See too:
- Basic Guide to Cutting Tool Materials (How to Choose?)
Types of materials for cutting tools
1. Loud Fast Iron

High-speed steel is a type of tool steel known for its high hardness, high wear resistance and high heat resistance, achieved through the addition of elements such as tungsten, molybdenum, chromium and vanadium. Also known as high-speed tool steel or hot work steel, it is commonly referred to as “white steel.”
High-speed steel is primarily used to create complex, lightweight, and impact-resistant metal cutting tools. The manufacturing process for high-speed steel tools is simple and allows for easy sharpening, which is why they still make up a significant proportion of metal cutting tools despite the emergence of newer materials.
2. Cemented and treed
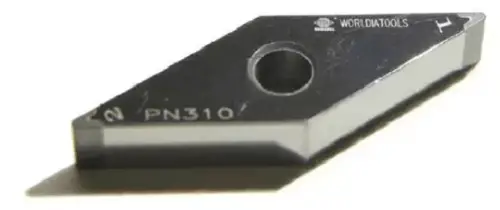
Cemented Carbide is an alloy made of refractory metals and binding metals, produced using P/M metallurgical techniques. This material has excellent properties such as high hardness, wear resistance, good strength and toughness, heat resistance and corrosion resistance.
In particular, its high hardness and wear resistance remain constant even at temperatures of up to 500°C, and it still has high hardness at 1000°C. Thus, carbide has superior cutting performance compared to high-speed steel and can improve tool durability by several to dozens of times.
With the same durability, carbide allows cutting speeds to increase by 4 to 10 times. As a result, it is widely used as a tool material, capable of cutting difficult-to-machine materials such as heat-resistant steel, stainless steel, high manganese steel, and tool steel.
3. Diamond
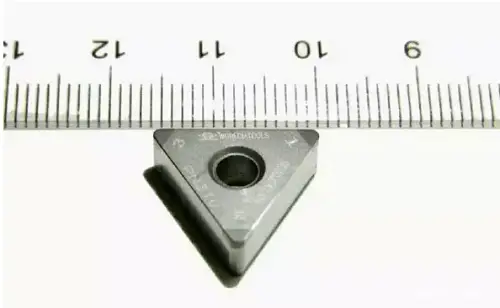
Diamond is considered the hardest substance with exceptional thermal conductivity among known mineral materials. Its friction wear with various metallic and non-metallic materials is only 1/50-1/800 of that of carbide, making it the ideal material for cutting tools.
Mainly, cutting tools are made of single crystal artificial diamonds. The cutting edge of diamond tools is incredibly sharp, which is important for cutting chips with small sections. Its cutting edge has low roughness and a low coefficient of friction, making the production of chips during cutting unlikely, resulting in high quality machined surfaces.
There are three types of diamond cutting tools: natural single crystal diamond tools, solid synthetic single crystal diamond tools and composite diamond tools. However, natural diamond tools are rarely used in actual production due to their high cost.
4. Cubic boron nitride
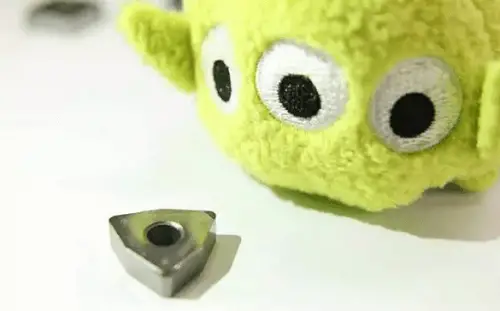
It is a newly developed artificially synthesized material sintered from CBN (cubic boron nitride) powder and a small amount of binder (such as Co-Ni, TiC, TiN or Al2O3) under high temperature and pressure and with the help of a catalyst . It has high hardness, good abrasion resistance, exceptional chemical stability and greater thermal stability compared to diamond tools.
It can maintain its properties even when used at temperatures between 1200-1300°C and does not react with iron group metals, which makes it ideal for steel processing. Hence, CBN cutting tools are mainly used for efficient machining of difficult-to-machine materials and have a wide range of applications in the machining industry.
