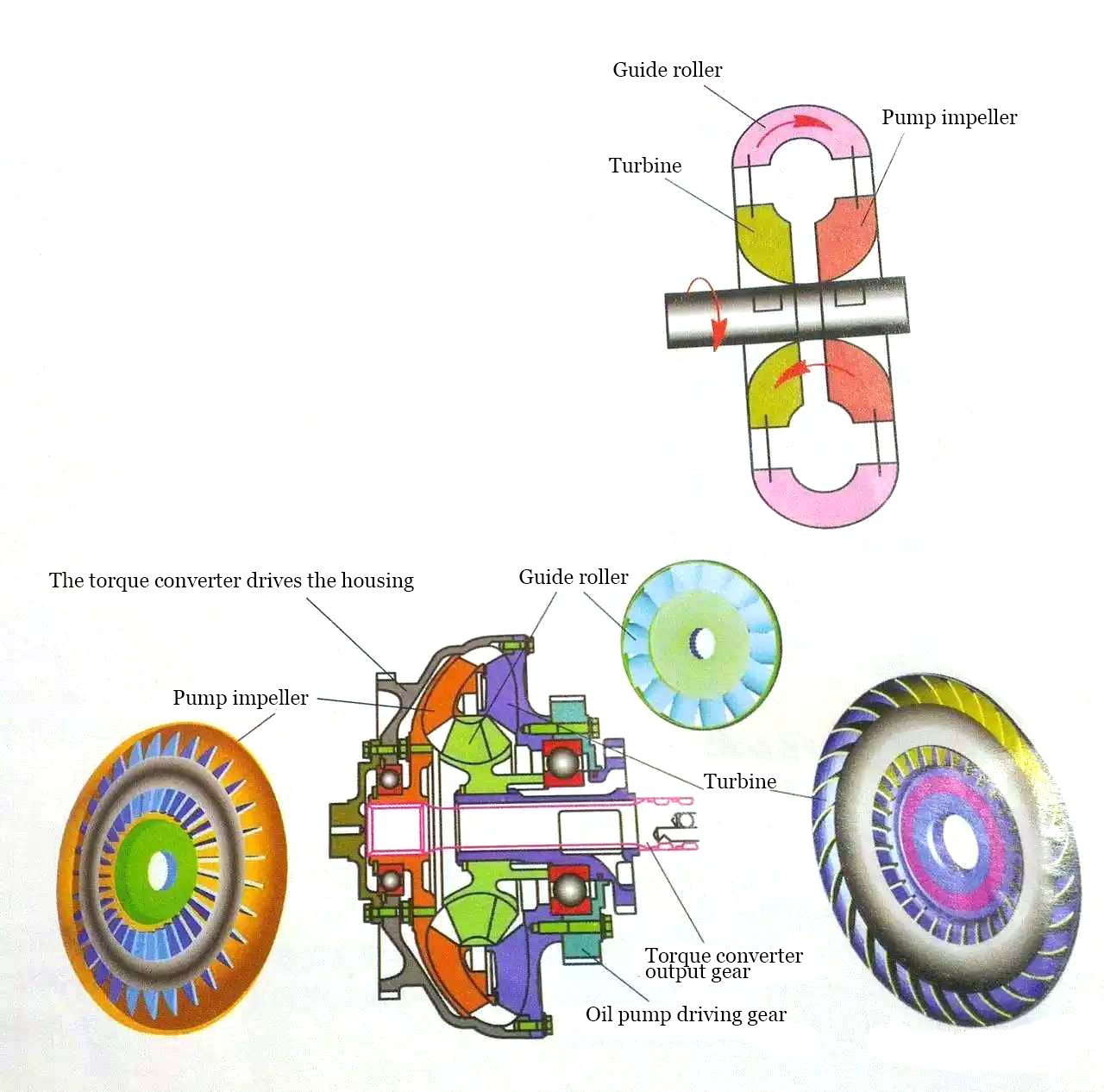
Características del accionamiento hidráulico.
Adaptabilidad automática
El convertidor de par hidráulico puede aumentar o disminuir automáticamente su par de salida con cambios en las cargas externas, y la velocidad puede aumentar o disminuir en consecuencia, logrando una regulación continua de la velocidad dentro de un amplio rango.
Aislamiento de vibraciones
Como el medio de trabajo entre los impulsores es líquido, su conexión no es rígida, lo que permite absorber los golpes y vibraciones del motor y las cargas externas. Esto asegura un arranque estable, aceleración y funcionamiento uniforme, prolongando la vida útil de las piezas.
Rendimiento de penetración
Cuando la velocidad de rotación de la bomba es constante y la carga cambia, el eje de entrada (es decir, la rueda de la bomba o el eje del motor) cambia.
