Compressed air is widely used in many industries as a source of energy, transportation and for various technological applications. It is important to note, however, that compressed air can contain a significant amount of moisture, which in turn can have a negative impact on the quality and performance of industrial equipment and the quality of products. This is why compressed air drying, a process of removing moisture from the air, is so important to ensure its proper functioning and quality.
Compressed air drying is a process that removes excess moisture from the air. In humid air, this moisture can lead to corrosion of machines, contamination of products, loss of equipment performance and even health problems. This is why it is so important to obtain compressed air with adequate humidity.
Many manufacturers of industrial equipment and machinery recommend using compressed air with humidity less than 50% to ensure proper product quality and equipment efficiency. Therefore, compressed air drying is necessary in many industries, for example in the food, pharmaceutical, chemical and heavy industries.
Another reason drying compressed air is so important is that moist air can cause water vapor to form in pipes and other parts of the compressed air system. This water vapor can damage equipment and increase system maintenance and repair costs.
Ultimately, the use of compressed air drying can increase the efficiency, durability and quality of industrial equipment and products, as well as save time and production costs.
Why should you use compressed air to dry?
Drying compressed air is extremely important as moisture in the air can cause many problems in many industries. Below you will find the most important reasons why you should use compressed air drying:
- Corrosion: Moisture in compressed air can cause corrosion of the internal parts of the compressed air system, including the compressor, piping, valves and air tanks. Corrosion can cause damage to devices and, in extreme cases, the failure of the entire system.
- Product Contamination: The moisture contained in compressed air can lead to contamination of products manufactured in an industrial process. For example, humidity in the food industry can lead to the formation of mold and bacteria, which in turn can lead to food spoilage and reduced shelf life.
- Equipment Damage: Moisture in compressed air can damage equipment such as pneumatic tools, motors, valves and pneumatic controls. Moisture can affect the operation of these devices, resulting in breakdowns and the need for repair or replacement.
- Time and cost savings: Compressed air drying can save time and production costs by allowing industrial equipment to operate more efficiently and produce less spoiled product.
In summary, drying with compressed air is necessary to guarantee the correct quality of products, durability and efficiency of equipment, in addition to saving time and production costs. The use of compressed air drying is therefore standard in many industries.
It is worth mentioning that drying with compressed air not only affects the quality of products and the efficiency of equipment, but can also affect the safety of employees. Therefore, when working in an industry where compressed air is used, adequate humidity control must be ensured.
What methods are there for drying compressed air?
There are several compressed air drying methods, each with its advantages and disadvantages.
- Adsorption dehumidifier: This method uses adsorption materials such as calcium silicates, lithium silicates or molecular sieves to absorb moisture from the air. Compressed air flows through the dryer and adsorbent material removes moisture. The material is then regenerated using heat or airflow. The disadvantage of this method is that large amounts of energy are required to regenerate the adsorption material.
- Cooling: This method uses the cooling effect to condense moisture from the air. Compressed air flows through a heat exchanger where it is cooled to a temperature at which moisture is condensed into water and removed. This method is relatively simple and low maintenance, but it is not suitable for removing moisture at high temperatures.
- Semi-permeable membranes: This method uses membranes that selectively allow water molecules to pass through and trap remaining gases. Compressed air flows through the membranes and moisture is trapped and removed. This method is relatively effective, but may require high investment costs.
- Drainage: In this method, moisture is removed from the air using low pressure. Compressed air is introduced into a low pressure chamber and moisture is removed through expansion. This method is relatively inexpensive to maintain, but requires large amounts of energy to create negative pressure.
What is compressed air drying used for? The answer is simple – to guarantee the correct quality of compressed air and thus improve efficiency and safety in the industry. The choice of drying method depends on individual needs and requirements, such as humidity, temperature, energy and investment costs.
Using the appropriate air drying method depends on many factors, such as the type of process in which compressed air is used, the moisture level required for the process, and capital and operating costs. Regardless of the method, drying compressed air is essential to ensure the reliability and efficiency of many processes and extend the useful life of compressors and other equipment.
What factors should be considered when choosing an air dehumidification method?