5. Ceramics
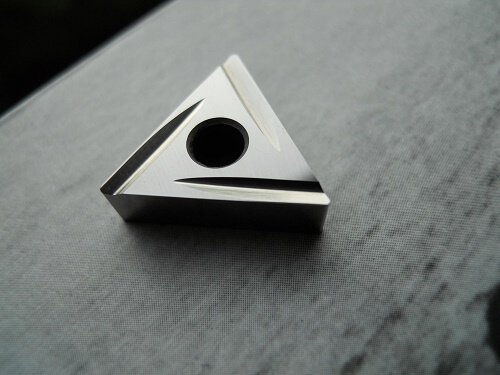
The main advantages of ceramic tool materials are their high hardness and abrasion resistance, as well as minimal reduction in bending strength and bending strength at high temperatures.
They have high chemical stability, low affinity for metals and good resistance to oxidation at high temperatures. They do not react with steel even at melting temperatures, resulting in less adhesion, diffusion and oxidative wear, as well as a lower coefficient of friction. Chips are also less likely to stick to cutting tools and are less likely to produce chips.
However, the disadvantages of ceramic tools include high brittleness, low strength and toughness, and weaker flexural strength compared to carbide.
Selection criteria for cutting tool materials
When choosing cutting tool materials, it is essential to consider several factors to ensure optimal performance and longevity. In this section, I will discuss my main considerations when selecting materials for cutting tools: strength and hardness, toughness, wear resistance, thermal stability, and affordability.
Strength and Hardness
Strength and hardness determine a material's ability to withstand the cutting forces and stresses experienced during machining operations. I typically consider the following when evaluating these properties:
- High tensile strength: This allows the cutting tool to resist deformation and fracture under cutting loads.
- High hardness: This ensures that the material has excellent resistance to wear and deformation of the cutting edge.
Toughness
Toughness is a crucial factor as it measures a material's ability to absorb energy and resist fracture or chipping. When evaluating the material toughness of a cutting tool, I consider:
- Chipping resistance: The cutting tool must be able to maintain its cutting edge without any chipping, which can affect the quality of the machined part.
- Impact resistance: The material must withstand sudden loads and impacts encountered during intermittent cutting operations.
Wear resistance
As the cutting tool continually experiences friction during machining processes, wear resistance is a critical consideration. I focus on:
- Abrasive wear resistance: Reducing the wear rate of the cutting edge ensures that the cutting tool maintains sharpness and precision.
- Adhesive wear resistance: The material must prevent the formation of any bonds between the tool surface and the workpiece, leading to material transfer and ultimately wear.
Thermal stability
Because cutting tools generate high temperatures during machining, thermal stability is vital. I consider the ability of a material to:
- Withstand high temperatures: The cutting tool material must maintain its hardness and resistance even at high temperatures.
- Resist thermal fatigue: The material must be able to handle rapid temperature changes without cracks or fractures forming in the cutting tool.
Accessibility
Finally, I evaluate the material affordability of a cutting tool, as cost is an essential factor in any machining process. I take into consideration:
- Material cost: The material cost of the cutting tool should not exceed the performance benefits.
- Tool life: Longer tool life can offset higher cost by reducing the frequency of tool replacements and maintenance downtime.
By carefully considering these factors, I can select the best cutting tool material for my specific machining needs.
Applications and industry trends
Machining Operations
In my experience, cutting tool materials are essential for many machining operations. They help improve productivity, reduce costs and achieve better product quality. Some common machining operations are:
- Milling: Here, cutting tools remove material from the workpiece through rotary movement. High speed steel (HSS) and carbide tools provide excellent performance in this operation.
- Rotating: In this operation, I observed that single-point cutting tools remove material from the part as it rotates. Common materials include ceramic, polycrystalline diamond (PCD), and carbide.
- Drilling: When drilling, a multi-point or single-point cutting tool is used to create cylindrical holes in the workpiece. HSS and carbide tools are my preferred choices for this operation.
Emerging technologies
I have noticed several emerging technologies shaping the cutting tool industry. These include:
- Additive Manufacturing: This technology allows the production of cutting tools with complex geometries, reducing material waste and production time.
- Coating technologies: Advanced coatings such as diamond-like carbon and nanocomposite coatings promise greater wear resistance, longer tool life and improved performance.
- Smart Tools: My experience with tools integrated with sensors and wireless connectivity shows potential for real-time monitoring and predictive maintenance, leading to reduced downtime and optimized tool usage.
By staying informed in these areas, industry professionals can make better decisions and maximize the efficiency of their cutting tools.