1. Projection welding is a multi-point welding process.
2. In resistance welding, the pressure is released after the weld cools.
3. Gray cast iron is best welded by oxy-acetylene.
4. Edge preparation for welding is not necessary up to 4 mm sheet thickness.
5. The relationship for cutting tool life is given by VTn = C where V is the cutting speed, T is the corresponding life n and C are constant depending on the cutting conditions. The numerical value of n for rough cutting compared to that for light cutting in carbon steel does not depend on the type of cutting.
6. A plug gauge is used for inspection to check the tolerance, i.e. upper and lower limits of the bore or cylindrical bore. Its work on the GO/NO-GO principle.
7. Aluminum has a higher cutting speed than cast iron and tool steel.
8. A magnetic chuck is generally used when a large number of components are rotated and separated from a bar.
9. Gear tooth vernier is used to measure the gear tooth profile.
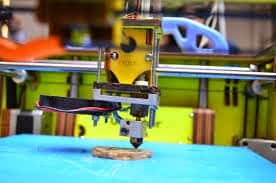
10. Undercut is the cutting of the base of a workpiece.
11. Laser welding is widely used in the electronics industry.
12. Different materials or materials of different thickness can be welded by controlling pressure and current.
13. In welding operations, the current value is decided by the size of the electrode.
14. The phenomenon of weld deterioration occurs in stainless steel.
15. The arc below occurs when welding stainless steel.
16. Cotton swab is used in casting to repair the mold.
17. The gag is used in foundry for cleaning castings.
18. Bellows are used in casting to smooth and clean depressions in the mold.
19. The permeability of a foundry sand is the ability to retain moisture.
20. What are metal molds used for in large-scale production of castings?
21. An important factor to consider when designing a core impression is the characteristics of the molding sand.
22. Weld spatter refers to welding defects.
23. If 't' is the thickness of the sheet to be spot welded, then the diameter of the electrode tip is equal to √t.
24. A sprue is a tool used in mold repair.
25. The gate is a ventilation hole to allow hot gases to escape.
26. Core impressions provided from the seat to support and hold the core.
27. The equipment used in the well to supply air is known as a centrifugal blower.
28. Draft tolerance on castings is generally 1-2 mm/M.
29. Tumbling is done to clean the surface of small parts.
30. The purpose of inoculation is to modify the structure and properties of a molten metal.
31. The print run margin for metallic patterns is smaller when compared to wooden ones.
32. The angle is not an angle measuring device.
33. The mold for casting ferrous materials in the continuous casting process is made of copper.
34. If V is the volume of metal in a casting and A is its surface areas, then the solidification time will be proportional to V2, 1/A2. The purpose of the riser is to help feed the casting until all solidification has occurred.
35. Silver refers to the equilibrium temperature between solid silver and liquid silver at normal atmospheric pressure.
36. The golden point refers to 10630C.
37. The silver tip refers to 960,500C.
38. Rotameter is used for flow of liquids and gases.
39. The impedance of the piezoelectric crystal is high.
40. Hot wire anemometers are generally used to measure the vapor velocity of air.
41. Scale sensitivity is defined as the ratio of a change in scale reading to the corresponding change in pointer deflection.
42. In the Cartias process, the cavity is filled with a pre-calculated amount of metal and a core or plunger is inserted to force the metal into the cavity.
43. In the mud casting process, metal is poured into the die cavity and, after a predetermined time, the mold is inverted to allow some of the still molten metal to flow out of the cavity.
44. Ornaments are cast by gravity.
45. During MIG welding, metal is transferred in the form of a fine spray of metal.
46. A collimated beam of light is used to produce heat in laser welding.
47. Wipping is the process of connecting loss tubes by means of solder alloy.
48. In the waterjet machining process, hydraulic fluid acts as a transfer medium.
49. Energy consumption in ultrasonic machining in kW/cm3/min is on the order of 10 kW/m3/min.
50. Sweep pattern is used to form parts with uniform symmetrical shape.
51. The helix angle on an HSS (high speed steel) twist drill for drilling cast iron is on the order of 24-320.
52. The usual value of the helix angle of a drill is 300.
53. A twist drill is specified by shank, material, and diameter.
54. The broaching operation is generally used in the automobile industry as semi-skilled operators can be employed.
55. For a proper broaching operation, at least three teeth must be in action at the same time.