El engranaje es el componente más importante de la caja de cambios. Durante el funcionamiento, la superficie del diente soporta la tensión de contacto, mientras que la raíz del diente soporta la tensión de flexión. En consecuencia, las formas de falla de los engranajes se clasifican principalmente en corrosión por picaduras y sarro debido a la fatiga de la superficie del diente y fractura del diente causada por la fatiga de la raíz del diente.
La carburación y el templado son los procesos más utilizados y desarrollados para engranajes de alta velocidad y de servicio pesado.
Este método puede mejorar simultáneamente la resistencia a la fatiga por contacto de la superficie del diente y la resistencia a la fatiga por flexión de la raíz del diente. Sin embargo, el proceso de cementación y enfriamiento es complicado y pueden ocurrir varios tipos de defectos durante el tratamiento térmico, lo que puede provocar fallas tempranas en los engranajes.
Durante la prueba de resistencia a la fatiga de un conjunto de transmisión recientemente desarrollado por nuestra empresa, uno de los engranajes se rompió.
Las especificaciones de diseño requieren que el material del engranaje sea 8620H. Pasó por carburación y enfriamiento y luego se atemperó a baja temperatura. La profundidad efectiva de la capa endurecida es de 0,8 a 1,3 mm, la dureza de la superficie es de 58 a 64 HRC y la dureza del núcleo es de 30 a 45 HRC.
Para determinar la causa de la fractura dental realizamos pruebas y analizamos la morfología de la fractura, el material y la calidad del tratamiento térmico.
1. Pruebas y análisis físicos y químicos.
(1) Observación macro
La Figura 1 ilustra la apariencia general del engranaje averiado. Varios dientes se rompen de raíz y el número de dientes rotos supera la mitad del número total de dientes.
La macromorfología de la fractura se muestra en la Figura 2.
Según la morfología de la fractura, la mayoría de las fracturas tienen características obvias de fractura por fatiga. El origen de la fractura se encuentra en la raíz del diente.
El área de expansión por fatiga suave que irradia hacia afuera representa aproximadamente de 1/3 a 1/2 del área total de la raíz.
La superficie de fractura del área de fractura transitoria es rugosa y de color gris oscuro.
Además de las fracturas por fatiga, algunas fracturas de engranajes no presentan características de fractura por fatiga y son el resultado de fracturas por sobrecarga única.
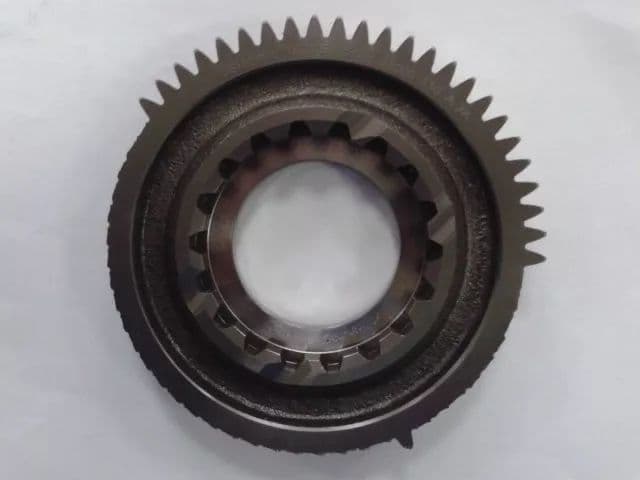
Fig. 1 Descripción general de los dientes rotos
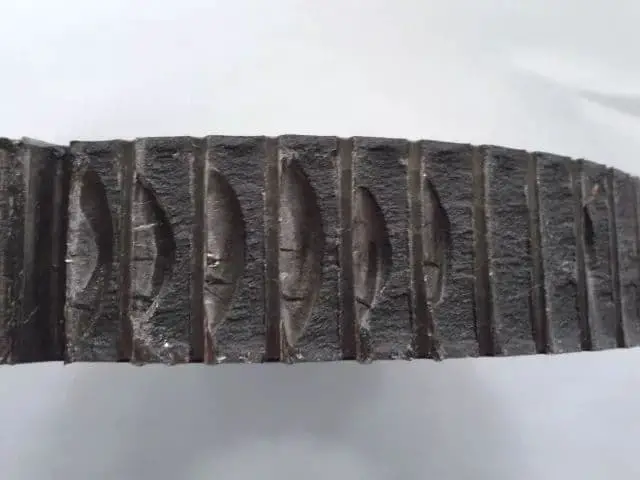
Fig. 2 Morfología de la fractura
(2) Fractografía
Después del muestreo, se observó la morfología de la fractura bajo un microscopio electrónico de barrido.
