What is non-traditional machining process?
First, let's look at the definition of non-traditional machining.
Non-traditional machining, also called “unconventional machining” or “modern machining method,” generally involves using energy from electricity, heat, light, electrochemistry, chemistry, sound, or special mechanics to remove or add materials.
This results in the removal, deformation, change in properties or coating of materials.
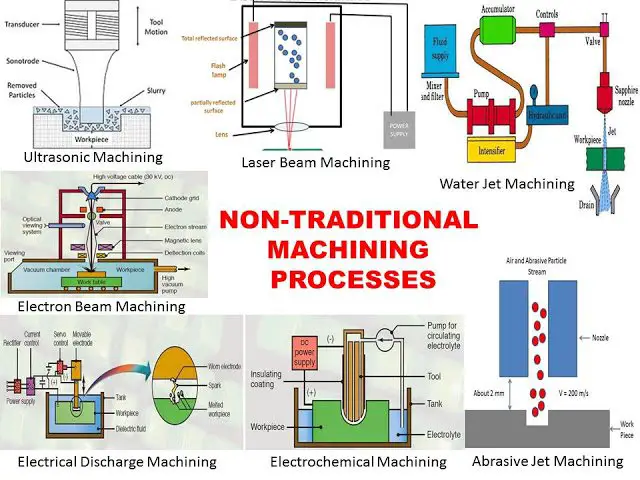
Development and Definition of Non-Traditional Machining
Traditional mechanical machining has a long history and has played a significant role in human production and material civilization.
Currently, most of our products are manufactured and assembled using traditional methods, such as household appliances (e.g. refrigerators, washing machines, air conditioners), transportation vehicles (e.g. cars, trains, planes) and weapons and equipment (e.g. guns, cannons, tanks, rockets).
Traditional mechanical machining involves using mechanical energy and cutting force to remove excess metal, resulting in a part with a specific geometric shape, size and surface roughness. The tool material must be harder than the workpiece material.
However, with the advancement of science and technology, especially since the 1950s, and the need for high-precision, high-speed, high-temperature, high-pressure and miniaturized products, particularly in the defense industry, the difficulty in machining Materials have increased, with more complex shapes and greater requirements for dimensional accuracy and surface roughness.
To meet these challenges, new requirements have emerged for the mechanical manufacturing industry, including the ability to machine difficult-to-cut materials such as hard alloys, titanium alloys, heat-resistant steels, stainless steels, hardening steels, diamond, precious jade, quartz, germanium, silicon and non-metallic materials.
Furthermore, new machining methods are needed to handle the machining of complex surfaces, such as the steric forming surface of steam turbine blades, integral turbines, engine casings and forging dies, as well as special sections on punching dies. and cold drawing, internal fluting, spraying nozzles, grids, holes and narrow slots in rotating nozzles.
To meet these demands, researchers have explored and developed non-traditional machining (NTM), also known as non-conventional machining (NCM), which uses physical energy (electricity, magnetism, sound, light and heat), chemical energy, and even even mechanical energy to directly affect the machining area and remove, deform or alter the material.
Traditional machining methods are no longer adequate to address these technical challenges, making non-traditional machining a necessary solution.
Non-Traditional Machining (NTM) has the following distinctive characteristics:
- The hardness of the tool material can be significantly lower compared to the workpiece material.
- The workpiece can be processed directly using energy sources such as electricity, electrochemical energy, sound energy or light energy.
- During machining, mechanical forces are minimal and the part suffers little or no mechanical or thermal deformation, which contributes to improving machining precision and surface quality.
- Different methods can be combined to create new process methods that significantly increase production efficiency and precision.
- With the development of new energy sources, new MNT methods are continually being developed.
Due to the above-mentioned characteristics, non-traditional machining technology is capable of processing materials, whether metallic or non-metallic, with any level of hardness, strength, toughness and brittleness, and is specialized in complex, micro-surface and low-strength machining. . stiffness parts.
At the same time, some methods can be used for superfinishing, mirror finishing and nanometer (atomic) machining.
