1. Materiales experimentales
1.1 Parámetros de rendimiento del material
El experimento estudió el acero de alta resistencia DP590, cuya composición química se presenta en la Tabla 1, y los parámetros de desempeño se presentan en la Tabla 2.
Tabla 1 Composición química del material (fracción de masa)
Grado del material | W. | Sí | Minnesota | PAG | s | Alabama | Tú |
DP590 | 0,078 | 0,03 | 1,76 | 0,01 | 0.004 | ≥ 0,020 | – |
Tabla 2 Parámetros de rendimiento del material
Parámetro | Valor |
Exponente de endurecimiento por trabajo n | 0,13 |
Relación de Poisson μ | 0,33 |
Módulo de elasticidad E/MPa | 199.000 |
Exponente de endurecimiento K | 1.003 |
Límite elástico/MPa | 318 |
Resistencia a la tracción/MPa | 626 |
Relación rendimiento/tracción/% | 50 |
1.2 Curva tensión-deformación
La prueba de tracción se llevó a cabo de acuerdo con el estándar de prueba GB/T 228.1-2010, y la curva tensión-deformación verdadera obtenida a partir de los datos de la prueba se muestra en la Figura 1.
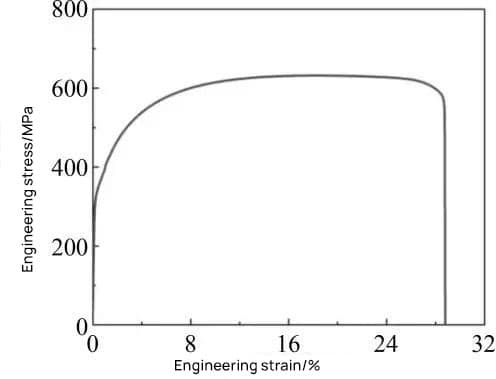
dos . Establecimiento del modelo de elementos finitos.
2.1 Establecimiento del modelo
Según el caso del estándar internacional NUMISHEET2011 y el tamaño de las piezas de viga comúnmente utilizadas en la producción real, el tamaño de la placa utilizada para la pieza en forma de U se determina como 100 mm × 360 mm × 1,2 mm.
La estructura bidimensional ensamblada se muestra en la Figura 2, y las dimensiones geométricas de las piezas del molde se muestran en la Tabla 3. El modelo se creó en el software UG NX de acuerdo con el dibujo y la estructura explosiva se ensambló como se muestra en la Figura 3.
Luego se importó a Dynaform para la generación de malla y la configuración básica de los parámetros del proceso, como se muestra en la Figura 4.
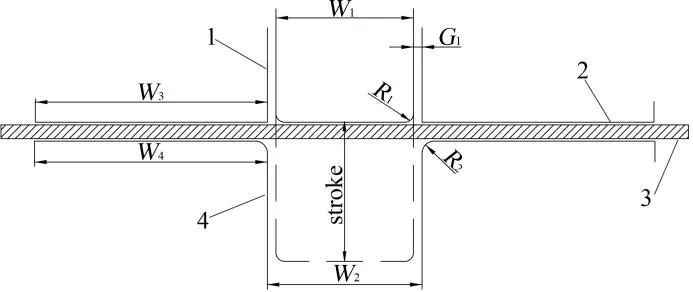
- 1. Golpe
- 2. Anillo con brida
- 3. Chapa
- 4. morir
Tabla 3 Dimensiones geométricas de las piezas del molde
Parámetro | Dimensiones/mm |
W1 | 80 |
W2 | 84 |
W3 | 135 |
W4 | 135,5 |
R1 | 5.0 |
R2 | 7.0 |
G1 | 1.2 |
ataque | 70 |
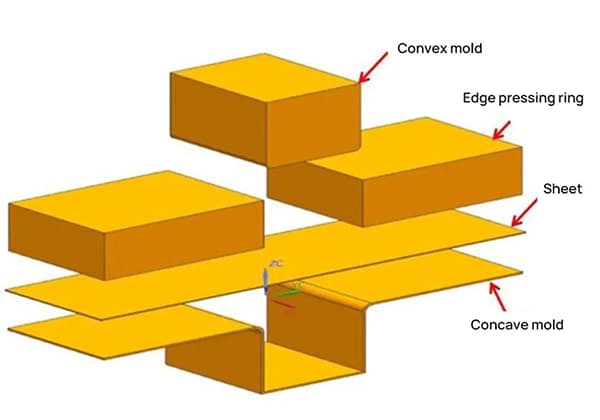
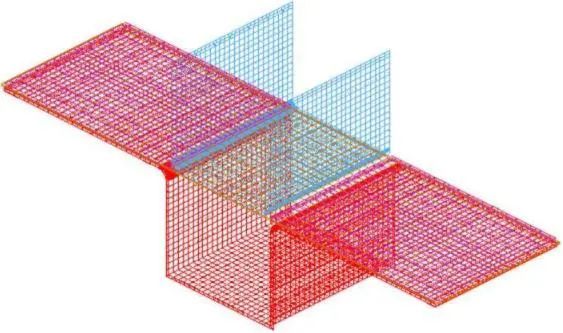
2.2 Razones para el Springback y los estándares de evaluación
Durante el proceso de estampación, la chapa sufrirá grandes deformaciones elásticas.