La Figura 3 muestra cómo se ve la fuente de la grieta.
El origen de la grieta se encuentra en la raíz del diente. En la figura, se puede ver que el origen de la grieta de fractura no converge en un punto, sino que es lineal.
La superficie de la fuente de la grieta es lisa debido a la fricción y extrusión repetidas.
Tras un examen más detenido, se ven estructuras negras anormales en el origen de la grieta (ver Fig. 4).
En la Fig. 2 se muestra la observación de la morfología microscópica de la zona de crecimiento por fatiga con un aumento de 1000x.
A gran aumento se pueden observar estrías de fatiga y prismas radiales.
La Figura 6 ilustra que la apariencia de la zona de fractura transitoria es una fractura ondulada + cuasi escisión, lo que indica una buena tenacidad del centro del engranaje.
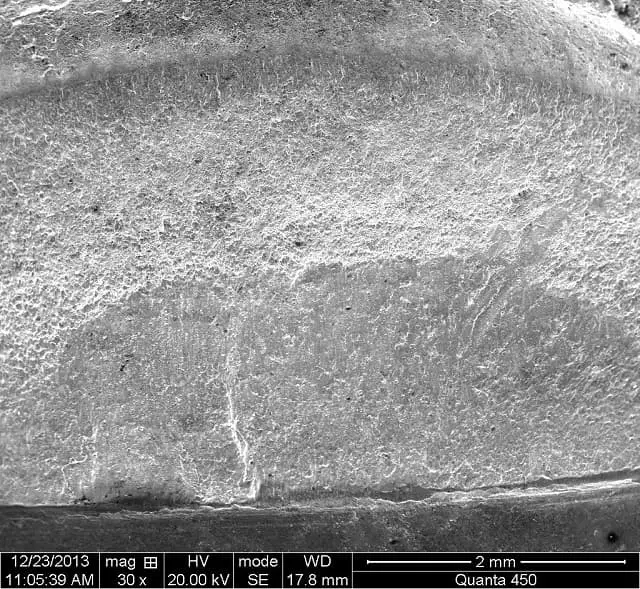
Fig. 3 Fuente de grietas
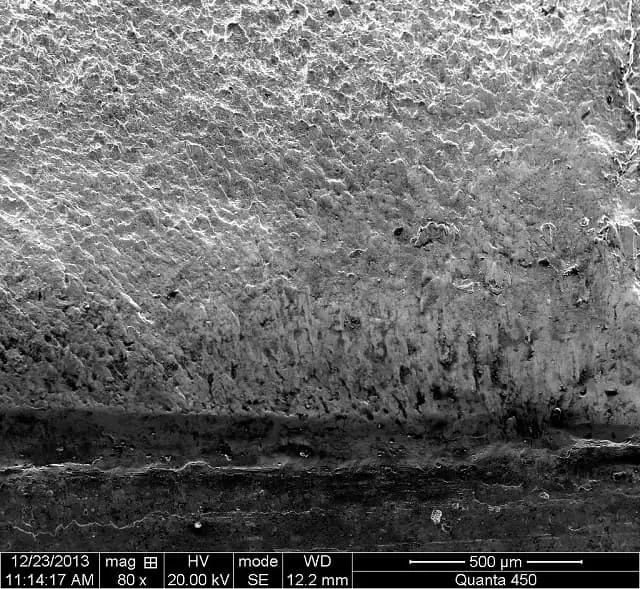
Fig. 4 Estructura de la fuente de la grieta negra
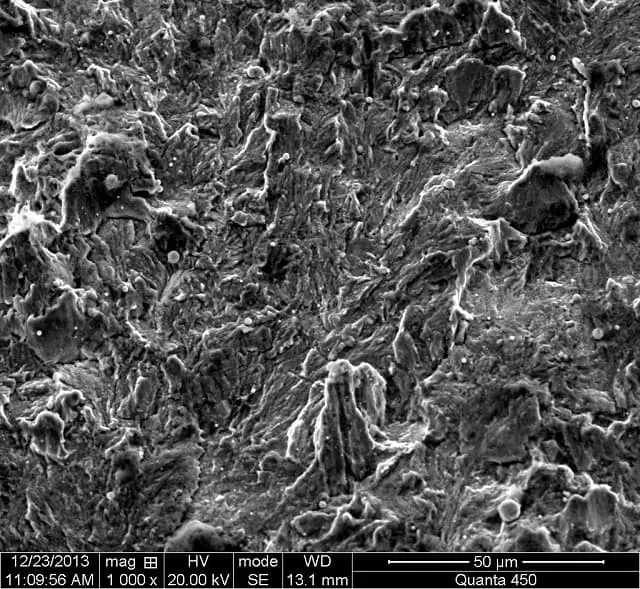
Fig. 5 Fractura por propagación de fatiga
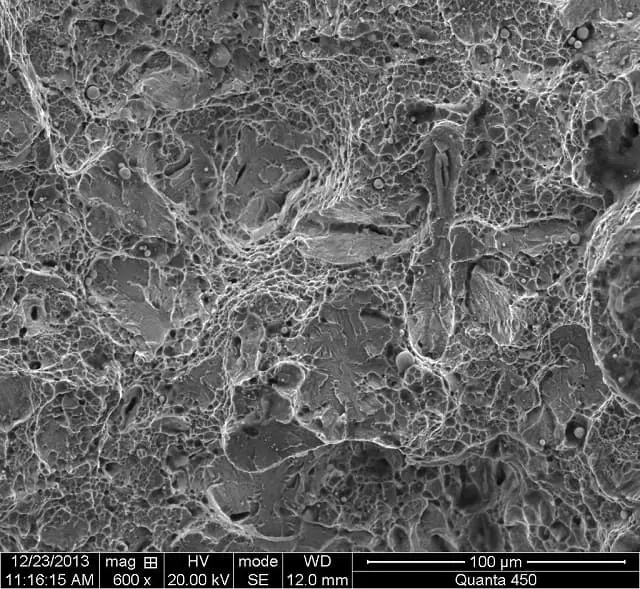
Fig. 6 Morfología de la ondulación + cuasi escisión en la zona de fractura transitoria
(3) Inspección del material de los engranajes
Se tomaron muestras del engranaje roto para análisis de composición química y los resultados se presentan en la Tabla 1.
Según el análisis, la composición química del engranaje cumple con los requisitos técnicos de la norma SAEJ1268 para acero 8620H.
Tabla 1 Resultados de las pruebas de composición química (fracción de masa) (%)
Elemento | W. | s | PAG | Sí | Minnesota | cr | No | Mes | Culo |
Valor estandar | 0,17~0,23 | ≤0,040 | ≤0,030 | 0,15~-0,35 | 0,60~0,95 | 0,35~0,65 | 0,35~0,75 | 0,15~0,25 | ≤0,35 |
Valor de detección | 0,22 | 0,017 | 0.010 | 0,28 | 0,87 | 0,58 | 0,45 | 0,18 | 0.086 |
(4) Inspección de calidad del tratamiento térmico de engranajes.
Para comprobar la calidad del tratamiento térmico, coloque el engranaje intacto junto al roto.