Se pueden utilizar diferentes tipos de elementos hidráulicos para satisfacer los requisitos del motor para diferentes máquinas de trabajo, mejorando la potencia mecánica y el rendimiento económico.
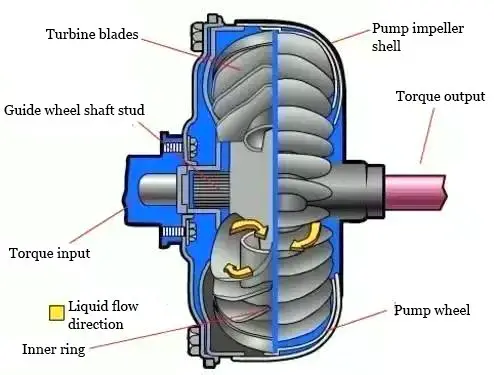
El principio básico del accionamiento hidráulico.
La fuente de energía original (como un motor de combustión interna, un motor, etc.) impulsa la rotación de la rueda de la bomba, aumentando la velocidad y la presión del fluido de trabajo y convirtiendo la energía mecánica en energía cinética neta.
El líquido de trabajo, ahora con energía cinética, golpea la turbina y libera energía a la turbina, haciendo que gire y alimente la salida, transfiriendo energía.
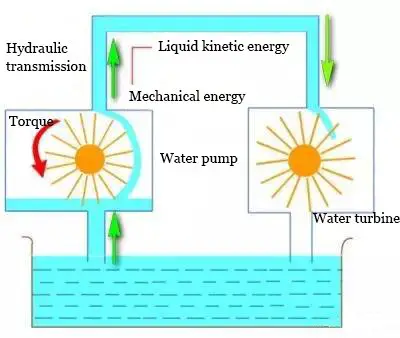
Dispositivo de transmisión hidráulica
La transmisión hidráulica utiliza energía cinética neta para transferir potencia y generalmente incluye acopladores hidráulicos, convertidores de par hidráulico y componentes mecánicos hidráulicos.
1. Acoplador hidráulico
Un acoplador hidráulico, también conocido como acoplamiento hidráulico, es un dispositivo mecánico que se utiliza para conectar una fuente de energía (generalmente un motor o motor) a una máquina en funcionamiento para proporcionar potencia de rotación.
Además de su uso en transmisiones automáticas de automóviles, los acopladores hidráulicos se utilizan ampliamente en la industria marina y pesada.
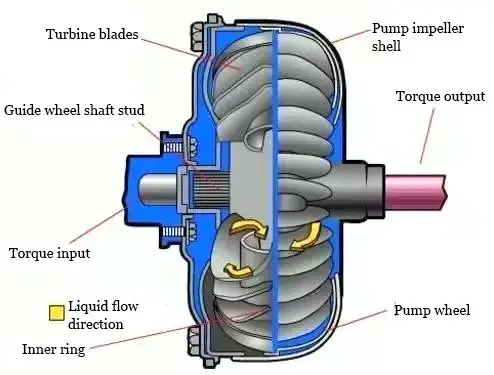
2. Convertidor de par
Un convertidor de par hidráulico es un elemento hidráulico que consta de una rueda de bomba, una turbina y una rueda guía. Se instala entre el motor y la transmisión y utiliza aceite hidráulico como medio de trabajo para transmitir y convertir el par, ajustar la velocidad y proporcionar la funcionalidad de desconexión.
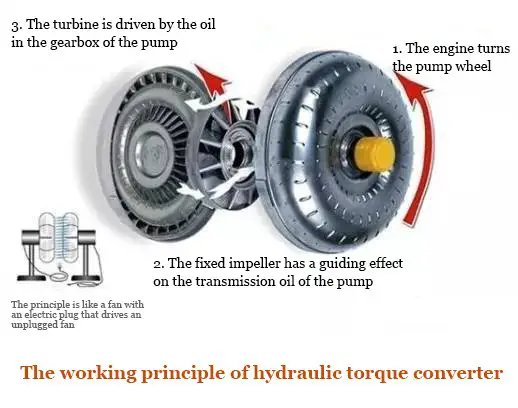
Aplicación de accionamiento hidráulico
El uso de la transmisión hidráulica en máquinas modernas se inició a principios del siglo XX, principalmente como equipos de potencia naval y mecanismos de transmisión entre hélices para resolver el problema de la velocidad limitada debido a las turbinas de vapor o gas de alta potencia y velocidad que sufren de “cavitación”. ”. "
Hoy en día, la transmisión hidráulica se utiliza ampliamente en automóviles, tractores, máquinas de construcción, locomotoras, vehículos blindados, perforadoras de petróleo, máquinas de elevación y transporte, ventiladores, bombas y otros equipos.