En la etapa final del estampado, la descarga de la carga hará que se libere la energía elástica previamente generada, provocando que las tensiones internas se recombinen, cambiando así la forma de la pieza. Esto da como resultado el defecto de recuperación elástica de la chapa.
Ahora, se selecciona la sección media de la pieza en forma de U para medir la situación de recuperación elástica, como se muestra en la Figura 5.
El tamaño del springback se caracteriza por el ángulo complementario μ del ángulo θ entre las superficies AB y CD. Cuanto mayor sea el ángulo μ, mayor será la amplitud del retorno elástico.
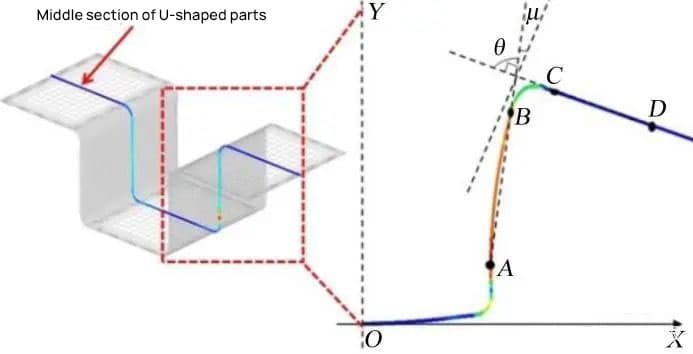
3. Investigación de los factores que afectan el ángulo de recuperación elástica.
Los factores que afectan la recuperación elástica de las piezas estampadas son principalmente la estructura del molde, la forma de la chapa y las propiedades mecánicas, además de los parámetros del proceso de estampado.
En vista de las características estructurales y del proceso de estampado de la pieza en forma de U, se seleccionaron cuatro factores principales, incluida la fuerza de brida, el coeficiente de fricción, el espesor de la chapa y el radio de la esquina del punzón, para explorar la influencia de diferentes factores en la variación del resorte. ángulo. .
3.1 Influencia de la fuerza de brida
En las condiciones de uso de acero de alta resistencia DP590 con un espesor de 1,2 mm y un coeficiente de fricción de 0,125, y un espacio (G1) de 1,2 mm entre el punzón y la matriz, la influencia de la fuerza de brida en el resorte fue estudiado realizando simulaciones de formación y recuperación elástica con fuerzas en las alas que van desde 10 kN a 120 kN.
La influencia de la fuerza de brida en el ángulo de recuperación elástica obtenido mediante la simulación se muestra en la Tabla 4 y la Figura 6.
Tabla 4 Relación entre fuerza de brida y recuperación elástica.
Fuerza de brida/kN | Ángulo de recuperación elástica (°) |
10 | 8.126 |
20 | 8,902 |
40 | 7.734 |
60 | 6.660 |
80 | 5.572 |
100 | 4,226 |
120 | 3.686 |
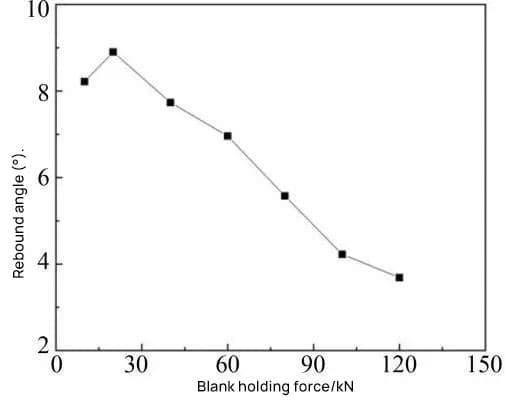
Como se muestra en la Figura 6, el ángulo de recuperación elástica de la pieza inicialmente aumenta y luego disminuye. En la Tabla 4, se puede ver que cuando la fuerza de la brida varía de 10 kN a 120 kN, el cambio máximo en el ángulo de recuperación elástica es de 5,216°, lo que indica que controlar la fuerza de la brida tiene un efecto más obvio sobre el ángulo de retorno elástico.