La dureza de la superficie es de 61 HRC y la dureza del núcleo es de 45 HRC.
La estructura superficial comprende martensita y austenita retenida, con un contenido de austenita retenida de aproximadamente el 15%. El centro está formado por martensita torneada y una pequeña cantidad de bainita.
La profundidad efectiva de la capa endurecida a la altura de 1/2 diente es de 1,01 mm.
El engranaje se ha sometido a cementación y enfriamiento, y todos los índices de tratamiento térmico cumplen con los requisitos de diseño especificados en el dibujo.
Para preparar una muestra, use una máquina de corte de precisión para cortar el engranaje a lo largo de la mitad del ancho del diente y luego examine la estructura metalográfica de la raíz del diente en la superficie de corte usando un microscopio metalográfico.
En ausencia de corrosión (ver Fig. 7), se puede observar un tejido negro severo en la raíz del diente, distribuido en una red, con una profundidad promedio de alrededor de 20 μm. La profundidad individual de las telas negras alcanza hasta 30 μm.
Una fisura recta se origina en el tejido negro de la raíz del diente y se extiende hacia adentro perpendicularmente a la raíz del diente.
La observación después de la corrosión (ver Fig. 8) revela que hay estructuras cementadas y endurecidas normales en ambos lados de la grieta.
La observación metalográfica de las dos caras frontales de la raíz de la muestra no muestra signos de grietas.
Con base en la inspección anterior, se infiere que las grietas observadas se generan durante el uso, lo que sugiere que los dientes probados desarrollaron grietas por fatiga que se expandieron y la prueba se detuvo antes de que ocurriera la fractura.
Si la prueba continuara, se esperaría que se produjera una fractura.
Según el análisis metalográfico, la grieta está estrechamente asociada con el tejido negro en la raíz del diente.