The choice of dehumidification method depends on many factors, such as the humidity level required by the process, capital and operating costs, process efficiency, and operating conditions at the dehumidifier installation location. Below are the main factors to consider when selecting the appropriate compressed air drying method.
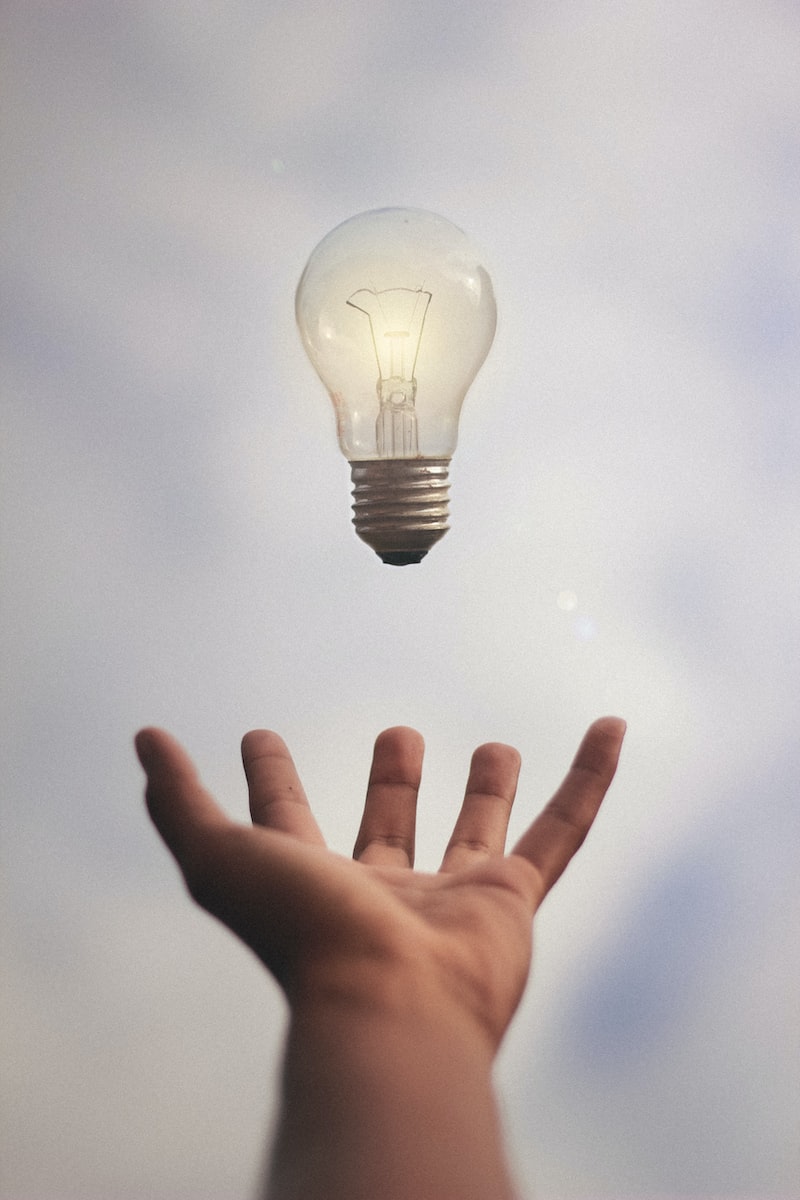
- Moisture level required for the process
One of the most important factors to consider when choosing an air drying method is the humidity required by the process in which compressed air is used. The lower the humidity required, the more advanced and expensive the dehumidification method will be. - Investment and operating costs
Investing in advanced dehumidification systems can be expensive and operating costs can vary depending on the method chosen. The costs of energy, consumables, services and repairs must be taken into account. - Process efficiency
Another important factor is the efficiency of the process in which compressed air is used. The air drying method must be chosen to ensure adequate moisture and not limit the efficiency of the process. - Working conditions at the dehumidifier installation site
Operating conditions at the dehumidifier installation site, such as temperature, pressure, and power availability, may influence the selection of the appropriate dehumidification method.
All of these factors must be taken into consideration when selecting a compressed air drying method to ensure correct moisture and process efficiency with minimal investment and operating costs.