Non-Traditional Machining Classifications
The classification of non-traditional machining has not yet been specified. Generally, it can be divided into different shapes based on power source, functional form and machining principle, as shown in the following table.
Machining method | Main energy form | Functional form | |
Electric discharge machining | EDM forming machining | Electricity, Thermal energy | Melting, gasification |
EDM cutting machining | Electricity, Thermal energy | Melting, gasification | |
Electrochemical machining | Electrochemical machining | electrochemical energy | Ion transfer |
Electroforming machining | electrochemical energy | Ion transfer | |
Plating machining | electrochemical energy | Ion transfer | |
High Energy Beam Machining | Laser beam machining | Light, Thermal energy | Melting, gasification |
Electron beam machining | Electricity, Thermal energy | Melting, gasification | |
Ion beam machining | Electricity, Mechanical Energy | Abscission | |
Plasma arc machining | Electricity, Thermal energy | Melting, gasification | |
Material cutting and erosion machining | Ultrasonic machining | Acoustic and mechanical energy | Abscission |
Abrasive flow machining | Mechanical energy | Abscission | |
Chemical machining | Chemical Milling Machining | Chemical energy | Corrosion |
Photographic plate manufacturing | Chemical energy | Corrosion | |
Light energy | |||
Lithography process | Light, Chemical Energy | Photochemistry, corrosion | |
Photoelectroforming coating | Light, Chemical Energy | Photochemistry, corrosion | |
engraving machining | Chemical energy | corrosion | |
Collage | Chemical energy | Chemical bonds | |
Explosion machining | Chemical energy, mechanical energy | explosion | |
Forming machining | powder metallurgy | Thermal energy | Thermoforming |
Mechanical energy | |||
Superplastic formation | Mechanical energy | Superplastic | |
Rapid prototyping | Thermal energy | Hot melt formation | |
Mechanical energy | |||
Composite machining | Electrochemical arc machining | electrochemical energy | Melting corrosion and gasification |
Electrodischarge mechanical grinding | Electricity, Thermal energy | Ion transfer, fusion, cutting | |
Electrochemical etching | Electrochemical energy, Thermal energy | Melting, gasification corrosion | |
Ultrasonic EDM | Sound, heat, electricity | Melting, Abscission | |
Complex electrolytic machining | Electrochemical energy, mechanical energy | Abscission | |
Combined Cutting Base Machining | Mechanical, acoustic and magnetic energy | Cut |
Types of unconventional machining processes
Electrical Discharge Machining (EDM):

Basic principle:
EDM, or Electrodischarge Machining, is a type of non-traditional machining method that involves etching conductive materials through electrical erosion caused by pulse discharge between two poles immersed in a working liquid. This process is also known as Discharge Machining or EDM Machining. The basic equipment for this method is an electrodischarge machine tool.
Main features of EDM:
- Capable of processing difficult-to-cut materials using traditional machining methods and complex shaped parts.
- No cutting forces are involved in the machining process.
- Prevents defects such as burrs, tool marks and grooves.
- The tool electrode material does not need to be harder than the workpiece material.
- The machining process is easily automated due to the direct use of electricity.
- Requires additional removal of the surface-generated metamorphic layer in some applications.
- Treatment of smoke pollution produced during purification and processing of the working fluid can be problematic.
Application scope:
- Machining of molds and parts with holes and cavities of complex shapes.
- Machining of various hard and brittle materials, such as hard alloys and hardened steel.
- Processing of deep fine holes, shaped holes, deep grooves, narrow slits and thin slice cutting, etc.
- Machining of all types of tools and measuring tools such as cutting tools, sample plates and screw ring gauges.
Electrolytic machining:
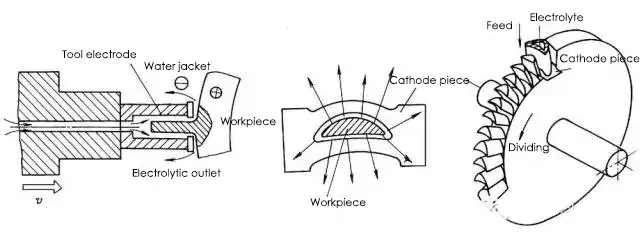
Basic principle:
The principle of electrochemical dissolution is used in electrolytic machining, with the aid of a mold as a cathode. The workpiece is machined to a specific shape and size.