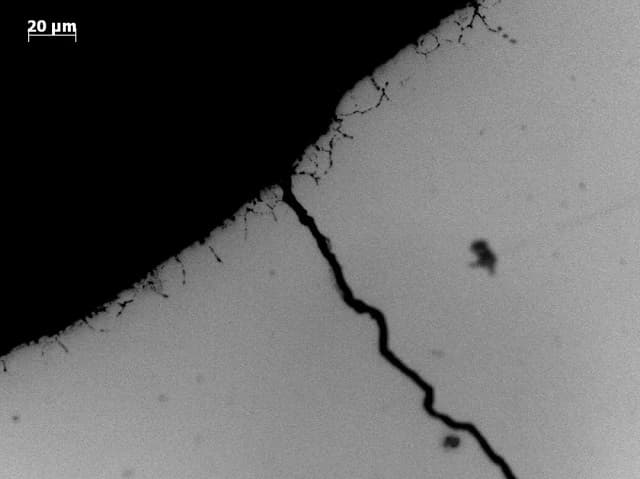
Fig. 7 Tejido negro y grieta en la raíz del diente (500 ×) Sin corrosión
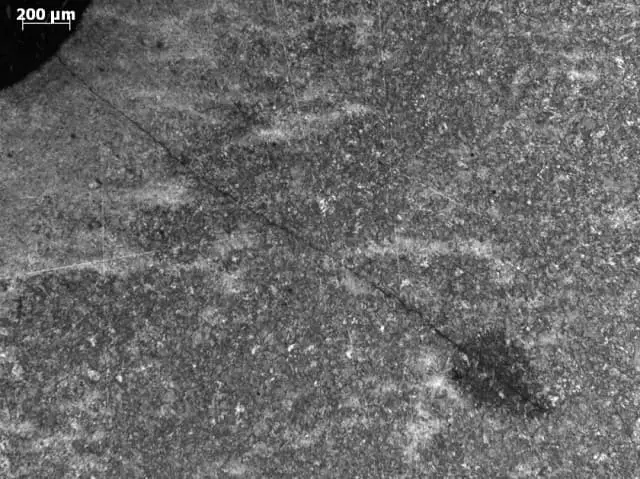
Fig. 8 Estructura en ambos lados de la grieta (solución de alcohol de ácido nítrico al 50×)4%).
2. Análisis y discusión
La mayoría de los dientes rotos en engranajes averiados se deben a fracturas por fatiga, y las grietas comienzan en la raíz de la parte media del ancho del diente.
A través de la observación metalográfica y con microscopio electrónico de barrido de la raíz del diente, es evidente que el tejido negro se convierte en la fuente de inicio de grietas durante el uso del engranaje.
A medida que aumenta el número de operaciones, la fuente de la grieta se expande y eventualmente conduce a una falla por fractura del engranaje.
Después de la cementación, la microestructura superficial del acero aleado generalmente presenta microestructuras reticuladas o con bandas de puntos negros distribuidas a lo largo del límite de grano.
La razón de este tipo de estructura es que el oxígeno del medio carburante se difunde en el acero, formando óxidos de cromo, manganeso, titanio, silicio y otros elementos en el límite del grano. Esto da como resultado elementos de aleación agotados en el límite de grano, provocando una disminución en la templabilidad local y la aparición de productos de descomposición austeníticos negros como la troostita.
Investigaciones realizadas tanto a nivel nacional como internacional indican que la presencia de tejido negro reduce significativamente la dureza superficial, la resistencia a la fatiga por flexión y la resistencia a la fatiga por contacto de las piezas, impactando negativamente en su vida útil.
Por ello, muchos fabricantes de vehículos de renombre, tanto en el país como en el extranjero, han establecido requisitos específicos para la profundidad del tejido negro. Por ejemplo, los fabricantes de automóviles alemanes como Benz y BMW exigen que la profundidad de la tela negra no supere los 3μm.
Además, FAW Group planea reducir la profundidad de la tela negra de menos de 20 μm a menos de 3 μm.
3. Sugerencias de mejora
A través de la inspección y análisis anteriores, es evidente que la profundidad de la estructura negra en la estructura metalográfica superficial de piezas cementadas y templadas requiere un control estricto. El control de la tela negra comienza principalmente con los dos aspectos siguientes:
- Mejorando la pureza del gas de carburación y reduciendo el contenido de oxígeno. Esto se puede lograr controlando estrictamente la pureza y el contenido de agua de los agentes carburantes como el metanol y la acetona y regulando la cantidad de aire.
- Adopte métodos de enfriamiento y enfriamiento más intensos, como usar un medio de enfriamiento con un rendimiento de enfriamiento y enfriamiento más fuerte o emplear un enfriamiento, enfriamiento y agitación más rápidos.