La razón del fenómeno anterior es: cuando la fuerza de brida es pequeña, la pieza se forma principalmente por flexión. La chapa de metal produce una tensión de flexión bajo la acción del punzón, y la tensión de flexión se libera después de que se descarga el punzón, lo que conduce a un aumento de la recuperación elástica.
Cuando la fuerza de la brida aumenta hasta cierto punto, la deformación plástica del material aumenta, lo que hace que disminuya la cantidad de deformación elástica liberada por la chapa y, por lo tanto, también disminuye la recuperación elástica.
3.2 Influencia del coeficiente de fricción
En las condiciones de uso de una fuerza de brida de 40 kN y un espacio de 1,2 mm entre el punzón y la matriz, se estudió la influencia del coeficiente de fricción en la recuperación elástica realizando simulaciones de conformación y recuperación elástica con coeficientes de fricción que oscilan entre 0,025 y 0,275. .
La influencia del coeficiente de fricción en el ángulo de recuperación elástica obtenido mediante la simulación se muestra en la Tabla 5 y la Figura 7.
Tabla 5 Relación entre Coeficiente de Fricción y Springback.
Coeficiente de fricción | Ángulo de recuperación elástica (°) |
0.025 | 8.126 |
0,075 | 8,902 |
0,125 | 7.734 |
0,175 | 6.660 |
0.225 | 5.572 |
0.275 | 4,226 |
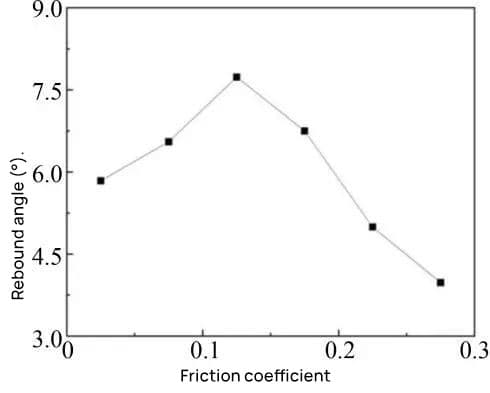
La Tabla 5 muestra que cuando el coeficiente de fricción varía de 0,025 a 0,275, el cambio máximo en el ángulo de recuperación elástica es de 4,676°, lo que indica que controlar el coeficiente de fricción tiene un efecto más obvio en el ángulo de recuperación elástica.
Como se muestra en la Figura 7, el ángulo de recuperación elástica de la lámina metálica aumenta primero y luego disminuye con el aumento del coeficiente de fricción.
La razón del fenómeno anterior es: inicialmente, debido a que el coeficiente de fricción es pequeño, la resistencia a la fricción del material es pequeña y el proceso de conformado de la chapa es principalmente de flexión, lo que resulta en una gran cantidad de recuperación elástica.
A medida que el coeficiente de fricción aumenta gradualmente, también aumenta la resistencia a la fricción del material. Cuando la resistencia a la fricción es lo suficientemente grande, el borde de la chapa es difícil de mover y el proceso de formación de la pieza es principalmente deformación plástica.
Después de descargar el punzón, la chapa liberará menos energía potencial elástica y, por lo tanto, la recuperación elástica de la chapa disminuirá.
3.3 Influencia del espesor de la chapa
En condiciones de utilizar una fuerza de brida de 40 kN, un espacio de 1,2 mm entre el punzón y la matriz, un coeficiente de fricción de 0,125 y un radio del punzón de R5 mm, se estudió la influencia del espesor de la chapa en el resorte. Realización de simulaciones de formación y recuperación elástica con espesores de chapa que oscilan entre 1,0 mm y 1,8 mm.
La influencia del espesor de la lámina en el ángulo de recuperación elástica obtenido mediante la simulación se muestra en la Tabla 6 y la Figura 8.
Tabla 6 Relación entre el Espesor de la Chapa y el Springback.