Application scope:
Electrolytic machining is ideal for difficult-to-machine materials and for parts with complex shapes or thin walls.
This method has been widely used for various applications, such as gun barrel rifling, blades, integral impellers, molds, holes and profiled parts, chamfering and deburring.
In many machining operations, electrolytic machining technology has gained a significant or even indispensable role.
Benefits:
- Wide range of machining – Almost all conductive materials can be processed through electrochemical machining without being limited by the mechanical and physical properties such as strength, hardness, toughness or metallographic structure of the material. It is often used to machine hard alloys, high temperature alloys, hardened steel, stainless steel and other difficult-to-machine materials.
- High production rate
- Good machining quality, especially in terms of surface quality
- Can be used for machining thin-walled and deformable parts – There is no contact between the tool and the workpiece, no mechanical cutting force, no residual stress or deformation, and no burrs or breakages during the electrochemical machining process.
- The tool cathode is free from wear.
Limitations:
- Low machining and machining precision
- High machining cost. The smaller the batch, the higher the additional cost per piece.
Laser machining:
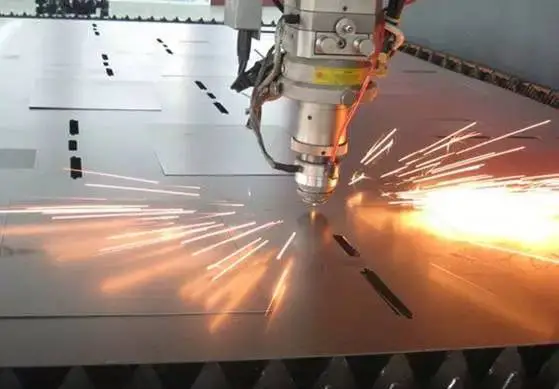
Basic principles:
Laser machining is a process that uses high-energy beams of light, focused by a lens, to melt or vaporize materials and remove them in a short space of time to achieve machining.
Benefits:
Laser machining technology has advantages such as minimal material waste, savings in large-scale production and versatility in machining objects. In Europe, laser technology is widely used to weld special materials such as high-quality car bodies, aircraft wings and spacecraft fuselages.
Application scope:
As the most commonly used application, laser machining technologies mainly include laser welding, laser cutting, surface modification, laser marking, laser drilling, micromachining and photochemical deposition, stereolithography, laser engraving and so on.
Electron beam machining:
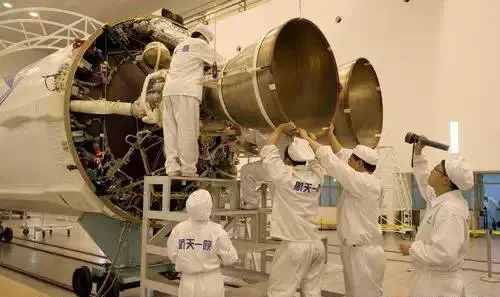
Basic principles:
Electron beam machining (EBM) is the machining of materials using the thermal or ionization effects of the high-energy convergent electron beam.
Main features:
High energy density, strong penetration, a wide range of unique melting depth, large weld width ratio, fast welding speed, small thermal impact zone, small working deformation.
Application scope:
Electron beam machining has a wide range of machinable materials and can machine very small areas.
It achieves nanometer-level machining precision, capable of molecular or atomic machining.
It has high productivity, but the cost of machining equipment is high.
The machining process produces minimal pollution.
It is suitable for micro-hole and narrow slot machining, and can also be used for welding and fine lithography.
Vacuum electron beam welding bridge coating technology is the main application of electron beam machining in the automobile industry.