Summary
The conclusion is that compressed air drying is essential in many industrial applications where low humidity air quality is necessary to ensure the reliability and durability of machines and equipment. Excessive moisture can cause corrosion, failures and other problems.
To dehumidify the air, there are several methods such as adsorption dehumidification, cold dehumidification and membrane dehumidification. Each of these methods has its advantages and disadvantages, and the choice of the appropriate method depends on the specificity of the application.
When choosing an air drying method, factors such as the required air moisture content, operation and maintenance costs, compressed air volume and pressure, and many others must be taken into consideration. In any case, it is important to adequately adapt the drying process to the needs of a specific application to obtain the best results and guarantee the reliability and longevity of the equipment, which translates into the safety and profitability of the entire process.
Advantages of using compressed air in industry
Compressed air is one of the most important media in the industry. It is used in various industries, from food production to the chemical industry and construction. Thanks to its properties such as flexibility, non-flammability and non-toxicity, compressed air is a safe and efficient source of energy in industrial processes.
Compressed air can be used to drive pneumatic tools, transport bulk materials, painting, air conditioning work and many other applications. As compressed air is saturated with moisture, it must be dried to avoid damage to industrial processes and pneumatic tools.
One of the most important applications of compressed air drying is to ensure safety in industrial processes. Moist air can cause corrosion and rust on machines and tools, which in turn can cause breakages and damage. Dry compressed air also allows for higher quality products, especially in the food and pharmaceutical industries where humidity can lead to product contamination.
In addition to ensuring product safety and quality, compressed air drying can also offer economic benefits. Moist air is less efficient in processes, which means it uses more energy and increases production costs. Dehumidified air is more efficient and requires less energy to perform the same tasks.
In summary, compressed air drying is crucial for the safety and efficiency of industrial processes, as well as the quality of products. Choosing the right dehumidification method depends on many factors, such as the moisture content of the air, the level of purity required for the process, cost, and more. In any case, compressed air drying is a crucial part of the industrial process and must be carried out in accordance with best practices and standards.
How do you maintain your air drying system?
In addition to choosing the appropriate air drying method, it is also important to ensure that the system is working properly. To guarantee its effectiveness and efficiency, all its components require regular maintenance.
First, air filters, which are responsible for removing pollutants from the air flowing through the system, must be replaced regularly. These contaminants can affect system performance and increase operating costs. Filters should be replaced every few months or as recommended by the manufacturer.
Another important element is condensate, which accumulates in the water separators. The water separator must be emptied regularly to avoid contamination and avoid possible failures.
Furthermore, it is important to regularly check and maintain the entire dehumidification system. If necessary, replace damaged components such as controls, valves or sensors.
Finally, remember to use the air drying system properly. Follow the manufacturer's recommendations and avoid overloading the system, which can result in increased operating costs and system damage.
By taking care of the air drying system in this way, you can ensure its effective and long-term operation, which helps to improve the efficiency of industrial processes and minimize operating costs.
The role of compressed air drying in industry is very important and cannot be underestimated. In addition to the drying process itself, there are other aspects related to compressed air that deserve attention. One of them is to avoid atmospheric pollutants, such as dust, oils and other chemicals that may be in the air.
These pollutants can affect the quality of products and services, as well as the safety of employees. Therefore, it is important to monitor pollution levels and use appropriate filters to ensure clean air in the production line.
Another important aspect is air temperature control. Compressed air often gets very hot, which can affect the performance of the compressor and other equipment. Therefore, it is worth investing in a refrigeration system that maintains the ideal air temperature.
The last but equally important aspect is noise reduction. Various types of noise-generating devices are frequently used in industry, with compressed air being one of the most important sound carriers. Therefore, it is worth investing in adequate acoustic insulation that reduces noise levels and guarantees working comfort for employees.
Important topics related to compressed air
In summary, when it comes to compressed air, in addition to the drying process itself, issues such as preventing air pollution, controlling air temperature and reducing noise are also important. By taking care of these aspects, you can not only maintain optimal product efficiency and quality, but also ensure the safety and work comfort of your employees.
Thank you for reading my article on compressed air drying. I hope I was able to provide interesting and useful information on this subject. It is always worth remembering that air dehumidification is of great importance for the operation of different types of devices and machines.