Espesor de chapa/mm | Ángulo de recuperación elástica (°) |
1 | 10.541 |
1.2 | 7.734 |
1.4 | 5.448 |
1.6 | 3.814 |
1.8 | 2030 |
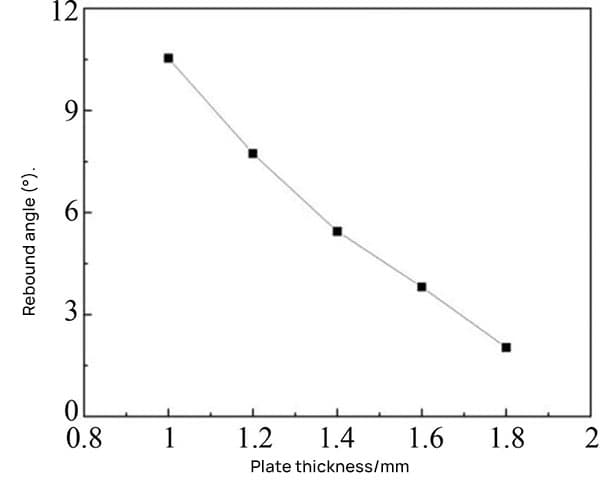
Como se muestra en la Tabla 6, cuando el espesor de la lámina varía de 1,0 mm a 1,8 mm, el cambio máximo en el ángulo de recuperación elástica es de hasta 8,511°, que es el mayor entre los cuatro factores seleccionados, lo que indica que el control del espesor de la lámina tiene un efecto relativamente obvio. efecto sobre el ángulo de recuperación elástica.
Como se muestra en la Figura 8, el ángulo de recuperación elástica de la chapa disminuye al aumentar el espesor de la chapa.
Esto se debe principalmente a que, bajo la condición de radio de punzón constante, cuanto mayor es el espesor de la chapa, menor es la relación entre el radio de curvatura y el espesor de la chapa, lo que da como resultado una menor deformación por flexión de la chapa y una menor proporción de deformación elástica en la deformación total.
Por lo tanto, cuando se descarga el punzón, la recuperación elástica de la lámina disminuye.
3.4 Influencia del radio de la esquina del punzón
En condiciones de uso de una fuerza en la brida de 40 kN y un coeficiente de fricción de 0,125, se estudió la influencia del radio de las esquinas del punzón en la recuperación elástica realizando simulaciones de conformación y recuperación elástica con radios de las esquinas del punzón que varían de R3 mm a R7 mm.
La influencia del radio de la esquina del punzón en el ángulo de recuperación elástica obtenido mediante la simulación se muestra en la Tabla 7 y la Figura 9.
Tabla 7 Relación entre el radio de las esquinas del punzón y la recuperación elástica.
Radio de filete de punzonado/mm | Ángulo de recuperación elástica (°) |
3 | 6.388 |
4 | 6.982 |
5 | 7.734 |
6 | 8.153 |
7 | 8.553 |
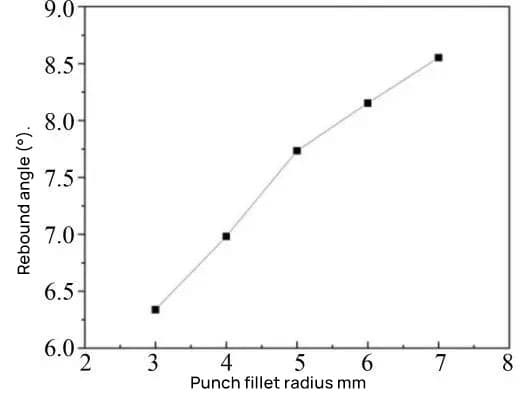
Según las observaciones realizadas en la Tabla 7 y la Figura 9, aumentar el radio del filete del punzón de 3 mm a 7 mm da como resultado un aumento en el ángulo de recuperación elástica de 6,388° a 8,553°.
Este comportamiento se atribuye al aumento del área de contacto entre el filete del punzón y la chapa, lo que posteriormente aumenta la deformación por flexión, provocando un mayor efecto de recuperación elástica.
Sin embargo, en la Tabla 7, se observa que el cambio en el valor máximo de recuperación elástica de 3 mm a 7 mm en el radio del filete del punzón es de sólo 2,165°, que es el efecto más pequeño entre los cuatro factores seleccionados.
Esto implica una influencia mínima del radio de filete del punzón en el ángulo de recuperación elástica.