Ion beam machining:
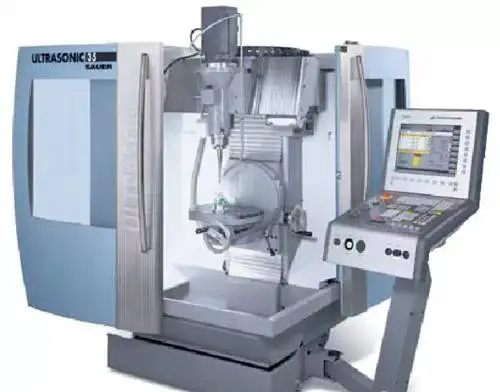
Basic principles:
Ion beam machining is performed by accelerating and focusing the ion flow generated by the ion source on the surface of the workpiece in a vacuum state.
Main features:
Due to the precise control of ion flux density and ion energy, ultra-precision machining at the nanometer, molecular and atomic levels can be achieved. Ion beam machining results in minimal pollution, stress, and deformation and is adaptable to processed materials, but is costly.
Application scope:
Ion beam machining can be divided into two types: engraving and coating.
Engraving machining:
Ionic etching is used in the machining of pneumatic gyroscope bearings and grooves in dynamic pressure motors, with high resolution, high precision and good repetition consistency.
Another application of ion beam recording is the recording of high-precision graphics such as integrated circuits, optoelectronic devices, and integrated optical devices.
Ion beam recording is also used for thinning materials to prepare samples for penetrating electron microscopy.
Coating machining:
Ion beam cladding machining has two forms: sputter deposition and ion plating.
Ionic plating can be applied to a wide variety of materials. Metallic or non-metallic films can be coated on metallic or non-metallic surfaces, and various alloys, compounds or synthetic materials, semiconductor materials and high melting point materials can also be coated.
Ion beam coating technology is used to coat lubricating films, heat-resistant films, wear-resistant films, decorative films and electrical films.
Plasma arc machining:
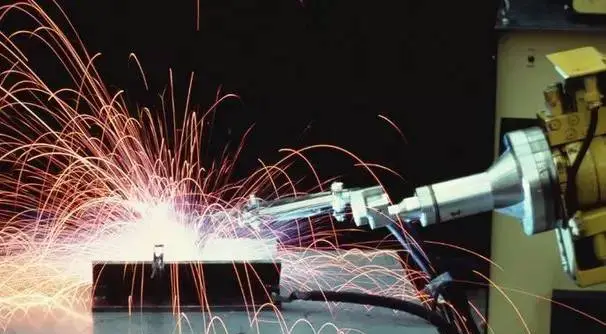
Basic principles:
Plasma arc machining is a non-traditional machining method for cutting, welding and spraying metal or non-metal by the thermal energy of plasma arc.
Main features:
- Microbeam plasma arc welding is capable of welding thin sheets and plates.
- It has a unique keyhole effect that allows welding on one side and free forming on two sides.
- The plasma arc has high energy density and temperature in the arc column, resulting in strong penetration capabilities. This means that chamfering is not necessary for steel with a thickness of 10-12 mm and complete weld penetration and formation of both sides can be achieved in a single pass, resulting in high welding speed, high productivity and minimum deformation due to voltage.
- However, the equipment for this process is complex and has high gas consumption, making it only suitable for internal welding.
Application scope:
It is widely used in industrial production, especially for welding of copper and copper alloys, titanium and titanium alloys, alloy steel, stainless steel, molybdenum used in military industry and high-end industrial technology such as aerospace, such as alloy missile shell of titanium, some of the aircraft's thin-walled containers.
Ultrasonic machining:
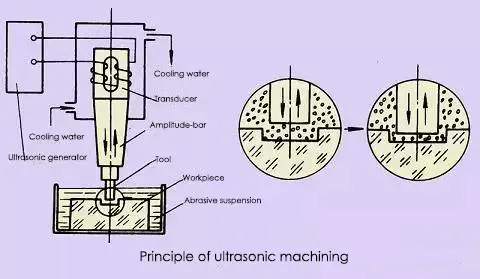
Basic principles:
Ultrasonic machining causes the surface of the part to break gradually by using ultrasonic frequency as a tool for small amplitude vibration and puncture on the processed surface by free abrasive in the liquid between it and the part.
Ultrasonic machining is often used for drilling, cutting, welding, nesting and polishing.
Main features:
It can machine any material, especially suitable for machining various hard, brittle and non-conductive materials, with high precision, good surface quality, but low productivity.
Application scope:
Ultrasonic machining is mainly used for drilling (including round holes, shaped holes and curved holes, etc.), cutting, grooving, nesting, carving of various hard and brittle materials, such as glass, quartz, ceramics, silicon, germanium, ferrite, precious stones and jade, deburring of small parts in batches, mold surface polishing and grinding wheel finishing.
Chemical machining:
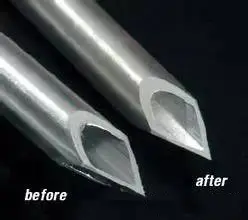
Basic principles:
Chemical machining uses acid, alkaline, or saline solutions to erode or dissolve material from parts to obtain the desired shape, size, or surface of the part.
Main features:
- It can process any metal material that can be cut, free from hardness and toughness.
- It is suitable for large area machining and can process many parts at the same time.
- The surface roughness reaches Ra1.25 ~ 2.5μm without any stress, crack or burr.
- Easy to operate.
- Not suitable for machining narrow channels and holes
- It is not suitable for eliminating defects such as surface roughness and scratches.
Application scope:
- Suitable for thinning over large areas;
- Suitable for machining complex holes in thin-walled parts
Rapid Prototyping:
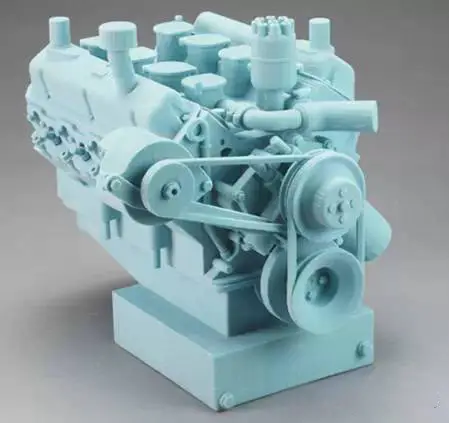
RP Technology is an integration and development of modern CAD/CAM technology, laser technology, computer numerical control technology, precision servo drive technology and new material technology. Different rapid prototyping systems have different forming principles and system characteristics due to the variety of forming materials, but the fundamental principle remains the same, which is 'layer manufacturing, building on each layer'.
It is similar to a mathematical integration process and, visually, the rapid prototyping system resembles a “3D printer.
Basic principles:
The integration and development of RP technology, based on modern CAD/CAM technology, laser technology, computer numerical control technology, precision servo drive technology and new material technology, enables direct receipt of product design (CAD) data and the rapid manufacture of new samples, molds or product models without the need for molds, cutters or accessories.
As a result, the widespread use and application of RP technology significantly shortens the new product development cycle, reduces development costs, and improves development quality.
The transition from the traditional “elimination method” to the current “growth method”, and from mold manufacturing to moldless manufacturing, represents the revolutionary impact of RP technology on the manufacturing industry.
Main features:
RP technology converts complex three-dimensional machining into a series of layered machining, significantly reducing machining difficulty. It has the following characteristics:
- The rapid speed of the overall forming process, making it ideal for today's fast-paced product market;
- Ability to create three-dimensional objects of any complex shape;
- There is no need for special accessories, dies or cutters during molding, which reduces costs and shortens the production cycle;
- High level of technological integration, the result of the advancement of modern science and technology, and demonstration of its comprehensive application, with distinct high-tech characteristics.
The above characteristics indicate that RP technology is ideal for the development of new products, the rapid manufacturing of single and small batch parts with complex shapes, the design and production of molds and models, and the production of difficult-to-machine materials.
Furthermore, it is suitable for shape design inspection, assembly and rapid reverse engineering.
Application scope:
Rapid prototyping technology can be applied in the fields of aviation, aerospace, automobile, communications, medical treatment, electronics, household appliances, toys, military equipment, industrial modeling (sculpture), building model, machinery industry, etc.
Conclusion
In this article we list nine types of non-traditional machining techniques, which can serve as a practical guide for anyone who wants to learn about the non-traditional machining process, its advantages, classifications and much more.